Jak osiągnąć dobrą jakość przedmiotu w procesie toczenia
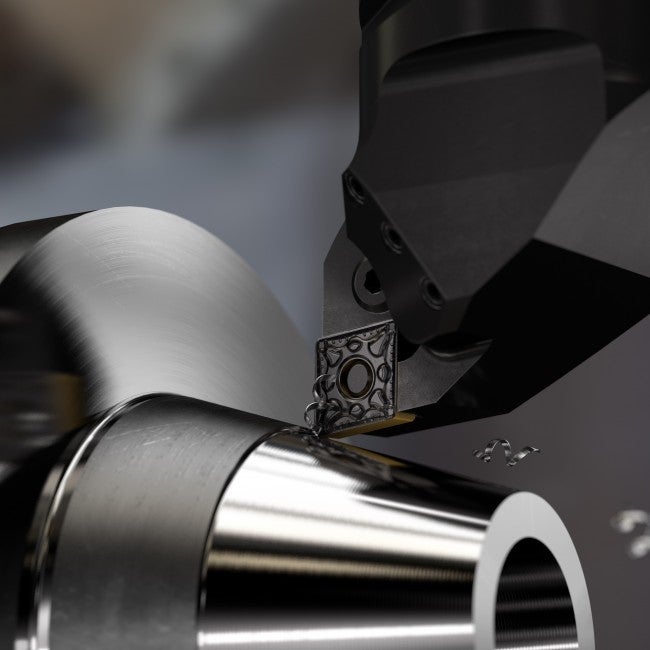
Kontrola spływu wiórów jest jednym z najważniejszych czynników, które należy uwzględnić, chcąc osiągnąć dobrą jakość toczonych przedmiotów. Wybierz prawidłowe parametry skrawania i postępuj zgodnie z naszymi wskazówkami odnośnie zastosowania, aby otrzymać wysokiej jakości przedmioty obrobione.
Skuteczna kontrola spływu wiórów
Zagadnienie kontroli spływu wiórów jest jedną z podstawowych kwestii w obróbce tokarskiej; istnieją trzy podstawowe sposoby łamania wiórów:
- Łamanie samoczynne (np. w przypadku żeliwa szarego)
- Łamanie o narzędzie
- Łamanie o przedmiot obrabiany
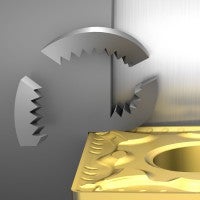
Łamanie samoczynne
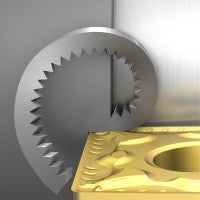
Łamanie o narzędzie
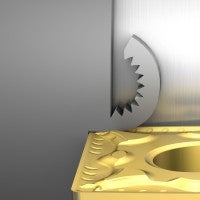
Łamanie o przedmiot obrabiany
Czynniki wpływające na łamanie wiórów
- Geometria płytki: W zależności od szerokości rowka wiórowego oraz kształtu mikro- i makrogeometrii będą powstawać wióry bardziej otwarte lub zwinięte
- Promień naroża: Mniejsza długość promienia zaokrąglenia naroża umożliwia lepszą kontrolę spływu wiórów
- Kąt przystawienia KAPR (lub PSIR): Od wielkości kąta przystawienia zależy kierunek spływu wiórów; w stronę powierzchni obrabianej lub w kierunku przeciwnym
- Głębokość skrawania: Zależy od materiału obrabianego; większa głębokość skrawania wiąże się z większą siłą potrzebną do łamania i odprowadzania wiórów
- Posuw na obrót: Zasadniczo przy większej wartości posuwu formowane są mocniejsze wióry. W niektórych przypadkach może to być korzystne dla przebiegu łamania i kontroli spływu wiórów
- Prędkość skrawania: Zmiana prędkości skrawania może wpływać na skuteczność łamania wiórów
- Materiał: Zasadniczo materiał obrabiany generujący krótki wiór (np. żeliwo) jest łatwy w obróbce. W przypadku materiałów charakteryzujących się bardzo dużą wytrzymałością mechaniczną i odpornością na pełzanie
(tendencją do powolnej zmiany kształtu lub odkształcania ciała stałego na skutek naprężeń, na przykład Inconel), łamanie wiórów stanowi większy problem
Parametry skrawania dla toczenia
Wybierając prawidłowe prędkości i posuwy dla toczenia, należy zawsze uwzględnić typ obrabiarki, narzędzia, płytki i materiału.
- Rozpocząć obróbkę z niskim posuwem, mając na uwadze bezpieczeństwo płytki i chropowatość powierzchni, a następnie zwiększyć posuw w celu sprawniejszego odprowadzania wiórów
- Stosować głębokość skrawania większą od promienia naroża, aby ograniczyć ugięcie płytki w kierunku promieniowym, co ma istotne znaczenie w obróbce wewnętrznej
- Użycie zbyt niskiej prędkości skrawania prowadzi do zbyt małej trwałości. Należy zawsze stosować zalecaną prędkość skrawania, vc m/min (ft/min)
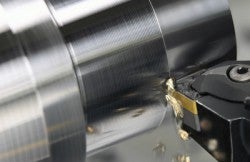
Poprawa jakości toczonego przedmiotu dzięki zastosowaniu chłodziwa
Prawidłowo doprowadzane chłodziwo zwiększa bezpieczeństwo procesu oraz poprawia efektywność pracy narzędzia i jakość wykonania przedmiotu. Używając chłodziwa, należy uwzględnić następujące zalecenia:
- Najbardziej zaleca się używanie narzędzi z precyzyjnym doprowadzaniem chłodziwa do obróbki wykończeniowej
- Wartość ciśnienia chłodziwa potrzebna do odłamania wióra zależy od średnicy dyszy (wylot), materiału poddawanego obróbce, głębokości skrawania i posuwu
- Wymagane natężenie przepływu chłodziwa zależy od ciśnienia i całkowitej powierzchni przekroju otworów doprowadzających chłodziwo
- W obróbce średniej i zgrubnej zaleca się podawanie chłodziwa na powierzchnię przyłożenia (od dołu)
- Do obróbki wykończeniowej zalecane jest podawanie chłodziwa z wysoką precyzją na powierzchnię natarcia (od góry) oraz na powierzchnię przyłożenia (od dołu)
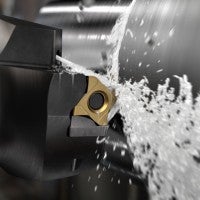
Jak poradzić sobie z trudnościami dzięki prawidłowemu użyciu chłodziwa?
- Problemy z kontrolą spływu wiórów: stosować chłodziwo podawane na powierzchnię natarcia (od góry)
- Problemy z uzyskaniem prawidłowych wymiarów: Zwykle są spowodowane wysoką temperaturą: stosować chłodziwo podawane na powierzchnię natarcia (od góry) i na powierzchnię przyłożenia (od dołu) pod możliwie największym ciśnieniem
- Niska jakość wykończenia powierzchni: Stosować chłodziwo podawane na powierzchnię natarcia (od góry), jeśli przyczyną uszkodzeń są wióry
- Nieprzewidywalna trwałość ostrzy podczas obróbki zgrubnej: stosować chłodziwo podawane na powierzchnię przyłożenia (od dołu)
- Nieprzewidywalna trwałość ostrzy podczas obróbki wykończeniowej: Stosować chłodziwo doprowadzane na powierzchnię natarcia (od góry) i na powierzchnię przyłożenia (od dołu)
- Mało efektywne odprowadzanie wiórów podczas obróbki wewnętrznej: Stosować chłodziwo podawane na powierzchnię natarcia (od góry) i na powierzchnię przyłożenia (od dołu) pod możliwie najwyższym ciśnieniem
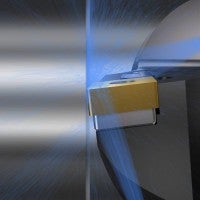
Jak stosować chłodziwo i ciecz obróbkową podczas toczenia
Jak osiągnąć dobrą jakość powierzchni toczonych przedmiotów
Ogólne zasady dotyczące chropowatości powierzchni:
- Chropowatość powierzchni można często poprawić, zwiększając prędkość skrawania
- Geometria płytki (neutralny, dodatni i ujemny kąt natarcia oraz dodatni kąt przyłożenia) ma wpływ na chropowatość powierzchni
- Wybrany gatunek płytki wpływa na chropowatość powierzchni w pewnym tylko stopniu
- W razie wystąpienia drgań należy zastosować płytkę z mniejszym promieniem naroża
Płytka wiper
Płytki wiper umożliwiają obróbkę przedmiotów z wysokimi posuwami, a zarazem zapewniają uzyskiwanie gładkiej powierzchni i korzystny przebieg łamania wiórów.
Ogólne wytyczne są następujące: Dwukrotnie wyższy posuw - ta sama chropowatość powierzchni, co dla płytki ze zwykłym zaokrąglonym narożem. Ten sam posuw - dwukrotnie lepsza chropowatość powierzchni.
Płytki wiper pracując wzdłuż przedmiotu obrabianego, wygładzają jego powierzchnię; efekt dogładzenia jest wykorzystywany przede wszystkim w toczeniu wzdłużnym i planowaniu.
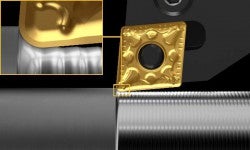
Naroże standardowe
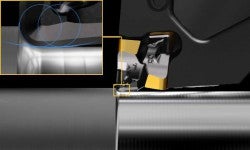
Naroże Wiper
Jak wybrać geometrię płytki wiper
Porównanie wartości posuwu dla płytki standardowej i płytki wiper
Uwaga! Wszystkie parametry dotyczące płytek z narożem standardowym zostały uzyskane na podstawie obliczeń teoretycznych. Parametry dla płytek dogładzających opierają się na wartościach eksperymentalnych, uzyskanych podczas obróbki stali niskostopowej.
Posuw mm (in) | Standardowy promień naroża (RE) 0.4 mm (0.016 in) Ra µm (µin) | Płytka wiper (-WF/-WM) RE 0.4 mm (0.016 in) Ra µm (µin) | Standardowy promień naroża RE 0.8 mm (0.031 in) Ra µm (µin) | Płytka wiper (-WMX) RE 0.8 mm (0.031 in) Ra µm (µin) |
0.07 (0.003) | 0.31 (12.4) | 0.30 (12.0) | - | - |
0.10 (0.004) | 0.63 (25.2) | 0.32 (12.8) | 0.31 (12.4) | - |
0.12 (0.005) | 0.90 (36.0) | 0.45 (18.0) | 0.45 (18.0) | - |
0.15 (0.006) | 1.41 (56.4) | 0.70 (28.0) | 0.70 (28.0) | 0.25 (10.0) |
0.18 (0.007) | 2.03 (80.8) | 1.00 (40.0) | 1.00 (40.4) | 0.30 (12.0) |
0.20 (0.008) | 2.50 (100.0) | 1.25 (50.0) | 1.25 (50.0) | 0.35 (14.0) |
0.22 (0.009) | 3.48 (139.2) | 1.74 (69.6) | 1.74 (69.6) | 0.40 (16.0) |
0.25 (0.010) | - | - | 2.25 (90.0) | 0.45 (18.0) |
0.28 (0.011) | - | - | 2.82 (112.8) | 0.50 (20.0) |
0.30 (0.012) | - | - | 3.23 (129.2) | 0.55 (22.0) |
0.35 (0.014) | - | - | 4.40 (176.0) | 0.60 (24.0) |
0.40 (0.016) | - | - | 5.75 (230.0) | 0.70 (28.0) |
0.45 (0.018) | - | - | 8.54 (341.6) | 1.1 (44.0) |
0.50 (0.020) | - | - | 10.55 (422.0) | 1.3 (51.0) |
Posuw mm (in) | Standardowy promień naroża RE 1.2 mm (0.047 in) Ra µm (µin) | Płytka wiper (-WMX) RE 1.2 mm (0.047 in) Ra µm (µin) | Standardowy promień naroża RE 1.6 mm (0.063 in) Ra µm (µin) | Płytka wiper (-WMX) RE 1.6 mm 1) (0.063 in) Ra µm (µin) |
0.15 (0.006) | 0.47 (18.8) | - | - | - |
0.18 (0.007) | 0.68 (27.2) | - | - | - |
0.20 (0.008) | 0.83 (33.3) | 0.3 (12.0) | 0.63 (25.2) | - |
0.22 (0.009) | 1.16 (46.4) | 0.3 (12.0) | 0.87 (34.8) | - |
0.25 (0.010) | 1.50 (60.0) | 0.4 (16.0) | 1.12 (44.8) | 0.3 (12.0) |
0.28 (0.011) | 1.88 (75.2) | 0.4 (16.0) | 1.41 (56.4) | 0.35 (14.0) |
0.30 (0.012) | 2.16 (86.4) | 0.4 (16.0) | 1.62 (64.8) | 0.4 (16.0) |
0.35 (0.014) | 2.93 (117.2) | 0.5 (20.0) | 2.20 (88.0) | 0.4 (16.0) |
0.40 (0.016) | 3.83 (153.2) | 0.65 (26.0) | 2.88 (115.2) | 0.4 (16.0) |
0.45 (0.018) | 5.70 (228.0) | 0.85 (34.0) | 4.27 (170.8) | 0.5 (20.0) |
0.50 (0.020) | 7.03 (281.2) | 1.15 (46.0) | 5.27 (210.8) | 0.7 (28.0) |
0.55 (0.022) | 8.51 (340.4) | 1.2 (48.0) | 6.38 (255.2) | 0.9 (36.0) |
0.60 (0.024) | 10.13 (405.2) | 1.3 (52.0) | 7.59 (303.6) | 1.05 (42.0) |
0.65 (0.026) | - | - | 8.91 (356.4) | 1.25 (50.0) |
0.70 (0.028) | - | - | 10.31 (413.6) | 1.3 (52.0) |
0.85 (0.033) | - | - | 15.24 (609.6) | 1.9 (76.0) |
0.90 (0.035) | - | - | 17.09 (683.0) | 2.1 (84.0) |
- Wartości dla naroża 1.6 mm (0.06 in) dotyczą płytki DNMX
Wskazówki dotyczące toczenia zewnętrznego
Przedmioty obrabiane podatne na drgania
Obróbka w jednym przejściu (np. obróbka rury)
Zaleca się wykonywać całą obróbkę w jednym przejściu, aby ukierunkować całkowitą siłę skrawania bardziej osiowo w stronę uchwytu/wrzeciona.
Przykład:
Średnica zewnętrzna (OD) 25 mm (0.984 in)
Średnica wewnętrzna (ID) 15 mm (0.590 in)
Głębokość skrawania, ap = 4.3 mm (0.169 in)
Uzyskana grubość ścianki = 0.7 mm (0.028 in)
OD = 25 mm (0.984 in) | ap 4.3 mm (0.169 in) |
![]() | ID = 15 mm (0.590 in) |
Można zastosować kąt przystawienia wg ISO bliski 90° (kąt przystawienia wg ANSI 0°), aby ukierunkować siły skrawania osiowo w stronę uchwytu. W ten sposób można ograniczyć siłę gnącą działającą na przedmiot.
Obróbka w dwóch przejściach
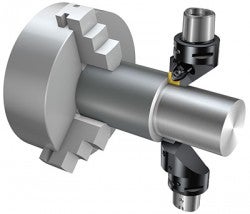
Obróbka synchroniczna na górnej i dolnej głowicy rewolwerowej pozwala wyważyć promieniową składową siły skrawania oraz uniknąć drgań i ugięcia przedmiotu.
Przedmioty smukłe/o cienkich ściankach
Podczas toczenia przedmiotów smukłych/o cienkich ściankach należy pamiętać o następujących zaleceniach:
- Stosować kąt przystawienia bliski 90° (PSIR 0°). Nawet niewielka zmiana kąta (z 91/-1 na 95/-5 stopni) wpływa na kierunek całkowitej siły skrawania podczas obróbki.
- Głębokość skrawania,ap, powinna być większa niż promień naroża (RE) płytki skrawającej. Przy dużej wartości ap wartość osiowej składowej siły skrawania Fz przeważa nad wartością składowej promieniowej Fx, co prowadzi do wzbudzenia drgań
- Stosować płytki o ostrej krawędzi i małym promieniu naroża RE, co pozwoli ograniczyć wartość siły skrawania
- Należy rozważyć zastosowanie gatunku z cermetalu lub pokrywanego metodą PVD, aby zapewnić odporność na zużycie i ostrą krawędź, wskazaną w tego typu zastosowaniach
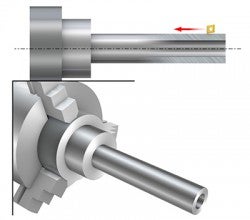
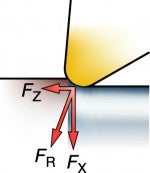
Toczenie kołnierzy/występów
Należy postępować zgodnie z zaleceniami 1-5, aby uniknąć uszkodzenia krawędzi płytki. Metoda ta jest bardzo korzystna przy obróbce za pomocą płytek z pokryciem nakładanym metodą CVD i może w znacznym stopniu ograniczyć powstawanie pęknięć.
Przejście 1-4:
Należy utrzymywać odległość między przejściami (1-4) równą posuwowi, aby uniknąć zakleszczania się wiórów.
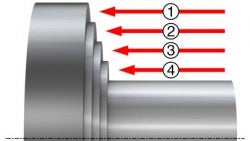
Przejście 5:
Ostatnie przejście należy wykonać w kierunku promieniowym, od średnicy zewnętrznej ku osi obrotu.
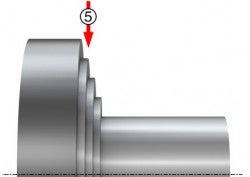
Podczas planowania czoła, w przejściu po powierzchni zaokrąglenia w kierunku od osi na zewnątrz, może pojawić się problem z zawijaniem się wiórów na promieniu naroża. Rozwiązaniem problemu może być zmiana kierunku przejścia, gdyż kierunek spływu wiórów ulegnie odwróceniu.
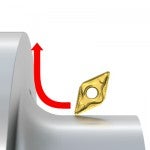
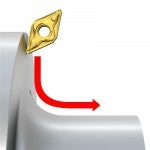
Toczenie powierzchni czołowej (planowanie)
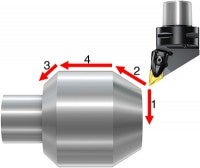
Rozpocząć obróbkę od planowania (1) i fazowania (2). W miarę możliwości, o ile pozwala na to geometria przedmiotu obrabianego, wykonać fazowanie (3). Ostatni etap obróbki to przejście wzdłużne (4), podczas którego płytka stopniowo zagłębia się w materiał i z niego wychodzi.
Pierwszym etapem obróbki powinno być planowanie, które pozwoli ustalić punkt odniesienia na powierzchni przedmiotu dla kolejnego przejścia.
Częstym problemem są zadziory na końcu przejścia (formujące się przy wychodzeniu narzędzia z materiału). Pozostawienie fazki lub zaokrąglenia (w narożniku) może ograniczyć lub wyeliminować problem powstających zadziorów.
Fazka na przedmiocie pozwala płynniej zagłębić ostrze w materiał (podczas planowania i toczenia wzdłużnego).
Skrawanie przerywane

Wskazówki dotyczące skrawania przerywanego:
- Zastosować gatunki z pokryciem PVD, aby zapewnić udarność płytki podczas częstych uderzeń, np. w przypadku toczenia prętów o przekroju sześciokątnym
- Zastosować udarne gatunki z pokryciem CVD, aby zapewnić ogólną udarność przy obróbce dużych przedmiotów i ciężkiej obróbce przerywanej
- Rozważyć zastosowanie mocniejszego łamacza wiórów, aby odpowiednio zwiększyć odporność na wykruszenia
- Korzystne może okazać się odłączenie chłodziwa w celu uniknięcia pęknięć cieplnych
Obróbka wykończeniowa przedmiotu ze szlifowanym podcięciem
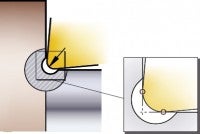
Do toczenia wzdłużnego i toczenia powierzchni czołowych (planowania) użyć płytki o jak największym promieniu naroża, RE, który zapewnia:
- Mocną krawędź i większą niezawodność obróbki
- Mała chropowatość powierzchni
- Możliwość obróbki z wysokimi posuwami
Nie przekraczać szerokości podcięcia, wykonać podcięcie jako ostatnią czynność w celu usunięcia zadziorów.
Wskazówki dotyczące toczenia wewnętrznego
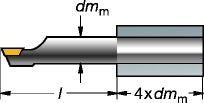
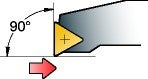
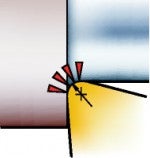
- Wybrać narzędzie z trzonkiem o jak największym przekroju poprzecznym i jednocześnie upewnić się, że między trzonkiem a ściankami otworu pozostaje wystarczająca ilość miejsca na odprowadzane wióry
- Upewnić się, że odprowadzanie wiórów przebiega odpowiednio do zastosowanych parametrów skrawania oraz że wióry mają właściwy kształt.
- Użyć jak najkrótszego wysięgu i upewnić się, że długość wytaczaka pozwala na zastosowanie mocowania o zalecanej długości. Długość mocowania nie powinna być krótsza niż trzykrotność średnicy trzonka
- Do produkcji detali wrażliwych na drgania należy używać wytaczaków z tłumieniem drgań
- Wybierz kąt przystawienia jak najbliższy 90° (PSIR 0°), aby skierować wypadkową sił skrawania wzdłuż osi wytaczaka. Kąt przystawienia nie powinien być mniejszy niż 75° (PSIR -15°)
- Priorytetowym zaleceniem jest, by płytki wymienne miały dodatni kształt podstawowy i dodatnią geometrię, pozwalające ograniczyć ugięcie narzędzia
- Wybrać płytkę o promieniu naroża mniejszym od głębokości skrawania
- Zbyt małe zagłębienie ostrza skrawającego może spowodować zwiększenie drgań powodowanych tarciem podczas skrawania. Zastosować zagłębienie ostrza większe od promienia naroża, aby zapewnić korzystny przebieg skrawania
- Zbyt duże zagłębienie ostrza (duża głębokość skrawania i/lub posuw) może powodować zwiększenie drgań na skutek ugięcia.
- Płytki niepokrywane lub z cienkim pokryciem generują zwykle mniejsze siły skrawania niż płytki z grubym pokryciem. Ma to szczególne znaczenie w przypadku dużej różnicy długości narzędzia i jego średnicy. Ostra krawędź sprzyja zazwyczaj poprawie jakości wykonania otworu przez ograniczenie tendencji do drgań
- Geometria z otwartym łamaczem wiórów często jest korzystnym wyborem przy toczeniu wewnętrznym
- W niektórych rodzajach obróbki, jeśli ryzyko zakleszczania się wiórów lub powstawania drgań jest duże, można rozważyć zastosowanie płytek w gatunku o dużej udarności.
- Jeśli konieczna jest poprawa przebiegu formowania wiórów, zastanowić się nad zmianą drogi narzędzia.
Wskazówki dotyczące toczenia na twardo
Oprócz ogólnych zaleceń dotyczących toczenia, w przypadku toczenia na twardo należy rozważyć pewne kluczowe czynniki (jeśli proces produkcji obejmuje przygotowanie przedmiotu we własnym zakresie przed utwardzeniem):
- Unikać zadziorów
- Zachowywać ścisłe klasy dokładności wymiarowej
- Wykonywać fazowania i obróbkę narożników przedmiotu obrabianego przed utwardzeniem
- Unikać gwałtownego wchodzenia/wychodzenia z materiału
- Wprowadzać/wyprowadzać narzędzie z materiału po drodze w kształcie łuku
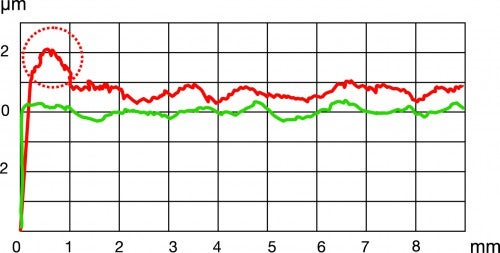
Wymiary powierzchni
Oś X: Długość toczonego elementu
Oś Y: Odchyłka wymiaru średnicy
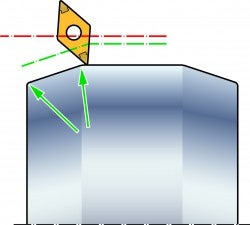
Powierzchnia krytyczna
Ustawienie i mocowanie
- Podstawowe znaczenie ma dobra stabilność przedmiotu w obrabiarce, jego zamocowanie i pozycja
- Wskazane jest, by dopuszczalny współczynnik długości przedmiotu do jego średnicy wynosił 2:1 w przypadku przedmiotów podpartych tylko z jednego końca. Jeśli do podparcia jest używany konik, współczynnik można zwiększyć
- Należy pamiętać, że dodatkową poprawę stabilności wymiarowej zapewni wrzeciennik i konik zachowujące symetrię przy wzroście temperatury
- Korzystać z systemu Coromant Capto®
- Stosować jak najkrótsze wysięgi dla zapewnienia maksymalnej sztywności układu
- Do toczenia wewnętrznego rozważyć użycie trzonka wytaczaka z węglika spiekanego i z tłumikiem drgań Silent Tools
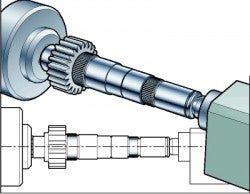
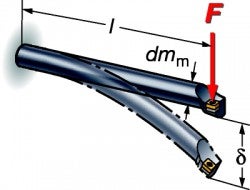
Mikrogeometria płytki
Dwa typowe rodzaje krawędzi dla płytek CBN mają kształt typu S oraz typu T.
- Typu S: ostrze o najlepszej wytrzymałości. Jest odporne na powstawanie mikrowykruszeń i zapewnia równomierną gładkość powierzchni.
- Typu T: zapewnia najlepszą gładkość powierzchni podczas skrawania ciągłego, ogranicza powstawanie zadziorów podczas skrawania przerywanego. Generuje niższe opory skrawania.
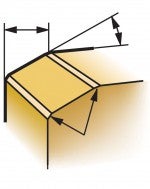
Krawędź typu S
Ścin z niewielkim honowaniem
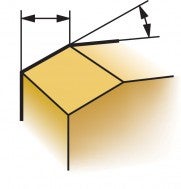
Krawędź typu T
Ścin bez honowania
Geometria naroża płytki
- W stabilnych warunkach należy zawsze stosować geometrię wiper, zapewniającą najlepszą gładkość powierzchni.
- Jeśli wymogi odnośnie produktywności są duże, należy stosować płytkę z małym kątem przystawienia do przedmiotu obrabianego.
- Płytki ze zwykłym narożem należy wybierać tylko w przypadku niskiej stabilności układu (np. do obróbki smukłego przedmiotu, itp.).
Obróbka na sucho lub z chłodziwem
Toczenie na twardo bez chłodziwa to rozwiązanie idealne i w pełni wykonalne. Zarówno płytki z CBN, jak i narzędzia ceramiczne tolerują wysokie temperatury skrawania, co pozwala wyeliminować koszty i problemy związane z użyciem chłodziwa.
W niektórych zastosowaniach chłodziwo może być konieczne, np. do kontrolowania stabilności termicznej obrabianego przedmiotu. W takich przypadkach należy zadbać o ciągły dopływ chłodziwa przez cały czas toczenia.
Zasadniczo, ciepło wydzielające się podczas obróbki rozchodzi się na wiór (80%), przedmiot obrabiany (10%) i płytkę (10%), co pozwala zrozumieć, dlaczego odprowadzanie wiórów ze strefy skrawania ma istotne znaczenie.
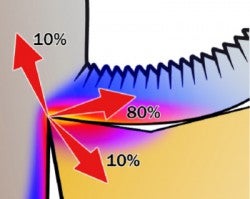
Parametry skrawania i zużycie
Wysoka temperatura w strefie skrawania prowadzi do zmniejszenia sił skrawania. Przy zbyt niskiej prędkości wydziela się zatem mniej ciepła, co może prowadzić do wyłamania płytki.
Zużycie kraterowe prowadzi do stopniowego spadku wytrzymałości płytki, ale nie ma dużego wpływu na chropowatość powierzchni, w przeciwieństwie do starcia powierzchni przyłożenia, które wpływa na klasę dokładności wymiarowej przedmiotu.
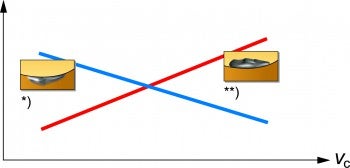
Udział objawów zużycia we wpływie na trwałość ostrzy narzędzi
*) Starcie powierzchni przyłożeni **) Zużycie kraterowe
Kryteria wymiany płytki
Wstępnie zdefiniowana określona chropowatość powierzchni (B) jest często stosowanym i praktycznym kryterium wymiany płytki. Pomiar chropowatości powierzchni jest przeprowadzany automatycznie w oddzielnym urządzeniu, a wynik zostaje podany dla określonej jakości wykończenia.
Aby zoptymalizować proces i nadać mu większą stabilność, należy ustawić wstępnie zdefiniowaną liczbę przedmiotów (A) jako kryterium wymiany płytki. Wartość ta powinna być o 10–20% mniejsza od wymaganej docelowo chropowatości powierzchni, dokładna wartość określana jest osobno dla każdego przypadku.
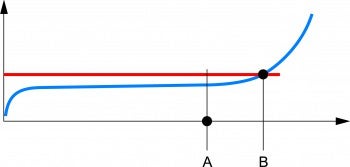
A: Wstępnie zdefiniowana liczba przedmiotów
B: Wstępnie zdefiniowana określona chropowatość powierzchni
Oś X: Liczba przedmiotów
Oś Y: Chropowatość powierzchni
Niebieska linia: Zużycie płytki
Czerwona linia: Maksymalna wartość Ra/Rz
Obróbka w jednym przejściu
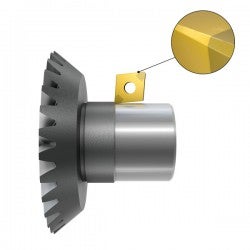
Strategię usuwania metalu jedną płytką można stosować zarówno w obróbce zewnętrznej, jak i wewnętrznej. Ważne znaczenie ma stabilność. W obróbce wewnętrznej wysięg narzędzia nie powinien być większy niż średnica wytaczaka (1×D). W celu zapewnienia udanego przebiegu obróbki zalecamy użycie płytek ze ścinem i niewielkim zaokrągleniem (S) oraz umiarkowanych prędkości i posuwów.
Zalety
- Najkrótszy możliwy czas maszynowy
- Jedno ustawienie narzędzia
Wady
- Trudności z uzyskaniem wysokiej dokładności wymiarowej
- Trwałość mniejsza niż przy obróbce dwiema płytkami
- Odchyłki wymiaru spowodowane stosunkowo szybkim zużyciem
Obróbka dwiema płytkami
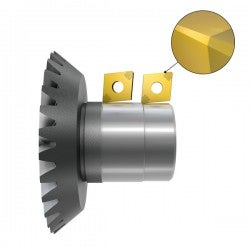
Strategia zakładająca użycie dwóch płytek umożliwia obróbkę bezobsługową powierzchni z wysoką jakością wykończenia. Zalecamy obróbkę zgrubną płytką o promieniu naroża 1.2 mm (0.047 in) oraz obróbkę wykończeniową z użyciem płytki ze ścinem, ale bez zaokrąglenia krawędzi (T). Oba rodzaje płytek powinny mieć geometrię wiper.
Zalety
- Narzędzia optymalne do obróbki zgrubnej i wykończeniowej
- Większe bezpieczeństwo, dokładniejsze wymiary i możliwość dłuższej pracy bez wymiany narzędzia
Wady
- Konieczność użycia dwóch płytek
- Dwie pozycje narzędzi
- Dodatkowa wymiana narzędzia