Fabryka przyszłości
Zakład produkcji narzędzi Sandvik Coromant w Gimo w Szwecji został uznany za jeden z najnowocześniejszych obiektów, działających zgodnie z ideą Industry 4.0, na Światowym Forum Ekonomicznym.
Zakład produkcji narzędzi Sandvik Coromant w Gimo, miejscowości położonej na północ od Sztokholmu, jest wysoko zautomatyzowanym obiektem, w pełni wykorzystującym dobrodziejstwa cyfrowej rewolucji. Fakt ten został niedawno dostrzeżony na Światowym Forum Ekonomicznym, które nominowało ten obiekt do grupy swoich światowych "drogowskazów" przemysłu spośród ponad 1000 zakładów. Każdy taki "drogowskaz" jest wybierany na podstawie ankiety dotyczącej udanego wdrażania technologii cyfrowych, popartego wymiernymi rezultatami.
Zdaniem przedstawicieli Światowego Forum Ekonomicznego zakład produkcyjny w Gimo znacząco poprawił swoją produktywność w konsekwencji wdrożenia cyfrowych rozwiązań w swoich procesach produkcyjnych. Jednym z przykładów jest system bezdotykowej wymiany, umożliwiający automatyczną wymianę wzorników nawet w trakcie zmian bezobsługowych. Dzięki takim zaawansowanym udoskonaleniom zakład w Gimo dołączył do grona światowych drogowskazów przemysłu, by gościć przedstawicieli innych firm z branży wytwórczej i dzielić się z nimi swoją wiedzą.
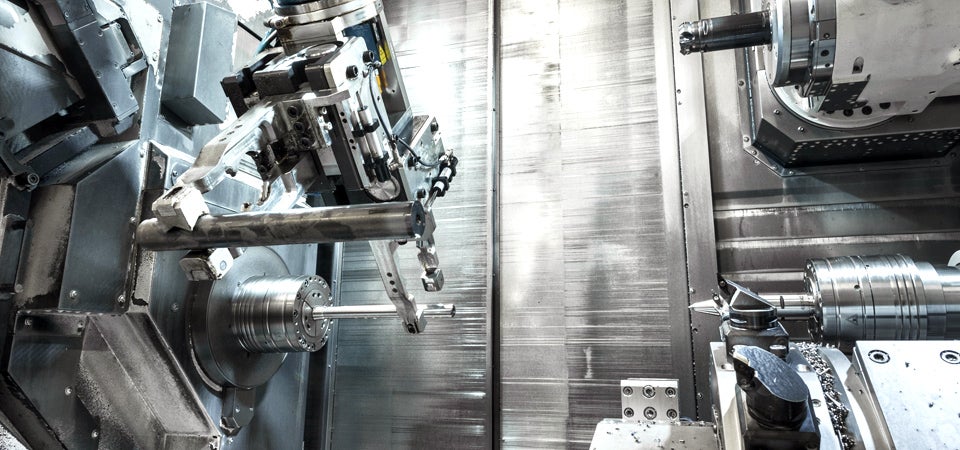
Wyróżnienie zostało przyjęte z prawdziwą dumą, mówi Lars Matiasson, dyrektor ds. technologii produkcji Sandvik Coromant, zwłaszcza że zostało przyznane jako wyraz uznania dla długotrwałych inicjatyw wspierających innowacje. – „Zakład w Gimo rozpoczął swoją drogę ku cyfrowej produkcji 30 lat temu, w momencie wdrożenia parametrycznego systemu CAD/CAM. Po kilku latach połączyliśmy go z systemem inteligentnej automatyki, tym samym tworząc pierwszą cyfrowo sterowaną linię produkcyjną. To była raczej ewolucja, niż rewolucja”.
„Obecnie cyfrowe rozwiązania i przepływ informacji obejmuje cały proces produkcyjny w zakładzie” – kontynuuje Lars Matiasson – „od zarządzania zapasami magazynowymi, przez działanie obrabiarek, po konserwację zapobiegawczą. Duch innowacyjności zawsze przychodził z góry, od kierownictwa zakładu, które zawsze zachęcało inżynierów do nieszablonowego myślenia i inicjowania zmian. Ostatecznie chodziło o to, by szukać metod wykorzystania technologii do poprawy wydajności i zwiększenia konkurencyjności zakładu. To z kolei pozwoliło myśleć o przyszłości w kategoriach zrównoważonego rozwoju”.
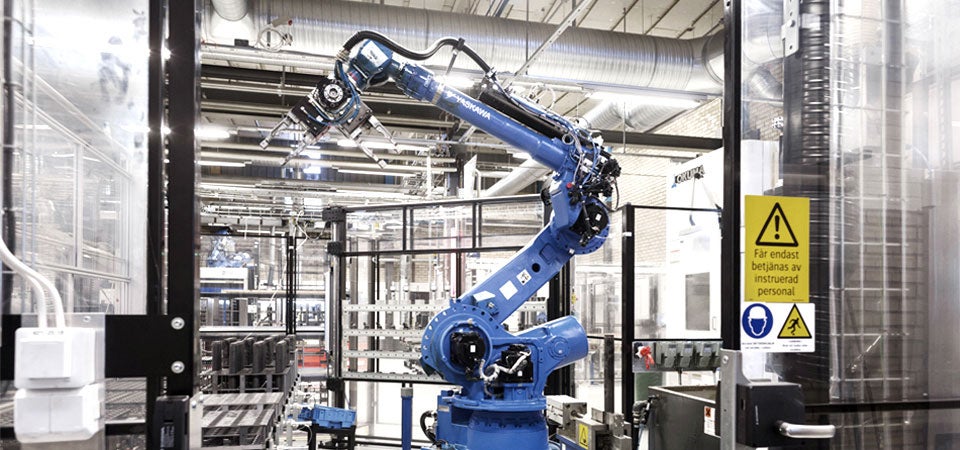
Dobrym przykładem jest system bezdotykowej wymiany. Wcześniej wzorniki w gniazdach obróbkowych były wymieniane ręcznie. Operatorzy ze zmiany dziennej przygotowywali obrabiarki do pracy w nocy, co zajmowało dużo czasu, pochłaniało zasoby i ograniczało elastyczność w trakcie zmian bezobsługowych. Alternatywą okazała się inwestycja w inteligentną automatykę, wykorzystującą uniwersalne roboty, obrabiarki, narzędzia i mocowania , które razem potrafiły wykonywać złożoną operację bezdotykowej wymiany bez nadzoru człowieka.
„Wiele osób mówi o metodach "szczupłej" produkcji, takich jak wymiana jednej formy w minutę, ale my chcieliśmy pójść o krok dalej. Myśleliśmy o całkowitym wyeliminowaniu obsługi” – mówi Lars Matiasson.
„Wszystko odbywało się stopniowo, w miarę nabywania wiedzy. Pierwsze zautomatyzowane gniazdo nie działało tak dobrze, jak się spodziewaliśmy. Właściwie to miało niższą wydajność niż przy obsłudze obrabiarki przez operatora. Ale digitalizacja zawsze tak wygląda - uczysz się na błędach. Stopniowo wprowadzaliśmy poważne ulepszenia i zrobotyzowane gniazda zaczęły osiągać pożądaną wydajność. Próby i błędy są ważną częścią późniejszego sukcesu”.
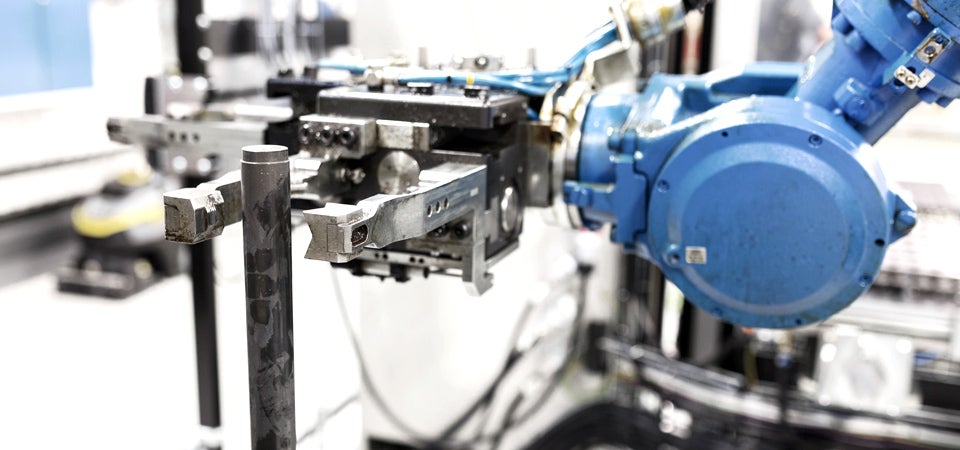
Technologie cyfrowe, stanowiące niewątpliwe ulepszenia, używane są także w innych obszarach działalności zakładu w Gimo, na przykład w obszarze utrzymania ruchu. Coraz częściej na różne maszyny i urządzenia w zakładzie montuje się czujniki zbierające dane o ciśnieniu, temperaturze, drganiach i poziomie hałasu. Te dane, poddane następnie skomplikowanej analizie, pozwalają uwidocznić schematy działania i problemy, zanim dojdzie do przestoju.
Obecnie inżynierowie zbierają dane z całego zakładu produkcyjnego dotyczące robotów, obrabiarek CNC, a nawet narzędzi skrawających. Po ich pozyskaniu i analizie, dane dostarczają cennych informacji na temat stanu urządzeń. Te z kolei pozwalają przewidywać i zapobiegać usterkom, co przekłada się na zwiększenie wydajności zakładu.
Sandvik Coromant coraz częściej prowadzi analizy środowiska produkcyjnego w czasie rzeczywistym, pozwalające na wykonywanie jeszcze dokładniejszych regulacji obrabiarki we właściwym czasie. – „Kolejnym etapem będzie wdrożenie zaawansowanych technologii, takich jak sztuczna inteligencja i uczenie maszynowe. W takiej technologii maszyna może uczyć się na podstawie danych historycznych i ma pewien stopień samokontroli. To naprawdę fascynujące”.
Pomimo godnych odnotowania rozwiązań technologicznych oraz tytułu światowego drogowskazu przemysłu przyznanego przez Światowe Forum Ekonomiczne, proces cyfryzacji w zakładzie w Gimo nieustannie trwa.