เพิ่มประสิทธิภาพการทำงานกับอะลูมิเนียม
~ เปลี่ยนมาใช้หัวกัดตัวเดียวแทนเครื่องมือหลายชิ้น เพื่อเพิ่มประสิทธิภาพให้กับการตัดเฉือนอะลูมิเนียม ~
อุตสาหกรรมยานยนต์กำลังเผชิญกับปัญหาที่กลืนไม่เข้าคายไม่ออกในเรื่องน้ำหนัก ตัวอย่างเช่น ในปี 2017 รถบรรทุกเบาที่ผลิตในสหรัฐอเมริกามีน้ำหนักเฉลี่ยอยู่ที่ 4,044 ปอนด์ (1.8 ตัน) ซึ่งอาจจะไม่ได้เบาสักเท่าไรนัก ชิ้นส่วนและเทคโนโลยีใหม่ๆ ส่งผลให้รถยนต์มีน้ำหนักเพิ่มขึ้น แต่ในขณะเดียวกัน กฎระเบียบด้านสิ่งแวดล้อมกลับกำหนดให้บริษัทผู้ผลิตต้องสร้างรถยนต์ที่มีน้ำหนักเบาลง อะลูมิเนียมเป็นวัสดุที่มีน้ำหนักเบาและสามารถแก้ปัญหาในเรื่องนี้ได้ แต่ส่งผลให้ขั้นตอนการกัดและการตัดเฉือนมีความท้าทายมากขึ้นด้วยเช่นกัน วันนี้ เอดูอาร์โด เดอโบเน ผู้จัดการฝ่ายธุรกิจอุตสาหกรรมยานยนต์ของบริษัทชั้นนำระดับโลกด้านงานตัดเฉือนโลหะอย่าง Sandvik Coromant จะมาเล่าให้เราฟังว่า ทำไมการใช้หัวกัดเพียงหัวเดียวจึงอาจเป็นทางออกสำหรับปัญหานี้
อะลูมิเนียมเป็นที่รู้จักกันดีในฐานะของวัสดุที่ทำให้มนุษยสามารถบินไปบนท้องฟ้าได้ การใช้อะลูมิเนียมในวงการการบินนั้นเริ่มต้นมาตั้งแต่ก่อนจะมีเครื่องบินลำแรกด้วยซ้ำ โดยในช่วงปลายทศวรรษ 1800 เคานต์ เฟอร์ดินานด์ เซปเปลิน ได้ใช้อะลูมิเนียมเป็นวัสดุในการสร้างโครงของเรือเหาะเซปเปลินอันโด่งดัง อะลูมิเนียมยังคงเป็นวัสดุที่ได้รับการยอมรับในเรื่องน้ำหนักที่เบามาจนถึงทุกวันนี้ ตัวอย่างเช่น การนำอะลูมิเนียมมาผลิตเป็นเสื้อสูบเครื่องยนต์ ซึ่งทำให้สามารถลดน้ำหนักและเพิ่มความประหยัดน้ำมันเชื้อเพลิงของรถยนต์ในปัจจุบันได้อย่างมาก
ถ้ามองไปที่อุตสาหกรรมยานยนต์ ระบบส่งกำลังของรถยนต์ส่วนบุคคลจากยุโรปมักจะประกอบด้วยอะลูมิเนียมประมาณ 80 กิโลกรัม ซึ่งแสดงให้เห็นว่า ชิ้นส่วนต่างๆ เช่น เครื่องยนต์และชุดเกียร์ กลายเป็นจุดที่น่าสนใจในการหาวิธีเพื่อลดน้ำหนักให้เบาลง อะลูมิเนียมยังคงเป็นโลหะที่ได้รับความนิยมมากขึ้นเรื่อยๆ ดังนั้น ผู้ผลิตเครื่องจักรและเครื่องมือจึงจำเป็นต้องคิดค้นระบบเครื่องมือที่สามารถช่วยให้ทำงานกับวัสดุชนิดนี้ได้ง่ายยิ่งขึ้น
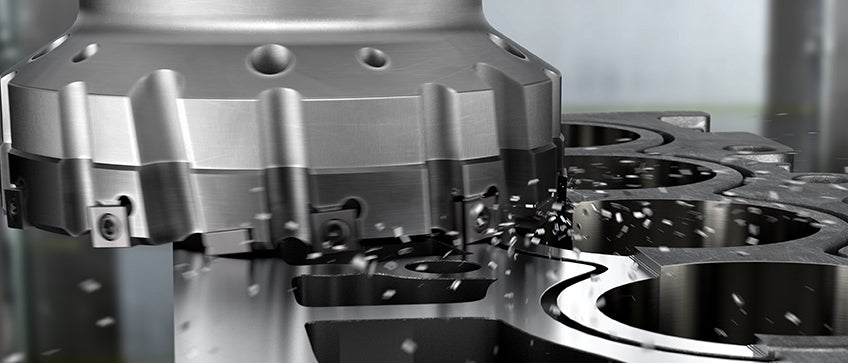
ชิ้นงานที่มีรูปทรงซับซ้อน
เสื้อสูบถือเป็นโครงสร้างหลักของเครื่องยนต์รถยนต์ โดยทำหน้าที่เป็นจุดยึดชิ้นส่วนเคลื่อนที่ต่างๆ ซึ่งทำงานร่วมกันเพื่อสร้างกำลังที่ใช้ในการขับเคลื่อนรถยนต์ ในอดีตนั้น เสื้อสูบมักจะผลิตจากเหล็กอัลลอยหล่อ แต่รถยนต์ส่วนบุคคลในปัจจุบันมักจะใช้เสื้อสูบที่ทำจากอะลูมิเนียมอัลลอยเป็นส่วนใหญ่เพื่อลดน้ำหนักให้เบาลง
การผลิตเสื้อสูบเป็นขั้นตอนที่จำเป็นต้องใช้จำนวนเครื่องจักรมากที่สุดเมื่อเทียบกับการผลิตชิ้นส่วนยานยนต์อื่นๆ และกระบวนการผลิตมักจะมีความซับซ้อน รวมทั้งจำเป็นต้องมีพิกัดความเผื่อต่ำมาก งานตัดเฉือนหยาบและเก็บผิวละเอียดเพื่อผลิตชิ้นส่วนยานยนต์ที่มีความสำคัญและซับซ้อน เช่น เสื้อสูบ เป็นงานที่ต้องใช้เวลานานและมีค่าใช้จ่ายสูง รวมทั้งยังจำเป็นต้องใช้เครื่องมือหลายประเภท ส่งผลให้ต้องใช้เวลาในการปรับตั้งมากขึ้นและใช้น้ำหล่อเย็นมากขึ้นเพื่อลดความร้อนเนื่องจากการเสียดทานที่สูงขึ้น
ฝาสูบเครื่องยนต์ถือเป็นอีกชิ้นส่วนหนึ่งที่มีความสำคัญไม่แพ้กันและมักจะผลิตจากอะลูมิเนียมเช่นกัน ฝาสูบเป็นชิ้นส่วนที่ติดตั้งอยู่เหนือเสื้อสูบ โดยทำหน้าที่ส่งอากาศและน้ำมันเชื้อเพลิงไปยังห้องเผาไหม้ ทั้งยังทำหน้าที่เป็นจุดยึดชิ้นส่วนต่างๆ เช่น วาล์ว หัวเทียน และหัวฉีดน้ำมันเชื้อเพลิง ดังนั้น การผลิตฝาสูบจึงจำเป็นต้องใช้ขั้นตอนการตัดเฉือนที่ละเอียดและมีคุณภาพสูงเช่นเดียวกันกับเสื้อสูบ
อะลูมิเนียมอาจจะมีน้ำหนักเบากว่าเหล็กหล่อ แต่ในขณะเดียวกันก็เป็นวัสดุที่อ่อนกว่าเหล็กหล่อมาก ดังนั้น ปัญหาที่พบได้ทั่วไปในการทำงานกับอะลูมิเนียมคือ ผิวงานคุณภาพต่ำ การเกิดครีบ และการสึกหรอไม่สม่ำเสมอของเครื่องมือ ถ้าเป็นเช่นนั้นแล้ว บริษัทผู้ผลิตรถยนต์มีวิธีใดบ้างที่จะเอาชนะความท้าทายเหล่านี้ เพื่อให้ผลิตได้เร็วขึ้น ผิวชิ้นงานมีคุณภาพดีขึ้น และประหยัดต้นทุนได้มากขึ้น
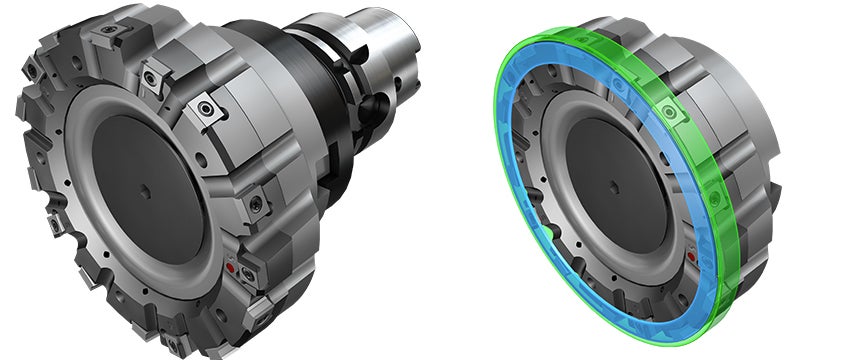
ตอบทุกความท้าทายในหนึ่งเดียว
ในฐานะผู้เชี่ยวชาญด้านงานตัดเฉือนโลหะ Sandvik Coromant เชื่อว่า การสร้างนวัตกรรมจะต้องเกิดจากแนวทางที่ง่ายที่สุด ดังนั้น การกัดปาดหน้าด้วยเครื่องมือเพียงชิ้นเดียวแทนการใช้เครื่องมือหลายชิ้น จึงสามารถแก้ปัญหาความท้าทายต่างๆ ของการทำงานกับอะลูมิเนียมได้ หัวกัดหัวเดียวที่ทำงานได้ครบทุกอย่างสามารถทำได้ทั้งการกัดหยาบและการเก็บผิวละเอียด จึงช่วยลดแรงเครียดในอะลูมิเนียม ทำให้ได้ชิ้นงานที่มีคุณภาพสูงขึ้น
ระบบเครื่องมือจาก Sandvik Coromant สำหรับงานตัดเฉือนอะลูมิเนียมประกอบด้วยหัวกัดรูปแบบต่างๆ ที่ออกแบบมาเป็นพิเศษและได้รับสิทธิบัตรแล้ว โดยสามารถกัดอะลูมิเนียมได้แบบไร้ปัญหา แม่นยำ และไม่เกิดคราบ โดยหนึ่งในผลิตภัณฑ์ของเรา ได้แก่ หัวกัดอะลูมิเนียม M5C90 ในตระกูล M5 ซึ่งออกแบบมาสำหรับการกัดปาดหน้าหยาบและการเก็บผิวละเอียดเพื่อผลิตฝาสูบ เสื้อสูบ และชิ้นส่วนอะลูมิเนียมล้วนที่ต้องใช้หน้าสัมผัสมิดชิด ยกเว้นชิ้นส่วนที่มีผนังบาง เครื่องมือรุ่นนี้สามารถทำงานทุกขั้นตอน ตั้งแต่การกัดหยาบไปจนถึงการเก็บผิวละเอียด ได้ในครั้งเดียว
เครื่องมือรุ่นนี้สามารถทำการกัดหยาบและเก็บผิวละเอียดได้ในการทำงานรอบเดียว และโดยส่วนใหญ่แล้ว สามารถใช้ระยะกินลึกแนวแกนได้สูงสุดถึงหกมิลลิเมตร ผลการทดสอบแสดงให้เห็นว่า อายุการใช้งานของเครื่องมือเพิ่มขึ้นถึงห้าเท่า พร้อมทั้งสามารถลดรอบระยะเวลาที่ใช้ในการผลิตลงได้ถึง 200 เปอร์เซ็นต์
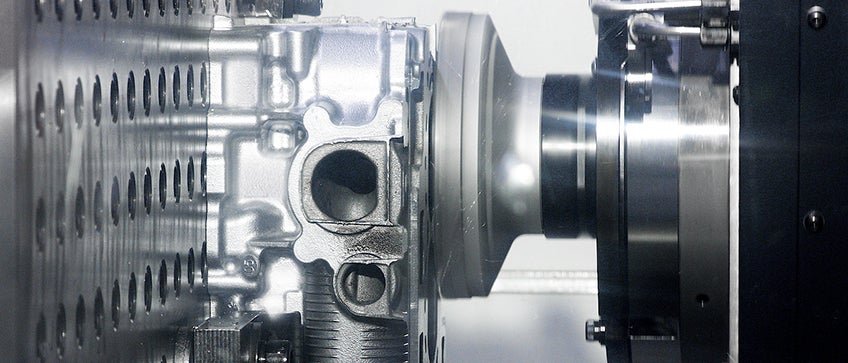
จุดเด่นหลักของหัวกัดตระกูล M5 คือเทคโนโลยีการกัดหลายขั้น โดยหัวกัดตระกูลนี้จะมีการจัดวางตำแหน่งคมตัดเพชรโพลีคริสตัลลีน (PCD) ซึ่งให้อายุการใช้งานยาวนานและความเที่ยงตรงสูง ในรูปแบบวงกลม โดยจะค่อยๆ ตัดเฉือนเนื้อวัสดุออกจากชิ้นงานเป็นขั้นๆ มากขึ้นเรื่อยๆ ทั้งในแนวแกนและแนวรัศมี นอกจากนี้ ฟันตัดสุดท้ายของเครื่องมือยังเป็นแบบไวเปอร์ ซึ่งให้คุณภาพและความเรียบของผิวงานที่เหนือกว่า โดยจะเห็นได้ว่าฟันตัดทั้งแบบธรรมดาและแบบไวเปอร์นั้นจะมีตำแหน่งที่ตายตัว จึงทำให้ไม่จำเป็นต้องทำขั้นตอนการปรับตั้งที่ยุ่งยากและเสียเวลา การผลิตชิ้นส่วนอะลูมิเนียมทั่วไปในอุตสาหกรรมยานยนต์มีข้อเสียคือ จำเป็นต้องใช้เครื่องมือหลายชิ้นเพื่อให้ออกมาเป็นชิ้นงานสุดท้าย แต่การเปลี่ยนมาใช้เครื่องมือชิ้นเดียวที่ทำงานได้ครบทุกแบบนี้ สามารถลดแรงเครียดที่เกิดกับผิวหน้าอะลูมิเนียมในระหว่างการตัดเฉือนได้อย่างมาก
อุตสาหกรรมยานยนต์ยังคงเดินหน้าอย่างต่อเนื่องในการค้นหาวิธีการใหม่ๆ ที่จะช่วยให้รถยนต์มีสมรรถนะเพิ่มขึ้นและเป็นมิตรต่อสิ่งแวดล้อมมากขึ้น และการเลือกวัสดุที่เหมาะสมถือเป็นอีกหนึ่งปัจจัยสำคัญที่จะทำให้รถยนต์มีน้ำหนักเบาลง ในขณะเดียวกัน ขั้นตอนการตัดเฉือนที่ง่ายยิ่งขึ้นจากการใช้เครื่องมือ เช่น หัวกัดอะลูมิเนียม M5C90 ก็เป็นอีกหนึ่งทางเลือกสำหรับผู้ผลิตในการตอบโจทย์ความต้องการและเอาชนะความท้าทายของงานตัดเฉือนอะลูมิเนียม ในอนาคตต่อจากนี้ ไม่แน่ว่าอะลูมิเนียมอาจจะกลายเป็นคำตอบสุดท้ายในการแก้ปัญหาเรื่องน้ำหนักของอุตสาหกรรมยานยนต์ก็เป็นได้