Chuck selection
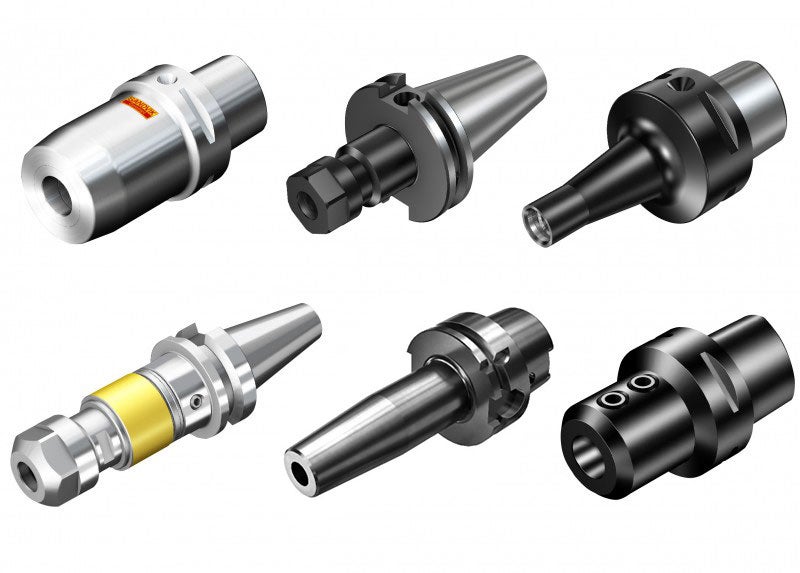
Chucks are used to hold round shank tools. There are many styles of chucks and the chuck selection varies depending on:
- Application: end mill, drill, tap, reamer
- Component material and tolerance
- Production: high volume or mixed
- Coolant: dry, emulsion, MQL – through tool or external
Chuck comparison
In the table below you can see a comparison between different styles of chucks which can help you to do the best chuck selection.
![]() | ![]() | ![]() | ![]() | ![]() | |
High-precision hydraulic chuck | Shrink fit | Power chuck | ER collet chuck | Weldon | |
Pull-out security, torque transmission | Very good | Very good | Good | Acceptable | Very good |
Easy handling | Very good | Acceptable | Good | Good | Very good |
High precision | Very good | Very good | Good | Acceptable | Acceptable |
Flexibility | Very good | Good | Very good | Very good | Acceptable |
Accessibility | Very good | Very good | Acceptable | Good | Acceptable |
Cylindrical shank
The cylindrical shank is clamped evenly and is used for best run-out accuracy for milling, drilling and reaming. With no flat or locking it has torque and axial force limits before the shank moves in the holder.
Hydraulic chuck
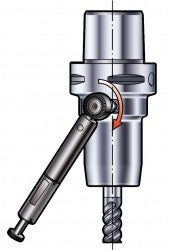
The hydraulic membrane provides high clamping force and run-out accuracy. It is very simple to handle without need for separate equipment. Collets can be used which reduces the number of chucks needed and allows coolant to be delivered through the tool (drilling) or through the collets (milling).
Shrink fit chuck
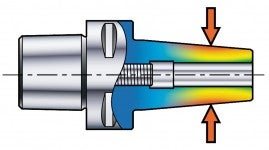
The bore of the chuck is slightly smaller than the shank diameter, the chuck is heated up to expand for changing the tool. Due to thermal expansion between the holder and the tool shank, shrink fit chucks are mainly used for solid carbide round tools. Heating equipment is needed to change tools and each chuck is just for one shank diameter and coolant delivery. This makes shrink fit best suited to production with a tool setting room for tool changing.
Shrink fit offers good accessibility and high run-out precision, with medium to high clamping force.
ER Collet chuck (DIN6499)
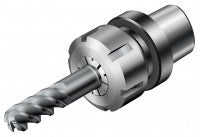
The run-out accuracy and clamping force are not as good as hydraulic or shrink fit chucks. However, the very good flexibility with collets makes the ER collet chuck an economic all-round chuck for drilling and light milling applications. The tool change can be handled at the machine with a fixture. Use a torque wrench to secure the chuck will not be overtightened, which reduces the accuracy and damages the chuck.
Shank with flat
A shank with flat is used for higher torque applications where torque security is more critical than run-out accuracy.
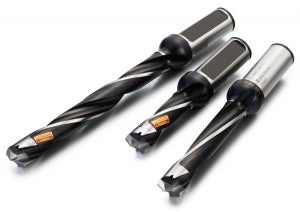
Drill adaptor for shank ISO9766
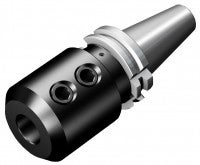
The drill adaptor is suited for medium to large drilling operations. The flat is all along the shank as the drill has only compressive axial forces (pull-out is not a risk), but has an axial face contact with the adaptor for best stability. The drill adaptor differs from the Weldon adaptor in that the face of the adaptor is ground and the shank is longer for best stability.
Weldon adaptor for shank DIN 6535-HB
The Weldon or “milling” adaptor was the traditional chuck used for milling applications. The short flats provide torque resistance and pull-out security. However, the downside with Weldon is the run-out accuracy which is an important factor for milling tool performance. More often this type of chuck is being replaced by shrink fit or hydraulic.
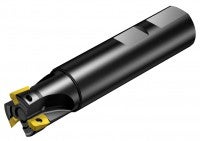
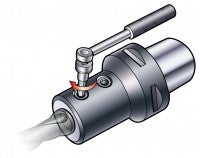
Modular screw coupling
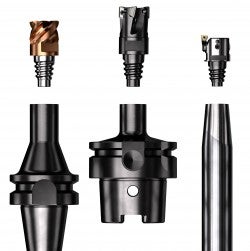
The modular screw coupling interface provides many benefits for milling and boring. For smaller machines removing the need of a chuck allows for shorter gauge lengths which dramatically reduces vibration. For long overhangs the shank material and shape can be optimized easier compared to solid tools.
For milling, longer solid carbide tools are costly and when only the end is used the tool costs can be significantly reduced.
Machine interface adaptors
Used mainly for small and medium machine spindles (HSK40/50/63 - steep taper #30, 40 - C3/C4/C5/C6). All other chucks build length into the assembly. Reduce the gauge length below three times the flange contact to reduce vibration and increase productivity.
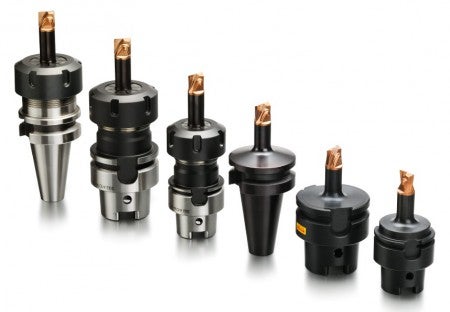
Cylindrical – steel/solid carbide
The length of shank is selected to best provide the stick out length from the chuck. Steel is used up to 3×D and solid carbide up to 8×D.
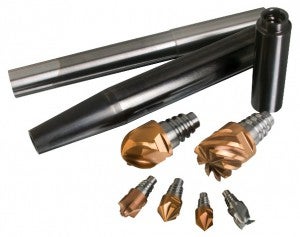
Conical – steel/solid carbide
The conical shape has a big impact for stability. Conical should always be used where clearance allows and for 5-axis machining. Replacing conical solid carbide end mills has a big impact on tooling costs. Conical shanks exist in cylindrical shanks as well as Coromant Capto® for steel.
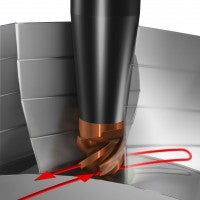
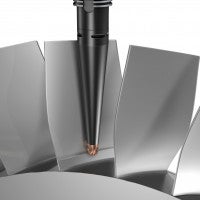
G undersized shanks – heavy metal
Over three times the shank diameter vibration is always an issue. Optimizing the stick out length to the absolute minimum required makes a difference. The G undersized shanks are 0.3 mm (0.012 inch) smaller than the cutting diameter and used in combination with dedicated collets for hydraulic chucks the shank length can easily be modified. Their application area is from 3–6 times the shank diameter.
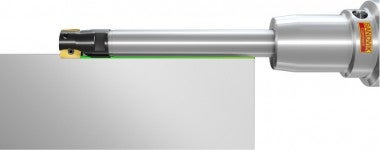
Cylindrical shank with square drive for tapping
The tap adaptors are designed for tapping operations in machines equipped with automatic tool change. A construction for pull and pressure compensates for differences between spindle feed and thread pitch. Even micro differences between calculated feed and actual pitch of the tap can lead to extremely high thrust forces on the tap flanges and an increase in cutting pressure. When threading with a tap, with cylindrical square shank, it is important to use a tap adaptor with the same size as the shank/square.
Synchronized tapping chucks
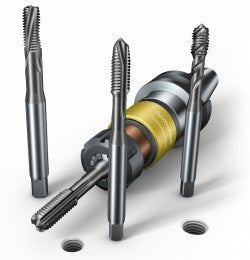
Synchronized tapping chucks, like CoroChuck® 970, are based on a micro compensator, which aligns radial and axial deviations. Thrust forces are reduced on the tap flanks, which results in better surface quality and longer tool life. Synchronized tapping chucks use ER-Collets with a square drive. It is not recommended to use a collet without the square due to the high torque that will make the tap rotate in the collet if not used.
Quick change
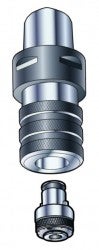
For quick change tap adaptors, it is also important to use the right size tap adaptor, otherwise the risk of tap breakage is high as well as poor tolerance on the finished thread.
To get the best result from machines not equipped for synchronized tapping, the following recommendations should be observed:
- Program machine feed 10% lower than theoretical value (thread pitch rpm). This enables the tap to cut precisely on pitch
- Reduce tapping depth by 10% to avoid tap breakage
- When tapping deep holes in soft materials, e.g. aluminium, feed and depth should be reduced by 3–5%
Chuck selection/recommendations
Chuck | First choice | Second choice |
Indexable insert drill | Drill adaptor | |
Exchangeable-tip drill | High-precision hydraulic chuck (use only with collet) Drill adaptor | |
Solid carbide drill | High-precision hydraulic chuck Shrink fit | ER collet chuck |
Reamers | High-precision hydraulic chuck Shrink fit | ER collet chuck |
Taps | Synchronized tapping chuck | ER collet chuck Quick change |
Indexable insert end mill | High-precision hydraulic chuck | Weldon adaptor |
Exchangeable-head end mill | High-precision hydraulic chuck (large machine tools and long overhangs) | Exchangeable head adaptor (small and medium machine tools and short overhangs) |
Solid carbide end mill | High-precision hydraulic chuck Shrink fit | ER collet chuck |