Korrektes Reiben einer Bohrung
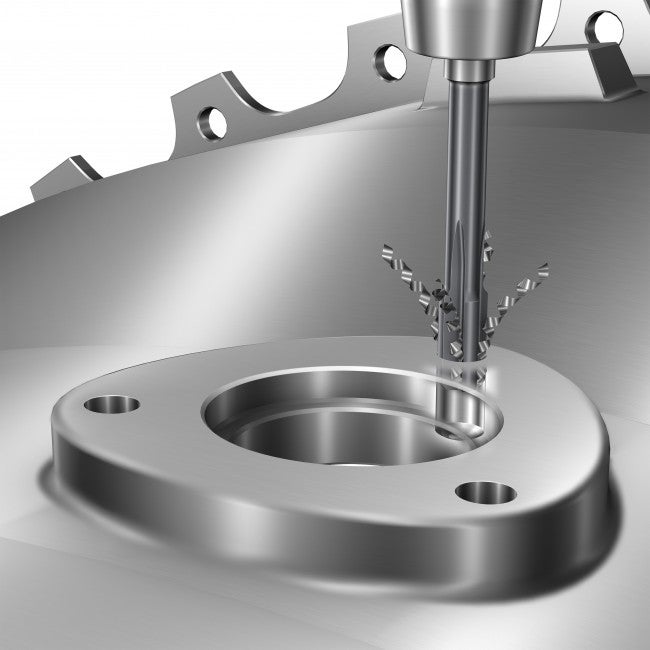
Beim Reiben einer Bohrung ist Folgendes zu berücksichtigen:
Materialabtrag
Beim Reiben hängt das empfohlene Aufmaß vom zu bearbeitenden Werkstoff und der Oberflächengüte der vorgefertigten Bohrung ab. Allgemeine Richtlinien zum jeweiligen Aufmaß finden Sie in der folgenden Tabelle.
Ø, mm | ||||||
Material | 1-3 | 3-5 | 5.1-10 | 10.1-20 | 20.1-30 | >30 |
P1 | 0.1-0.2 | 0.1-0.2 | 0.2 | 0.2-0.3 | 0.3-0.4 | 0.4-0.5 |
P2 | 0.1-0.2 | 0.1-0.2 | 0.2 | 0.2 | 0.3 | 0.3-0.4 |
P3 | 0.1-0.2 | 0.1-0.2 | 0.2 | 0.2 | 0.3 | 0.3-0.4 |
P4 | 0.1-0.2 | 0.1-0.2 | 0.2 | 0.2-0.3 | 0.3-0.4 | 0.4-0.5 |
P5 | 0.1-0.2 | 0.1-0.2 | 0.2 | 0.2 | 0.3 | 0.3-0.4 |
M1 | 0.1-0.2 | 0.1-0.2 | 0.2 | 0.2 | 0.3 | 0.3-0.4 |
M2 | 0.1-0.2 | 0.1-0.2 | 0.2 | 0.2 | 0.3 | 0.3-0.4 |
M3 | 0.1-0.2 | 0.1-0.2 | 0.2 | 0.2 | 0.3 | 0.3-0.4 |
K1 | 0.1-0.2 | 0.1-0.2 | 0.2 | 0.3 | 0.3 | 0.5 |
K2 | 0.1-0.2 | 0.1-0.2 | 0.2 | 0.2-0.3 | 0.3-0.4 | 0.4-0.5 |
K3 | 0.1-0.2 | 0.1-0.2 | 0.2 | 0.3 | 0.4 | 0.5 |
K4 | 0.1-0.2 | 0.1-0.2 | 0.2 | 0.3 | 0.4 | 0.5 |
K5 | 0.1-0.2 | 0.1-0.2 | 0.2 | 0.3 | 0.4 | 0.5 |
N1.1 | 0.1-0.2 | 0.1-0.2 | 0.2-0.3 | 0.3-0.4 | 0.4-0.5 | 0.5 |
N1.2 | 0.1-0.2 | 0.1-0.2 | 0.2-0.3 | 0.3-0.4 | 0.4-0.5 | 0.5 |
N1.3 | 0.1-0.2 | 0.1-0.2 | 0.2-0.3 | 0.3-0.4 | 0.4-0.5 | 0.5 |
N1.4 | 0.1-0.2 | 0.1-0.2 | 0.2-0.3 | 0.3-0.4 | 0.4-0.5 | 0.5 |
N2 | 0.1-0.2 | 0.1-0.2 | 0.2-0.3 | 0.3-0.4 | 0.4-0.5 | 0.5 |
N3.1 | 0.1-0.2 | 0.1-0.2 | 0.2-0.3 | 0.2-0.3 | 0.3 | 0.5 |
N3.2 | 0.1-0.2 | 0.1-0.2 | 0.2-0.3 | 0.2-0.3 | 0.3 | 0.3-0.4 |
N3.3 | 0.1-0.2 | 0.1-0.2 | 0.2-0.3 | 0.2-0.3 | 0.3 | 0.3-0.4 |
N3.4 | 0.1-0.2 | 0.1-0.2 | 0.2-0.3 | 0.2-0.3 | 0.3 | 0.3-0.4 |
N4 | 0.1-0.2 | 0.1-0.2 | 0.2-0.3 | 0.2-0.3 | 0.3 | 0.3-0.4 |
S1 | 0.1-0.2 | 0.1-0.2 | 0.2 | 0.2-0.3 | 0.3-0.4 | 0.4-0.5 |
S2 | 0.1-0.2 | 0.1-0.2 | 0.2 | 0.2 | 0.3 | 0.3-0.4 |
S3 | 0.1-0.2 | 0.1-0.2 | 0.2 | 0.2 | 0.3 | 0.3-0.4 |
S4 | 0.1-0.2 | 0.1-0.2 | 0.2 | 0.2-0.3 | 0.3-0.4 | 0.3-0.4 |
S5 | 0.1-0.2 | 0.1-0.2 | 0.2 | 0.2-0.3 | 0.3-0.4 | 0.3-0.4 |
S6 | 0.1-0.2 | 0.1-0.2 | 0.2 | 0.2-0.3 | 0.3-0.4 | 0.3-0.4 |
H1 | 0.1-0.2 | 0.1-0.2 | 0.2 | 0.2 | 0.3 | 0.3-0.4 |
H2 | 0.1-0.2 | 0.1-0.2 | 0.2 | 0.2 | 0.3 | 0.3-0.4 |
H3 | 0.1-0.2 | 0.1-0.2 | 0.2 | 0.2 | 0.3 | 0.3-0.4 |
H4 | 0.1-0.2 | 0.1-0.2 | 0.2 | 0.2 | 0.3 | 0.3-0.4 |
Ø, Zoll | ||||||
Werkstoff | 0.0394-0.1181 | 0.1181-0.1969 | 0.1969-0.3937 | 0.3937-0.7874 | 0.7874-1.1811 | >1.1811 |
P1 | 0,004-0,008 | 0,004-0,008 | 0,008 | 0,008-0,012 | 0,012-0,016 | 0,016-0,020 |
P2 | 0,004-0,008 | 0,004-0,008 | 0,008 | 0,008 | 0,012 | 0,016-0,020 |
P3 | 0,004-0,008 | 0,004-0,008 | 0,008 | 0,008 | 0,012 | 0,016-0,020 |
P4 | 0,004-0,008 | 0,004-0,008 | 0,008 | 0,008-0,012 | 0,012-0,016 | 0,016-0,020 |
P5 | 0,004-0,008 | 0,004-0,008 | 0,008 | 0,008 | 0,012 | 0,016-0,020 |
M1 | 0,004-0,008 | 0,004-0,008 | 0,008 | 0,008 | 0,012 | 0,016-0,020 |
M2 | 0,004-0,008 | 0,004-0,008 | 0,008 | 0,008 | 0,012 | 0,016-0,020 |
M3 | 0,004-0,008 | 0,004-0,008 | 0,008 | 0,008 | 0,012 | 0,016-0,020 |
K1 | 0,004-0,008 | 0,004-0,008 | 0,008 | 0,008 | 0,012 | 0,020 |
K2 | 0,004-0,008 | 0,004-0,008 | 0,008 | 0,008-0,012 | 0,012-0,016 | 0,016-0,020 |
K3 | 0,004-0,008 | 0,004-0,008 | 0,008 | 0,012 | 0,016 | 0,020 |
K4 | 0,004-0,008 | 0,004-0,008 | 0,008 | 0,012 | 0,012 | 0,020 |
K5 | 0,004-0,008 | 0,004-0,008 | 0,008 | 0,012 | 0,012 | 0,020 |
N1,1 | 0,004-0,008 | 0,004-0,008 | 0,008-0,012 | 0,012-0,016 | 0,016-0,020 | 0,020 |
N1,2 | 0,004-0,008 | 0,004-0,008 | 0,008-0,012 | 0,012-0,017 | 0,016-0,020 | 0,020 |
N1,3 | 0,004-0,008 | 0,004-0,008 | 0,008-0,012 | 0,012-0,018 | 0,016-0,020 | 0,020 |
N1,4 | 0,004-0,008 | 0,004-0,008 | 0,008-0,012 | 0,012-0,019 | 0,016-0,020 | 0,020 |
N2 | 0,004-0,008 | 0,004-0,008 | 0,008-0,012 | 0,012-0,020 | 0,016-0,020 | 0,020 |
N3,1 | 0,004-0,008 | 0,004-0,008 | 0,008-0,012 | 0,008-0,012 | 0,012 | 0,020 |
N3,2 | 0,004-0,008 | 0,004-0,008 | 0,008-0,012 | 0,008-0,012 | 0,012 | 0,016-0,020 |
N3,3 | 0,004-0,008 | 0,004-0,008 | 0,008-0,012 | 0,008-0,012 | 0,012 | 0,016-0,020 |
N3,4 | 0,004-0,008 | 0,004-0,008 | 0,008-0,012 | 0,008-0,012 | 0,012 | 0,016-0,020 |
N4 | 0,004-0,008 | 0,004-0,008 | 0,008-0,012 | 0,008-0,012 | 0,012 | 0,016-0,020 |
S1 | 0,004-0,008 | 0,004-0,008 | 0,008 | 0,008-0,012 | 0,012-0,016 | 0,016-0,020 |
S2 | 0,004-0,008 | 0,004-0,008 | 0,008 | 0,008 | 0,012 | 0,016-0,020 |
S3 | 0,004-0,008 | 0,004-0,008 | 0,008 | 0,008 | 0,012 | 0,016-0,020 |
S4 | 0,004-0,008 | 0,004-0,008 | 0,008 | 0,008-0,012 | 0,012-0,016 | 0,016-0,020 |
S5 | 0,004-0,008 | 0,004-0,008 | 0,008 | 0,008-0,012 | 0,012-0,016 | 0,016-0,020 |
S6 | 0,004-0,008 | 0,004-0,008 | 0,008 | 0,008-0,012 | 0,012-0,016 | 0,016-0,020 |
H1 | 0,004-0,008 | 0,004-0,008 | 0,008 | 0,008 | 0,012 | 0,016-0,020 |
H2 | 0,004-0,008 | 0,004-0,008 | 0,008 | 0,008 | 0,012 | 0,016-0,020 |
H3 | 0,004-0,008 | 0,004-0,008 | 0,008 | 0,008 | 0,012 | 0,016-0,020 |
H4 | 0,004-0,008 | 0,004-0,008 | 0,008 | 0,008 | 0,012 | 0,016-0,020 |
Suchen Sie Werkzeugempfehlungen?
Hier finden Sie unsere Zerspanungswerkzeuge chevron_right
Brauchen Sie Beratung?
Stellen Sie uns eine Frage chevron_right
Was es sonst noch über die Grundlagen unserer Metallzerspanung zu lernen gibt?
Registrieren Sie sich für unser kostenloses E-Learning Programm chevron_right
Bauteilspannung
- Achten Sie auf eine sichere Bauteilspannung
- Stellen Sie bei Durchgangsbohrungen ausreichend Platz für die abzuführenden Späne sicher
- Beim Reiben dünnwandiger Bauteile darauf achten, dass die Spannkraft von allen Seiten gleichmäßig auf das Bauteil wirkt

Kühlschmierstoff beim Reiben
Die Hauptaufgabe des Kühlschmierstoffs besteht darin, das Kühlmittel direkt an die Schneidzone zu bringen, um eine höhere Standzeit des Werkzeugs und eine gute Spanabfuhr zu erreichen.
- Bei gerade genuteten Vollhartmetall-Reibahlen verläuft die innere Kühlmittelzufuhr axial, bei gedrallten Spankanälen dagegen lateral
- Emulsion als Kühlschmierstoff sorgt in der Regel für längere Standzeit als Öl
- Der empfohlene Druck liegt bei 15 bar
- Ein erhöhter Kühlschmierstoffdruck kann sich positiv auf Spankontrolle und Spanbruch auswirken
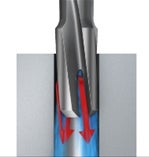
Spiral genutet – laterale Kühlschmierstoffzufuhr
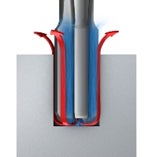
Gerade genutet – axiale Kühlschmierstoffzufuhr
Position der Reibahle
Um Vibrationen zu vermeiden, sollte der Versatz zwischen vorgefertigter Bohrung und Reibahle so gering wie möglich sein.
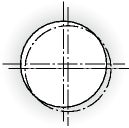
Schnittunterbrechungen
Reibahle können normalerweise für folgende Bearbeitungen eingesetzt werden:
- Kreuzbohrungen unter 2 mm im Durchmesser, wenn der Durchmesser des Reibahlenkopfes kleiner als 22 mm (0.866 Zoll) ist
- Kreuzbohrungen unter 3 mm Durchmesser, wenn der Durchmesser des Reibahlenkopfes 22 mm (0.866 Zoll) oder größer ist.
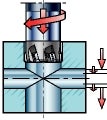
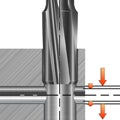
Bearbeitung einer gewinkelten oder schrägen Fläche
Bei der Bearbeitung gewinkelter oder schräger Flächen mit einem Reibwerkzeug:
- Empfohlener maximaler Eingangswinkel: 5 Grad
- Achten Sie auf bestmögliche Rundlaufgenauigkeit
- Bei der Verwendung von Vollhartmetall-Reibwerkzeugen wenden Sie sich bitte an einen technischen Experten
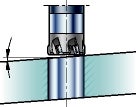
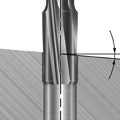
Reiben einer vorgefertigten Bohrung
Das Reiben ist nicht zum Korrigieren von Lage- oder Geradheitsfehlern der vorgefertigten Bohrung geeignet
- Die Geradheit der vorgefertigten Bohrung sollte weniger als 0,05 mm betragen
- Darauf achten, dass der Durchmesser der vorgefertigten Bohrung die empfohlenen radialen Schnitttiefen erlaubt
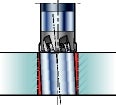
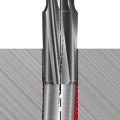
Suchen Sie Werkzeugempfehlungen?
Hier finden Sie unsere Zerspanungswerkzeuge chevron_right
Brauchen Sie Beratung?
Stellen Sie uns eine Frage chevron_right
Was es sonst noch über die Grundlagen unserer Metallzerspanung zu lernen gibt?
Registrieren Sie sich für unser kostenloses E-Learning Programm chevron_right