仕上げボーリング
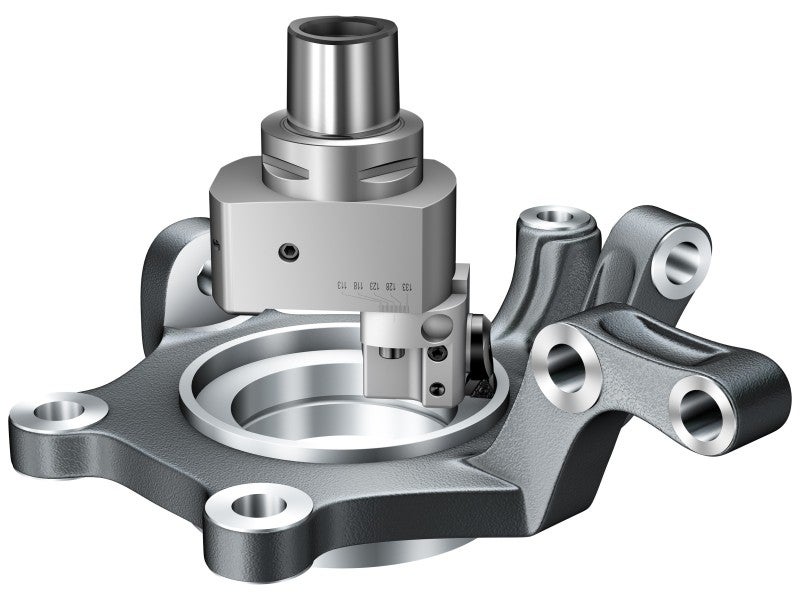
ファインボーリング加工は、穴公差が厳しく、正確な位置決めと高品質の面仕上げが求められる仕上げを目的として行われるものです。加工は、通常0.5 mm (0.020”) 未満の 小さな切込みで行われます。
シングルエッジボーリング工具は、厳しい穴公差 (IT6 から IT8) または高品質の面仕上が要求される場合に小さい切込みで行う仕上げ加工に使用します。ファインボーリング工具の径は、精密なメカニズムによりミクロン単位で調整が可能です。シングルエッジボーリング工具は、荒ボーリング工具と合わせて、公差 IT9 またはそれ以上の穴の仕上げ加工に対応します。
バックボーリング
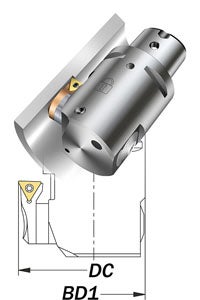
バックボーリングは、入口にショルダー部のある穴の加工に使用します。穴全体が1方向からのみ加工されるので、穴の同心度を高めるために用いることもできます。
注: ボーリング工具がショルダー部を越える際、ワークと干渉しないことを確認してください。バックボーリングでは、ボーリング工具は最小径 (DC/2 + BD1/2) の穴を通る構造となっています。
バックボーリングの工具設定:
- 切削油の供給位置を正しくするために、上側の切削油出口からグラブスクリューを外し、下側の切削油出口に取り付けてください。
- (最小工具サイズの場合には、グラブスクリューを下側の切削油出口に取付けできません。)
- カートリッジを180°回します。
- 必要に応じてスライドエクステンションを使用します。
- 回転方向を逆にします。
外径ボーリング
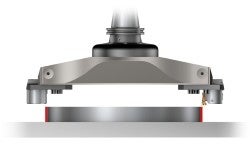
厳しい加工径公差に対応するために、ファインボーリング工具により外径加工を行うことができます。
外径ボーリングの工具設定:
- 回転方向を逆にします。
- ヘッドを180°反転させます。
- 干渉を避けるために可能な最大加工長さl3と工具の外径を考慮します。
外径加工では、質量のあるスライドとファインボーリングヘッドがワークの周囲を回転し、高い遠心力を発生させます。従って外径加工の最大切削速度は、チップの位置での最大切削速度を考慮して計算します。
計算例
- 加工外径:80 mm (3.15 inch)
- スライドとヘッドがこの位置にある場合の加工可能な内径:210 mm (8.27 inch)
注: 最大回転数を計算するための径を得るために、常に加工径に130 mm (5.12”) を加算します。 - 内径加工に基づいた最大切削速度(CoroBore® 825でのこの例の場合): 1200 m/min (3937 ft/min)
- 210 mm (8.27 inch) 径での1200 m/min (3937 ft/min) は1820 rpmとおなじです。つまり、1820 rpm がこのスライドとヘッド位置用に使用できる最大切削速度です
- 外径加工では、1820 rpm が80 mm (3.15 inch) 径での切削速度 460 m/min (1509 ft/min) に相当します
仕上げ加工用チップの選定
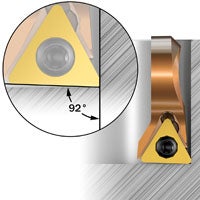
ポジチップはネガチップより切削抵抗が低いので、全てのファインボーリング加工の第一推奨です。様々なチップブレーカを取り揃えています。
背分力を最小にしてびびりを抑えるために、ファインボーリングの切込角は900° (アプローチ角0°) 以上にしてください。
サンドビック・コロマントのファインボーリングユニットのほとんどは、ショルダー部および止まり穴に刃先がかみ合わないように、切込角を92° (アプローチ角-2°) としています。
適切な旋削チップの選定方法の詳細をご覧ください。
仕上げボーリング加工での切削抵抗
切削中、主分力と背分力によって、工具はワークから離れようとします。主分力により、工具は中心線からずら離れようとします。これにより、工具の逃げ角は小さくなります。
径方向のたわみは切込みおよび切りくず厚みの減少を意味し、びびりの原因となります。
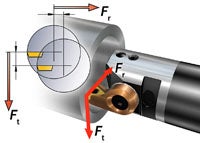
仕上げボーリング加工でのバランス調整
工具の非対称や大きな振れによるアンバランスは、遠心力により増幅されます。たいていの加工において、アンバランスにより発生する力は切削抵抗と比較して無視できるものです。
しかし高速で突出し量が長い場合には、アンバランスはびびりを発生させて穴の品質に影響を与えることがあります。
工具のたわみ
主分力および背分力の大きさは、切込み、ノーズRおよび切込角の影響を受けます。
径方向でのたわみは加工穴径に影響します。接線方向でのたわみは、中心線を超えて下方にたわむことによりチップの刃先部分に影響します。当社の推奨事項に従って径方向のたわみを補正してください。サンドビック・コロマントのファインボーリングユニットは、2 μm (0.0787 μ”) の範囲内で径を調整できる調整メカニズムを備えています。
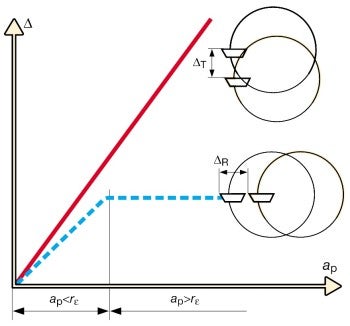
X軸: 切込み
Y軸: たわみ
赤い線: 接線方向のたわみ
青い線: 径方向
ファインボーリングの加工チェックリスト
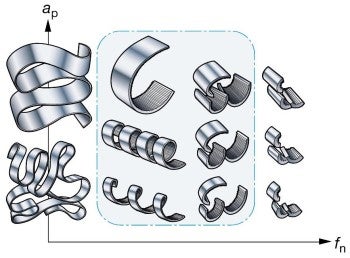
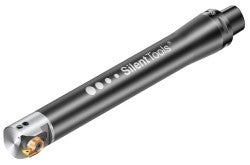
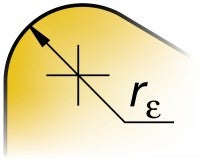
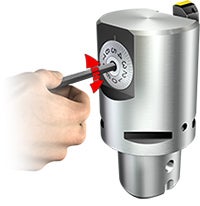
- 可能な限り大きなカップリングサイズまたは工具径を選択してください。
- 適切な切りくず処理が行われることを確認してください。短い切りくず/硬い切りくずはびびりを発生させることがあり、長い切りくずは仕上げ面の品質低下あるいはチップの破損の原因となることがあります。
- 可能な限り短い突出し量を選定して、カップリングサイズの4倍以上の突出し量には防振型ボーリングバイトを使用してください。
- チップのノーズR (RE) が大きいと、 加工安全性と仕上げ面粗さを向上させることができますが、びびりが発生することがあります。0.4mm (0.016 inch) を超えるノーズRは避けてください。小径ボーリングバイトを使用する際は、ノーズR0.2 mm (0.008 inch)をお勧めします。
- 薄膜コーティングチップやノンコートチップは、厚膜コーティングチップと比較して切削抵抗が低くなります。刃先のシャープさは、突出しが大きい場合は特に重要です。
- シャープな刃先はびびりを最小化して、穴の品質を向上させます。
- オープンチップブレーカ形状は、多くの場合有利になることがあります。
- 軽切削チップを選択して良好な加工面品質を達成してください(不安定な加工条件や長い突き出し量は避けてください)。
- 刃先の食いつきが不十分だと、切削中の摩擦によるびびりが大きくなることがあります。
- 刃先の食いつきが大きすぎると(大きな 切込み および/または送り)、工具のたわみのためにびびりが大きくなることがあります。
- じん性の高いチップ材種は、切りくずの詰まりやびびりに対応することできるので、 特定の加工では検討する場合があります。
- 穴公差が厳しい場合には、最終調整は工具が機上にある状態で行ってください。これにより、プリセッタと工作機械スピンドルとの差、径方向のたわみあるいはチップの摩耗を補正します。
- ボーリングツールとワークを適切にクランプしてください。
- 切りくず排出、工具寿命および穴の形状を向上させるため切削油を使用してください。
- 小径用のモジュラーシステム円錐ホルダでは、使用するチャックに関係なく、長い突出し量で真っすぐな穴を加工できます。突出し量が長い場合(6×Dまで)は、円錐超硬ホルダを選びます。円筒ホルダでは、短い突出し量により真直度の高い穴加工が可能です。短い突出し量で加工安定性を最大にして、びびりを少なくするには、ヘビーメタルホルダを選びます。最高の安定性および生産安全性を達成するためには高精度油圧チャックを選びます。
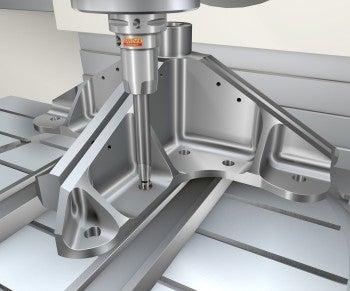
一般推奨事項用のボーリング加工の適用方法も参照してください。
推奨締付けトルクを見るには、下の表を参照してください。
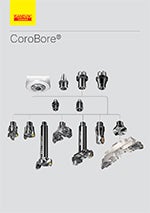