Como obter boa qualidade da peça no torneamento
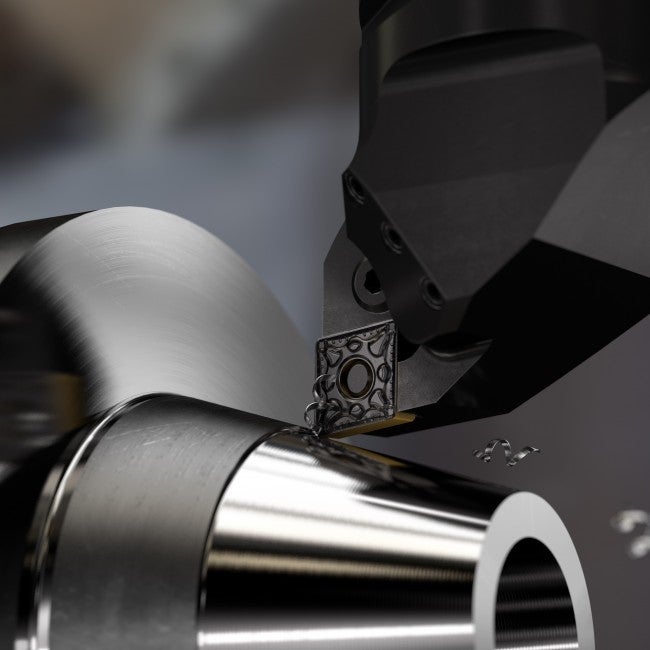
O controle de cavacos é um dos fatores mais importantes a serem considerados para se obter uma boa qualidade das peças torneadas. Escolha os dados de corte corretos e siga as dicas de aplicação para obter uma boa qualidade da peça.
Controle de cavacos bem-sucedido
O controle de cavacos é um dos principais fatores no torneamento e há três alternativas principais referente a quebra de cavacos:
- Quebra automática (por exemplo, ferros fundidos cinzentos)
- Quebra contra a ferramenta
- Quebra contra a peça
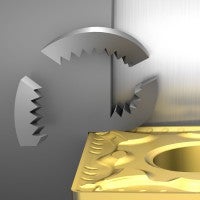
Quebra automática
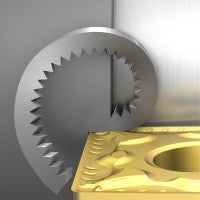
Quebra contra a ferramenta
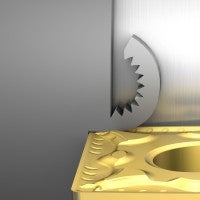
Quebra contra a peça
Fatores que influenciam a quebra de cavacos
- Geometria da pastilha: Com base na largura do canal de cavacos e do desenho da micro e da macrogeometria, os cavacos poderão ser abertos ou mais compactos
- Raio de ponta: O raio de ponta menor controla melhor os cavacos que um raio de ponta maior
- Ângulo de posição (ataque): Dependendo do ângulo, os cavacos são direcionados de diferentes maneiras; na direção do canto a 90 graus ou para fora do canto
- Profundidade de corte: Dependendo do material da peça, a profundidade de corte maior influenciará a quebra de cavacos, levando a forças maiores para quebrar e remover os cavacos
- Avanço: Um avanço mais alto irá gerar cavacos mais fortes. Em alguns casos, pode ajudar na quebra e no controle dos cavacos
- Velocidade de corte: A mudança na velocidade de corte pode influenciar o desempenho da quebra de cavacos
- Material: Um material com cavacos curtos (por exemplo, ferros fundidos) é fácil de usinar em geral. Para materiais com excelente resistência mecânica e resistência à deformação
(tendência para sólidos que se movem lentamente ou se deformam sob tensão, p. ex. Inconel), a quebra de cavacos é um ponto importante a ser considerado
Dados de corte para torneamento
Ao escolher as velocidades e os avanços corretos para torneamento, considere sempre a máquina, a ferramenta, a pastilha e o material.
- Inicie com uma taxa de avanço baixa para garantir a segurança da pastilha e o acabamento superficial, depois aumente a taxa de avanço para melhorar a quebra de cavacos
- Usine com profundidades de corte maiores que o raio de ponta. Isso minimizará a deflexão radial da pastilha, o que é importante na usinagem interna
- Definir uma velocidade de corte muito baixa resultará em vida útil da ferramenta inadequada. Trabalhe sempre com a velocidade de corte recomendada, vc m/min (pés/min.)
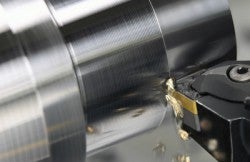
Melhore a qualidade da peça do torneamento com refrigeração
Quando a refrigeração é aplicada corretamente, aumentará a segurança do processo e melhorará o desempenho da ferramenta e a qualidade da peça. Considere o seguinte quando usar refrigeração:
- As ferramentas com refrigeração de precisão são fortemente recomendadas para aplicações de acabamento
- A pressão de refrigeração necessária para quebrar os cavacos depende do diâmetro do olhal (saída), do material usinado, da profundidade de corte e do avanço
- A vazão de refrigeração necessária depende da pressão e da área total dos canais de refrigeração
- Em aplicações médias e de desbaste, recomenda-se o uso de refrigeração
- Para operações de acabamento, recomenda-se o uso combinado de refrigeração de precisão e de refrigeração
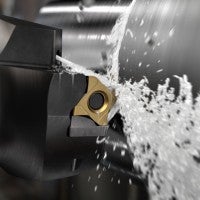
Soluciona os desafios com refrigeração aplicada corretamente
- Problemas com controle de cavacos: Use a refrigeração superior
- Problemas com dimensões: Normalmente causados pela temperatura muito alta – use a refrigeração superior e inferior e o máximo de pressão possível
- Acabamento superficial insatisfatório: Use refrigeração superior se o defeito for causado por cavacos
- A vida útil da ferramenta é imprevisível em operações de desbaste: Use refrigeração inferior somente
- A vida útil da ferramenta é imprevisível em operações de acabamento: Use a refrigeração superior e a inferior
- Escoamento de cavacos insatisfatório em operações internas: Use a refrigeração superior e inferior e pressão mais alta possível
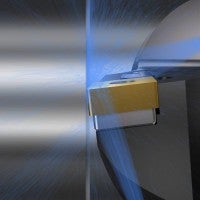
Como aplicar refrigeração e fluido de corte em torneamento
Como obter um bom acabamento superficial no torneamento das peças
Regras gerais para acabamento superficial:
- Geralmente o acabamento superficial é melhorado usando velocidade de corte mais alta
- A geometria da pastilha (ângulos de saída neutro, positivo e negativo, bem como ângulos de folga positivos) influencia no acabamento superficial
- A seleção da classe da pastilha tem influência no acabamento superficial
- No caso de tendência à vibração, selecione um raio de ponta menor
Pastilha Wiper (alisadora)
As pastilhas Wiper são capazes de tornear peças com altas faixas de avanço, sem perder a capacidade de gerar bom acabamento superficial ou de quebrar cavacos.
Uma orientação geral é: Duas vezes a faixa de avanço, mesmo acabamento superficial. Mesma faixa de avanço, acabamento superficial duas vezes melhor.
As pastilhas Wiper são desenvolvidas para suavizar a superfície gerada enquanto a pastilha avança ao longo da peça, o efeito Wiper foi projetado principalmente para faceamento e torneamento reto.
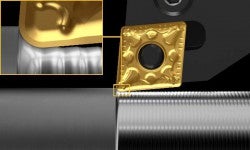
Raio standard
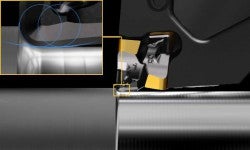
Raio Wiper
Como escolher a geometria wiper
Comparação entre pastilhas standard e Wiper com base na faixa de avanço
Nota! Todos os valores para raios standard foram calculados teoricamente. Os valores para raios Wiper foram baseados em valores experimentais para aços baixa-liga.
Avanço mm (pol.) | Standard RE 0,4 mm (0,016 pol.) Ra µm (µpol.) | Wiper (-WF/-WM) RE 0,4 mm (0,016 pol.) Ra µm (µpol.) | Standard RE 0,8 mm (0,031 pol.) Ra µm (µpol.) | Wiper (-WMX) RE 0,8 mm (0,031 pol.) Ra µm (µpol.) |
0,07 (0,003) | 0,31 (12,4) | 0,30 (12,0) | - | - |
0,10 (0,004) | 0,63 (25,2) | 0,32 (12,8) | 0,31 (12,4) | - |
0,12 (0,005) | 0,90 (36,0) | 0,45 (18,0) | 0,45 (18,0) | - |
0,15 (0,006) | 1,41 (56,4) | 0,70 (28,0) | 0,70 (28,0) | 0,25 (10,0) |
0,18 (0,007) | 2,03 (80,8) | 1,00 (40,0) | 1,00 (40,4) | 0,30 (12,0) |
0,20 (0,008) | 2,50 (100,0) | 1,25 (50,0) | 1,25 (50,0) | 0,35 (14,0) |
0,22 (0,009) | 3,48 (139,2) | 1,74 (69,6) | 1,74 (69,6) | 0,40 (16,0) |
0,25 (0,010) | - | - | 2,25 (90,0) | 0,45 (18,0) |
0,28 (0,011) | - | - | 2,82 (112,8) | 0,50 (20,0) |
0,30 (0,012) | - | - | 3,23 (129,2) | 0,55 (22,0) |
0,35 (0,014) | - | - | 4,40 (176,0) | 0,60 (24,0) |
0,40 (0,016) | - | - | 5,75 (230,0) | 0,70 (28,0) |
0,45 (0,018) | - | - | 8,54 (341,6) | 1,1 (44,0) |
0,50 (0,020) | - | - | 10,55 (422,0) | 1,3 (51,0) |
Avanço mm (pol.) | Standard RE 1,2 mm (0,047 pol.) Ra µm (µpol.) | Wiper (-WMX) RE 1,2 mm (0,047 pol.) Ra µm (µpol.) | Standard RE 1,6 mm (0,063 pol.) Ra µm (µpol.) | Wiper (-WMX) RE 1,6 mm 1) (0,063 pol.) Ra µm (µpol.) |
0,15 (0,006) | 0,47 (18,8) | - | - | - |
0,18 (0,007) | 0,68 (27,2) | - | - | - |
0,20 (0,008) | 0,83 (33,3) | 0,3 (12,0) | 0,63 (25,2) | - |
0,22 (0,009) | 1,16 (46,4) | 0,3 (12,0) | 0,87 (34,8) | - |
0,25 (0,010) | 1,50 (60,0) | 0,4 (16,0) | 1,12 (44,8) | 0,3 (12,0) |
0,28 (0,011) | 1,88 (75,2) | 0,4 (16,0) | 1,41 (56,4) | 0,35 (14,0) |
0,30 (0,012) | 2,16 (86,4) | 0,4 (16,0) | 1,62 (64,8) | 0,4 (16,0) |
0,35 (0,014) | 2,93 (117,2) | 0,5 (20,0) | 2,20 (88,0) | 0,4 (16,0) |
0,40 (0,016) | 3,83 (153,2) | 0,65 (26,0) | 2,88 (115,2) | 0,4 (16,0) |
0,45 (0,018) | 5,70 (228,0) | 0,85 (34,0) | 4,27 (170,8) | 0,5 (20,0) |
0,50 (0,020) | 7,03 (281,2) | 1,15 (46,0) | 5,27 (210,8) | 0,7 (28,0) |
0,55 (0,022) | 8,51 (340,4) | 1,2 (48,0) | 6,38 (255,2) | 0,9 (36,0) |
0,60 (0,024) | 10,13 (405,2) | 1,3 (52,0) | 7,59 (303,6) | 1,05 (42,0) |
0,65 (0,026) | - | - | 8,91 (356,4) | 1,25 (50,0) |
0,70 (0,028) | - | - | 10,31 (413,6) | 1,3 (52,0) |
0,85 (0,033) | - | - | 15,24 (609,6) | 1,9 (76,0) |
0,90 (0,035) | - | - | 17,09 (683,0) | 2,1 (84,0) |
- Valores para raio de 1,6 mm (0,06 pol.) baseados em uma pastilha DNMX
Dicas de aplicação para torneamento externo
Peças com tendência à vibração
Corte em um passe (por exemplo, um tubo)
A recomendação é usinar o corte todo em um passe para direcionar a força no mandril/fuso na direção axial.
Exemplo:
Diâmetro externo (OD) de 25 mm (0,984 pol.)
Diâmetro interno (ID) de 15 mm (0,590 pol.)
Profundidade de corte, ap, é 4,3 mm (0,169 pol.)
Espessura resultante da parede = 0,7 mm (0,028 pol.)
OD = 25 mm (0,984 pol.) | ap 4,3 mm (0,169 pol.) |
![]() | ID = 15 mm (0,590 pol.) |
Um ângulo de posição próximo a 90° (ângulo de ataque 0°) pode ser usado para direcionar as forças de corte na direção axial. Reduz a força de deflexão mínima na peça.
Corte em dois passes
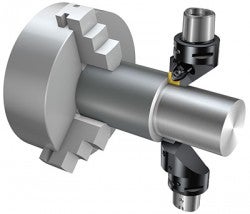
A usinagem com as torres superior e inferior sincronizadas nivelará as forças de corte radiais e evitará vibração e flexão da peça.
Peças delgadas/com paredes finas
Ao tornear peças delgadas/com paredes finas, considere:
- Use um ângulo de posição próximo de 90° (ângulo de ataque 0°). Mesmo uma pequena alteração (de um ângulo de 91/-1 graus para um de 95/-5 graus) afetará a direção da força de corte durante a usinagem
- A profundidade do corte,ap, deve ser maior que o raio de ponta, RE. Um ap maior aumenta a força axial, Fz e diminui a força de corte radial, Fx, o que causa vibração
- Use uma pastilha com aresta viva e raio de ponta pequeno, RE, que irá gerar baixas forças de corte
- Considere o uso de Cermet ou uma classe PVD para propiciar resistência ao desgaste e uma aresta de pastilha viva que é recomendada nesse tipo de operação
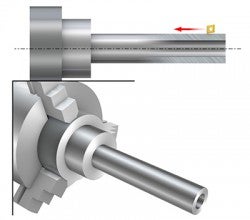
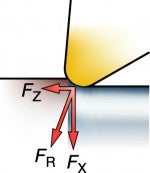
Fresamento/torneamento de cantos a 90 graus
Siga as etapas 1 a 5 para evitar dano à aresta da pastilha. Este método é muito favorável para pastilhas com cobertura CVD e pode reduzir as fraturas consideravelmente.
Passo 1-4:
Mantenha a distância de cada passo (1-4) como a mesma que a faixa de avanço para evitar o entupimento de cavacos.
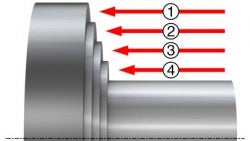
Passo 5:
Usine o corte final em um corte vertical, começando do diâmetro externo para o interno.
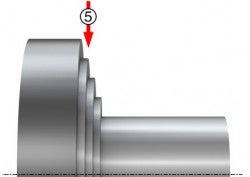
Problemas também podem ocorrer com cavacos enroscados nos raios, se no faceamento de cantos a 90 graus o percurso da ferramenta for do diâmetro interno para o externo. Alterar o percurso da ferramenta pode reverter a direção dos cavacos e resolverá o problema.
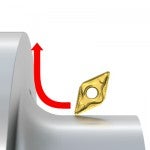
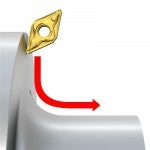
Faceamento
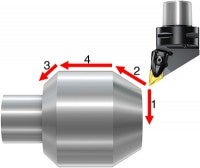
Inicie com faceamento (1) e o chanframento (2). Se possível e se as condições geométricas na peça permitirem, usine o chanfro (3). O corte longitudinal (4) é a última operação e a pastilha terá uma entrada e saída suaves durante a usinagem.
O faceamento deve ser a primeira operação para ajustar o ponto de referência na peça para o próximo passe.
A formação de rebarbas é frequentemente um problema na extremidade do corte (na saída da peça). Deixar um chanfro ou um raio (rolagem em um canto) pode minimizar ou evitar a formação de rebarbas.
Um chanfro na peça levará a uma entrada mais suave da aresta da pastilha (tanto no faceamento quanto no torneamento longitudinal).
Cortes interrompidos

Na usinagem de cortes interrompidos:
- Use uma classe PVD para oferecer maior robustez na aresta em aplicações com interrupções rápidas, por exemplo, barras hexagonais
- Use uma classe CVD mais difícil para proporcionar um grau de tenacidade em aplicações com peças grandes e muita interrupção.
- Considere usar um quebra-cavacos forte para aumentar resistência suficiente ao lascamento
- Pode ser útil desativar a refrigeração para evitar trincas térmicas
Acabamento de peças com saída para retífica (folga para retificação)
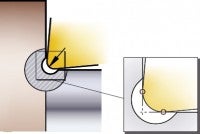
Usar o maior raio de ponta possível, RE, para torneamento longitudinal e frontal, leva a:
- Uma aresta robusta e mais confiabilidade
- Bom acabamento superficial
- Possibilidade de usar altos avanços
Não exceda a largura da saída para retífica e faça da saída para retífica a última operação para remoção de rebarbas.
Dicas de aplicação para torneamento interno
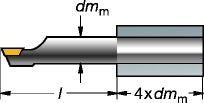
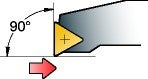
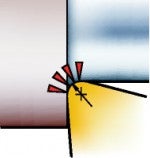
- Escolha a barra com o maior diâmetro possível, mas, ao mesmo tempo, garanta para que haja espaço suficiente para escoamento de cavacos entre a barra e o furo
- Certifique-se de que o escoamento de cavacos seja suficiente em relação aos dados de corte aplicados e que o tipo correto de cavacos seja produzido
- Escolha o menor balanço possível, mas, ao mesmo tempo, certifique-se de que o comprimento da barra de mandrilar permita os comprimentos de fixação recomendados. O comprimento de fixação nunca deve ser menor que três vezes o diâmetro da barra
- Use barras de mandrilar antivibratórias se forem produzidas peças sensíveis à vibração
- Selecione um ângulo de posição o mais próximo possível de 90° (ângulo de ataque de 0° ) para direcionar as forças de corte ao longo da barra de mandrilar. O ângulo de posição não deve nunca ser menor que 75° (ângulo de ataque de -15°)
- Como primeira escolha, a pastilha intercambiável deve ter formato básico positivo e geometria positiva para minimizar a deflexão da pastilha
- Selecione um raio de ponta da pastilha que é menor que a profundidade de corte
- O contato insuficiente da aresta de corte pode aumentar as vibrações causadas pelo atrito durante o corte. Escolha um contato de aresta de corte maior que o raio de ponta para uma boa ação de corte
- O contato excessivo da aresta de corte (maior profundidade de corte e/ou avanço) pode aumentar a vibração causada pela deflexão da ferramenta
- Pastilhas sem cobertura ou com cobertura fina normalmente produzem forças de corte mais baixas se comparadas com pastilhas com cobertura mais espessa. Isso é especialmente importante quando a relação entre o comprimento/diâmetro da ferramenta for maior. Uma aresta de corte viva normalmente melhora a qualidade do furo ao minimizar a tendência a vibrações
- Uma geometria com um quebra-cavacos aberto pode ser mais vantajosa para torneamento interno
- Uma classe da pastilha com maior tenacidade pode ser considerada em algumas operações, pois pode lidar com riscos de entupimento de cavacos ou tendência à vibrações
- Considere percursos alternativos da ferramenta se for necessária melhor formação dos cavacos
Dicas de aplicação para torneamento de peças duras
Além das recomendações gerais para torneamento, há alguns fatores essenciais a serem considerados no torneamento de peças duras (se o processo de produção incluir a preparação da peça antes do endurecimento):
- Evite rebarbas
- Mantenha as tolerâncias dimensionais estreitas
- Faça o chanfro e produza os raios no estágio verde
- Não entre ou saia do corte de forma abrupta
- Entre ou saia para fora ou dentro do corte por rolagem
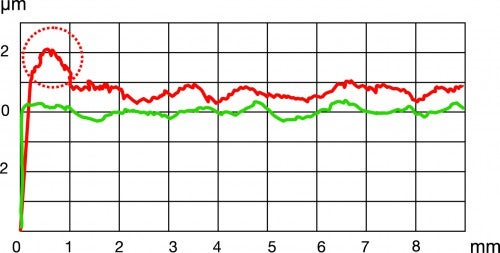
Medições de superfície
Eixo X: Comprimento do recurso
Eixo Y: Desvio do diâmetro
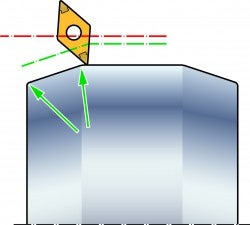
Superfície crítica
Set-up
- Boa estabilidade da máquina, fixação e alinhamento da peça são cruciais
- Como orientação, uma proporção comprimento/diâmetro da peça de até 2:1 é aceita normalmente para peças com fixação somente em uma extremidade. Com fixação adicional com contraponta, essa proporção pode aumentar
- Observe que uma construção simétrica do contraponta e do cabeçote fixo da placa, agregará mais estabilidade dimensional
- Use o sistema Coromant Capto®
- Minimize todos os balanços para maximizar a rigidez do sistema
- Considere a barra de mandrilar de haste de metal duro e Silent Tools para torneamento interno
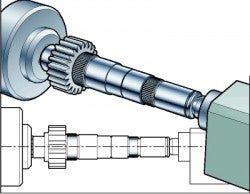
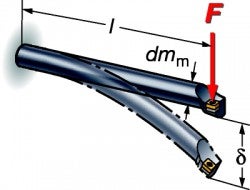
Geometria da micropastilha
Duas preparações de aresta típicas para pastilhas CBN são o tipo S e o tipo T.
- Tipo S: Tem a melhor resistência da aresta de corte. Resistente contra o microlascamento e assegura acabamento superficial consistente.
- Tipo T: Para melhor acabamento superficial em cortes contínuos e formação de rebarbas minimizada em cortes interrompidos. Forças de cortes mais baixas.
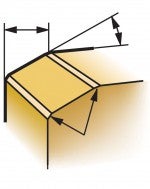
Tipo S
Chanfro com roneamento leve
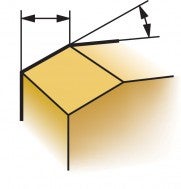
Tipo T
Chanfro sem roneamento
Geometria de canto da pastilha
- Se as condições forem estáveis, use sempre a geometria Wiper para melhor acabamento superficial.
- Use a pastilha com uma abordagem de baixo ângulo de posição quando as exigências de produtividade forem altas.
- Um raio de pastilha normal deve ser usado somente quando a estabilidade for ruim (peças delgadas etc.).
Usinagem com ou sem refrigeração
O torneamento de peças duras sem refrigeração é a situação ideal e é totalmente viável. Ambas as pastilhas de CBN e cerâmica toleram altas temperaturas de corte que eliminam os custos e as dificuldades associadas à refrigeração.
Algumas aplicações podem precisar de refrigeração, por exemplo, para controlar a estabilidade térmica da peça. Nesses casos, assegure um fluxo contínuo de refrigeração durante toda a operação de torneamento.
Geralmente, o calor gerado durante a usinagem é distribuído pelos cavacos (80%), pela peça (10%) e pela pastilha (10%). Isso mostra a importância de escoar os cavacos da zona da aresta de corte.
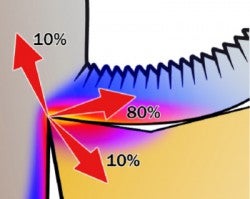
Dados de corte e desgaste
Muito calor na zona da aresta de corte reduz as forças de corte. Portanto, a velocidade de corte que é muito baixa gera menos calor e pode quebrar a pastilha.
A craterização afeta a pastilha gradualmente a força da pastilha, mas não afeta o acabamento superficial num primeiro momento. Ao contrário, o desgaste do flanco afeta a tolerância dimensional gradualmente.
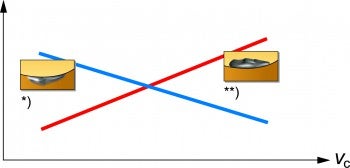
Compartilhamento da vida útil da ferramenta determinando o desgaste
*) Desgaste de flanco **) Craterização
Critério de troca da pastilha
O acabamento superficial (B) predeterminado é um critério prático e frequente para troca da pastilha. O acabamento superficial é medido automaticamente numa estação separada e é dado um valor para uma qualidade específica de acabamento.
Para um processo otimizado e mais estável, defina um número de peças (A) pré-definido como um critério de troca de pastilha. Este valor deve ser entre 10–20% menor que o acabamento superficial pré-definido, a figura exata é determinada de acordo com cada caso.
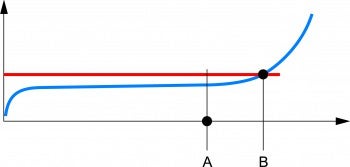
A: Número de peças predeterminado
B: Acabamento superficial predeterminado
X-axis: Número de peças
Eixo Y: Acabamento superficial
Linha azul: Desgaste da pastilha
Linha vermelha: Valor máximo Ra/Rz
Estratégia para um corte
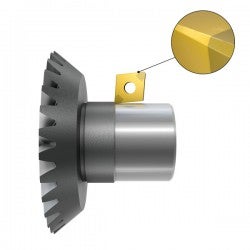
Uma estratégia para remoção de metal em um corte é viável tanto para operações internas quanto externas. Um set-up estável é importante e o balanço da ferramenta não deve ser mais que uma vez o diâmetro da barra no torneamento interno (1×D). Para uma boa usinagem, recomendamos pastilhas chanfradas e levemente roneadas com avanço e velocidade moderados.
Vantagens
- O tempo mais rápido possível de usinagem
- Posição de uma ferramenta
Desvantagens
- Dificuldades em atender às tolerâncias rígidas dimensionais
- Menor vida útil da ferramenta (menor do que com dois cortes)
- Desvios de tolerância devido ao desgaste relativamente rápido
Estratégia para dois cortes
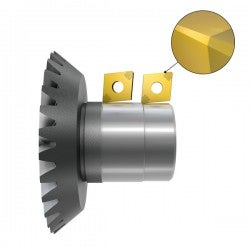
Uma estratégia de dois cortes permite a usinagem sem monitoramento de superfícies acabadas com alta qualidade. Recomendamos pastilhas para desbaste com 1,2 mm (0,047 pol.) de raio e pastilhas para acabamento com apenas um chanfro. As duas pastilhas na geometria Wiper.
Vantagens
- Ferramentas otimizadas para desbaste e acabamento
- Maior segurança, tolerâncias mais estreitas e operações potencialmente mais longas para a troca de ferramenta
Desvantagens
- São necessárias duas pastilhas
- Duas posições de ferramenta
- Uma troca extra de ferramenta