Schruppen
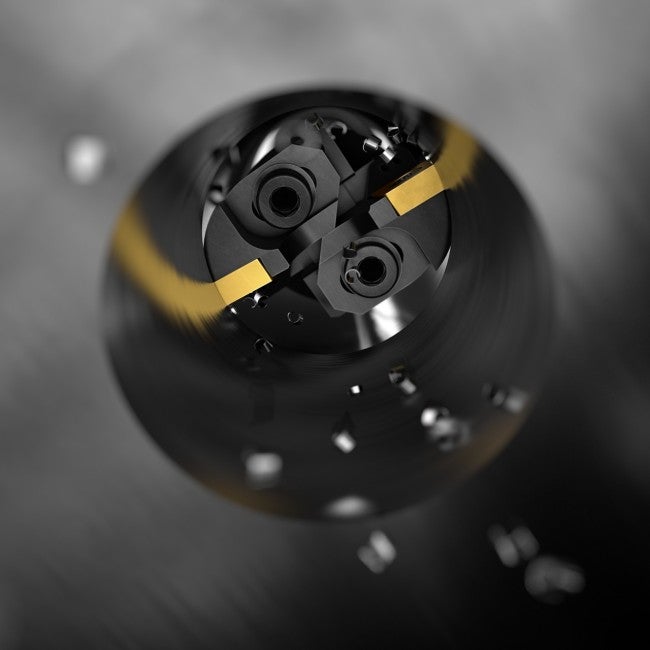
Das Schruppen erfolgt mit Fokus auf die Zerspanung und dient der Erweiterung einer bestehenden Bohrung. Das Schruppen wird durchgeführt, um eine vorhandene Bohrung zu vergrößern, die durch Methoden wie Vorbearbeitung, Gießen oder Schmieden hergestellt wurde. Werkzeuge zum Schruppaufboren können auch zum produktiven Einschneiden- und Stufenaufbohren eingerichtet werden.
Produktives Aufbohren
Produktives Aufbohren ist die Grundeinrichtung für die meisten Aufbohranwendungen und die beste Wahl für höchste Priorität.
Es umfasst zwei oder drei Schneiden und wird für Schruppbearbeitungen von Bohrungen mit einer Toleranz von IT9 oder größer eingesetzt, bei denen die Zerspanungsrate oberste Priorität besitzt. Die Vorschubgeschwindigkeit wird ermittelt, indem der Vorschub für jede Wendeschneidplatte mit der Anzahl der Wendeschneidplatten multipliziert wird (fn = fz × z).
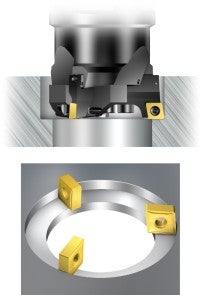
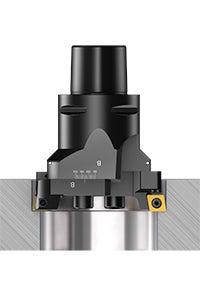
Stufenaufbohren
Bei einem Werkzeug zum Stufenaufbohren sind die Wendeschneidplatten auf verschiedene axiale Höhen und Durchmesser eingestellt. Diese Methode wird verwendet, wenn ein große radiale Schnitttiefe erforderlich ist, oder für eine verbesserte Spankontrolle in lang spanenden Werkstoffen, da die Spanbreite in mehrere kleinere, leicht zu handhabende Späne unterteilt werden kann. Die Anzahl der Werkzeuge und Werkzeugwechsel ist beim Stufenaufbohren möglicherweise geringer.
Die Vorschubrate und die erreichte Oberflächengüte sind die gleichen wie bei Verwendung von nur einer Wendeschneidplatte (fn=fz). Die erreichte Bohrungstoleranz ist IT9 oder größer.
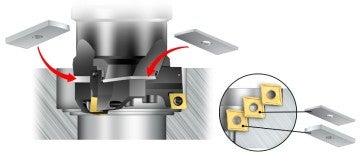
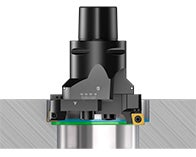
Einschneidenaufbohren
Beim einschneidigen Aufbohren wird nur eine Schneide verwendet. Dies kann speziell in Werkstoffen vorteilhaft sein, bei denen sich die Spankontrolle schwierig gestaltet (z. B. bei lang spanenden Werkstoffen), oder wenn die Werkzeugleistung begrenzt ist (fn = fz).
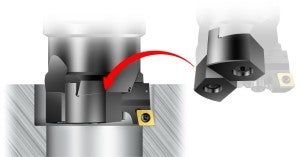
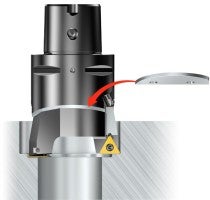
Wahl der Wendeschneidplatte zum Schruppaufbohren
Zur Erzielung guter Spankontrolle und Bearbeitungsleistung sind Plattenausführung, Einstellwinkel (Eintrittswinkel), Geometrie und Sorte sorgfältig auszuwählen.
Wendeschneidplatten mit positiver oder negativer Grundform
Negative Wendeschneidplatten: Bei stabilen Bedingungen negative Wendeschneidplatten verwenden, um eine höhere Effektivität zu erzielen oder schwierige Anwendungen bewältigen zu können, die stabile Wendeschneidplatten und eine erhöhte Prozesssicherheit erfordern.
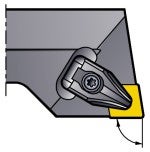
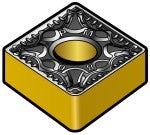

Positive Wendeschneidplatten: Beim Schruppaufbohren ist es von Vorteil, Wendeschneidplatten mit positiven Grundformen zu verwenden, da sie, verglichen mit negativen Wendeschneidplatten, für niedrigere Schnittkräfte sorgen. Ein kleiner Spitzenwinkel und ein kleiner Eckenradius tragen ebenfalls zu geringeren Schnittkräften bei.
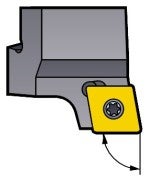
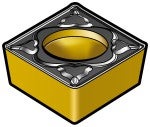
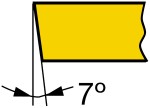
Einstellwinkel (Eintrittswinkel) beim Schruppaufbohren
Der Einstellwinkel (Eintrittswinkel) von Aufbohrwerkzeugen wirkt sich auf die Richtung und das Ausmaß der axialen und radialen Kräfte aus. Ein großer Einstellwinkel (kleiner Eintrittswinkel) erzeugt große axiale Schnittkräfte, während ein kleiner Einstellwinkel (großer Eintrittswinkel) zu einer größeren radialen Schnittkraft führt.
90° Einstellwinkel (0° Eintrittswinkel)
Erste Wahl für allgemeine Arbeiten, Stufenaufbohren und Eckenbearbeitung.
84°/75° Einstellwinkel (6°/25° Eintrittswinkel)
Für Schnittunterbrechungen, Sandeinschlüsse, Paket-Aufbohren usw. Nur Durchgangsbohrungen.
95° Einstellwinkel (-5° Eintrittswinkel)
Für hohe Vorschübe oder verbesserte Oberflächengüte mit Wiper-Wendeschneidplatten unter stabilen Bedingungen.
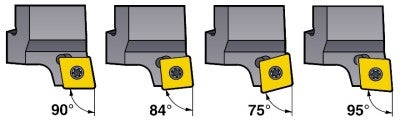
Positive Wendeschneidplatten
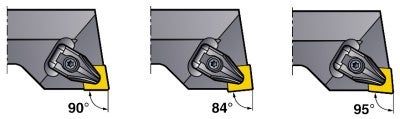
Negative Wendeschneidplatten
Wendeschneidplattengeometrien und -sorten zum Aufbohren
Die Wahl der Wendeschneidplattengeometrie und -sorte wird durch den Bauteilwerkstoff, die Bearbeitungsart und den Bearbeitungsbedingungen bestimmt. Zum Aufbohren werden Wendeschneidplatten zum Drehen verwendet. Weitere Informationen hierzu, siehe Wahl der richtigen Wendeschneidplatte zum Drehen.
Empfehlungen
- Für große Schnitttiefen eine Geometrie zum Schruppen verwenden
- Für kleinere Schnitttiefen oder besseren Spanbruch eine mittlere Geometrie wählen
- Ein großer Eckenradius (RE) verbessert die Prozesssicherheit und ermöglicht einen höheren Vorschub, kann jedoch zu Vibrationen führen. Empfohlener Startwert für Eckenradius ist 0.08 mm (0.031 Zoll)
Suchen Sie Werkzeugempfehlungen?
Hier finden Sie unsere Zerspanungswerkzeuge chevron_right
Brauchen Sie Beratung?
Stellen Sie uns eine Frage chevron_right
Was es sonst noch über die Grundlagen unserer Metallzerspanung zu lernen gibt?
Registrieren Sie sich für unser kostenloses E-Learning Programm chevron_right
Überlegungen zur Maschine beim Schruppaufbohren
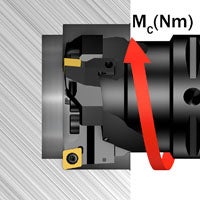
Beim Schruppen sicherstellen, dass die Maschine die erforderliche Drehzahl und die Leistung für die spezifische Aufbohranwendung aufbringen kann. Vorschub, Anzahl der Wendeschneidplatten, Bohrungsdurchmesser und Schnitttiefe sind die Parameter mit den größten Auswirkungen.
Aufbohren großer Durchmesser
Bohrungen mit großem Durchmesser erfordern ein höheres Drehmoment als Bohrungen mit kleinem Durchmesser. Aufbohrwerkzeuge zum Schruppen großer Durchmesser haben größere Wendeschneidplatten und können daher größere Schnitttiefen bewältigen als Werkzeuge für kleinere Durchmesser. Sicherstellen, dass die Maschine die benötigte Leistung und das benötigte Drehmoment liefert.
Aufbohren von Grundbohrungen
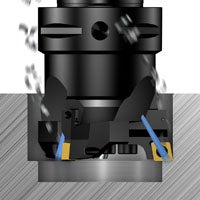
Bei der Herstellung von Grundbohrungen ist eine effiziente und ordnungsgemäße Spanabfuhr ein entscheidender Faktor.
- Korrekte Schnittdaten sind für eine gute Spanbildung wichtig
- Sicherstellen, dass die Späne nicht verklemmen oder den Verschleiß der Wendeschneidplatten erhöhen
- Druck und Durchfluss des Kühlschmierstoffs sollten ausreichen, um die Späne abzuführen.
- Vertikalmaschinen sind im Hinblick auf eine effiziente Spanabfuhr kritischer als Horizontalmaschinen
Aufbohren mit Schnittunterbrechungen
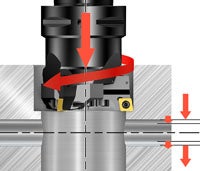
Die Bearbeitung mit Schnittunterbrechungen wie bei Kreuzbohrungen stellt hohe Ansprüche an die Schnittbedingungen der Wendeschneidplatte.
- Zähe Sorte wählen
- Eine stabile, quadratische Wendeschneidplatte mit negativer Grundform für erhöhte Prozesssicherheit bei stabilen Bedingungen wählen
- Bei großen Unterbrechungen die Schnittdaten verringern
Aufbohren mit Sandeinschlüssen – gegossene Werkstücke
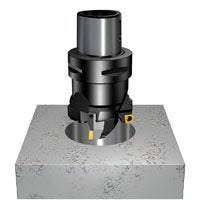
Sandeinschlüsse in Gusswerkstücken erhöhen den Verschleiß der Wendeschneidplatten.
- Zähe Sorte wählen
- Schnittdaten verringern
- Eine stabile, quadratische Wendeschneidplatte mit negativer Grundform für erhöhte Prozesssicherheit und minimierten Verschleiß wählen.
Bohrungsherstellung durch Brennschneiden
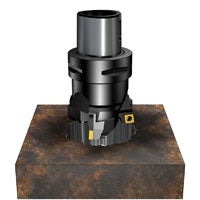
Durch Brennschneiden erstellte Bohrungen können an ihrer Oberfläche über unterschiedliche Härte verfügen und verursachen einen größeren Verschleiß an den Wendeschneidplatten.
- Zähe Sorte wählen
- Schnittdaten verringern
- Eine stabile, quadratische Wendeschneidplatte mit negativer Grundform für erhöhte Prozesssicherheit und minimierten Verschleiß wählen.
Aufbohren mit großen Schnitttiefen
Wird eine besonders große Schnitttiefe benötigt, ist das Stufenaufbohren möglicherweise eine gute Alternative. Sicherstellen, dass die Maschine die benötigte Leistung und das benötigte Drehmoment liefert.
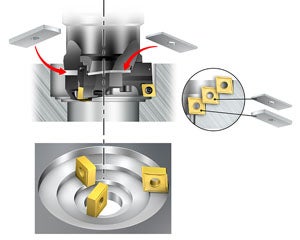
Aufbohren exzentrischer Bohrungen
Sind die Zentrumslinien der vorgefertigten Bohrung und das Aufbohrwerkzeugs nicht konzentrisch, könnte die Schnitttiefe auf einer Seite der Bohrung beträchtlich größer ausfallen. Dies tritt häufig bei Gusswerkstücken auf.
Eine gute Lösung für diese Anwendungen ist das Stufenaufbohren, um die große Schnitttiefe zu erreichen. Asymmetrische Schnittkräfte können das Werkzeug auslenken und ein geringes Verrutschen aus der Mitte kann dann Vibrationen hervorrufen, insbesondere bei Bearbeitungen mit großem Überhang.
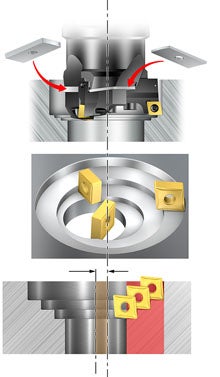
Checkliste für Schruppaufbohranwendungen
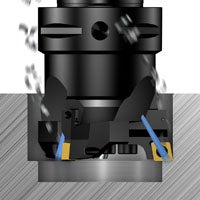
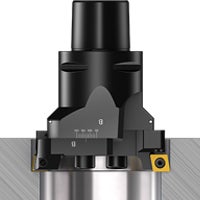
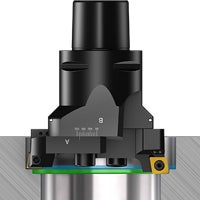
- Produktives Aufbohren (mit drei oder zwei Schneiden), Stufenaufbohren oder Einschneidenaufbohren wählen
- Die größtmögliche Kupplungsgröße wählen
- Geeigneten Einstellwinkel wählen
- Einwandfreie Spankontrolle gewährleisten Kurze/harte Späne können zu Vibrationen führen, und lange Späne können die Oberflächengüte verschlechtern oder Plattenbruch verursachen
- Horizontale Bearbeitung und Kühlschmierstoff können die Spanabfuhr in Grundbohrungen verbessern
- Wendeschneidplattensorte und -geometrie wählen:
- Kürzestmöglichen Überhang wählen, und bei Überhängen größer als 4xKupplungsgröße schwingungsgedämpfte Bohrstangen verwenden
- Geeignete Schnittdaten wählen und den Überhang berücksichtigen.
Hinweis: Nicht den maximal empfohlenen Vorschub und ap zur gleichen Zeit verwenden. Die maximal empfohlene Startgeschwindigkeit beträgt 200 m/min (656 Fuß/min) für eine ordnungsgemäße Spanabfuhr - Ein großer Eckenradius (RE) verbessert die Prozesssicherheit und ermöglicht einen höheren Vorschub, kann jedoch zu Vibrationen führen. Empfohlener Startwert für Eckenradius ist 0.8 mm (0.031 Zoll)
- Positive Wendeschneidplatten verwenden, da sie im Vergleich zu negativen Wendeschneidplatten niedrige Schnittkräfte erzeugen
- Bei stabilen Bedingungen negative Wendeschneidplatten verwenden, um eine höhere Wirtschaftlichkeit zu erreichen oder schwierige Anwendungen bewältigen zu können, die stabile Wendeschneidplatten und eine erhöhte Prozesssicherheit erfordern.
- Ein unzureichender Schneideneingriff kann durch Reibung während der Bearbeitung zu erhöhten Vibrationen führen
- Eine sichere Spannung mit Flächenkontakt zur Spindel erhöht die Stabilität
- Ein übermäßiges Eingreifen der Schneidkante (große Schnitttiefe und/oder großer Vorschub) kann die Vibrationen erhöhen
- Sicherstellen, dass die Maschine das erforderliche Drehmoment und die Leistung für die spezifische Aufbohranwendung aufbringen kann
- Wiper-Wendeschneidplatten können verwendet werden, um die Oberflächengüte zu verbessern oder den Vorschub zu erhöhen, werden jedoch für instabile Bedingungen und lange Überhänge nicht empfohlen.
- Auf ordnungsgemäßes Einspannen von Aufbohrwerkzeug und Werkstück achten
- Kühlschmierstoff verwenden, um die Spanabfuhr, Standzeit und Bohrungsgeometrie zu verbessern
- Für eine optimale Leistung des Mehrschneiden-Aufbohrwerkzeugs sollte im höheren Bereich der ap und der Vorschubempfehlungen bearbeitet werden, insbesondere bei längeren Überhängen. Hinweis: Nicht den maximal empfohlenen Vorschub und ap zur gleichen Zeit verwenden
- Ein produktives Aufbohren ermöglicht eine maximale Vorschubgeschwindigkeit. Wird eine relativ hohe Schnitttiefe benötigt, ist eine Stufen-Bearbeitung möglicherweise produktiver, da so die Zykluszeiten minimiert und die Anzahl der Werkzeuge verringert werden können
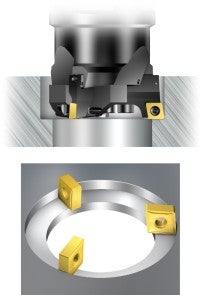
Siehe auch, Aufbohren - Korrekte Anwendung für allgemeine Empfehlungen.
Für Empfehlungen zu Drehmomentwerten, siehe Bedienanleitung unten.
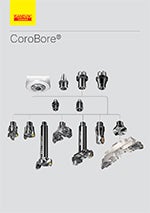
Suchen Sie Werkzeugempfehlungen?
Hier finden Sie unsere Zerspanungswerkzeuge chevron_right
Brauchen Sie Beratung?
Stellen Sie uns eine Frage chevron_right
Was es sonst noch über die Grundlagen unserer Metallzerspanung zu lernen gibt?
Registrieren Sie sich für unser kostenloses E-Learning Programm chevron_right
CoroMill® Plura Gannet - optimized mill for HRSA roughing
CoroMill® Plura Gannet, a solid end mill especially developed for plunging in HRSA.... open_in_new
M5F90 milling cutter – one shot roughing and finishing of thin wall aluminium parts
Demo film presenting M5F90. This is a concept face-milling cutter that enables roughing... open_in_new
CM300 roughing
open_in_new
M5R90 milling cutter – for roughing and semi-finishing of aluminium automotive parts
Demo film presenting M5R90. This is our first choice for roughing to semi-finishing... open_in_new