Step drilling and chamfer drilling
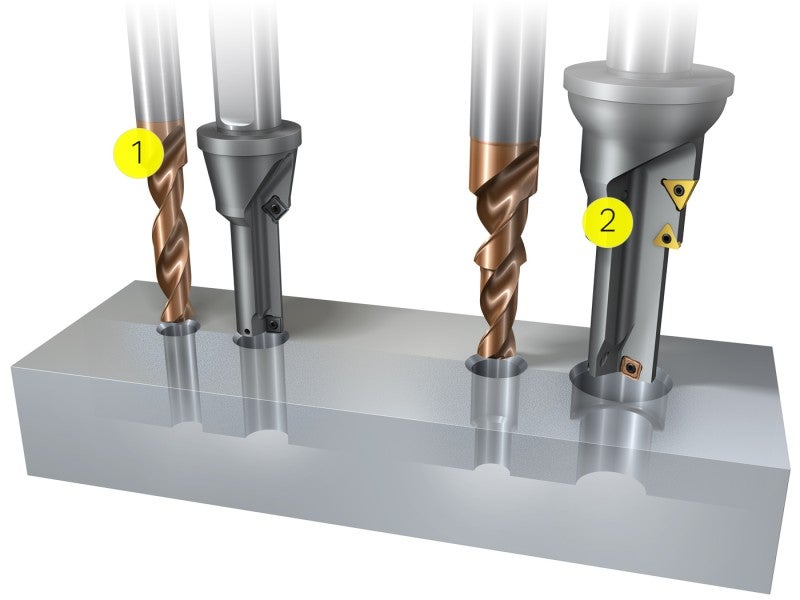
- Chamfer drilling
- Step drilling or step and chamfer drilling
Chamfer drilling
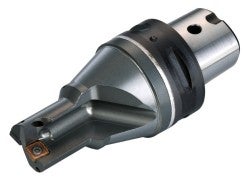
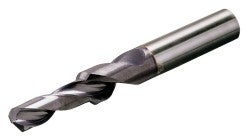
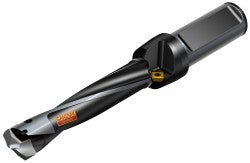
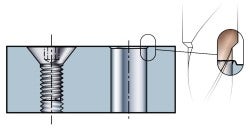
What is a chamfered hole?
A large number of all holes produced need a chamfer or at least some deburring. Some typical examples are screw and rivet holes.
There are a number of drills to choose from, and by using circular interpolation, even a turning or a milling tool can be used.
Solid carbide drills
A standard program of drills for 45° chamfers adapted for different thread/tap holes up to hole depths of 2–3 × DC.
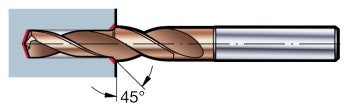
How to apply chamfer drilling
Normally, the same feed, fn(mm/rev), should be used when the chamfer insert is cutting. This is especially important when drilling a blind hole because a reduction in feed can result in long chips from the drilling operation.
However, in long-chipping materials, feed adjustment may sometimes be necessary during the chamfering operation to prevent long chips from wrapping around the drill.
fn drill
fn chamfering
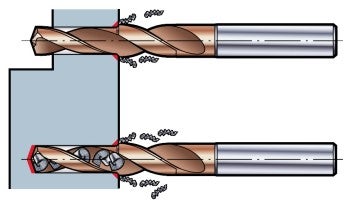
Step drilling or step and chamfer drilling
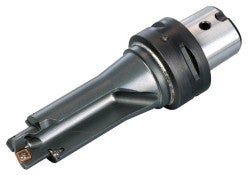
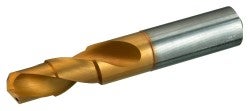
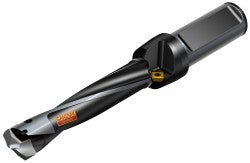
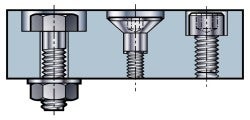
Another common type of hole is a stepped, or stepped and chamfered hole. Typical applications are components with countersunk screws or bolts.
Drilling stepped or stepped and chamfered holes
Step/chamfer holes in one pass
Solid carbide drills – available with steps and chamfers.
Stepped holes by drilling two holes
Solid carbide drills – choose drill according to hole size and depth.
Stepped holes by drilling and boring
Solid carbide drills – choose drill and boring tool according to hole size and depth.
Stepped holes by helical interpolation
The step diameter hole can be 2 × Dc. Helical interpolation is a slow operation and should not be used for deep steps. Choose cutter according to hole size.
Non-rotating drill
Choose a standard drill and program the tool path.
How to apply
Step/chamfer holes in one pass
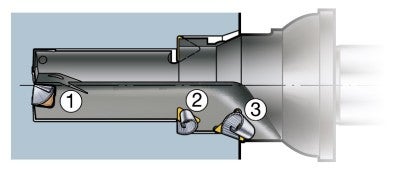
The challenge when using a multidiameter tool is to achieve good chip breaking from all edges in the cut. In long-chipping materials, such as low carbon steels and stainless steels, the initial tests should be made in steps:
- First, check chip formation from the drill
- Check chip formation from step insert
- Check chip formation from chamfer insert
Stepped holes by drilling two holes
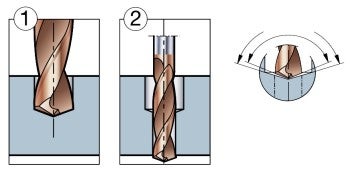
First the larger diameter, then the smaller.
Always start drilling the large diameter to ensure centering of the drill point and avoid chipping cutting edges.
When drilling the small diameter, make sure that the drill point angle is equal to or smaller than that of the large drill to ensure that the point hits the workpiece first.
Stepped holes by drilling and boring
Start with drilling then boring.
Stepped holes by helical interpolation
See Milling to learn more about hole making with milling cutters.
Drilling
Drilling is often carried out late in the manufacturing process, after previous operations... chevron_right
Radial adjusted drilling
Radial adjusted drilling is only possible using indexable insert drills. Radial... chevron_right
CoroDrill® 400
Complex, multi-step form drills with a diameter range of 3–25 mm, up to 8 x Straight-flute... chevron_right
CoroDrill® 430
Complex, multi-step form drills with a diameter range of 3–25 mm, up to 8 x Straight-flute... chevron_right