Sådan vælger du maskinspindel
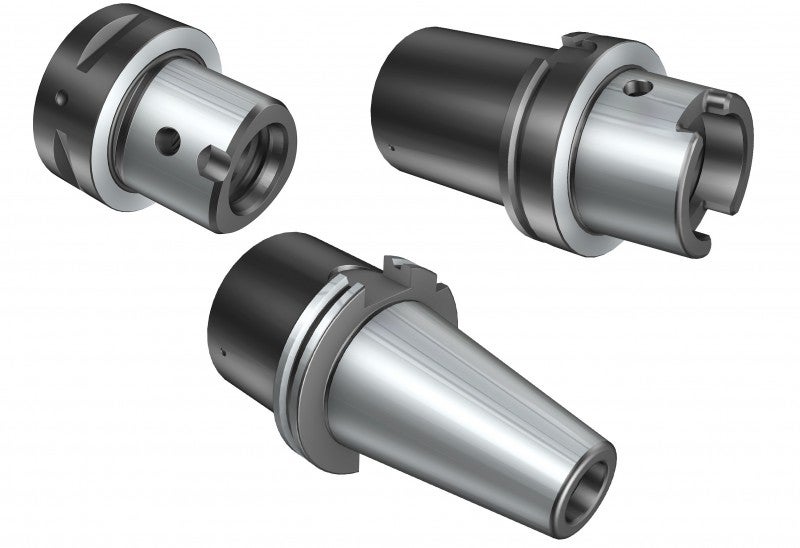
Hvordan man vælger maskinspindel-interface er en afgørende beslutning, da det ofte definerer grænserne for effektiv spåntagende bearbejdning. Der findes ikke noget entydig svar på, hvilket interface der er bedst. Det afhænger af de komponenter, der skal bearbejdes, og af de typer bearbejdning, der udføres. Man bør ikke gå ud fra, at standard-spindeludstyret på en maskine nødvendigvis er det bedste valg af interface.
Krav til maskinspindel
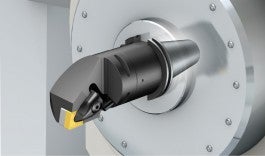
Når der ikke bearbejdes, skal maskinens spindel-interface muligøre hurtige vkt. skift. Men når der bearbejdes, er det afgørende, at forbindelsen mellem spindel og værktøj er solidt, også selv om skærekræfterne gør hvad de kan for at "rive" dem fra hinanden Det er vigtigt at have et interface der giver en god bøjningsstivhed og momentkapacitet.
- Bøjningsstivhed: Kræves for at få en stabil bearbejdningsproces med lange værktøjsudhæng eller kraftig belastning ved spåntagende bearbejdning
- Momentoverførsel: Operationer med store vkt. diametre er de mest følsomme. Den belastning der påføres i en bestemt afstand fra spindlens centerlinje (moment = kraft × radius) skal opvejes af et større medbringerkontaktareal
- Nøjagtig værktøjscenterposition: Ved drejning er det særlig vigtigt med en god gentagelsesnøjagtighed for at opnå en sikker produktion
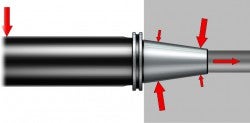
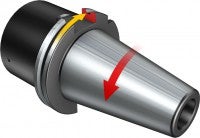
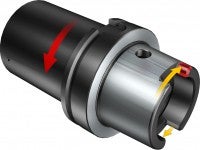
De koblingskarakteristika, der er afgørende for at kunne modstå store bøjningskræfter eller radiale skærekræfter er:
- Flangekontaktdiameter: Ved flangefladekontakt øges platformsarealet og reducerer skærekraftens løftestangsvirkning
- Fastspændingskraft: Jo større fastspændingskraft til at fastholde en kobling, jo større skærekraft skal der til at "rokke" koblingen
- Tværsnitsareal: En reduktion af værktøjsdiameteren i forhold til flangekontaktdiameteren vil nedsætte værktøjets stivhed
- Momentoverførsel: Som det fremgår helt klart i forbindelse med værktøjer med stor diameter og drejeværktøjer vil manglende evne til at modstå momentet betyde tab af centerhøjde og præcision
Maskinspindel interfacens historie
Maskinspindel interfacet er udviklet løbende i forbindelse med udviklingen af maskiner. Nogle af de centrale milepæle, der har påvirket ændringerne, er:
- NC-styring, der har givet mulighed for automatisk værktøjsskift og opbevaring af værktøjer. Det giver en stejl konus med brug af antræksbolt og griberspor
- Højere spindelomdrejningstal
- Multifunktionel bearbejdning, drejning, fræsning og boring med samme kobling
Den første, velkendte kobling var Morse-konus, der blev udvikling til boring helt tilbage i 1868. Derefter blev den stejle konus 7/24, også kaldet ISO-konus, introduceret i 1927. Griberspor og antræksbolte blev tilføjet til værktøjsskift i 60'erne, men med tre regionale varianter. MAS-BT i Asien, ISO/DIN i Europa og CAT-V i USA.
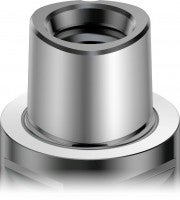
Ulempen ved den stejle konus er bøjningsstivhed og omdrejningskapacitet på grund af lavere spændekræfter og mangel på fladekontakt med spindelnæsen. Det førte til nye innovationer i 1990'erne med BIG-PLUS® (udviklet i Japan af BIG Daishowa ), HSK (udviklet i Tyskland af DIN-kommitteen) og Coromant Capto® (lanceret i 1990, som det eneste system, der fra dag ét er udviklet til alle applikationstyper: drejning, fræsning og boring).
Typer maskinspindelinterfaces
Nedenstående tabel viser de fire hovedtyper og udviklingen trin for trin fra den traditionelle stejle konus til Coromant Capto®. Alle koblinger, bortset fra BIG-PLUS®, er standardiseret som DIN, ISO eller ANSI.
Konusvinkel | Flangekontakt | Fastspændingsmetode | Momentoverførsel | |
Stejl konus | 16,26° | Nej | Antræksbolt | Medbringere på flangekontakt |
BIG-PLUS® | 16,26° | Ja | Antræksbolt | Medbringere på flangekontakt |
HSK-A | 5,7° | Ja | Indvendig segmentfastspænding | Medbringere på konus |
Coromant Capto® | 2,88° | Ja | Indvendig segmentfastspænding | Polygon |
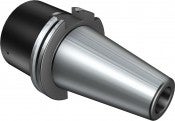
Grundholder til
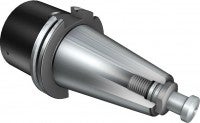
BIG-PLUS®
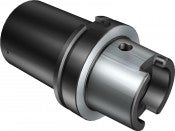
HSK-A
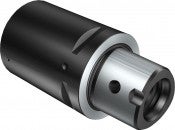
Coromant Capto®
Stejl konus 7/24
Konusvinklen er altid den samme til sejle konusser. Griberspor og gevind på antræksbolten kan variere. Fås som CAT, ISO, DIN og MAS BT.
BIG-PLUS®
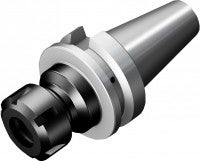
BIG-PLUS® er udviklet til bearbejdningscenterapplikationer. Konussen og gribersporet er det samme som på den traditionelle stejle konus, men i kraft af snævre tolerancer opnås der fladekontakt og dermed bedre bøjningsstivhed. En standard stejl konus-holder kan monteres i en BIG-PLUS®-spindel, men det kan ikke anbefales at blande. Fås som CAT, ISO, DIN og MAS BT.
HSK
HSK (DIN 69893) er udviklet til bearbejdningscentre. Den har flangekontakt og hul konus med segmentfastspænding, der fjerner behovet for antræksbolte. Medbringerne har forskellige konfigurationer afhængig af varianten, og i nogle tilfælde ingen til højhastighedsapplikationer.
- Type A: Generel bearbejdning, store bøjningsbelastninger og moderat moment, automatisk værktøjsskift
- Type B: Stationær applikation, moderate bøjningsbelastninger, højt moment, specialapplikationer, automatisk værktøjsskift
- Type C: Generel bearbejdning, store bøjningsbelastninger og moderat moment, manuelt værktøjsskift (ref. type A)
- Type D: Stationær applikation, moderate bøjningsbelastninger, højt moment, specialapplikationer, manuelt værktøjsskift (ref. type B)
- Type E: Højhastighedsapplikation, lette og hurtige spindler, lave bøjningsmomenter og lavt fastspændingsmoment, automatisk værktøjsskift, nem afbalancering
- Type F: Applikationer med moderate hastigheder, bearbejdning af bløde materialer, mellemstore bøjningsmomenter og lavt fastspændingsmoment, automatisk værktøjsskift, nem afbalancering
- Type T: Roterende og statiske applikationer med snævrere tolerancer i medbringersporet (til værktøjspositionering). Der er ikke behov for "hals", og det giver forbedrede bøjemomentegenskaber
Bemærk! De fleste maskiner, der kan bruge HSK-T-spindelkobling, kræver stadig en hals til automatisk værktøjsskift og magasiner, og det betyder, at der er behov for HSK A/C/T-værktøjer
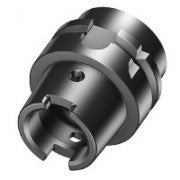
A
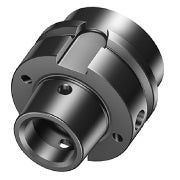
B
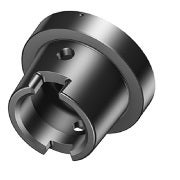
C
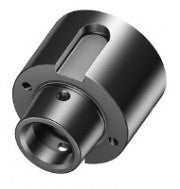
D
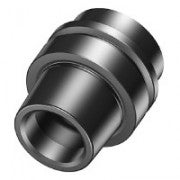
E
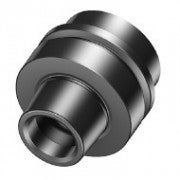
F
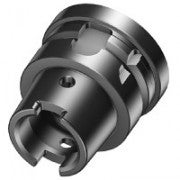
T
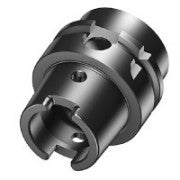
A/C/T
Coromant Capto®
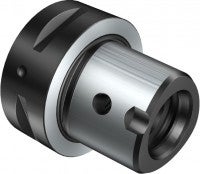
Coromant Capto® (ISO 26623) har samme fordele som både HSK og BIG-PLUS®, men har fjernet behovet for medbringere ved i stedet at blive drevet af en konisk polygon med flangekontakt. Det stærke koblingstværsnit giver plads til segmentfastspænding med den højeste fastspændingskraft, der sikrer uovertruffen bøjningsstivhed, momentoverførsel og centerpositionsnøjagtighed.
Den forbedrede radiale præcision og momentoverførsel var nødvendige for at dække kravene til tre applikationsområder:
- Maskinspindelinterface – bearbejdningscentre og karruseldrejebænke
- Modulær kobling – bearbejdningscentre
- Manuelt Quick Change-system – drejebænke
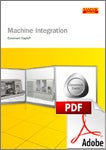
Coromant Capto® er den mest almindelige kobling til multitask-maskiner, da den kan bruges til både statiske (dreje-) og roterende (fræse-/bore-) applikationer.

Maskinspindelanbefalinger til forskellige maskintyper
Bearbejdningscentre (kun roterende)
Det anbefales at bruge en spindelkobling med fladekontakt. BIG-PLUS® og HSK-A har en tilstrækkelig god stabilitet til de fleste roterende applikationer i bearbejdningscentre. Til heavy duty-applikationer bør Coromant Capto® C10 overvejes før en større kobling som SK-A 125 eller SK60. Til applikationer med høje omdrejningstal skal man overveje at bruge HSK-E eller F.
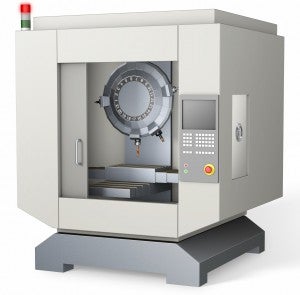
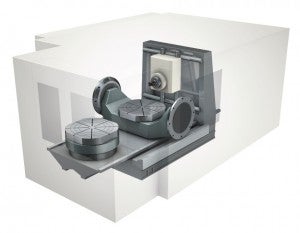
Multifunktionelle maskiner (statiske og roterende)
Coromant Capto® er den eneste kobling, der er kan leve op til kravene om moment og bøjningsstivhed i statiske og roterende applikationer.
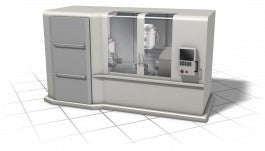

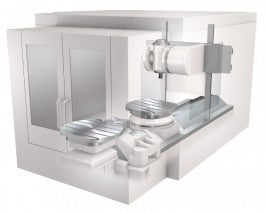
Der findes forskellige mekanismer til spindelfastspænding, lige som der er forskellige spindelinterface løsninger. Sandvik Coromant arbejder aktivt sammen med maskinproducenter om at understøtte integration af Coromant Capto® i deres maskiner. Vores primære fokus ligger på nedennævnte maskintyper og koblinger, hvor fordelene ved Coromant Capto® er størst.
C3 | C4 | C5 | C6 | C8 | C10 | |
Drejecenter | * | * | ||||
Heavy duty-drejebænk | ||||||
Karruseldrejebænk | ||||||
Multitask-maskine | ||||||
Bearbejdningscenter med drejning | ||||||
Bearbejdningscenter, heavy duty |
* Lange udborestænger på store drejecentre
Sammenligning af fastspændingskraft
Den indvendige segmentfastspænding der bruges til hule konuser (HSK og Coromant Capto®) kan yde en højere fastspændingskraft end antræksbolten kan yde på en stejl konus. Tabellen viser den fastspændingskraft, der påføres de respektive koblinger. Det øgede tværsnitsareal og koblingslængden på Coromant Capto® giver mulighed for meget højere fastspændingskræfter sammenlignet med HSK-A.
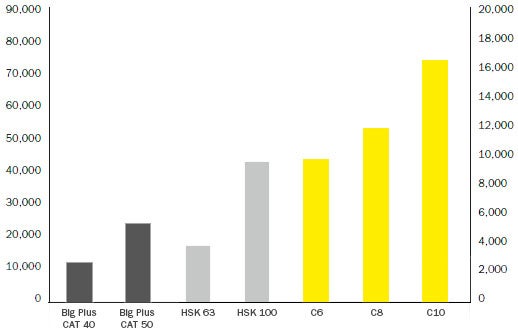
Kilder: HSK-håndbog, copyright 1999.
Big Daishowa (Big plus-spindelsystem)
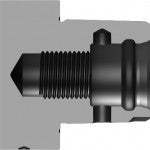
Coromant Capto®
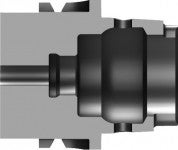
HSK-A
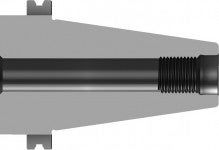
Stejl konus (SK)
Sammenligning af momentoverførsel og bøjningsstivhed
Stejl konus – medbringerne på en stor radius giver god kørsel i roterende applikationer
HSK-A – et lille kontaktareal med sporene på konussen i stedet for på flangediameteren (lille radius), så den anbefales ikke til applikationer med højt moment.
Coromant Capto® – til drejning er der behov for centerpositionsnøjagtighed, og her er polygondrevet bedst egnet.
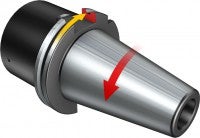
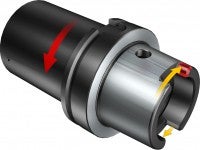
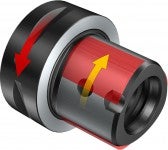
Koblingens størrelse giver begrænsninger af bøjningstivhed og maksimalt omdrejningstal. En stor kobling giver god stivhed men et lavere omdrejningstal, og en lille kobling giver mulighed for et højere omdrejningstal men en lavere bøjningsstivhed.
Diagrammet nedenfor viser begrænsingerne for de respektive koblinger på basis af teoretiske (FEA) beregninger af, hvornår fladekontakten mistes (bøjningsstivhed) og træthedsgrænsen nås (maks. moment).
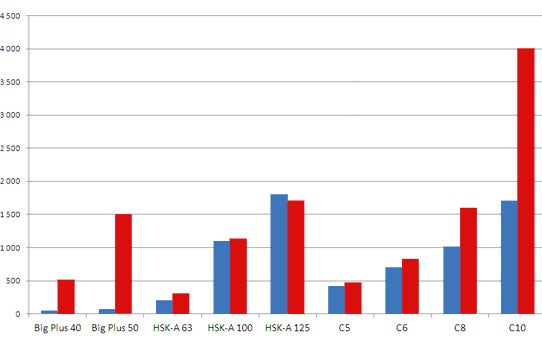
Blå: Maks. bøjningsmoment (Nm)
Rød: Maks. drejningsmoment (Nm) inden for udmattelsesgrænsen
BIG-PLUS® og HSK har en tilstrækkelig god stabilitet til de fleste roterende applikationer, men i multitask-maskiner er Coromant Capto® den eneste kobling, der er kan leve op til kravene om moment og bøjningsstivhed.
Kobling | Størrelse og fastspændingstype | Fastspændingskraft (trækbolt eller trækstang) | Maks. omdrejningstal (afhængigt af spindel og lejer) | |
N | lbs | |||
BIG-PLUS® ISO/CAT/BT 7/24 konus | Konus 40 | 12000 | 2703 | 16000 |
Konus 50 | 24000 | 5405 | 12000 | |
HSK-A | HSK-A 63 | 18000 | 4054 | 20500 |
HSK-A 100 | 45000 | 10135 | 12500 | |
HSK-A 125 | 70000 | 15766 | 9500 | |
Coromant Capto® | C5 | 32000 | 7207 | 28000 |
C6 | 41000 | 9234 | 20000 | |
C8 | 50000 | 11261 | 14000 | |
C10 | 70000 | 15766 | 10000 |
Statisk test, der sammenligner bøjningsstivhed og modstand over for drejningsmomenter
Det velanskrevne RWTH Aachen-universitet i Tyskland udførte en serie statiske tests i maskinlaboratoriet (WZL), hvor man sammenlignede bøjningsstivhed og momentmodstand for de forskellige spindelkoblinger.
Coromant Capto® blev målt med to fastspændingskræfter: den samme som for HSK-A, (22 kN for C6 og 50 kN for C10) og derefter den højere standard-fastspændingskraft (45 kN for C6 og 80 kN for C10).
Bøjningsstabilitet
Nedbøjning [mm/m]
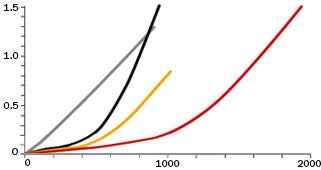
Bøjningsmoment [Nm]




C6- 45kN
C6- 22kN
HSK-A63-22kN
7/24 konus, str. 40-15kN
Bøjningsstabilitet
Nedbøjning [mm/m]
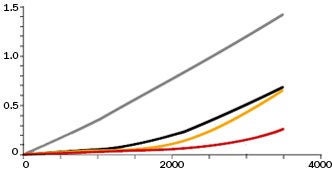
Bøjningsmoment [Nm]




C10-80kN
C10-50kN
HSK-A100-50kN
7/24 konus, str. 50-25kN
Resultaterne viser, at selv med samme fastspændingskraft som HSK-A havde den stærkere kobling forbedret bøjningsstivhed, men med den højere fastspændingskraft var påvirkningskraften 2,88 gange bedre for C6 end for HSK-A 63 og 2,15 gange bedre for C10 end for HSK-A 100.
Stabilt drejningsmoment
Nedbøjning [mm/m]
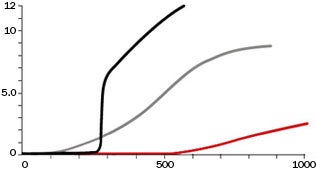
Torsionsmoment [Nm]



C6- 46kN
HSK-A63-22kN
7/24 konus, str. 40-15kN
Stabilt drejningsmoment
Nedbøjning [mm/m]
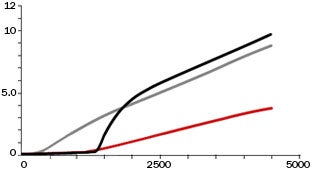
Torsionsmoment [Nm]



C10-50kN
HSK-A100-50kN
7/24 konus, str. 50-25kN
Grafikkerne viser, at Coromant Capto® C6 har 2,29 gange bedre modstand over for drejningsmomenter end HSK-A 63. Vridningsvinklen var 7,1 gange bedre. De tilsvarende tal for C10 var 1,85 gange bedre modstand over for drejningsmomenter og 4,0 gange bedre vridningsvinkel end HSK-A 100.