การสึกหรอและการแก้ปัญหาการเจาะ
การแก้ปัญหา
- ดอกสว่านเม็ดมีด
- ดอกสว่านแบบเปลี่ยนปลายได้
- ดอกสว่านคาร์ไบด์
ดอกสว่านเม็ดมีด
รูเจาะใหญ่กว่าที่ต้องการ
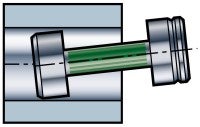
การเจาะแบบหมุนดอกสว่าน
- เพิ่มปริมาณน้ำหล่อเย็น ทำความสะอาดกรอง และล้างสิ่งอุดตันในรูจ่ายน้ำหล่อเย็นภายในตัวดอกสว่าน
- ลองใช้เม็ดมีดตัวนอกที่มีความเหนียวมากขึ้น (ใช้เม็ดมีดตัวในแบบเดิม)
การเจาะแบบหมุนชิ้นงาน
- ตรวจเช็คศูนย์ของเครื่องกลึง
- หมุนดอกสว่าน 180 องศา
- ลองใช้เม็ดมีดตัวนอกที่มีความเหนียวมากขึ้น (ใช้เม็ดมีดตัวในแบบเดิม)
รูเจาะเล็กกว่าที่ต้องการ
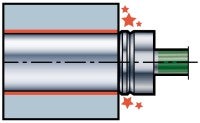
การเจาะแบบหมุนดอกสว่าน
- เพิ่มปริมาณน้ำหล่อเย็น ทำความสะอาดกรอง และล้างสิ่งอุดตันในรูจ่ายน้ำหล่อเย็นภายในตัวดอกสว่าน
- ลองใช้เม็ดมีดตัวในที่มีความเหนียวมากขึ้นและใช้เม็ดมีดตัวนอกที่มีหน้าลายแบบแรงตัดต่ำ
การเจาะแบบหมุนชิ้นงาน
- ดอกสว่านอยู่กบถ: ตรวจเช็คศูนย์ของเครื่องกลึง
- ดอกสว่านอยู่กบถ: หมุนดอกสว่าน 180 องศา
- ลองใช้เม็ดมีดตัวในที่มีความเหนียวมากขึ้นและใช้เม็ดมีดตัวนอกที่มีหน้าลายแบบแรงตัดต่ำ
มีแกนจากการเจาะเหลืออยู่ในรู
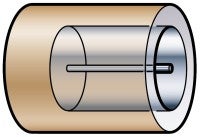
การเจาะแบบหมุนดอกสว่าน
- เพิ่มปริมาณน้ำหล่อเย็น ทำความสะอาดกรอง และล้างสิ่งอุดตันในรูจ่ายน้ำหล่อเย็นภายในตัวดอกสว่าน
- ลองใช้เม็ดมีดตัวนอกหน้าลายอื่นๆ และปรับอัตราป้อนงานให้อยู่ภายในช่วงค่าการตัดที่แนะนำ
- ลดระยะยื่นของดอกสว่านให้สั้นลง
การเจาะแบบหมุนชิ้นงาน
- ตรวจเช็คศูนย์ของเครื่องกลึง
- เพิ่มปริมาณน้ำหล่อเย็น ทำความสะอาดกรอง และล้างสิ่งอุดตันในรูจ่ายน้ำหล่อเย็นภายในตัวดอกสว่าน
- ลดระยะยื่นของดอกสว่านให้สั้นลง
- ลองใช้เม็ดมีดตัวนอกหน้าลายอื่นๆ และปรับอัตราป้อนงานให้อยู่ภายในช่วงค่าการตัดที่แนะนำ
การสั่นสะท้าน
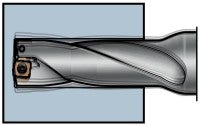
- ลดระยะยื่นของดอกสว่านให้สั้นลง และเพิ่มความมั่นคงในการจับยึดชิ้นงาน
- ลดความเร็วตัดลง
- ลองใช้เม็ดมีดตัวนอกหน้าลายอื่นๆ และปรับอัตราป้อนงานให้อยู่ภายในช่วงค่าการตัดที่แนะนำ
เครื่องจักรมีแรงบิดไม่พอ
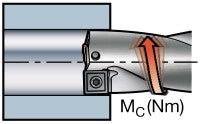
- ลดอัตราป้อน
- เลือกหน้าลายที่มีแรงตัดต่ำ เพื่อลดแรงตัด
เครื่องจักรมีกำลังไม่พอ
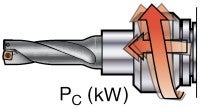
- ลดความเร็ว
- ลดอัตราป้อน
- เลือกหน้าลายที่มีแรงตัดต่ำ เพื่อลดแรงตัด
รูเจาะไม่สมมาตร
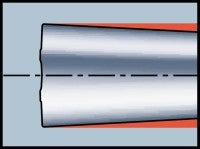
กันรูใหญ่กว่าปากรู (เนื่องจากมีเศษติดที่เม็ดมีดตัวใน)
- เพิ่มปริมาณน้ำหล่อเย็น ทำความสะอาดกรอง และล้างสิ่งอุดตันในรูจ่ายน้ำหล่อเย็นภายในตัวดอกสว่าน
- ลองใช้เม็ดมีดตัวนอกหน้าลายอื่นๆ และปรับอัตราป้อนงานให้อยู่ภายในช่วงค่าการตัดที่แนะนำ
- ลดระยะยื่นของดอกสว่านให้สั้นลง
เครื่องมามีอายุการใช้งานสั้น
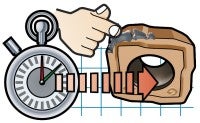
- ตรวจสอบค่าการตัดที่แนะนำ
- เพิ่มปริมาณน้ำหล่อเย็น ทำความสะอาดกรอง และล้างสิ่งอุดตันในรูจ่ายน้ำหล่อเย็นภายในตัวดอกสว่าน
- ลดระยะยื่นของดอกสว่านให้สั้นลง เพิ่มความมั่นคงในการจับยึดชิ้นงาน และตรวจสอบการจับยึดเครื่องมือ
- ตรวจหาความเสียหายของปลายสว่าน/ช่องใส่เม็ดมีดและสกรู
- ดูในส่วนการสึกหรอทั่วไปสำหรับวิธีแก้ปัญหาแต่ละประเภทโดยเฉพาะ
- ถ้าสามารถทำได้ ให้เลือกเกรดที่ต้านทานการสึกหรอได้มากขึ้น
สกรูยึดเม็ดมีดหัก
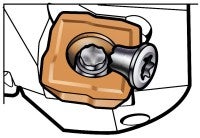
- ขันสกรูโดยใช้ไขควงวัดแรงขัน รวมกับจาระบี Molykote
ผิวงานมีคุณภาพต่ำ
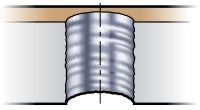
- จำเป็นที่จะต้องมีการควบคุมเศษที่มีประสิทธิภาพ
- ลดอัตราป้อนงาน (ถ้าจำเป็นต้องใช้ vf เท่าเดิม ให้เพิ่มความเร็วด้วยเช่นกัน)
- เพิ่มปริมาณน้ำหล่อเย็น ทำความสะอาดกรอง และล้างสิ่งอุดตันในรูจ่ายน้ำหล่อเย็นภายในตัวดอกสว่าน
- ลดระยะยื่นของดอกสว่านให้สั้นลง เพิ่มความมั่นคงในการจับยึดชิ้นงาน
เศษติดในร่องดอกสว่าน
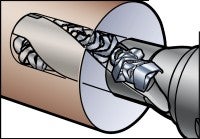
สาเหตุมาจากเศษยาว
- ตรวจสอบหน้าลายและค่าการตัดที่แนะนำ
- เพิ่มปริมาณน้ำหล่อเย็น ทำความสะอาดกรอง และล้างสิ่งอุดตันในรูจ่ายน้ำหล่อเย็นภายในตัวดอกสว่าน
- ลดอัตราป้อนงานลงให้อยู่ภายในช่วงค่าการตัดที่แนะนำ
- เพิ่มความเร็วตัดให้อยู่ภายในช่วงค่าการตัดที่แนะนำ
การโก่งตัว
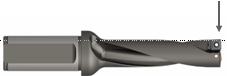
- พิกัดความเผื่อของรูอยู่นอกช่วงที่ต้องการ
- ผิวสำเร็จมีคุณภาพต่ำ - มีรอยจากการถอนดอกสว่าน
- การสึกหรอที่ตัวเครื่องมือ
- เม็ดมีดหัก
สาเหตึ | วิธีแก้ไข |
แรงตัดสูงเกินไป | 1. เลือกหน้าลายที่มีรัศมีมุมเล็กลง 2. ลดอัตราป้อนงาน 3. ลดอัตราป้อนงานขณะเจาะเข้า |
ความมั่นคงไม่ดีพอ | 1. เพิ่มความมั่นคง 2. เลือกตัวดอกสว่านที่สั้นลง (4xD -> 3xD) |
ปัญหากับรูปร่างของเศษ
วัสดุที่เกิดเศษยาว เช่น เหล็กสเตนเลสหรือเหล็กกล้าคาร์บอนต่ำ
ผลที่เกิดขึ้น | สาเหตุที่เป็นไปได้ | วิธีแก้ไข |
เศษมีรูปร่างไม่ดี/เศษยาว - เศษตัด | หน้าลายไม่เหมาะสม | เลือกหน้าลาย –LM |
ผิวงานมีคุณภาพต่ำ | ความเร็วตัดต่ำเกินไป | เพิ่มความเร็วตัด |
เม็ดมีดหรือเครื่องมือหัก | อัตราป้อนงานสูงเกินไป | ลดอัตราป้อนงาน |
วัสดุที่เกิดเศษสั้น เช่น เหล็กกล้าปกติ
ผลที่เกิดขึ้น | สาเหตุที่เป็นไปได้ | วิธีแก้ไข |
เศษมีรูปร่างไม่ดี/เศษยาว - เศษตัด | การเจาะแบบหมุนชิ้นงาน (เครื่องกลึง) | เลือกหน้าลายสำหรับอัตราป้อนงานต่ำ (GR -> GM) |
ผิวงานมีคุณภาพต่ำ | หน้าลายไม่เหมาะสม | เพิ่มอัตราป้อนงาน |
เม็ดมีดหรือเครื่องมือหัก | 1. ความเร็วตัดต่ำเกินไป 2. อัตราป้อนงานต่ำเกินไป | เพิ่มความเร็วตัด |
ดอกสว่านแบบเปลี่ยนปลายได้
พิกัดความเผื่อของรอยนอกช่วงที่ต้องการ
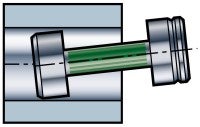
- ตรวจหาการสึกหรอของปลายสว่าน
- ตรวจหาการเบี่ยงเบนหนีศูนย์
- ลดอัตราป้อนงานลง
- ตรวจสอบความมั่นคงของชิ้นงาน การจับยึดเครื่องมือ และผิวของชิ้นงาน
- ใช้ดอกสว่านเจาะนำ/ดอกสว่านเจาะเฉพาะจุดสำหรับการเจาะรูลึก
- ในกรณีที่เป็นการเจาะแบบหมุนชิ้นงาน - ตรวจเช็คศูนย์ของเครื่องกลึง
การสั่นสะเทือน
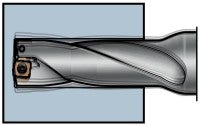
- ลดระยะยื่นของดอกสว่านให้สั้นลง เพิ่มความมั่นคงของชิ้นงาน ตรวจสอบการจับยึดเครื่องมือ
- ลดความเร็วตัดลง
- ปรับอัตราป้อนงาน/รอบ
เครื่องจักรมีกำลังหรือแรงบิดไม่พอ
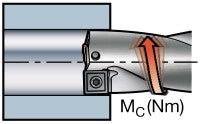
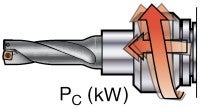
- ลดความเร็ว
- ลดอัตราป้อน
- เลือกหน้าลายที่มีแรงตัดต่ำ เพื่อลดแรงตัด
รูไม่กลม
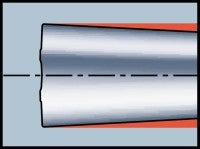
ปากกว้างกว่า
- ตรวจหาการเบี่ยงเบนหนีศูนย์
- ปรับอัตราป้อนงาน
- ลดระยะยื่นของดอกสว่านให้สั้นลงและตรวจสอบการจับยึดเครื่องมือ
- เจาะรูนำด้วยดอกสว่านสั้นก่อน สำหรับการเจาะรูลึก
เครื่องมือมีอายุการใช้งานสั้น
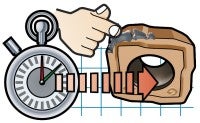
ตรวจสอบค่าการตัดที่แนะนำ
- เพิ่มปริมาณน้ำหล่อเย็น ทำความสะอาดกรอง และล้างสิ่งอุดตันในรูจ่ายน้ำหล่อเย็นภายในตัวดอกสว่าน
- ลดระยะยื่นของดอกสว่านให้สั้นลง เพิ่มความมั่นคงของชิ้นงาน และตรวจสอบการจับยึดเครื่องมือ
- ตรวจหาความเสียหายของปลายสว่าน/ช่องใส่เม็ดมีดและสกรู
- ดูในส่วนการสึกหรอทั่วไปสำหรับวิธีแก้ปัญหาแต่ละประเภทโดยเฉพาะ
- ถ้าสามารถทำได้ ให้เลือกเกรดที่ต้านทานการสึกหรอได้มากขึ้น
ผิวสำเร็จมีคุณภาพต่ำ
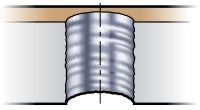
- จำเป็นที่จะต้องมีการควบคุมเศษที่มีประสิทธิภาพ
- ลดอัตราป้อนงาน (ถ้าจำเป็นต้องใช้ vf เท่าเดิม ให้เพิ่มความเร็วด้วยเช่นกัน)
- เพิ่มปริมาณน้ำหล่อเย็น ทำความสะอาดกรอง และล้างสิ่งอุดตันในรูจ่ายน้ำหล่อเย็นภายในตัวดอกสว่าน
- ลดระยะยื่นของดอกสว่านให้สั้นลง และเพิ่มความมั่นคงในการจับชิ้นงาน
เศษติดในร่องคายเศษของสว่าน
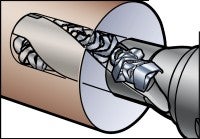
- ปรับค่าการตัดให้ควบคุมเศษได้อย่างมีประสิทธิภาพมากขึ้น
- เพิ่มปริมาณน้ำหล่อเย็น ทำความสะอาดกรอง ล้างสิ่งอุดตันในรูจ่ายน้ำหล่อเย็นภายในตัวดอกสว่าน ตรวจสอบความเข้มข้นของน้ำหล่อเย็น
- ปัญหาเศษติดสามารถทำให้ตัวดอกสว่านสึกหรอรุนแรงได้
- ทำความสะอาดเศษวัสดุชิ้นงานที่ติดอยู่บนตัวดอกสว่าน เพื่อป้องกันปัญหาเศษติด
เศษขณะเจาะเข้า
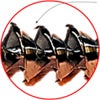
"หนาม" ที่ขอบนอกของเศษ
- อาจเกิดการสึกหรออย่างรุนแรงหากสามารถสังเกตเห็นหนามที่ขอบนอกของเศษขณะที่เริ่มเจาะ
- สาเหตุที่เป็นไปได้ - ความไม่สมดุลเนื่องจาก: การเบี่ยงเบนหมุนศูนย์การเจาะเข้าไปบนพื้นผิวเอียง อัตราป้อนงานสูงเกินไป สภาพการทำงานไม่มั่นคง/ไม่แข็งแรง การหัก/การสึกหรอที่มุม
การควบคุมเศษ - การเพิ่มประสิทธิภาพ
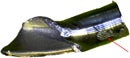
- รอยขีดขัดบนเศษตามภาพด้านบนเป็นสัญญาณบอกถึงปัญหาเศษติด ซึ่งจะส่งผลกระทบต่อคุณภาพของรู ดังนั้น เพื่อให้ได้รูที่มีคุณภาพดีขึ้น ขอแนะนำให้ลดอัตราป้อนงานลง และถ้าสามารถทำได้ ให้เพิ่มความเร็วตัด
ดอกสว่านคาร์ไบด์
เศษขณะเจาะเข้า – ดอกสว่านคาร์ไบด์/ดอกสว่านแบบเปลี่ยนปลายได้
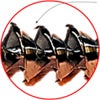
"หนาม" ที่ขอบนอกของเศษ
- อาจเกิดการสึกหรออย่างรุนแรงหากสามารถสังเกตเห็นหนามที่ขอบนอกของเศษขณะที่เริ่มเจาะ
- สาเหตุที่เป็นไปได้ - ความไม่สมดุลเนื่องจาก: การเบี่ยงเบนหมุนศูนย์การเจาะเข้าไปบนพื้นผิวเอียง อัตราป้อนงานสูงเกินไป สภาพการทำงานไม่มั่นคง/ไม่แข็งแรง การหัก/การสึกหรอที่มุม
การควบคุมเศษ - การเพิ่มประสิทธิภาพ
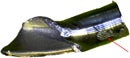
- รอยขีดขัดบนเศษตามภาพด้านบนเป็นสัญญาณบอกถึงปัญหาเศษติด ซึ่งจะส่งผลกระทบต่อคุณภาพของรู ดังนั้น เพื่อให้ได้รูที่มีคุณภาพดีขึ้น ขอแนะนำให้ลดอัตราป้อนงานลง และถ้าสามารถทำได้ ให้เพิ่มความเร็วตัด
ลักษณะการสึกหรอจากการเจาะ
- ดอกสว่านเม็ดมีด
- ดอกสว่านแบบเปลี่ยนปลายได้
- ดอกสว่านคาร์ไบด์
ดอกสว่านเม็ดมีด
การสึกหรอด้านหน้า
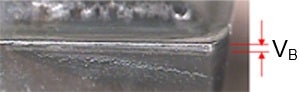
การสึกหรอด้านหน้าเป็นการสึกหรอที่ควรเกิดขึ้นเมื่อลดอกสว่านมีความสมดุล การสึกหรอด้านหน้าสามารถส่งผลให้
- ผิวงานมีคุณภาพต่ำ
- พิกัดความเผื่อของรูอยู่นอกช่วงที่ต้องการ
- ต้องใช้กำลังเพิ่มขึ้น
สาเหตุ | วิธีแก้ไข |
1. ความเร็วตัดสูงเกินไป (vc) | 1. ลดความเร็วตัด (vc) |
2. เกรดที่ใช้มีความต้านทานการสึกหรอไม่เพียงพอ | 2. เลือกเกรดที่ต้านทานการสึกหรอได้มากขึ้น |
การสึกหรอเป็นหลุมด้านบน
เม็ดมืดตัวใน
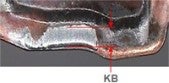
เม็ดมืดตัวนอก
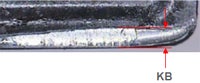
การสึกหรอเป็นหลุมด้านบนสามารถส่งผลให้
- คมตัดแข็งแรงน้อยลง ส่งผลให้คมตัดหักหรือเศษมีรูปร่างไม่ดี
- ผิวงานมีคุณภาพต่ำ
- ต้องใช้กำลังเพิ่มขึ้น
สาเหตุ | วิธีแก้ไข |
เม็ดมีดตัวใน: เศษ (วัสดุชิ้นงาน) มีคุณสมบัตเสียดสี | เม็ดมีดตัวใน: ลดอัตราป้อน |
เม็ดมีดตัวนอก: การสึกหรอจากการแพร่ซึมของวัสดุ เนื่องจากอุณหภูมิสูง (รุนแรงกว่าถ้าเป็นการเคลือบผิว PVD) | เม็ดมีดตัวนอก: 1. ลดความเร็วตัด 2. เลือกเกรดที่มีความต้านทานการสึกหรือสูงขึ้น (มักจะเป็นเกรด MT-CVD) |
เลือกคมตัดเป็นมุมบวกมากขึ้น เพื่อให้เศษมีรูปร่างดีขึ้น |
เกิดการเสียรูปถาวร
รอยยุบ
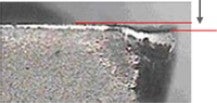
รอยกด
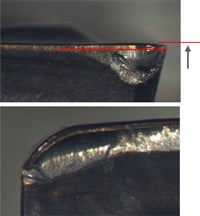
รอยยุบหรือรอยกดที่คมชัดอาจทำให้ประสิทธิภาพการควบคุมเศษแย่ลง คุณภาพผิวงานต่ำลง และไม่ได้พิกัดความเผื่อที่ต้องการ
สาเหตุ | วิธีแก้ไข |
อุณหภูมิการตัดสูงเกินไป รวมทั้งมีแรงกัดสูง (อัตราป้อนงานและ/หรือความแข็งของชิ้นงาน) | ลดอัตราป้อนงาน (fn) เลือกเกรดที่มีความต้านทานการเสียรูปถาวรสูงขึ้น (ความแข็งขณะร้อน) ลดความเร็วตัด (vc) |
ผลสดุทายจากการสึกหรอด้านหน้าและ/หรือการสึกหรอเป็นหลุมด้านบนอย่างรุนแรง | เลือกเกรดที่มีความต้านทานการเสียรูปถาวรสูงขึ้น (ความแข็งขณะร้อน) ลดความเร็วตัด (vc) |
การกะเทาะที่บริเวณตัด
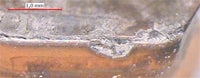
การกะเทาะทบรเวณตัดสามารถส่งผลให้
- เกิดการสึกหรอด้านหน้าอย่างรุนแรง
- ผิวงานมีคุณภาพต่ำ
สาเหตุ | วิธีแก้ไข |
สภาพการทำงานไม่มั่นคง | เพิ่มความมั่นคง (ระยะยืนของเครื่องมือ การจับยึดชิ้นงาน) |
พื้นผิวไม่สม่ำเสมอ | ลดอัตราป้อนงานขณะเจาะเข้า เลือกหน้าลายที่มีความเหนียวมากขึ้น |
เกรดมีความเหนียวไม่เพียงพอ | เลือกใช้เกรดที่มีความเหนียวมากขึ้น |
หน้าลายเม็ดมีดแข็งแรงไม่พอ | เลือกหน้าลายที่แข็งแรงมากขึ้น |
น้ำหล่อเย็นไม่เพียงพอ | เพิ่มปริมาณน้ำหล่อเย็น |
มีทรายปนในชิ้นงาน (เหล็กหล่อ) | เลือกหน้าลายที่แข็งแรงมากขึ้น ลดอัตราป้อนงานลง |
การหัก
การหักสามารถส่งผลให้
- เครื่องมือเสียหาย
- ชิ้นงานเสียหาย
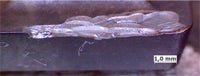
สาเหตุ | วิธีแก้ไข |
ความมั่นคงไม่ดีพอ | เพิ่มความมั่นคง (ลดระยะยืนของเครื่องมือ ปรับปรุงการจับยึดชิ้นงาน เป็นต้น) |
การตัดกระแทก | ลดอัตราป้อนงาน เลือกหน้าลายที่มีความเหนียวมากขึ้น (-GR หรือ -GT) |
น้ำหล่อเย็นไม่เพียงพอ | เพิ่มปริมาณน้ำหล่อเย็น |
อัตราป้อนงานสูงเกินไป หรือความเร็วตัดสูง/ต่ำเกินไป | ปรับค่าการตัด |
เกรดมีความเปราะเกินไป (เม็ดมีด P) | เลือกเกรดที่มีความเหนียวมากขึ้น |
เม็ดมีดเสื่อมสภาพ | ตรวจสอบอาุยการใช้งานที่ปลอดภัยของเม็ดมีดตัวนอก |
เศษวัสดุพอกติดที่คมตัด (BUE)
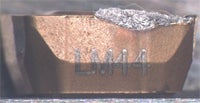
เศษวัสดุพอกติดที่คมตัดสามารถส่งผลให้
- ผิวงานมีคุณภาพต่ำและคมตัดค่อยๆ แตกเป็นชิ้นเล็กๆ เมื่อเศษที่พอกติดอยู่ถูกเศษจากการตัดกระแทกหลุดออก
- การกะเทาะของคมตัด
สาเหตุ | วิธีแก้ไข |
อุณหภูมิไม่เหมาะสม (ความเร็วต่ำ) | เพิ่ม/ลดความเร็วติด (อุณหภูมิสูง/ต่ำ) เลือกเกรดที่มีการเคลือบผิว |
รูปทรงคมตัดเป็นมุมลับมากเกินไป | เลือกคมตัดเป็นมุมบวกมากขึ้น |
วัสดุมีความเหนียว | เพิ่มส่วนผสมของน้ำมัน และเพิ่มปริมาณ/แรงดันของน้ำหล่อเย็น |
น้ำหล่อเย็นมีส่วนผสมของน้ำมันน้อยเกินไป | เพิ่มส่วนผสมของน้ำมัน และเพิ่มปริมาณ/แรงดันของน้ำหล่อเย็น |
ดอกสว่านแบบเปลี่ยนปลายได้
การสึกหรอโดยทั่วไปในวัสดุต่างๆ สำหรับหน้างาน -PM
เหล็กกล้าแบบไม่ใช่อัลลอย / CMC01.1
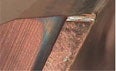
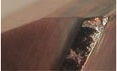
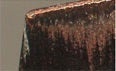
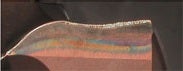
- การสึกหรอที่ปลายขอบ / ด้านนอกจะเริ่มต้นจากการสึกหรอเป็นรอยบาก จากนั้น จึงลามออกไปตามความกว้างของปลายขอบต่อไปยังร่องคายเศษ
- คมตัดหลักมีการสึกหรอเพิ่มขึ้นอย่างต่อเนื่อง
เหล็กกล้าอัลลอยต่ำ / CMC02.2
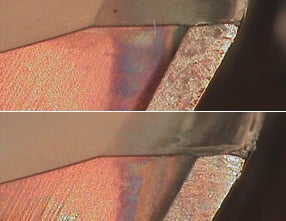
- คมตัดหลัก/ปลายขอบใกล้กับมุมมีการสึกหรอเพิ่มขึ้นอย่างต่อเนื่อง
การสึกหรอด้านหน้า
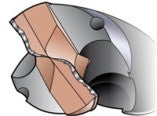
การสึกหรอด้านหน้าที่คมตัดหลัก
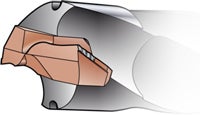
การสึกหรอด้านหน้าที่สันคมรอบนอก
การสึกหรอตามปกติและควรเกิดขึ้นเมื่อดอกสว่านมีความสมดุล
สาเหตุ | วิธีแก้ไข |
ความเร็วตัดสูงเกินไป | ลดความเร็วตัด |
สัดส่วนของน้ำมันในน้ำหล่อเย็นน้อยเกินไป | เพิ่มส่วนผสมของน้ำมันในน้ำหล่อเย็น (ควรตรวจสอบข้อมูลกับบริษัทผู้ผลิตน้ำมันก่อนทุกครั้ง เพื่อป้องกันไม่ให้มีการผสมน้ำมันในอัตราส่วนมากเกินไป) |
ปริมาณน้ำหล่อเย็นไม่เพียงพอ | เพิ่มปริมาณน้ำหล่อเย็น |
การเบี่ยงเบนหนีศูนย์รวมมากเกินไป (ถามการสึกหรอที่ปลายขอบดอกสว่าน) | ตรวจสอบการเบี่ยงเบนหนีศูนย์ในแนวรัศมี (ถามการสึกหรือที่ปลายขอบดอกสว่าน) |
เกิดการเสียรูปถาวร
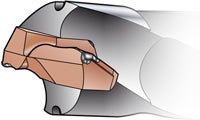
สาเหตุ | วิธีแก้ไข |
ความเร็วต่ำและ/หรืออัตราผ่อนงานสูงเกินไป | ลดความเร็วติดและ/หรืออัตราป้อนงาน |
ปริมาณน้ำหล่อเย็นไม่เพียงพอ | เพิ่มปริมาณน้ำหล่อเย็น |
การกะเทาะ
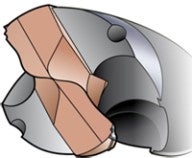
การกะเทาะที่ขอบนอก
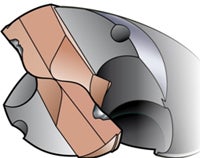
การกะเทาะที่คมตัดหลัก
การกะเทาะเป็นรูปแบบการสึกหรอที่พบได้บ่อยสำหรับการเจาะซ้ำเข้าในรูที่เจาะไว้เดิม ถ้ามียอดสว่านแคบกว่ารูที่เจาะไว้เดิม การทำงานจะมีความมั่นคงต่ำ และอาจเกิดความเสียหายที่บริเวณมุมได้ ปัญหานี้อาจเกิดขึ้นได้เช่นกันในกรณีที่พิกัดความเผื่อของมุมยอดสว่านไม่เท่ากัน การป้องกันปัญหานี้สามารถทำได้โดยการใช้ดอกสว่านแบบสั่งทำหรือโดยการทำรูกันเรียบด้วยวิธีการกด
สาเหตุ | วิธีแก้ไข |
สภาพการทำงานไม่มั่นคง | ตรวจเช็คการปรับตั้ง |
การเบี่ยงเบนหนีศูนย์มากเกินไป | ตรวจเช็คการเบี่ยงเบนหนีศูนย์ในแนวรัศมี |
อัตราป้อนงานสูงเกินไป | ลดอัตราป้อนงาน |
ปริมาณน้ำหล่อเย็นไม่เพียงพอ (การแตกร้าวเนื่องจากความร้อน) | ตรวจสอบการจ่ายน้ำหล่อเยน |
เศษวัสดพอกตัดที่คมตัด
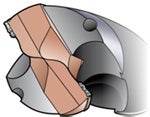
สาเหตุ | วิธีแก้ไข |
ความเร็วตัดไม่เหมาะสม | 1. เพิ่มความเร็วตัดในกรณีที่เศษวัสดุพอกติดที่คมตัดตรงกลาง 2. ลดความเร็วตัดในกรณีที่เศษวัสดุพอกติดที่คมตัดรอบนอก |
ส่วนผสมของน้ำมันในน้ำหล่อเย็นต่ำเกินไป | เพิ่มสัดส่วนของน้ำมันในน้ำหล่อเย็น (ควรตรวจสอบข้อมูลกับบริษัทผู้ผลิตน้ำมันก่อนทุกครั้ง เพื่อป้องกันไม่ให้มีการผสมน้ำมันในอัตราส่วนมากเกินไป) |
ถ้าไม่สามารถหลีกเลี่ยงบริเวณที่มีการพอกติดของเศษวัสดุได้ทั้งหมด ให้คำนวณค่าความเร็วตัดที่จะทำให้เศษวัสดุพอกติดที่บริเวณที่แข็งแรงที่สุดของดอกสว่าน (= 50% ของเส้นผ่านศูนย์กลาง)
การจ่ายน้ำหล่อเย็นภายนอกอาจส่งผลเสียต่อประสิทธิภาพการคายเศษ
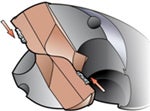
เพิ่มความเร็วตัดเพื่อให้เศษวัสดุ
พอกติดใกล้กับบริเวณกลางดอกสว่าน
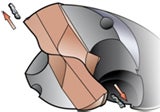
ลดความเร็วตัดเพื่อให้เศษวัสดุพอกติดที่
บริเวณขอบนอกหรือป้องกันการพอกติด
ดอกสว่านคาร์ไบด์
การสึกหรอด้านหน้า
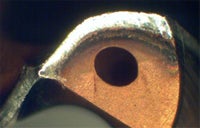
การสึกหรอด้านหน้าที่คมตัดหลัก
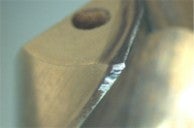
การสึกหรอด้านหน้าที่สันคมรอบนอก
การสึกหรอที่ควรเกิดขึ้นเมื่อลดอกสว่านมีความสมดุล
สาเหตุ | วิธีแก้ไข |
การเบี่ยงเบนหนีศูนย์มากเกินไป | ตรวจเช็คการเบี่ยงเบนหนีศูนย์ในแนวรัศมี |
ความเร็วตัดสูงเกินไป | ลดความเร็วตัดลง |
อัตราป้อนงานต่ำเกินไป | เพิ่มอัตราป้อนงาน |
เกรดอ่อนเกินไป | เลือกเกรดที่แข่งขัน |
น้ำหล่อเย็นไม่เพียงพอ | เพิ่มแรงดันน้ำหล่อเย็น |
การสึกหรอด้านหน้าที่คมจัก
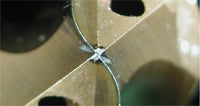
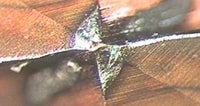
สาเหตุ | วิธีแก้ไข |
การเบี่ยงเบนหนีศูนย์มากเกินไป | ตรวจเช็คการเบี่ยงเบนหนีศูนย์ในแนวรัศมี |
ความเร็วตัดต่ำเกินไป | เพิ่มความเร็วตัด |
อัตราป้อนงานสูงเกินไป | ลดอัตราป้อนงานลง |
การสึกหรอด้านหน้าของมีดจะส่งผลต่อคุณภาพของรูด้วยเช่นกัน เนื่องจากจะทำให้ศูนย์เจาะไม่ตรง
การกะเทาะ
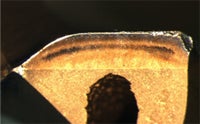
การกะเทาะที่ขอบนอก
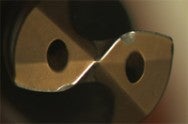
การกะเทาะที่คมตัดหลัก
การกะเทาะเป็นรูปแบบการสึกหรอที่พบได้บ่อยสำหรับการเจาะซ้ำเข้าในรูที่เจาะไว้เดิม ถ้ามียอดสว่านแคบกว่ารูที่เจาะไว้เดิม การทำงานจะมีความมั่นคงต่ำ และอาจเกิดความเสียหายที่บริเวณมุมได้ ปัญหานี้อาจเกิดขึ้นได้เช่นกันในกรณีที่พิกัดความเผื่อของมุมยอดสว่านไม่เท่ากัน การป้องกันปัญหานี้สามารถทำได้โดยการใช้ดอกสว่านแบบสั่งทำหรือโดยการทำรูกันเรียบด้วยวิธีการกัด
สาเหตุ | วิธีแก้ไข |
สภาพการทำงานไม่มั่นคง | ตรวจเช็คการปรับตั้ง |
การเบี่ยงเบนหนีศูนย์มากเกินไป | ตรวจเช็คการเบี่ยงเบนหนีศูนย์ในแนวรัศมี |
น้ำหล่อเย็นไม่เพียงพอ (การแตกราวเนื่องจากความร้อน) | ตรวจสอบการจ่ายน่ำหล่อเย็น |
มีการใช้งานดอกสว่านจนสึกหรอเกินกว่าระดับสูงสุดที่กำหนด | ปรับค่าการตัด |
ดอกสว่านหัก
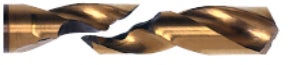
สาเหตุ | วิธีแก้ไข |
การเบี่ยงเบนหนีศูนย์มากเกินไป | ตรวจเช็คการเบี่ยงเบนหนีศูนย์ในแนวรัศมี |
สภาพการทำงานไม่มั่นคง | ตรวจเช็คการปรับตั้ง |
สปินเดลมีกำลงไม่พอ | ตรวจสอบค่าการตัด |
เศษตัด | ตรวจสอบการจ่ายน้ำหล่อเย็น |
อัตราป้อนงานสูงเกินไป | ลดอัตราป้อนงาน |
การสึกหรออย่างรุนแรง | ตรวจหาการสึกหรอให้บ่อยขึ้น |
เศษวัสดุพอกตัดที่คมตัด
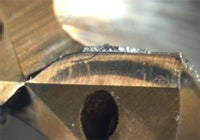
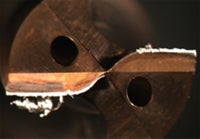
สาเหตุ | วิธีแก้ไข |
ความเร็วตัดและอุณหภูมิที่คมตัดต่ำเกินไป | 1. เพิ่มความเร็วตัดในกรณีที่เศษวัสดุพอกติดที่คมตัดตรงกลาง 2. ลดความเร็วตัดในกรณีที่เศษวัสดุพอกติดที่คมตัดรอบนอก |
สังคมเป็นมุมลบมากเกินไป | เลือกคมตัดที่มีความคมมากขึ้น |
ไม่มีการเคลือบผิว | เลือกคมตัดที่มีการเคลือบผิว |
ถ้าไม่สามารถหลีกเลี่ยงบริเวณที่มีการพอกติดของเศษวัสดุได้ทั้งหมด ให้คำนวณค่าความเร็วตัดที่จะทำให้เศษวัสดุพอกติดที่บริเวณที่แข็งแรงที่สุดของดอกสว่าน (= 50% ของเส้นผ่านศูนย์กลาง)
การจ่ายน้ำหล่อเย็นภายนอกอาจส่งผลเสียต่อประสิทธิภาพการคายเศษ
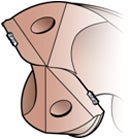
เพิ่มความเร็วตัดเพื่อให้
เศษวัสดุพอกติดใกล้กับบริเวณกลางดอกสว่าน
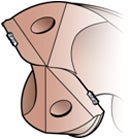
ลดความเร็วตัดเพื่อให้เศษวัสดุพอกติดที่
บริเวณขอบนอกหรือป้องกันการพอกติด
การสึกหรอตามปกติ
วัสดุทุกชนิด
- มีการสึกหรอด้านหน้าเสมอ
- มักจะไม่ค่อยพบการกะเทาะ กระบวนการทำงานเชื่อถือได้
เหล็กกล้าแบบไม่ใช่อลูมิเนียม / CMC01.1
- การสึกหรอที่ปลายขอบดอกสว่าน / ขอบนอก การสึกหรอจะเริ่มต้นจากการเป็นรอยบากลามต่อไปยังบริเวณมุม
เหล็กกล้าอลูมิเนียมต่ำ / CMC02.2
- การสึกหรอที่มุม
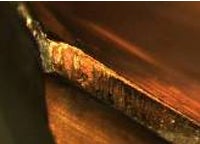
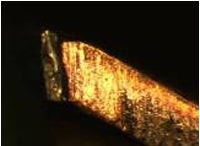
เหล็กกล้าอลูมิเนียมสูง / CMC03.11
- การสึกหรอด้านหน้าอย่างเห็นได้ชัด
- มีความเสียหายเล็กน้อยที่บริเวณมุม
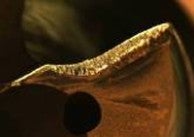
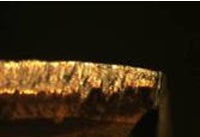
การออกแบบมุม
ข้อควรระวัง!
- ระวังเข้าใจผิดว่า ส่วนเสริมความแข็งแรงเป็นการสึกหรอ
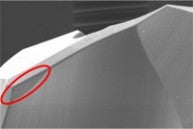
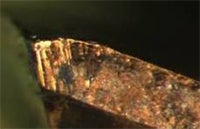