วิธีเพิ่มคุณภาพชิ้นงานในการกลึง
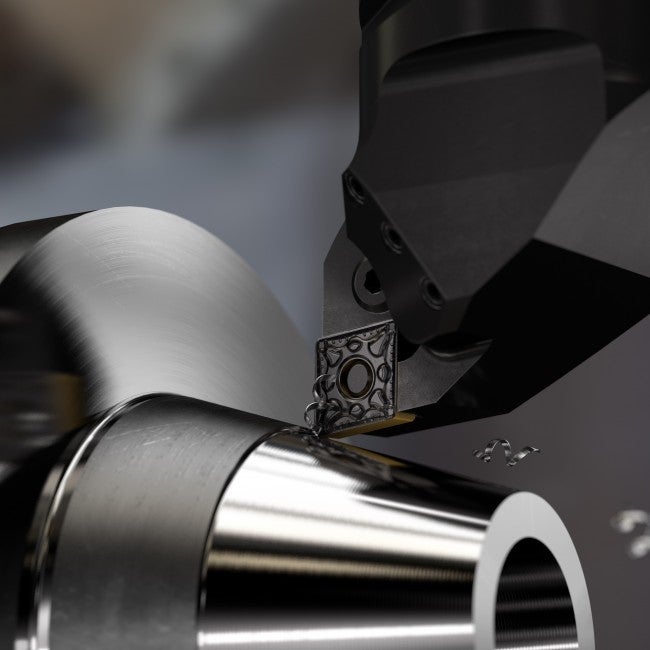
การควบคุมเศษเป็นปัจจัยที่มีความสำคัญสูงสุดประการหนึ่งที่ต้องคำนึงถึงเพื่อให้ได้ชิ้นงานกลึงที่มีคุณภาพสูง เลือกใช้ค่าการตัดที่ถูกต้องและปฏิบัติตามคำแนะนำการใช้งานของเราเพื่อให้ได้ชิ้นงานที่มีคุณภาพ
การควบคุมเศษอย่างมีประสิทธิภาพ
การควบคุมเศษเป็นปัจจัยสำคัญประการหนึ่งในการกลึง โดยมีตัวเลือกในการหักเศษสามแบบ ได้แก่:
- การหักอัตโนมัติ (เช่น เหล็กหล่อเทา)
- การหักกระทบเครื่องมือ
- การหักกระทบชิ้นงาน
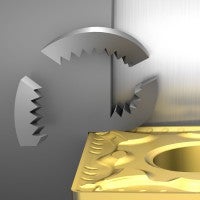
การหักอัตโนมัติ
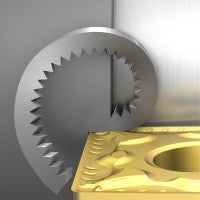
การหักกระทบเครื่องมือ
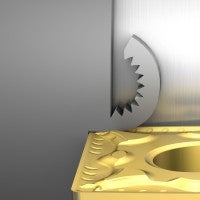
การหักกระทบชิ้นงาน
ปัจจัยที่มีผลต่อการหักเศษ
- หน้าลายเม็ดมีด: เศษจะเปิดออกหรือถูกบีบอัดมากขึ้นตามความกว้างของร่องคายเศษและการออกแบบรูปทรงขนาดเล็กและขนาดใหญ่
- รัศมีปลายคมตัด: รัศมีปลายคมตัดที่เล็กกว่าจะควบคุมเศษได้มากกว่ารัศมีปลายคมตัดที่ใหญ่กว่า
- มุมเข้างาน (นำ): เศษจะถูกพาไปในทิศทางต่างๆ ขึ้นอยู่กับมุมเข้างาน ได้แก่ ทิศทางเข้าหางานหรือออกจากงาน
- ระยะกินลึก: ระยะกินลึกที่กว้างจะส่งผลต่อการหักเศษ ทำให้มีแรงหักและคายเศษมากขึ้น ทั้งนี้ขึ้นอยู่กับวัสดุชิ้นงาน
- อัตราป้อน: โดยทั่วไปอัตราป้อนที่สูงจะทำให้เศษแข็งขึ้น ในบางกรณีอาจช่วยในการหักเศษและการควบคุมเศษ
- ความเร็วตัด: การเปลี่ยนแปลงความเร็วตัดอาจส่งผลต่อประสิทธิภาพในการหักเศษ
- วัสดุ: โดยทั่วไปวัสดุที่เกิดเศษสั้น (เช่น เหล็กหล่อ) จะตัดเฉือนได้ง่าย สำหรับวัสดุที่มีความแข็งแรงทางกลและความต้านทานการเปลี่ยนรูป (แนวโน้มที่ของแข็งจะเกิดการเคลื่อนที่หรือเปลี่ยนแปลงรูปร่างอย่างช้าๆ ภายใต้แรงเค้น เช่น อินโคเนล) ดีเยี่ยมนั้น การหักเศษถือเป็นปัจจัยสำคัญที่ต้องพิจารณา
ค่าการตัดสำหรับการกลึง
การเลือกใช้ความเร็วและอัตราป้อนที่ถูกต้องสำหรับการกลึงนั้น จะต้องคำนึงถึงเครื่องจักร เครื่องมือ เม็ดมีด และวัสดุเสมอ
- เริ่มการทำงานโดยใช้อัตราป้อนงานต่ำ เพื่อให้เม็ดมีดทำงานได้อย่างมั่นคงและได้คุณภาพผิวงานตามที่ต้องการ จากนั้นจึงเพิ่มอัตราป้อนงานเพื่อเพิ่มประสิทธิภาพการหักเศษ
- ทำงานที่ระยะกินลึกมากกว่ารัศมีปลายคมตัด วิธีดังกล่าวจะช่วยลดการเบี่ยงเบนในแนวรัศมีของเม็ดมีด ซึ่งมีความสำคัญต่อการตัดเฉือนด้านใน
- การเลือกความเร็วตัดต่ำเกินไปจะส่งผลให้อายุการใช้งานของเครื่องมือสั้นลง ควรใช้ค่าความเร็วตัด vc ม./นาที (ฟุต/นาที) ที่แนะนำทุกครั้ง
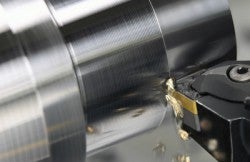
ทำให้ชิ้นงานกลึงมีคุณภาพดียิ่งขึ้นโดยใช้น้ำหล่อเย็น
การใช้น้ำหล่อเย็นอย่างถูกต้องจะช่วยให้กระบวนการทำงานมีความปลอดภัยมากขึ้น รวมถึงช่วยเพิ่มประสิทธิภาพการทำงานของเครื่องมือและได้ชิ้นงานที่มีคุณภาพดียิ่งขึ้น สิ่งที่ควรพิจารณาเมื่อใช้น้ำหล่อเย็นมีดังนี้
- ขอแนะนำให้ใช้เครื่องมือที่มีระบบน้ำหล่อเย็นความเที่ยงตรงสูงในการเก็บผิวละเอียด
- แรงดันน้ำหล่อเย็นที่ต้องใช้ในการหักเศษขึ้นอยู่กับเส้นผ่านศูนย์กลางของหัวฉีด (ช่องออก) วัสดุที่ทำการตัดเฉือน ระยะกินลึก และอัตราป้อน
- อัตราการไหลของน้ำหล่อเย็นที่เหมาะสมจะขึ้นอยู่กับแรงดันและพื้นที่จายน้ำหล่อเย็นทั้งหมดของช่องจายน้ำหล่อเย็น
- ขอแนะนำให้ใช้ระบบจายน้ำหล่อเย็นด้านล่างเสมอในการตัดเฉือนปานกลางและหยาบ
- สำหรับการทำงานเก็บผิวละเอียด ขอแนะนำให้ใช้ทั้งน้ำหล่อเย็นความเที่ยงตรงสูงและน้ำหล่อเย็นด้านล่าง
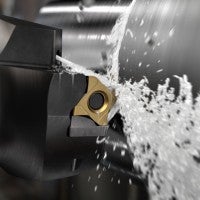
จัดการกับทุกความท้าทายด้วยการปรับใช้ระบบน้ำหล่อเย็นอย่างถูกต้อง
- ปัญหาเกี่ยวกับการควบคุมเศษ: ใช้ระบบจายน้ำหล่อเย็นด้านบน
- ปัญหาเกี่ยวกับขนาด: โดยปกติแล้วมักเกิดจากอุณหภูมิที่สูง ให้ใช้ระบบจายน้ำหล่อเย็นทั้งด้านบนและด้านล่าง และใช้แรงดันให้สูงที่สุด
- คุณภาพผิวงานไม่ดี: ใช้ระบบจายน้ำหล่อเย็นด้านหากเกิดข้อผิดพลาดขึ้นจากเศษวัสดุ
- ไม่สามารถคาดการณ์อายุการใช้งานเครื่องมือในการกลึงหยาบ: ใช้เฉพาะระบบจายน้ำหล่อเย็นด้านล่าง
- ไม่สามารถคาดการณ์อายุการใช้งานเครื่องมือในการเก็บผิวละเอียด: ใช้ระบบจายน้ำหล่อเย็นทั้งด้านบนและด้านล่าง
- ประสิทธิภาพการคายเศษต่ำสำหรับการกลึงใน: ใช้ระบบจายน้ำหล่อเย็นทั้งด้านบนและด้านล่าง และใช้แรงดันให้สูงที่สุด
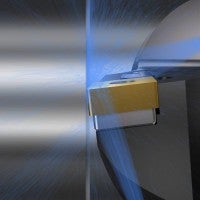
วิธีการใช้ระบบน้ำหล่อเย็นและน้ำหล่อเย็นสำหรับการกลึง
วิธีเพิ่มคุณภาพผิวสำเร็จสำหรับชิ้นงานกลึง
หลักเกณฑ์ทั่วไปสำหรับผิวสำเร็จ:
- โดยทั่วไปแล้ว การใช้ความเร็วตัดสูงขึ้นจะช่วยให้สามารถปรับปรุงคุณภาพของผิวสำเร็จให้ดีขึ้นได้
- รูปทรงเม็ดมีด (มุมคายเป็นกลาง บวก และลบ รวมถึงมุมหลบเป็นบวก) จะมีผลต่อผิวสำเร็จ
- การเลือกเกรดเม็ดมีดมีผลต่อผิวสำเร็จ
- ในกรณีที่มีโอกาสเกิดการสั่นสะท้าน ให้เลือกปลายคมตัดที่มีรัศมีเล็กลง
เม็ดมีดไวเปอร์
เม็ดมีดไวเปอร์มีประสิทธิภาพในการกลึงชิ้นงานด้วยความเร็วสูง โดยไม่ลดทอนคุณภาพผิวสำเร็จหรือความสามารถในการหักเศษ
คำแนะนำทั่วไปมีดังนี้ อัตราป้อนงานสองเท่า ให้คุณภาพผิวสำเร็จคงเดิม อัตราป้อนงานคงเดิม ให้คุณภาพผิวสำเร็จดีขึ้นสองเท่า
เม็ดมีดไวเปอร์ได้รับการออกแบบเพื่อให้ผิวงานที่เกิดจากการป้อนเม็ดมีดตลอดชิ้นงานมีความเรียบเนียน และคมตัดของเม็ดมีดไวเปอร์โดยส่วนใหญ่ออกแบบสำหรับการกลึงเป็นเส้นตรงและการกลึงปาดโดยเฉพาะ
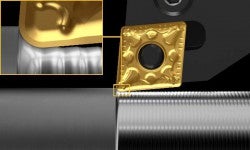
มุมมนมาตรฐาน
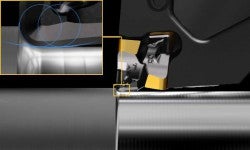
มุมมนไวเปอร์
การเปรียบเทียบเม็ดมีดขนาดมาตรฐานกับเม็ดมีดไวเปอร์ตามอัตราป้อน
หมายเหตุ! ค่าทั้งหมดสำหรับมุมมนมาตรฐานเป็นการคำนวณตามหลักทฤษฎี ค่าสำหรับมุมมนไวเปอร์อ้างอิงตามค่าที่ได้จากการทดลองกับเหล็กเหนียวอัลลอยต่ำ
อัตราป้อน มม. (นิ้ว) | RE มาตรฐาน 0.4 มม. (0.016 นิ้ว) Ra µm (µinch) | ไวเปอร์ (-WF/-WM) RE 0.4 มม. (0.016 นิ้ว) Ra µm (µinch) | RE มาตรฐาน 0.8 มม. (0.031 นิ้ว) Ra µm (µinch) | ไวเปอร์ (-WMX) RE 0.8 มม. (0.031 นิ้ว) Ra µm (µinch) |
0.07 (0.003) | 0.31 (12.4) | 0.30 (12.0) | - | - |
0.10 (0.004) | 0.63 (25.2) | 0.32 (12.8) | 0.31 (12.4) | - |
0.12 (0.005) | 0.90 (36.0) | 0.45 (18.0) | 0.45 (18.0) | - |
0.15 (0.006) | 1.41 (56.4) | 0.70 (28.0) | 0.70 (28.0) | 0.25 (10.0) |
0.18 (0.007) | 2.03 (80.8) | 1.00 (40.0) | 1.00 (40.4) | 0.30 (12.0) |
0.20 (0.008) | 2.50 (100.0) | 1.25 (50.0) | 1.25 (50.0) | 0.35 (14.0) |
0.22 (0.009) | 3.48 (139.2) | 1.74 (69.6) | 1.74 (69.6) | 0.40 (16.0) |
0.25 (0.010) | - | - | 2.25 (90.0) | 0.45 (18.0) |
0.28 (0.011) | - | - | 2.82 (112.8) | 0.50 (20.0) |
0.30 (0.012) | - | - | 3.23 (129.2) | 0.55 (22.0) |
0.35 (0.014) | - | - | 4.40 (176.0) | 0.60 (24.0) |
0.40 (0.016) | - | - | 5.75 (230.0) | 0.70 (28.0) |
0.45 (0.018) | - | - | 8.54 (341.6) | 1.1 (44.0) |
0.50 (0.020) | - | - | 10.55 (422.0) | 1.3 (51.0) |
อัตราป้อน มม. (นิ้ว) | RE มาตรฐาน 1.2 มม. (0.047 นิ้ว) Ra µm (µinch) | ไวเปอร์ (-WMX) RE 1.2 มม. (0.047 นิ้ว) Ra µm (µinch) | RE มาตรฐาน 1.6 มม. (0.063 นิ้ว) Ra µm (µinch) | ไวเปอร (-WMX) RE 1.6 มม. 1) (0.063 นิ้ว) Ra µm (µinch) |
0.15 (0.006) | 0.47 (18.8) | - | - | - |
0.18 (0.007) | 0.68 (27.2) | - | - | - |
0.20 (0.008) | 0.83 (33.3) | 0.3 (12.0) | 0.63 (25.2) | - |
0.22 (0.009) | 1.16 (46.4) | 0.3 (12.0) | 0.87 (34.8) | - |
0.25 (0.010) | 1.50 (60.0) | 0.4 (16.0) | 1.12 (44.8) | 0.3 (12.0) |
0.28 (0.011) | 1.88 (75.2) | 0.4 (16.0) | 1.41 (56.4) | 0.35 (14.0) |
0.30 (0.012) | 2.16 (86.4) | 0.4 (16.0) | 1.62 (64.8) | 0.4 (16.0) |
0.35 (0.014) | 2.93 (117.2) | 0.5 (20.0) | 2.20 (88.0) | 0.4 (16.0) |
0.40 (0.016) | 3.83 (153.2) | 0.65 (26.0) | 2.88 (115.2) | 0.4 (16.0) |
0.45 (0.018) | 5.70 (228.0) | 0.85 (34.0) | 4.27 (170.8) | 0.5 (20.0) |
0.50 (0.020) | 7.03 (281.2) | 1.15 (46.0) | 5.27 (210.8) | 0.7 (28.0) |
0.55 (0.022) | 8.51 (340.4) | 1.2 (48.0) | 6.38 (255.2) | 0.9 (36.0) |
0.60 (0.024) | 10.13 (405.2) | 1.3 (52.0) | 7.59 (303.6) | 1.05 (42.0) |
0.65 (0.026) | - | - | 8.91 (356.4) | 1.25 (50.0) |
0.70 (0.028) | - | - | 10.31 (413.6) | 1.3 (52.0) |
0.85 (0.033) | - | - | 15.24 (609.6) | 1.9 (76.0) |
0.90 (0.035) | - | - | 17.09 (683.0) | 2.1 (84.0) |
- ค่าสำหรับมมมน 1.6 มม. (0.06 นิ้ว) อิงตามเม็ดมีด DNMX
คำแนะนำการใช้งานเครื่องมือกลึงนอก
ชิ้นงานที่มีโอกาสเกิดการสั่นสะท้าน
การกลึงตัดรอบเดียว (เช่น ท่อ)
ขอแนะนำให้ตัดเฉือนทั้งหมดในรอบเดียวเพื่อส่งแรงไปยังหัวจับ/สปินเดลในทิศทางแนวแกน
ตัวอย่าง: เส้นผ่านศูนย์กลางด้านนอก (OD) 25 มม. (0.984 นิ้ว) เส้นผ่านศูนย์กลางด้านใน (ID) 15 มม. (0.590 นิ้ว) ระยะกินลึก ap = 4.3 มม. (0.169 นิ้ว) ส่งผลให้ผนังมีความหนา = 0.7 มม. (0.028 นิ้ว)
OD = 25 มม. (0.984 นิ้ว) | ap 4.3 มม. (0.169 นิ้ว) |
![]() | ID = 15 มม. (0.590 นิ้ว) |
สามารถใช้มุมเข้ามาใกล้เคียง 90° (มุมนำ 0°) เพื่อส่งแรงตัดไปในทิศแนวแกน ซึ่งจะทำให้เกิดแรงโก่งตัวน้อยที่สุดบนชิ้นงาน
การกลึงตัดสองรอบ
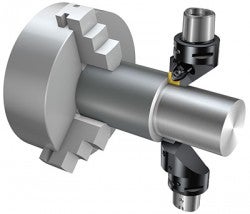
การตัดเฉือนของป้อมมีดชุดบนและชุดล่างที่ประสานเป็นจังหวะเดียวกันจะช่วยรักษาแรงตัดในแนวรัศมีให้สม่ำเสมอ และป้องกันไม่ให้เกิดการสั่นสะเทือนและการโก่งตัวของชิ้นงาน
ชิ้นงานผอม/มีผนังบาง
สิ่งที่ควรพิจารณาเมื่อทำการตัดเฉือนชิ้นงานผอม/มีผนังบางมีดังนี้
- ใช้มุมเข้ามาใกล้เคียง 90° (มุมนำ 0°) แม้จะมีความเปลี่ยนแปลงเพียงน้อย (ตั้งแต่มุมองศา 91/-1 ถึง 95/-5) ก็จะส่งผลต่อทิศทางแรงตัดระหว่างการตัดเฉือนด้วยเช่นกัน
- ระยะกินลึก ap ควรใหญ่กว่ารัศมีปลายคมตัด, RE ขนาด ap ที่ใหญ่จะช่วยเพิ่มแรงในแนวแกน Fz และลดแรงตัดในแนวรัศมี Fx ซึ่งทำให้เกิดการสั่นสะเทือน
- ใช้เม็ดมีดที่มีคมตัดที่คมและรัศมีปลายคมตัด RE ขนาดเล็กเพื่อให้เกิดแรงตัดที่ต่ำ
- พิจารณาเลือกใช้เกรด Cermet หรือ PVD เพื่อเพิ่มความต้านทานการสึกหรอ และใช้คมตัดเม็ดมีดที่คมซึ่งเหมาะสำหรับการใช้งานในรูปแบบนี้
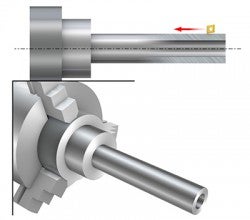
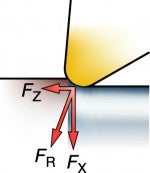
การกัดบ่าฉาก/การกลึงบ่า
ปฏิบัติตามขั้นตอน 1-5 เพื่อป้องกันไม่ให้คมตัดเม็ดมีดได้รับความเสียหาย วิธีการทำงานนี้ส่งผลดีต่อเม็ดมีดเคลือบผิว CVD และยังอาจช่วยลดโอกาสการแตกหักได้อย่างมาก
ขั้นตอน 1-4:
รักษาระยะระหว่างแต่ละขั้นตอน (1-4) ให้เท่ากับอัตราป้อนงานเพื่อป้องกันเศษติด
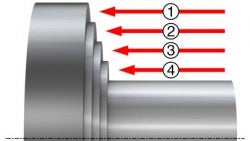
ขั้นตอน 5:
ควรทำการตัดเฉือนขั้นสุดท้ายให้เสร็จภายในการตัดแนวตั้งเพียงครั้งเดียว โดยเริ่มจากเส้นผ่านศูนย์กลางด้านนอกไปยังเส้นผ่านศูนย์กลางด้านใน
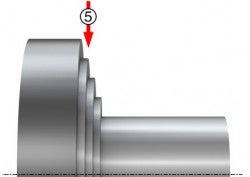
การตัดเฉือนจากเส้นผ่านศูนย์กลางด้านในไปยังเส้นผ่านศูนย์กลางด้านนอกขณะปาดหน้าบ่างานอาจก่อให้เกิดปัญหาเศษพันรอบรัศมีของเม็ดมีดได้ การเปลี่ยนทางเดินเครื่องมือจะสามารถช่วยกลับทิศทางของเศษและแก้ปัญหาในส่วนนี้ได้
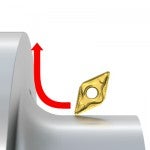
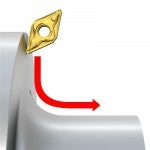
การกลึงปาด
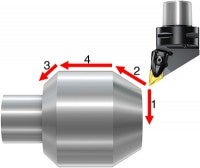
เริ่มจากการกลึงปาดหน้า (1) และการลบมุม (2) หากเป็นไปได้และในกรณีที่ชิ้นงานมีรูปทรงที่เหมาะสม ขอแนะนำให้ตัดเฉือนลบมุม (3) การกลึงตามยาว (4) เป็นขั้นตอนการทำงานสุดท้าย และเม็ดมีดจะมีมุมเข้ามาและมุมออกงานที่นุ่มนวลขณะตัดเฉือน
ควรทำการกลึงปาดเป็นขั้นตอนแรกเพื่อปรับตั้งจุดอ้างอิงบนชิ้นงานสำหรับรอบการกลึงครั้งต่อไป
การเกิดเศษคับเป็นปัญหาที่พบได้บ่อยในขั้นตอนการกลึงครั้งสุดท้าย (ขณะออกจากชิ้นงาน) การคงขั้นตอนการลบมุมหรือความโค้ง (กลึงโค้งลบขอบมุม) อาจช่วยลดหรือป้องกันการเกิดเศษคับได้
การลบมุมบนชิ้นงานจะช่วยให้การเข้ามาของคมตัดเม็ดมีดมีความนุ่มนวลขึ้น (ทั้งในการกลึงปาดและการกลึงตามยาว)
การตัดกระแทก

ขณะคว้านกระแทก:
- ใช้เกรด PVD เพื่อให้คมตัดมีความเหนียวมากขึ้นในงานกลึงกระแทกแบบรวดเร็ว เช่น แทงหกเหลี่ยม
- ใช้เกรด CVD แบบเหนียวเพื่อให้มีความเหนียวโดยรวมมากขึ้นสำหรับชิ้นงานขนาดใหญ่และการกลึงกระแทกรุนแรง
- พิจารณาเลือกใช้ร่องหักเศษที่แข็งแรงเพื่อเพิ่มความทนทานต่อการกะเทาะ
- ควรปิดระบบน้ำหล่อเย็นเพื่อไม่ให้เกิดการแตกร้าวเนื่องจากความร้อน
การเก็บผิวละเอียดชิ้นงานด้วยการกลึงรองบ่า (การเจียขอบนอก)
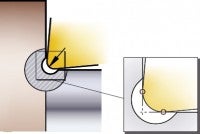
ใช้รัศมีปลายคมตัด RE ที่ใหญ่ที่สุดเท่าที่จะเป็นไปได้สำหรับการกลึงปาดหน้าและตามแนวยาวเพื่อให้ได้:
- คมตัดแข็งแรงและเชื่อถือได้มากขึ้น
- คุณภาพผิวงานดี
- สถานการณ์ที่ควรใช้อัตราป้อนสูง
ห้ามใช้ความกว้างของการกลึงรองบ่าเกินขนาด และทำการกลึงรองบ่าเป็นขั้นตอนสุดท้ายเพื่อขจัดคับ
คำแนะนำการใช้งานเครื่องมือกลึงใน
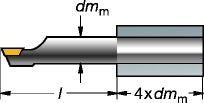
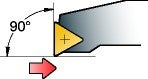
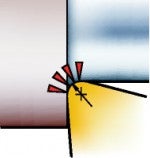
- เลือกเส้นผ่านศูนย์กลางของด้ามที่ใหญ่ที่สุด ทั้งนี้ต้องแน่ใจว่ามีพื้นที่ว่างเพียงพอสำหรับการคายเศษระหว่างด้ามกับรูด้วย
- ต้องตรวจดูให้แน่ใจว่าการคายเศษเพียงพอกับค่าการตัดที่ใช้ และเศษมีลักษณะที่เหมาะสม
- เลือกใช้ระยะยื่นที่เล็กที่สุด ทั้งนี้ต้องแน่ใจว่าด้ามกลึงคว้านมีขนาดยาวพอที่จะใช้ระยะจับยึดที่แนะนำได้ด้วย ไม่ควรใช้ระยะจับยึดต่ำกว่าสามเท่าของเส้นผ่านศูนย์กลาง
- ใช้ด้ามกลึงคว้านลดแรงสั่นสะเทือนหากมีชิ้นส่วนที่ไวต่อการสั่นสะเทือน
- เลือกมุมเข้ามาชิดกับมุม 90° (มุมนำ 0°) ให้มากที่สุดเพื่อส่งแรงตัดไปตามด้ามกลึงคว้าน ไม่ควรใช้มุมเข้ามาเล็กกว่า 75° (มุมนำ -15°)
- อันดับแรก เม็ดมีดแบบถอดเปลี่ยนได้ควรมีมุมบวกและมีรูปทรงเม็ดมีดเป็นมุมบวก เพื่อลดโอกาสที่เครื่องมือจะเบี่ยงเบนออกจากชิ้นงาน
- เลือกรัศมีปลายคมตัดของเม็ดมีดที่เล็กกว่าระยะกินลึก
- ในกรณีที่หน้าสัมผัสคมตัดไม่เพียงพอ อาจทำให้การสั่นสะเทือนจากแรงเสียดสีในระหว่างการตัดเพิ่มขึ้นได้ เลือกหน้าสัมผัสคมตัดที่ใหญ่กว่ารัศมีปลายคมตัดเพื่อให้กระบวนการตัดมีประสิทธิภาพ
- หน้าสัมผัสคมตัดที่มากเกินไป (อัตราป้อนและ/หรือระยะกินลึกมาก) อาจทำให้การสั่นสะเทือนเพิ่มขึ้นได้เมื่อมีการเบี่ยงทิศทางของเครื่องมือ
- โดยปกติแล้ว เม็ดมีดที่ไม่มีการเคลือบผิวหรือมีการเคลือบผิวแบบบางจะให้แรงตัดที่ต่ำกว่าเมื่อเทียบกับเม็ดมีดที่มีการเคลือบผิวหนา ลักษณะข้างต้นมีความสำคัญมากเมื่อความยาวของเครื่องมือกับเส้นผ่านศูนย์กลางมีขนาดใหญ่ โดยทั่วไปคมตัดที่แหลมจะลดโอกาสเกิดการสั่นสะเทือน จึงทำให้ริมคุณภาพดียิ่งขึ้น
- หน้าลายที่มีร่องหักเศษแบบเปิดเป็นผลดีต่อการกลึงในมากกว่า
- ทั้งนี้ควรพิจารณาเลือกใช้เกรดเม็ดมีดที่มีความเหนียวระดับสูงขึ้นสำหรับการทำงานบางอย่างที่ต้องการลดความเสี่ยงของการเกิดเศษติดหรือการสั่นสะเทือน
- พิจารณาเลือกใช้ทางเดินของเครื่องมือตัดแบบอื่นหากจำเป็นต้องปรับปรุงลักษณะของเศษให้ดีขึ้น
คำแนะนำการใช้งานเครื่องมือกลึงชิ้นงานที่ผ่านการชุบแข็ง
นอกจากคำแนะนำทั่วไปสำหรับการกลึงแล้ว ยังมีปัจจัยสำคัญบางประการที่ต้องคำนึงถึงเมื่อต้องใช้เครื่องมือกลึงชิ้นงานที่ผ่านการชุบแข็ง (ในกรณีที่กระบวนการผลิตมีการเตรียมชิ้นงานก่อนทำการชุบแข็ง):
- ป้องกันการเกิดเศษคราบ
- คงพิกัดความเผื่อแคบ
- ลบมุมและทำให้เกิดรัศมีก่อนชุบแข็ง
- ห้ามเข้าออกจากการตัดโดยฉับพลัน
- เข้าออกโดยการเดินหัวกัดเป็นแนวโค้งเข้าออก
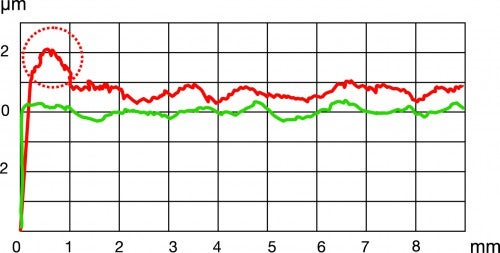
ค่าการวัดผิวงาน
แกน X: ความยาวที่เหมาะสม
แกน Y: ค่าเบี่ยงเบนของเส้นผ่านศูนย์กลาง
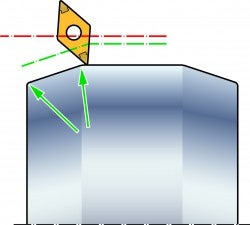
ผิวงานที่ต้องการควบคุม
การปรับตั้ง
- ความมั่นคงของเครื่องจักร การจับยึด และการวางแนวของชิ้นงานที่มีประสิทธิภาพนับเป็นปัจจัยสำคัญยิ่ง
- อัตราส่วนความยาวต่อเส้นผ่านศูนย์กลางของชิ้นงานที่แนะนำโดยปกติต้องไม่เกิน 2:1 ซึ่งเป็นอัตราที่ยอมรับได้สำหรับชิ้นงานที่มีการรองรับปลายไว้ด้านหนึ่งเท่านั้น หากมีการรองรับน้ำหนักยันศูนย์ท้ายเพิ่ม สามารถเพิ่มอัตราส่วนดังกล่าวได้
- อย่างไรก็ตาม การออกแบบหัวจับและยันศูนย์ท้ายแบบสมมาตรด้วยความร้อนจะทำให้ได้ขนาดที่สม่ำเสมอกว่าปกติ
- ใช้ระบบจับยึด Coromant Capto®
- ลดระยะยันทั้งหมดเพื่อให้ระบบมีความแข็งแรงสูงสุด
- พิจารณาเลือกใช้ด้ามกลึงคว้านคาร์ไบด์และ Silent Tools สำหรับการกลึงใน
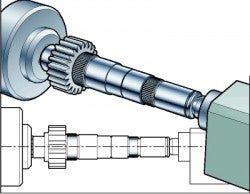
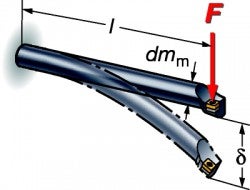
รูปทรงเม็ดมีดในระดับเล็กมาก
โดยทั่วไป การเตรียมคมตัดสำหรับเม็ดมีด CBN มีสองประเภท ได้แก่ คมตัด S และคมตัด T
- คมตัด S: มีขอบคมตัดที่แข็งแรงที่สุด ทนต่อการกะเทาะในระดับจุลภาคและมั่นใจได้ถึงคุณภาพผิวงานที่มีความสม่ำเสมอ
- คมตัด T: ให้ผิวสำเร็จคุณภาพดีเยี่ยมในการตัดที่ต่อเนื่อง และลดการเกิดเศษคราบในการตัดกระแทก ใช้แรงตัดน้อยลง
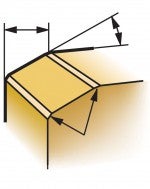
คมตัด S
ลบมุมโดยเจียรลบคมเล็กน้อย
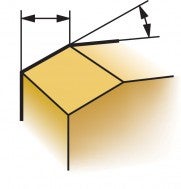
คมตัด T
ลบมุมโดยไม่เจียรลบคม
รูปทรงมุมเม็ดมีด
- หากสภาพการทำงานมีความมั่นคง ให้เลือกใช้รูปทรงไวเปอร์ทุกครั้ง เพื่อให้ได้ผิวสำเร็จที่มีคุณภาพสูงสุด
- ใช้เม็ดมีดที่มีมุมเข้างานต่ำเมื่อต้องการเพิ่มประสิทธิภาพการผลิต
- ควรใช้เม็ดมีดที่มีรัศมีปกติในกรณีที่สภาพการทำงานไม่มีความมั่นคงมากนัก (ชิ้นงานทรงผอม เป็นต้น) เท่านั้น
การตัดเฉือนแบบเปียกหรือแบบแห้ง
การกลึงชิ้นงานที่ผ่านการชุบแข็งโดยไม่ใช้น้ำหล่อเย็นเป็นสภาพการทำงานที่เหมาะสมและเอื้อต่อการทำงาน ทั้งเม็ดมีด CBN และเม็ดมีดเซรามิกสามารถทนต่ออุณหภูมิในการตัดเฉือนได้สูง จึงช่วยลดต้นทุนและขจัดปัญหาเกี่ยวกับน้ำหล่อเย็นได้
ในการใช้งานบางประเภท อาจต้องใช้น้ำหล่อเย็นเพื่อควบคุมความเสถียรทางความร้อนของชิ้นงาน เป็นต้น ในกรณีดังกล่าว ต้องแน่ใจว่ามีการจ่ายน้ำหล่อเย็นอย่างต่อเนื่องตลอดการกลึง
โดยทั่วไป ความร้อนที่เกิดขึ้นขณะตัดเฉือนจะกระจายไปยังเศษ (80%) ชิ้นงาน (10%) และเม็ดมีด (10%) ด้วยเหตุนี้ การคายเศษออกจากบริเวณคมตัดจึงมีความสำคัญอย่างมาก
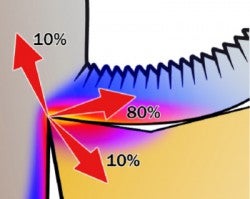
ค่าการตัดและการสึกหรอ
ความร้อนสูงบริเวณคมตัดจะทำให้แรงตัดลดลง ความเร็วตัดที่ต่ำเกินไปจึงทำให้เกิดความร้อนน้อย และทำให้เม็ดมีดแตกหักได้
การสึกหรอเป็นหลุมด้านบนจะค่อยๆ ส่งผลต่อความแข็งแรงของเม็ดมีด แต่จะไม่มีผลต่อผิวสำเร็จมากนัก ในทางตรงข้าม การสึกหรอด้านหน้าจะส่งผลต่อพิกัดความเผื่อของขนาดทีละน้อย
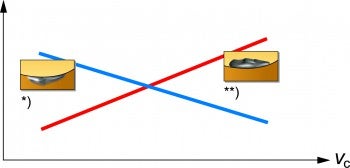
อายุการใช้งานเครื่องมือเป็นส่วนหนึ่งที่มีผลต่อระดับการสึกหรอ *) การสึกหรอด้านหน้า **) การสึกหรอเป็นหลุมด้านบน
เกณฑ์สำหรับการเปลี่ยนเม็ดมีด
ผิวสำเร็จที่กำหนดไว้ล่วงหน้า (B) เป็นเกณฑ์ที่มักใช้ในการเปลี่ยนเม็ดมีด โดยจะทำการวัดผิวสำเร็จโดยอัตโนมัติเมื่อแยกสถาน และระบุค่าคุณภาพผิวสำเร็จตามที่กำหนดไว้
กำหนดจำนวนชิ้นงานที่จะใช้เป็นเกณฑ์สำหรับการเปลี่ยนเม็ดมีดไว้ล่วงหน้า (A) เพื่อให้มีประสิทธิภาพการทำงานที่มั่นคงยิ่งกว่าเดิม ค่าดังกล่าวควรน้อยกว่าผิวสำเร็จที่กำหนดไว้ล่วงหน้า 10–20% โดยจะกำหนดตัวเลขที่แน่นอนแล้วแต่กรณีไป
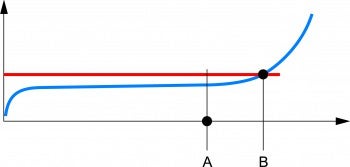
A: จำนวนชิ้นงานที่กำหนดไว้ล่วงหน้า
B: ผิวสำเร็จที่กำหนดไว้ล่วงหน้า
แกน X: จำนวนชิ้นงาน
แกน Y: ผิวสำเร็จ
เส้นสีน้ำเงิน: การสึกหรอของเม็ดมีด
เส้นสีแดง: ค่า Ra/Rz สูงสุด
แนวคิดตัดรอบเดียว
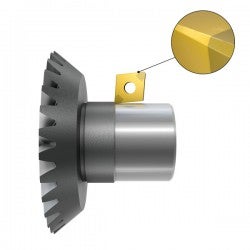
"การขจัดเนื้อโลหะ" ในการตัดรอบเดียวเป็นแนวคิดที่เหมาะสำหรับการกลึงนอกและการกลึงใน การปรับตั้งระบบให้มีความมั่นคงมีความสำคัญ และระยะยันของเครื่องมือไม่ควรเกินเส้นผ่านศูนย์กลางด้ามในการกลึงใน (1×D) ขอแนะนำให้เลือกใช้เม็ดมีดเจียรลบคมเล็กน้อยแบบลบมุม โดยใช้ความเร็วและอัตราป้อนระดับปานกลางเพื่อให้การตัดเฉือนมีประสิทธิภาพ
ข้อดี
- ใช้เวลาในการตัดเฉือนเร็วที่สุด
- ตำแหน่งเครื่องมือมาตำแหน่งเดียว
ข้อเสีย
- ปัญหาเกี่ยวกับพิกัดความเผื่อทางขนาดที่เข้มงวด
- อายุการใช้งานเครื่องมือสั้นลง (สั้นกว่าการตัดสองรอบ)
- พิกัดความเผื่อมีค่าเบี่ยงเบนเนื่องจากสึกหรอค่อนข้างเร็ว
แนวคิดตัดสองรอบ
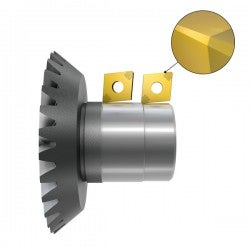
แนวคิดตัดสองรอบช่วยให้ตัดเฉือนผิวสำเร็จให้มีคุณภาพสูงได้โดยไม่ต้องใช้คนควบคุม ขอแนะนำให้ใช้เม็ดมีดกลึงหยาบที่มีรัศมี 1.2 มม. (0.047 นิ้ว) และเม็ดมีดเก็บผิวละเอียดแบบลบมุมเท่านั้น เม็ดมีดทั้งสองรูปแบบควรมีรูปทรงไวเปอร์
ข้อดี
- เป็นระบบเครื่องมือที่เหมาะสำหรับการกลึงหยาบและการเก็บผิวละเอียด
- มีความปลอดภัยสูงกว่า พิกัดความเผื่อต่ำ และไม่จำเป็นต้องเปลี่ยนเครื่องมือบ่อย
ข้อเสีย
- ต้องใช้เม็ดมีดสองชุด
- ตำแหน่งเครื่องมือมีสองตำแหน่ง
- ต้องเปลี่ยนเครื่องมือเพิ่มขึ้นอีกหนึ่งชุด