Scanalatura esterna
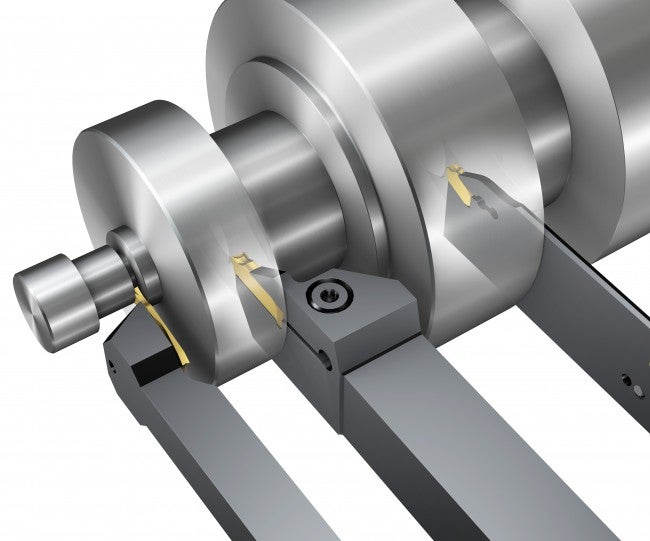
Nelle operazioni di scanalatura, l'obiettivo è una produttività elevata. Generalmente, la scanalatura esterna presenta esigenze di tenacità inferiori rispetto alla troncatura e, grazie a questo, la sicurezza del processo è più facile da ottenere. Questo consente di puntare al miglioramento della produttività, soprattutto per le scanalature ampie che richiedono più tempo rispetto a quelle piccole ed incidono notevolmente sul tempo di lavorazione totale del componente.
Metodi di scanalatura esterna
Per le scanalature profonde, a causa delle lunghe sporgenze richieste e delle difficoltà legate all'evacuazione truciolo e all'accesso del refrigerante al tagliente, la sicurezza del processo può diventare una sfida. La scanalatura a passata singola è il metodo più economico e ad alta produttività per l'esecuzione di scanalature. Tuttavia, se la profondità della scanalatura è superiore alla larghezza dell'inserto, è possibile ricorrere alla scanalatura a passata multipla, alla tornitura a tuffo, alla lavorazione di piani inclinati o alla profilatura. Per la scanalatura esterna, la scelta prioritaria è rappresentata dagli utensili con refrigerante ad alta precisione.
Consigli applicativi: come procedere alla scanalatura esterna
Scanalatura a passata singola

La scanalatura a passata singola è un metodo economico e ad alta produttività per l'esecuzione di scanalature. In caso di passata singola, gli aspetti da considerare sono i seguenti:
- Se la finitura superficiale è importante, utilizzare una geometria di inserto con tecnologia Wiper
- Utilizzare un inserto con tolleranze strette e i corretti valori di raggio di punta e larghezza, privilegiando gli inserti rettificati (ad es. -GF)
- Per la produzione in serie, utilizzare un inserto con profilo e smusso corretti. Se non fosse disponibile nell'assortimento standard, è consigliabile investire in inserti Tailor Made
Sgrossatura di scanalature ampie
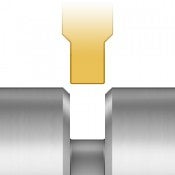
I metodi più comuni per l'esecuzione di scanalature ampie o la tornitura tra spallamenti sono:
- Scanalatura a passata multipla
- Tornitura a tuffo
- Lavorazione di piani inclinati
Tutti e tre i metodi sono operazioni di sgrossatura che devono essere seguite da un'operazione di finitura separata.
Regola empirica: se la larghezza della scanalatura è inferiore alla profondità, utilizzare il metodo della scanalatura a passata multipla; in caso contrario, ricorrere alla tornitura a tuffo. Per i componenti con elevate sporgenze, tuttavia, è possibile utilizzare il metodo della lavorazione di piani inclinati.
Scanalatura a passata multipla

- Per scanalature ampie e profonde (profondità maggiore della larghezza)
- Le flange lasciate per le passate finali (4 e 5) dovrebbero avere una larghezza inferiore a quella dell’inserto (CW -2 x raggi di punta)
- Aumentare l’avanzamento del 30-50% durante la lavorazione delle flange
- La geometria di scelta prioritaria è -GM
Tornitura a tuffo
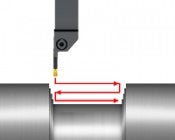
- Per scanalature più ampie e meno profonde (larghezza maggiore della profondità)
- Non eseguire l’avanzamento contro lo spallamento
- Le geometrie di scelta prioritaria sono -TF e -TM
Lavorazione di piani inclinati (tornitura/profilatura)
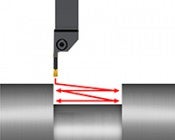
- Migliore controllo truciolo
- Riduce al minimo le forze di taglio radiali e l'usura ad intaglio
- Le geometrie di scelta prioritaria sono -RO ed –RM
Tornitura di finitura di una scanalatura
- Opzione 1: usare una geometria per tornitura
- Opzione 2: usare una geometria di profilatura, ad es. per scanalature con raggi grandi
- Profondità di taglio assiale e radiale consigliata 0.5–1.0 mm (0.02–0.04 poll.)
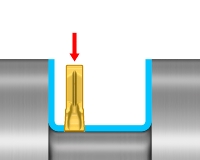
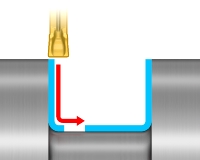
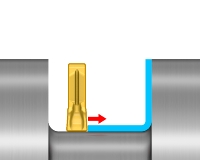
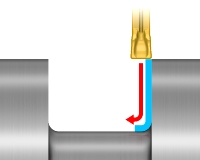
Tornitura e scanalatura esterna
Tornitura con inserto per troncatura e scanalatura
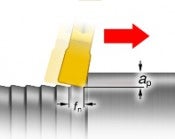
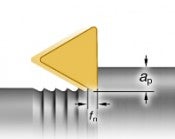
- Per la tornitura laterale, utilizzare una profondità di taglio (ap) superiore al raggio di punta dell'inserto
- Effetto raschiante − la velocità di taglio per profondità di taglio (fn/ap) deve essere abbastanza alta da assicurare una leggera flessione di utensile e inserto. Ciò assicura il necessario disimpegno tra tagliente e superficie lavorata
- Con valori di fn/ap troppo bassi, si possono verificare effetti di sfregamento sull’utensile, vibrazioni e finitura superficiale insoddisfacente
- Max ap = 75% della larghezza dell’inserto
Finitura superficiale | |||||
Ra µm | |||||
![]() | |||||
Avanzamento, fn mm/giro poll./giro |
![]() | TNMG 160404 |
![]() | TNMG 160408 |
![]() | Inserto di troncatura e scanalatura -5 mm -RM |
![]() | Inserto di troncatura e scanalatura -4 mm -TF |
![]() | Inserto di troncatura e scanalatura -6 mm -TM |
Nel grafico è rappresentata la finitura superficiale ottenuta con inserti di troncatura e scanalatura in confronto a un inserto TNMG con raggio di punta 04 o 08.
Tornitura di una scanalatura
Durante la tornitura laterale, si deve necessariamente verificare una flessione dell’utensile e dell’inserto. Tuttavia, una flessione eccessiva può provocare vibrazioni e rotture:
- Una lama più spessa riduce la flessione
- Una sporgenza più corta (OH) riduce la flessione (δ)
- Evitare operazioni di tornitura con utensili lunghi e/o sottili
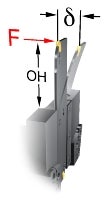
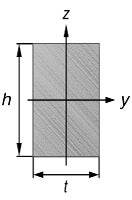
Una sporgenza più corta riduce la flessione laterale
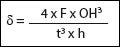
Esecuzione di scarichi e scanalatura esterna
Diversi componenti richiedono operazioni di rettifica o filettatura. Per eseguire queste operazioni su uno spallamento è necessario un disimpegno; pertanto, è consigliabile utilizzare inserti specifici per l'esecuzione di scarichi. Ad esempio: T-Max Q-Cut® e CoroCut® 1-2
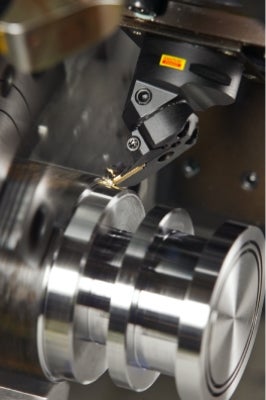
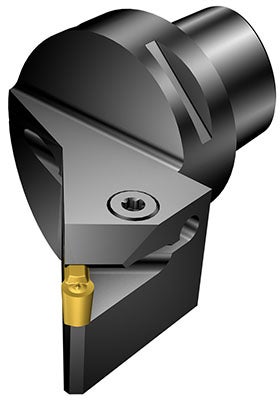