Wytaczanie wykończeniowe
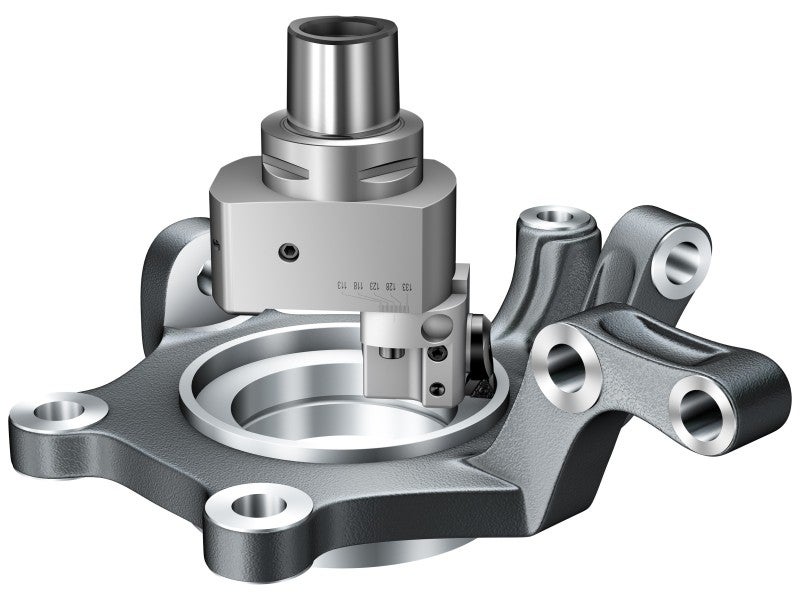
Wytaczanie wykończeniowe jest wykonywane, aby zapewnić istniejącym otworom wąskie tolerancje wymiaru i położenia oraz niską chropowatość powierzchni. Obróbka jest realizowana z małą głębokością skrawania, zwykle poniżej 0.5 mm (0.020 cala).
Wytaczanie jednoostrzowe jest stosowane do wykończania z małą głębokością skrawania, w zastosowaniach wymagających wysokich klas dokładności (od IT6 do IT8) lub wysokiej gładkości powierzchni. Średnicę wykończeniowego narzędzia wytaczarskiego można ustawiać z mikrometryczną dokładnością za pomocą bardzo precyzyjnego mechanizmu. Skrawając z użyciem jednego ostrza wytaczadłem do obróbki zgrubnej, można wykonywać wykończeniowe wytaczanie otworów w klasie dokładności IT9 lub wyższej.
Wytaczanie wsteczne
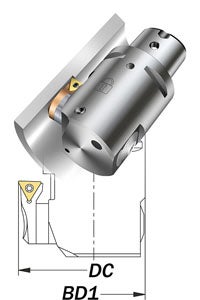
Wytaczanie wsteczne jest stosowane przy obróbce otworów z występami, do których dostęp z przeciwnej strony nie jest możliwy. Wytaczanie z ruchem posuwowym w kierunku do wylotu z otworu można stosować również w celu poprawy współosiowości powierzchni walcowych otworu z występem, ponieważ obróbka całego otworu odbywa się bez zmiany pozycji.
Uwaga: Należy upewnić się, czy narzędzie ma możliwość przejścia przez światło otworu występów oraz czy czoło narzędzia nie uderzy przy tym w dno otworu/czoło występu. Narzędzie wytaczarskie do wytaczania wstecznego przygotowane jest do wykonania przejścia na wylot przez otwór o średnicy co najmniej DC/2 + BD1/2.
Ustawianie narzędzia do wytaczania od tyłu:
- W celu zapewnienia doprowadzenia chłodziwa we właściwe miejsce należy wykręcić wkręt dociskowy z górnego wylotu cieczy obróbkowej
- Następnie wkręcić go do dolnego wylotu (w przypadku bardzo małych narzędzi wkrętu dociskowego może nie dać się wkręcić do dolnego wylotu cieczy obróbkowej)
- Obrócić wkładkę o 180°
- W razie potrzeby użyć zespołu do przedłużania suwaka
- Odwrócić kierunek obrotu
Wytaczanie zewnętrzne
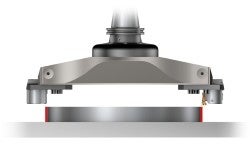
Zewnętrzną obróbkę wykończeniową, w celu uzyskania dokładnego wymiaru średnicy, można wykonywać wytaczadłem wykończeniowym.
Ustawianie narzędzia do wytaczania zewnętrznego:
- Odwrócić kierunek obrotu
- Obrócić głowicę o 180°
- Uwzględnić największą możliwą długość przejścia l3 oraz średnicę zewnętrzną narzędzia, dla których nie występuje ryzyko uderzenia w obrabiany przedmiot
Podczas obróbki zewnętrznej ruchem obrotowym wokół obrabianego przedmiotu na masę suwaka z wykończeniową głowicą wytaczarską działa duża siła odśrodkowa. Z tego względu maksymalną prędkość skrawania w obróbce zewnętrznej wałka należy wyliczać w odniesieniu do maksymalnej prędkości skrawania dla średnicy, w której głowica jest odwrócona o 180°, tj. jak do wewnętrznego wytaczania wykończeniowego otworu.
Przykładowe obliczenia:
- Średnica zewnętrzna wałka przeznaczona do obróbki: 80 mm (3.15 cala)
- Średnica wewnętrzna otworu, jaką można obrabiać w danym ustawieniu suwaka i głowicy: 210 mm (8.27 cala)
Uwaga: Do obrabianej średnicy wałka zawsze należy dodać 130 mm (5.12 cala), aby uzyskać średnicę stanowiącą podstawę do wyliczenia maksymalnej prędkości obrotowej. - Maksymalna prędkość skrawania w obróbce wewnętrznej otworu (na przykładzie CoroBore® 825): 1200 m/min (3937 stóp/min)
- 1200 m/min (3937 stóp/min) na średnicy 210 mm (8.27 cala) to 1820 obr./min. Oznacza to, że 1820 obr./min stanowi wartość maksymalną, jaką należy stosować w danym ustawieniu suwaka i głowicy
- W obróbce zewnętrznej wałka o średnicy 80 mm (3.15 cala) prędkość obrotowa 1820 obr./min odpowiada prędkości skrawania 460 m/min (80 stóp/min)
Wybór płytki do obróbki wykończeniowej
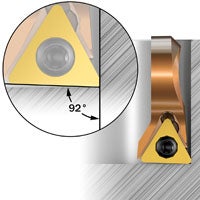
Płytki dodatnie stanowią pierwszy wybór do wszystkich operacji wytaczania wykończeniowego ze względu na mniejsze opory skrawania od płytek ujemnych. Dostępny jest tu szeroki wybór geometrii płytek.
Kąt przystawienia w przypadku wytaczania wykończeniowego powinien wynosić przynajmniej 90° (kąt PSIR 0°), aby zminimalizować wartość promieniowej składowej siły skrawania i nie dopuścić do wzbudzenia drgań.
Dla większości wykończeniowych narzędzi wytaczarskich Sandvik Coromant kąt przystawienia wynosi 92° (kąt PSIR -2°), co umożliwia obróbkę występów i otworów nieprzelotowych bez konieczności zagłębiania całego ostrza w materiał.
Dowiedz się więcej o wyborze właściwej płytki do toczenia.
Siła skrawania w procesie wytaczania wykończeniowego
W czasie gdy narzędzie jest zagłębione w materiał, działają na nie styczna i promieniowa składowe siły, których skutkiem jest ugięcie narzędzia względem powierzchni obrabianego otworu. Składowa styczna próbuje skierować narzędzie w dół oraz odchylić je od osi otworu. Prowadzi to do zmniejszenia kąta przyłożenia narzędzia.
Jakiekolwiek ugięcie promieniowe powoduje zmniejszenie głębokości skrawania i grubości wiórów, co może prowadzić do drgań.
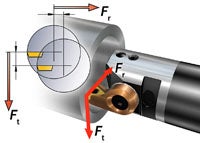
Niewyważenie w procesie wytaczania wykończeniowego
Na skutek niewyważenia, spowodowanego zastosowaniem niesymetrycznego narzędzia lub dużą odchyłką bicia, powstają siły działające na wytaczadło. W większości zastosowań wpływ sił powstających na skutek niewyważenia jest znikomy w porównaniu do sił skrawania.
W obróbce z dużymi prędkościami, szczególnie na długich wysięgach, niewyważenie może być przyczyną drgań, wpływając na jakość wykonania otworu.
Ugięcie narzędzia
Wielkość składowej stycznej i promieniowej sił skrawania zależy od głębokości skrawania, promienia naroża i kąta przystawienia.
Ugięcie od promieniowej składowej siły ma wpływ na średnicę obrabianego otworu. Ugięcie od stycznej składowej siły ma wpływ na krawędź skrawającą płytki, odchylając ją w dół względem poziomu na którym znajduje się oś obrotu. Aby skompensować ugięcie od składowej promieniowej, należy postępować zgodnie z naszymi zaleceniami. Wykończeniowe narzędzia wytaczarskie Sandvik Coromant posiadają mechanizm regulacji, który umożliwia ustawienie średnicy z dokładnością do 2 μm (0.0787 μcala).
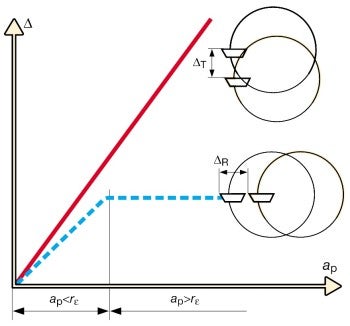
Oś X: Głębokość skrawania
Oś Y: Ugięcie
Czerwona linia: Ugięcie od stycznej składowej siły
Niebieska linia: Ugięcie od promieniowej składowej siły
Lista kontrolna zastosowań do wytaczania wykończeniowego
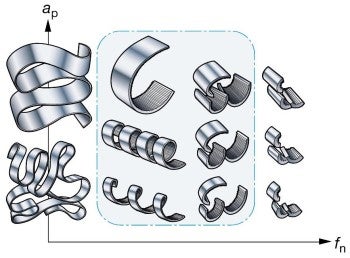
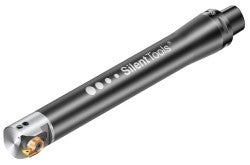
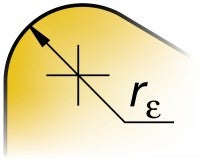
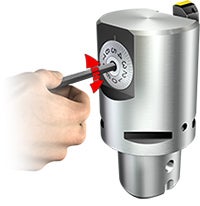
- Wybrać złącze lub chwyt o jak największej średnicy
- Zadbać o właściwą kontrolę wiórów. Wióry krótkie/twarde mogą powodować drgania; wióry długie mogą być przyczyną pogorszenia jakości wykończenia powierzchni lub wyłamywania się płytki.
- Należy stosować jak najkrótszy wysięg i używać trzonków z funkcją tłumienia drgań do wysięgów większych niż czterokrotność długości średnicy przekroju poprzecznego trzonka
- Duży promień naroża (RE) płytki zwiększa bezpieczeństwo obróbki i pozwala uzyskać powierzchnię o mniejszej chropowatości, ale może też powodować drgania. Niezalecane jest stosowanie naroży o promieniu powyżej 0,4 mm (0.016 cala). Zaleca się stosowanie naroży o promieniu 0,2 mm (0.008 cala) w przypadku stosowania narzędzi do obróbki otworów o małej średnicy
- Płytki z cienkim pokryciem lub niepokrywane generują zwykle mniejsze opory skrawania niż płytki z grubym pokryciem. Ma to szczególne znaczenie w przypadku dużej różnicy długości narzędzia i jego średnicy.
- Ostra krawędź skrawająca sprzyja zazwyczaj poprawie jakości wykonania otworu przez ograniczenie tendencji do drgań
- Często korzystnym rozwiązaniem jest wybór geometrii z otwartym łamaczem wiórów
- Zastosować płytkę do obróbki z niskimi oporami skrawania, aby uzyskać dobrą chropowatość powierzchni (niezalecane w przypadku obróbki w niestabilnych warunkach lub na długich wysięgach)
- Zbyt małe zagłębienie naroża ostrza może spowodować zwiększenie drgań powodowanych tarciem podczas skrawania
- Zbyt duże zagłębienie ostrza (duża głębokość skrawania i/lub posuw) może powodować zwiększenie drgań na skutek ugięcia
- W niektórych rodzajach obróbki, jeśli ryzyko zakleszczania się wiórów lub powstawania drgań jest duże, można rozważyć zastosowanie płytek w gatunku o dużej udarności
- Przy obróbce otworów o wąskich tolerancjach ostateczne ustawienie należy przeprowadzić po pomiarze średnicy otworu, gdy narzędzie wciąż pozostaje zamocowane we wrzecionie obrabiarki. Pozwala to uniknąć niedopasowań między wrzecionem obrabiarki a przyrządem do ustawiania narzędzi, wpływu zmiany ugięcia promieniowego i stanu zużycia ostrza płytki
- Należy zadbać o odpowiednie mocowanie narzędzia wytaczarskiego i przedmiotu obrabianego
- Zastosowanie cieczy obróbkowej usprawni odprowadzanie wiórów, zwiększy trwałość ostrzy i pozwoli uzyskać otwór o lepszej geometrii
- Modułowy system narzędzi o małej średnicy Trzonek stożkowy pozwala uzyskać lepszą prostoliniowość otworu przy obróbce na długich wysięgach, niezależnie od użytej oprawki zaciskowej. Węglikowy trzonek stożkowy należy stosować przy obróbce na wysięgach do 6xDW przypadku trzonków cylindrycznych najlepszą prostoliniowość otworu uzyskuje się zwykle przy obróbce na krótkich wysięgachTrzonki z ciężkiego metalu zapewniają najlepszą stabilność i niewielkie ryzyko drgań przy obróbce na krótkich wysięgachNależy wybierać dużej precyzji oprawki zaciskowe z mocowaniem hydraulicznym, aby uzyskać najwyższy poziom stabilności i niezawodności produkcji
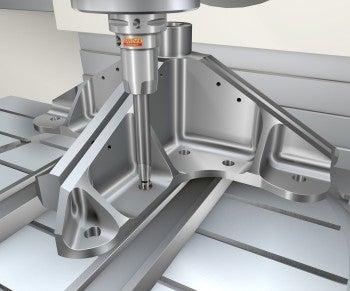
Zobacz także zalecenia ogólne w rozdziale Jak stosować wytaczanie.
Odczytaj zalecany moment dokręcenia w poniższej instrukcji użytkowania.
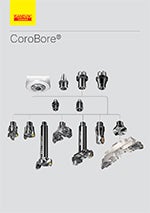