穴をあける
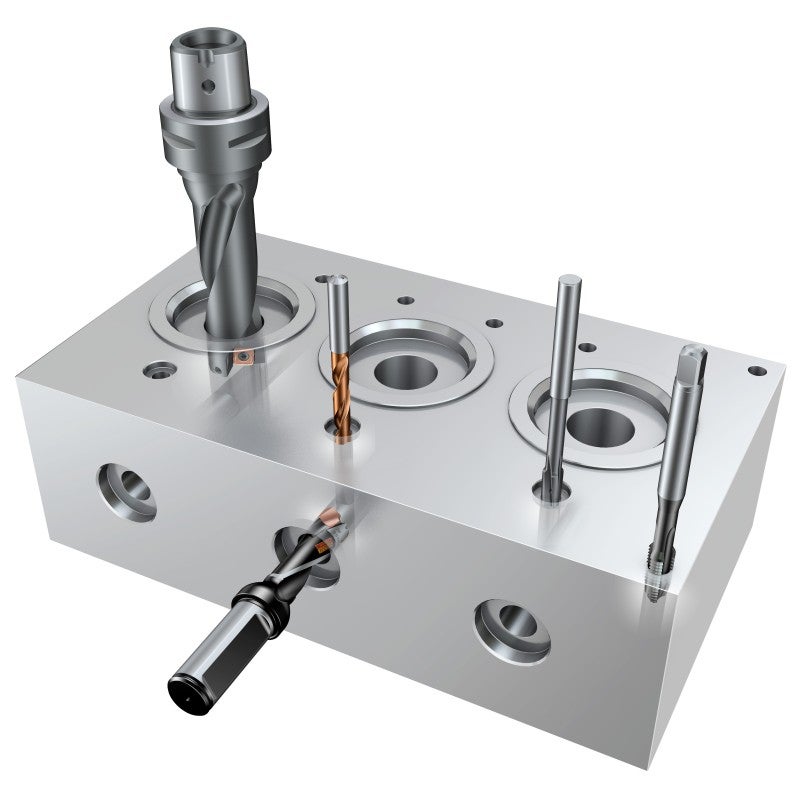
「前工程で、すでに当初の加工物の価値がより高くなっている場合、穴あけ加工は生産工程の後期で行われることが少なくありません。穴あけ加工は一見シンプルですが、工具に故障が生じた場合や工具の能力を超えて使用した場合に、重大な結果を招く恐れのある複雑な加工です。
穴あけ用の初期の考慮事項
1. 穴
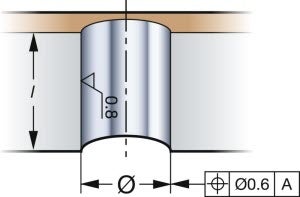
穴あけの際の穴に関する最も基本的な3つの考慮事項:
- 加工径
- 加工深さ
- 穴品質
穴タイプと要求される精度は工具の選定に影響します。穴あけ加工は凹凸面や食い付き/抜け際の傾斜面、交差穴に影響を受けることがあります。
穴の種類
貫通穴
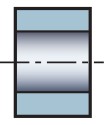
止まり穴
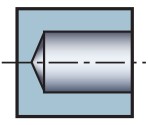
面取り
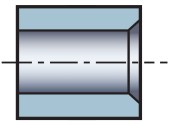
段付き
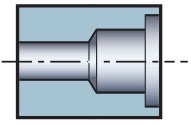
入り
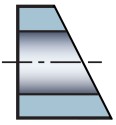
抜け
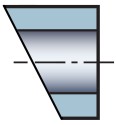
交差
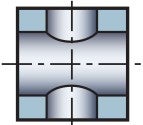
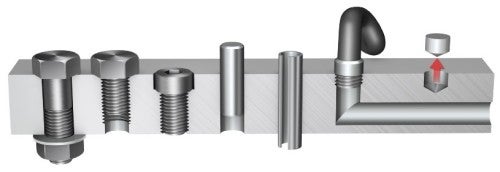
- ボルト用クリアランス付き穴
- ねじ穴
- 座ぐり穴
- はめあい穴
- 管用穴(熱交換器)
- 通路を形成する穴
- バランス調整用穴
- 深穴/クーラント穴
2. 加工物
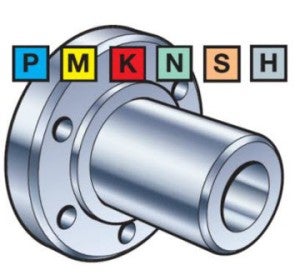
必要な穴を分析したら、被削材、ワークの形状および品質について検討します。
被削材
- 被削材は切りくず処理特性に優れていますか?切りくずが長い被削材ですか?それとも短い被削材ですか?
- 被削性は?
- 被削材硬度は?
- 合金成分は?
加工ワークの形状
- ワークは穴を中心にして回転対称ですか?つまり固定ドリルで加工することができますか?
- ワークは安定していますか?それともびびりの発生原因となる薄肉箇所がありますか?
- ワークは適切な位置に固定できますか?安定性について検討する項目はありますか?
- 工具エクステンションは必要ですか?突出し量の長い工具を使用する必要がありますか?
数量
加工数量によって使用するドリルが決まります。
- 加工数量が多い場合 - 最適化されたドリル、テーラーメイドドリルを使用する
- 加工数量が少ない場合 - 汎用性のあるドリルを使用する
3. 機械
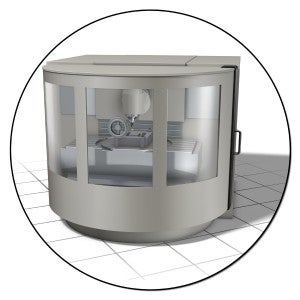
安全で生産性の高い穴あけ加工を実行する方法を理解することが重要です。機械にあわせて下記の要件を選択してください:
- 加工方法
- 使用するツールホルダ/コレットのタイプ
必ず以下の項目を検討してください。
- 基本的な機械の安定性、特にスピンドル
- 小径穴の加工に十分な主軸回転数(rpm)ですか?
- クーラント供給クーラント量は大径ドリルに十分ですか?
- クーラント圧は小径ドリルに十分ですか?
- ワークのクランプ十分安定していますか?
- 横型スピンドルですか、それとも縦型スピンドルですか?横型スピンドルの方が切りくず排出に優れています。
- 動力およびトルク大径穴の加工に十分な動力ですか?十分でない場合は、トレパンドリルが使用できますか?もしくは代わりにフライス工具によるヘリカル加工が使用できますか?
- ツールマガジンのスペースは限られていますか?その場合、ステップおよび面取りドリルが適切なソリューションになり得ますか?
ツールホールディング
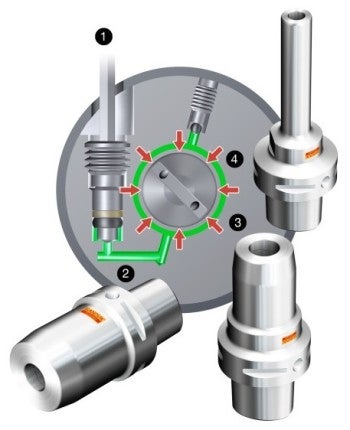
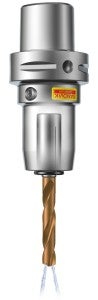
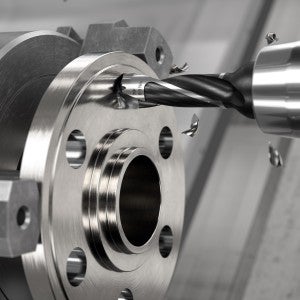
生産性は、材種やブレーカの影響のみならず、クランプ保持性能やクランプ精度によっても影響されます。必ずできるだけ短いドリルと工具突出し量を使用します。
すべての穴あけ法を含むすべての金属加工用に設計されたモジュラーツーリングシステムを検討する。このシステムでは、同じ工具とアダプタを、異なる加工用途や機械で使用可能です。このため、1つのツーリングシステムを使用して工場全体を標準化することが可能です。
工具の振れ
穴あけ加工をうまく行うには、工具の振れを 最小限に抑えることが必要です。振れは20マイクロメートルをこないこと。 アライメントは以下のため平行でなければなりません。
- 厳しい穴公差と真直度
- 良好な加工面品質
- 長くばらつきのない工具寿命
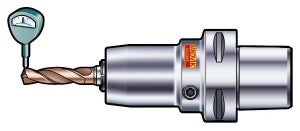
加工法の選定
カウンターボア – 加工法
ワンツールソリューション
- 段付き穴/カウンターボア
- ドリルタイプ 4/5
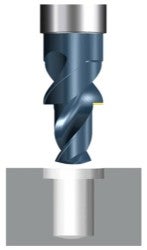
長所
+ カスタマイズ工具
+ 最速加工法
短所
- 柔軟性に欠ける
ツーツールソリューション
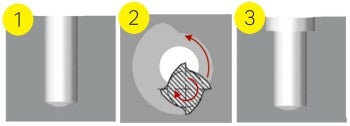
長所
+ 標準工具
+ 比較的柔軟性がある
短所
- ツーツール
- 2工具位置が必要
- より長いサイクルタイム
ステップと面取り – ワンドリル加工法
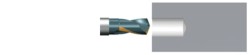
ドリルタイプ 1
標準
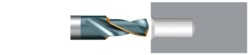
ドリルタイプ 2
2径ドリル (パイロット + ボディ径)
パイロットと面取り付き。ボディ切削ではない
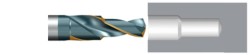
ドリルタイプ 4
2径ドリル (パイロット + ボディ径)
パイロットと面取り付き。ボディ切削
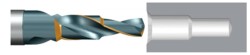
ドリルタイプ 5
3径ドリル (パイロット + ステップ + ボディ径)
パイロット、ステップ、面取り付き。ボディ切削ではない
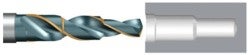
ドリルタイプ 6
3 径ドリル (パイロット + ボディ径)
パイロット、ステップ、面取り付き。ボディ切削
穴あけ加工
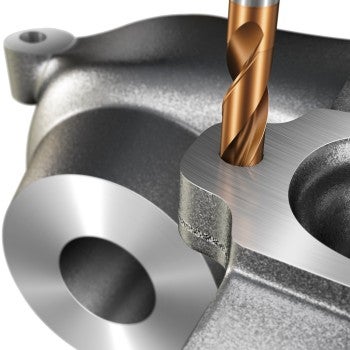
1穴当たりのコストを最も低くし、必要な穴品質を実現するために、 正しい選択を行うことが重要になります。異なる穴タイプには異なる工具を考慮する必要があります。
- 小径から中径までの穴
- 大径穴加工
- 深穴
- 微細穴
小中径穴あけ
小中径穴あけ加工には、3つの異なるソリューションがあります。超硬ソリッドドリル、ヘッド交換式ドリル、刃先交換式ドリルです。穴公差、穴の長さ、穴径の3つは、ドリルタイプの選定時に考慮すべき重要な要素です。それぞれのソリューションには、加工法に応じて、独自の利点があります。
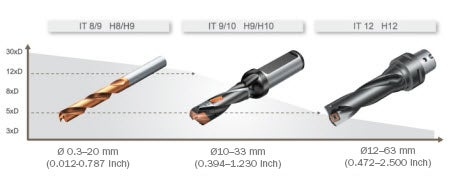
大径穴あけ
機械動力が限られている場合の大径穴加工用として、次の3つの方法があります。
- トレパニング工具を使用する
- ボーリングツールで穴を広げる
- フライス加工用工具でヘリカル加工を行う
大径穴の加工では、ワークと機械の両方に剛性が重要です。また、機械動力とトルクは加工を制限する要素です。生産性の観点から、穴あけ工具の選択が最良です - ヘリカル加工を使用するとフライス工具の5倍で穴あけできます。しかしトレパニング工具は貫通穴加工に飲み使用可能です。フライスカッターでは、圧倒的に低い動力とトルクでの加工が可能です。
深穴加工
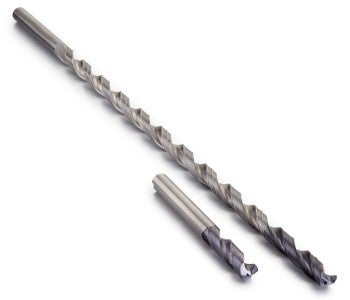
パイロット穴あけ
パイロットドリルは、深穴加工用ドリルとの併用して使用するドリルとして設計され、最高の穴位置精度と逃げが少ない穴加工を実現します。
切削速度と送り
深穴加工用ドリルに推奨される切削速度と送りは、長い工具寿命と高い生産性を併せもつように算出されています。計算された切削速度と送りにより、スムーズな加工開始が可能です。最良の結果を得るために、それぞれの加工において、速度と送りの調整が必要になることがあります。
微細穴加工
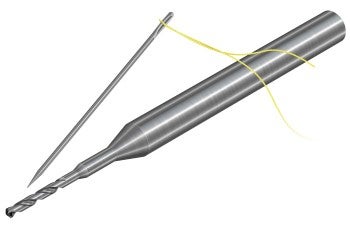
切削速度と送り
この微細穴加工用ドリルに推奨される切削速度と送りは、長い工具寿命と高い生産性を併せもつように算出されています。計算された切削速度と送りにより、スムーズな加工開始が可能です。最良の結果を得るために、それぞれの加工において、速度と送りの調整が必要になることがあります。
クーラント
微細穴加工用ドリルでは、クーラント圧が重要な要素です。クーラント圧や供給量が不十分な場合、早期の工具故障を引き起こすことがあります。高圧クーラントの使用を推奨します。推奨される標準的なクーラント圧は40-70 barです。