Hoe een goede componentkwaliteit bereiken bij het draaien
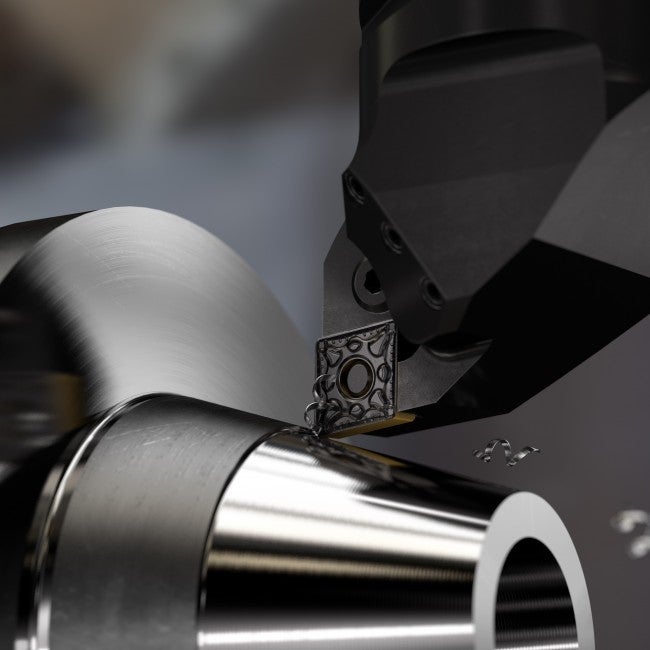
Om gedraaide componenten van goede kwaliteit te verkrijgen, is spaanbeheersing één van de belangrijkste factoren om rekening mee te houden. Selecteer de juiste snijgegevens en volg onze toepassingstips voor een goede componentkwaliteit.
Succesvolle spaanbeheersing
Spaanbeheersing is één van de sleutelfactoren bij het draaien, en er zijn in principe drie manieren van spaanbreken:
- Zelfbrekend (bijvoorbeeld grijs gietijzer)
- Spaanbreking tegen het gereedschap
- Spaanbreking tegen het werkstuk
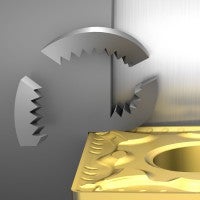
Zelfbrekend
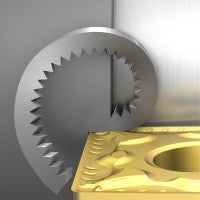
Spaanbreking tegen het gereedschap
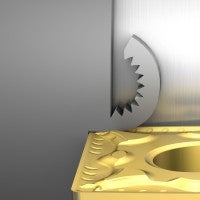
Spaanbreking tegen het werkstuk
Factoren die invloed hebben op spaanbreking
- Wisselplaatgeometrie: Gebaseerd op de breedte van de spaangroef en het micro- en macro-geometrieontwerp, zal de spaan open of meer gecomprimeerd zijn
- Neusradius: Een kleinere neusradius beheerst de spaan beter dan een grotere neusradius
- Instel (geleiding) hoek: Afhankelijk van de hoek wordt de spaan in diverse richtingen geleid; naar een hoek toe of vanuit een hoek
- Snedediepte: Afhankelijk van het werkstukmateriaal beïnvloedt een grotere snijdiepte de spaanbreking, wat leidt tot grotere krachten om de spaan te breken en te verwijderen
- Voeding: Een hogere voeding zorgt in het algemeen voor sterkere spanen. Kan in sommige gevallen helpen bij de spaanbreking en de spaanbeheersing
- Snijsnelheid: Een verandering in snijsnelheid kan de spaanbrekingsprestaties beïnvloeden
- Materiaal: Een kortspanend materiaal (bijvoorbeeld gietijzer) is over het algemeen gemakkelijk te bewerken. Voor materialen met een uitstekende mechanische sterkte en bestendigheid tegen kruipvervorming
(de neiging voor vaste stoffen om langzaam te bewegen of te vervormen onder belasting, bijvoorbeeld, Inconel), is de spaanbreking een groter punt van zorg
Snijgegevens voor draaien
Houd altijd rekening met de machine, het gereedschap, de wisselplaat en materiaal bij het kiezen van de juiste snelheden en voedingen voor draaien.
- Start met een lage voeding om de veiligheid van de wisselplaat en de oppervlakte-afwerking te garanderen, verhoog vervolgens de voeding om de spaanbreking te verbeteren
- Werk met een snijdiepte die groter is dan de neusradius. Dit minimaliseert de radiale afbuiging van de wisselplaat, wat belangrijk is bij inwendig bewerken
- Een te laag ingestelde snijsnelheid zal de standtijd verkorten. Werk altijd met de aanbevolen snijsnelheid, vc m/min (ft/min)
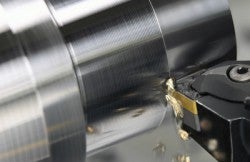
Verbeter de kwaliteit van het draaicomponent met koelmiddel
Wanneer koelmiddel correct wordt toegepast, zal het de proceszekerheid verhogen en de prestaties van het gereedschap en de componentkwaliteit verbeteren. Houd rekening met het volgende bij het gebruik van koelmiddel:
- Gereedschappen met precisiekoeling worden sterk aanbevolen voor nabewerken
- De benodigde koelmiddeldruk voor het breken van de spaan hangt af van de spuitmonddiameter (uitvoer), het materiaal dat wordt bewerkt, de snedediepte en voeding
- De benodigde koelmiddelstroom hangt af van de druk en het totale koelmiddeltoevoergebied van de koelmiddelgaten
- In voor- en tussenbewerkingen wordt aanbevolen om indien mogelijk koelmiddel van onderaf toe te passen
- Voor nabewerkingen wordt aanbevolen om zowel precisiekoelmiddel als onderkoelmiddel toe te passen.
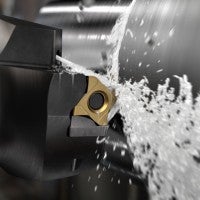
Uitdagingen oplossen met correct toegepast koelmiddel
- Spaanbeheersingsproblemen: Gebruik koelmiddel van boven
- Afmetingsproblemen: Normaliter veroorzaakt door te hoge temperatuur – gebruik koelmiddel boven en onder met zo veel mogelijk druk
- Slechte oppervlaktekwaliteit: Gebruik koelmiddel van boven wanneer het probleem wordt veroorzaakt door spanen
- Onvoorspelbare standtijd bij voorbewerkingen: Gebruik alleen onderkoeling
- Onvoorspelbare standtijd bij nabewerkingen: – Gebruik zowel boven- als onderkoeling
- Slechte spaanverwijdering bij inwendige bewerkingen: Gebruik boven- en onderkoeling plus een zo hoog mogelijke druk
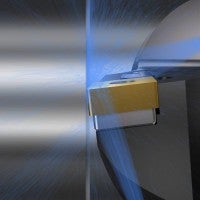
Hoe koelmiddel en snijvloeistof toe te passen bij draaien
Hoe u een goede oppervlakte-afwerking voor draaiwerkstukken kunt bereiken
Algemene regels voor oppervlakte-afwerking:
- De oppervlaktewaarde kan vaak worden verbeterd door een hogere snijsnelheid toe te passen
- De wisselplaatgeometrie (neutrale, positieve en negatieve spaanhoek alsmede positieve vrijloophoeken) hebben invloed op de oppervlakte-afwerking
- De keuze van de wisselplaatsoort heeft enige invloed op de oppervlaktewaarde
- Kies in geval van neiging tot trillingen een kleinere neusradius
Wiper wisselplaat
Wiper-wisselplaten kunnen componenten draaien bij hoge voedingen, zonder dat dit ten koste gaat van een goede oppervlakte-afwerking of spaanbreekcapaciteit.
Een algemene richtlijn is: Twee keer de voedingssnelheid, zelfde oppervlakte-afwerking. Dezelfde voedingssnelheid, een twee keer zo goede oppervlakte-afwerking.
Wiper-wisselplaten zijn ontworpen om het gegenereerde oppervlak glad te maken als de wisselplaat langs het werkstuk wordt ingevoerd. Het wiper-effect is primair bedoeld voor het rechtlijnig draaien en vlakken.
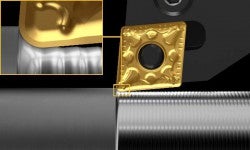
Standaard radius
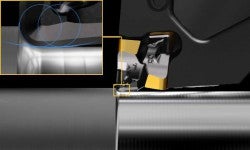
Wiper radius
Hoe de wiper-geometrie te kiezen
Vergelijking, standaard wisselplaat versus wiper wisselplaat gebaseerd op voeding
Opmerking! Alle waarden voor standaard radii zijn theoretisch berekend. De waarden voor de wiper-radius zijn gebaseerd op experimentele waarden in laaggelegeerd staal.
Voeding mm (inch) | Standaard RE 0.4 mm (0.016 inch) Ra µm (µinch) | Wiper (-WF/-WM) RE 0.4 mm (0.016 inch) Ra µm (µinch) | Standaard RE 0.8 mm (0.031 inch) Ra µm (µinch) | Wiper (-WMX) RE 0.8 mm (0.031 inch) Ra µm (µinch) |
0,07 (0,003) | 0.31 (12.4) | 0.30 (12.0) | - | - |
0.10 (0.004) | 0.63 (25.2) | 0.32 (12.8) | 0.31 (12.4) | - |
0,12 (0,005) | 0.90 (36.0) | 0,45 (18,0) | 0.45 (18.0) | - |
0,15 (0,006) | 1.41 (56.4) | 0.70 (28.0) | 0.70 (28.0) | 0.25 (10.0) |
0.18 (0.007) | 2.03 (80.8) | 1.00 (40.0) | 1.00 (40.4) | 0.30 (12.0) |
0.20 (0.008) | 2.50 (100.0) | 1.25 (50.0) | 1.25 (50.0) | 0.35 (14.0) |
0.22 (0.009) | 3.48 (139.2) | 1.74 (69.6) | 1.74 (69.6) | 0.40 (16.0) |
0.25 (0.010) | - | - | 2.25 (90.0) | 0.45 (18.0) |
0.28 (0.011) | - | - | 2.82 (112.8) | 0.50 (20.0) |
0.30 (0.012) | - | - | 3.23 (129.2) | 0.55 (22.0) |
0.35 (0.014) | - | - | 4.40 (176.0) | 0.60 (24.0) |
0.40 (0.016) | - | - | 5.75 (230.0) | 0.70 (28.0) |
0.45 (0.018) | - | - | 8.54 (341.6) | 1.1 (44.0) |
0.50 (0.020) | - | - | 10.55 (422.0) | 1.3 (51.0) |
Voeding mm (inch) | Standaard RE 1.2 mm (0.047 inch) Ra µm (µinch) | Wiper (-WMX) RE 1.2 mm (0.047 inch) Ra µm (µinch) | Standaard RE 1.6 mm (0.063 inch) Ra µm (µinch) | Wiper (-WMX) RE 1.6 mm 1) (0.063 inch) Ra µm (µinch) |
0,15 (0,006) | 0.47 (18.8) | - | - | - |
0.18 (0.007) | 0.68 (27.2) | - | - | - |
0.20 (0.008) | 0.83 (33.3) | 0.3 (12.0) | 0.63 (25.2) | - |
0.22 (0.009) | 1.16 (46.4) | 0.3 (12.0) | 0.87 (34.8) | - |
0.25 (0.010) | 1.50 (60.0) | 0.4 (16.0) | 1.12 (44.8) | 0.3 (12.0) |
0.28 (0.011) | 1.88 (75.2) | 0.4 (16.0) | 1.41 (56.4) | 0.35 (14.0) |
0.30 (0.012) | 2.16 (86.4) | 0.4 (16.0) | 1.62 (64.8) | 0.4 (16.0) |
0.35 (0.014) | 2.93 (117.2) | 0.5 (20.0) | 2.20 (88.0) | 0.4 (16.0) |
0.40 (0.016) | 3.83 (153.2) | 0.65 (26.0) | 2.88 (115.2) | 0.4 (16.0) |
0.45 (0.018) | 5.70 (228.0) | 0.85 (34.0) | 4.27 (170.8) | 0.5 (20.0) |
0.50 (0.020) | 7.03 (281.2) | 1.15 (46.0) | 5.27 (210.8) | 0.7 (28.0) |
0.55 (0.022) | 8.51 (340.4) | 1.2 (48.0) | 6.38 (255.2) | 0.9 (36.0) |
0.60 (0.024) | 10.13 (405.2) | 1.3 (52.0) | 7.59 (303.6) | 1.05 (42.0) |
0.65 (0.026) | - | - | 8.91 (356.4) | 1.25 (50.0) |
0.70 (0.028) | - | - | 10.31 (413.6) | 1.3 (52.0) |
0.85 (0.033) | - | - | 15.24 (609.6) | 1.9 (76.0) |
0.90 (0.035) | - | - | 17.09 (683.0) | 2.1 (84.0) |
- Waarden voor 1,6 mm (0,06) radius zijn gebaseerd op een DNMX-wisselplaat
Toepassingstips voor uitwendig draaien
Trillingsgevoelige componenten
Snede in één pas (bijvoorbeeld een buis)
Het wordt aanbevolen om de hele snede in één pas te bewerken om de kracht naar de klauwplaat/spil in axiale richting te leiden.
Voorbeeld:
Buitendiameter (OD) of 25 mm (0.984 inch)
Binnendiameter (ID) of 15 mm (0.590 inch)
Snedediepte, ap = 4,3 mm (0.169 inch)
Resulterende wanddikte = 0,7 mm (0.028 inch)
OD = 25 mm (0.984 inch) | ap 4.3 mm (0.169 inch) |
![]() | ID = 15 mm (0.590 inch) |
Een instelhoek dicht bij 90° (instelhoek 0°) kan worden gebruikt voor het geleiden van de snijkrachten in axiale richting. Dit leidt tot een minimale buigkrachten op het werkstuk.
Snede in twee passen
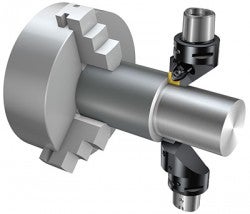
Gesynchroniseerde bewerking van bovenste en onderste revolver zal radiale snijkrachten tegen elkaar opheffen en trilling en buiging van het werkstuk voorkomen.
Slanke/dunwandige werkstukken
Indien werkstukken met slanke/dunne wand worden gedraaid, houd dan rekening met het volgende:
- Gebruik een instelhoek dicht bij 90° (geleidingshoek 0°). Zelfs een kleine wijziging (van een 91/-1 naar een 95/-5 gradenhoek) heeft invloed op de snijkrachtrichting tijdens het bewerken
- De snedediepte,ap, moet groter zijn dan de neusradius, RE. Een grote ap verhoogt de axiale kracht, Fz, en verlaagt de radiale snijkracht, Fx, welke trilling veroorzaakt
- Gebruik een wisselplaat met scherpe snijkant en kleine neusradius, RE, die geringe snijkrachten genereert
- Overweeg het gebruik van Cermet of PVD soort voor slijtvastheid en een scherpe snijkant van de wisselplaat, hetgeen de voorkeur geniet in dit type gebruik
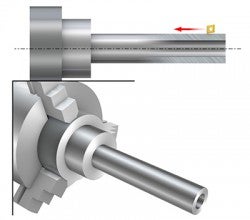
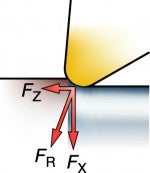
Draaien in hoeken
Volg stappen 1-5 om beschadiging van de wisselplaatsnijkant te voorkomen. Deze methode is zeer gunstig voor CVD-gecoate wisselplaten en kan de breukfrequentie aanzienlijk reduceren.
Stap 1-4:
Houd de afstand van elke stap (1-4) hetzelfde als de voeding om spaanophoping te voorkomen.
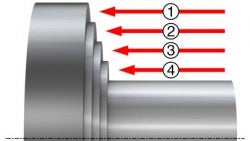
Stap 5:
Bewerk de laatste snede in één verticale snede, te beginnen van de buitendiameter, gericht naar de binnendiameter.
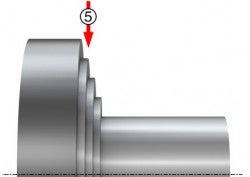
Er kunnen ook problemen optreden met spanen op de radii bij het bewerken van de binnendiameter naar de buitendiameter bij het vlakken in de hoek. Het wijzigen van het gereedschapspad kan de spaanrichting omdraaien en het probleem oplossen.
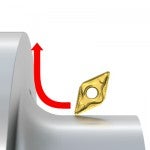
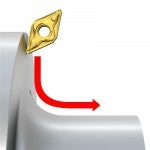
Vlakken
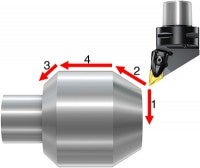
Begin met het vlakken (1) en de aanschuining (2). Indien mogelijk en als geometrische condities op het werkstuk het toestaan, bewerk dan de aanschuining (3). De langssnede (4) is de laatste bewerking en de wisselplaat zal een soepele intrede en uittrede uitvoeren tijdens de bewerking.
Vlakken moet de eerste bewerking zijn om het referentiepunt op het werkstuk in te stellen voor de volgende pas.
Braamvorming is vaak een probleem aan het einde van een snede (bij het uittreden uit het werkstuk). Door een aanschuining of radius over te laten (over een hoek rollen) zou braamvorming kunnen minimaliseren of voorkomen.
Een aanschuining op het component zal leiden tot een soepelere intrede van de wisselplaatsnijkant (zowel bij het vlakken als longitudinaal draaien).
Onderbroken bewerking

Bij het uitvoeren van onderbroken sneden:
- Gebruik een PVD-soort om snijkanttaaiheid te bieden in toepassingen met snelle onderbrekingen, bijvoorbeeld zeskantstaven
- Gebruik een taaie CVD hardmetaalsoort voor bulk hardheid in toepassingen met grote componenten en zware onderbrekingen
- Overweeg om een sterke spaanbreker te gebruiken om voldoende uitbrekingsbestendigheid te bieden
- Het kan gunstig zijn om de koeling uit te schakelen om thermische barsten te voorkomen
Nabewerken van werkstuk met ondersnijding (slijp-vrijsteek)
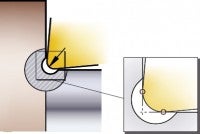
Gebruik de grootst mogelijke neusradius, RE, voor langsdraaien en vlakdraaien, wat resulteert in:
- Een sterke snijkant en meer betrouwbaarheid
- Goede oppervlaktewaarde
- Mogelijkheid om hoge voeding te gebruiken
Overschrijd niet de breedte van de ondersnijding en voer de ondersnijding uit als de laatste bewerking om bramen te verwijderen.
Toepassingstips voor inwendig draaien
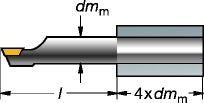
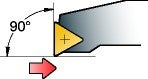
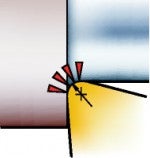
- Kies de grootst mogelijke baardiameter, maar zorg er tegelijkertijd voor dat er genoeg ruimte is voor de spaanafvoer tussen de baar en het gat
- Zorg ervoor dat de spaanverwijdering voldoende is in functie tot de toegepaste snijgegevens en dat het juiste type spanen wordt geproduceerd
- Kies de kleinst mogelijke uitsteeklengte maar zorg er tevens voor dat de lengte van de boorbaar de aanbevolen opspanlengtes toelaat. De opspanlengte mag nooit kleiner zijn dan drie maal de diameter van de baar
- Gebruik gedempte boorbaren wanneer trillingsgevoelige onderdelen worden geproduceerd
- Selecteer een instelhoek zo dicht mogelijk bij 90° (0° instelhoek) om de snijkrachten langs de kotterbaar te leiden. De instelhoek mag nooit kleiner zijn dan 75° (-15° geleidingshoek)
- Als eerste voorkeur moet de wisselplaat een positieve standaardvorm hebben en een positieve wisselplaatgeometrie om de gereedschapsafbuiging te minimaliseren
- Kies een wisselplaatneusradius die kleiner is dan de snedediepte
- Onvoldoende aangrijping van de snijkant kan trillingen vergroten als gevolg van frictie tijdens het snijden. Kies, voor een goede snijactie, een aangrijping van de snijkant die groter is dan de neusradius
- Overmatige aangrijping van de snijkant (grote snedediepte en/of voeding) kan de trillingen versterken door gereedschapsafbuiging
- Wisselplaten met dunne coatings of ongecoate wisselplaten produceren normaal gesproken lagere snijkrachten vergeleken met dik gecoate exemplaren. Dit wordt vooral belangrijk wanneer de relatie tussen lengte/diameter groot is. Een scherpe snijkant verbetert normaal gesproken de gatkwaliteit door de neiging tot trilling te minimaliseren
- Een geometrie met een open spaanbreker kan vaak gunstiger zijn voor inwendig draaien
- Een wisselplaat-hardmetaalsoort met een hogere taaiheid kan worden overwogen in sommige bewerkingen als antwoord op risico's van spaanblokkering of trillingsneigingen
- Overweeg andere gereedschapspaden wanneer spaanvorming verbeterd moet worden
Toepassingstips voor het draaien van harde werkstukken
Naast de algemene aanbevelingen voor draaien, zijn er enkele sleutelfactoren waar rekening mee gehouden moet worden bij het draaien van harde werkstukken (wanneer het productieproces de eigen voorbereiding van het werkstuk omvat vóór het harden):
- Vermijd bramen
- Houd nauwe dimensionale toleranties aan,
- Verricht aanschuinen en maak radii in de zachte fase
- De snede niet abrupt beginnen of beëindigen
- Beginnen of eindigen door in of uit de snede te rollen
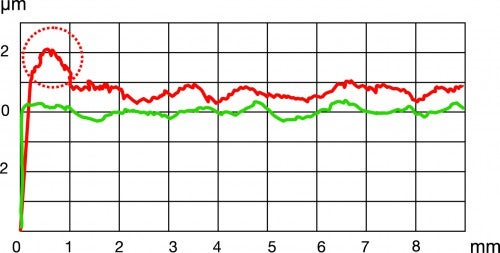
Oppervlaktemetingen
X-as: Kenmerk lengte
Y-as: Diameterafwijking
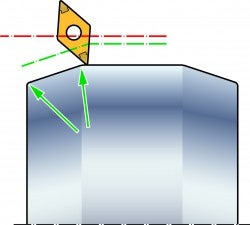
Kritiek oppervlak
Set-up
- Goede machinestabiliteit, opspanning en uitlijning van het werkstuk zijn cruciaal
- Als vuistregel geldt dat een werkstuk-lengte/diameter-verhouding van 2:1 normaal gesproken acceptabel is voor werkstukken die slechts aan één zijde worden ondersteund. Met een extra tegenpuntsteun kan deze verhouding worden uitgebreid
- Merk op dat een thermisch symmetrisch ontwerp van de vaste en losse kop extra maatvastheid zal toevoegen
- Gebruik het Coromant Capto®-systeem
- Om de stijfheid van het systeem te maximaliseren, moeten alle uitsteeklengtes worden geminimaliseerd
- Overweeg hardmetalen boorbaren en Silent Tools voor inwendig draaien
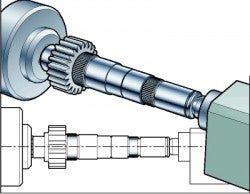
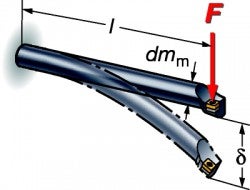
Microgeometrie van de wisselplaat
Twee typische snijkantsvoorbereidingen voor CBN wisselplaten zijn S-type en T-type.
- S-type: Heeft de beste snijkantsterkte. Bestand tegen microschilfering en waarborgt een consistente oppervlaktekwaliteit.
- T-type: Voor de beste oppervlakte-afwerking bij continue sneden en geminimaliseerde braamvorming bij onderbroken sneden. Lagere snijkrachten.
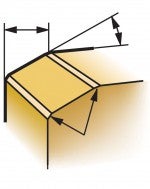
S-type
Aanschuining met lichte fase
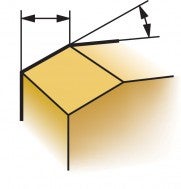
T-type
Aanschuining zonder fase
Hoekgeometrie van de wisselplaat
- Gebruik, wanneer de condities stabiel zijn, altijd een wiper voor de beste oppervlakte-afwerking.
- Gebruik een wisselplaat met lage instelhoek benadering wanneer productiviteitesvereisten hoog zijn.
- Alleen bij slechte stabiliteit (dun werkstuk, etc.) moet een normale radiuswisselplaat worden gebruikt.
Nat of droog bewerken
Draaien van harde werkstukken zonder koelmiddel is de ideale situatie en is volledig uitvoerbaar. Zowel CBN als keramische wisselplaten zijn bestand tegen hoge snijtemperaturen, waardoor de kosten en moeite die gepaard met koelmiddelen worden geëlimineerd.
Sommige toepassingen kunnen koelmiddel vereisen, bijvoorbeeld voor het regelen van de thermische stabiliteit van het werkstuk. Zorg in dergelijke gevallen voor een continue doorstroming van koelmiddel tijdens het hele draaiproces.
In het algemeen wordt de opgewekte hitte tijdens het bewerken verdeeld over de spaan (80%), het werkstuk (10%) en de wisselplaat (10%). Dit onderstreept de noodzaak om de spanen van de snijkantzone te verwijderen.
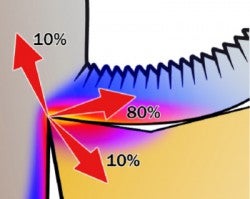
Snijgegevens en slijtage
Een grote hitte in de snijkantzone reduceert de snijkrachten. Daarom kan een te lage snijsnelheid (minder hitte) leiden tot wisselplaatbreuk.
Kraterslijtage beïnvloedt de wisselplaatsterkte geleidelijk, maar niet primair op de oppervlakte-afwerking. Flankslijtage daarentegen heeft geleidelijk invloed op de dimensionale tolerantie.
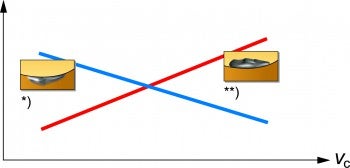
Deel van de standtijd die slijtage bepaalt
*) Vrijloopvlakslijtage **) Kolkslijtage
Criteria voor het vervangen van de wisselplaat
Vooraf bepaalde oppervlakte-afwerking (B) is een veel voorkomend en praktisch criterium voor het vervangen van de wisselplaat. De oppervlakte-afwerking wordt automatisch gemeten in een apart station, en er wordt een waarde toegekend aan een specifieke afwerkingskwaliteit.
Stel voor een geoptimaliseerd en stabieler proces, een vooraf ingesteld aantal werkstukken in (A) als criterium voor het vervangen van de wisselplaat. Deze waarde moet 10–20% minder zijn van de vooraf bepaalde oppervlakte-afwerking, de exacte waarde wordt per geval bepaald.
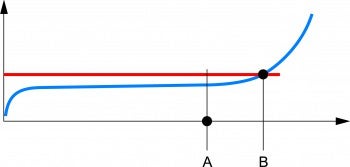
A: Vooraf bepaald aantal componenten
B: Vooraf bepaalde oppervlaktewaarde
X-as: Aantal componenten
Y-as: Oppervlaktewaarde
Blauwe lijn: Wisselplaatslijtage
Rode lijn: Maximum Ra/Rz waarde
Eénsnede-strategie
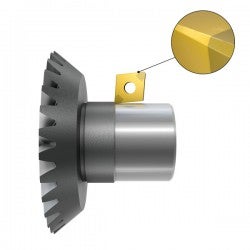
Een één-snede "metaalverwijder"-strategie is uitvoerbaar voor zowel inwendige als uitwendige bewerkingen. Een stabiele set-up is belangrijk, en de gereedschapuitsteeklengte mag niet meer zijn dan eenmaal de baardiameter bij inwendig draaien (1xD). Voor een goede bewerking raden wij aangeschuinde, licht-gefaseerde wisselplaten aan en gematigde snelheid en voeding.
Voordelen
- De snelst mogelijke bewerkingstijd
- Eén gereedschapspositie
Nadelen
- Problemen om te voldoen aan strikte dimensionale toleranties
- Kortere standtijd (dan twee sneden)
- Tolerantieafwijkingen als gevolg van relatief snelle slijtage
Twee-snedenstrategie
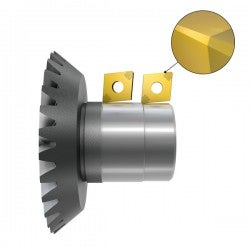
Een twee-snedenstrategie maakt onbewaakte bewerking van hoogwaardige afgewerkte oppervlakken mogelijk. Wij adviseren voorbewerkingswisselplaten met een 1.2 mm (0.047 inch) radius, en de nabewerkingswisselplaten met slechts een aanschuining. Beide wisselplaten in wiper-geometrie.
Voordelen
- Gereedschap geoptimaliseerd voor voorbewerken en nabewerken
- Grotere zekerheid, nauwere toleranties en potentieel langere intervallen voordat wisselen van gereedschap nodig is
Nadelen
- Er zijn twee wisselplaten nodig
- Twee gereedschapsposities
- Eén extra gereedschapswisseling