Verschleiß an den Schneidkanten
Um die Vor- und Nachteile jedes Werkstoffes richtig zu verstehen, ist es wichtig, Kenntnisse über die verschiedenen Verschleißmechanismen zu haben, denen Schneidwerkzeuge ausgesetzt sind.
Freiflächenverschleiß
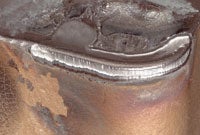
Abrasiv
Die am meisten vorkommende und bevorzugte Art von Verschleiß, da sie eine berechenbare und stabile Standzeit bietet. Freiflächenverschleiß erfolgt aufgrund von Reibung, die durch harte Bestandteile im Werkstoff verursacht wird.
Kolkverschleiß
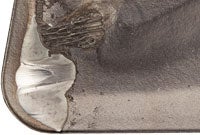
Chemisch
Kolkverschleiß tritt an der Spanfläche der Wendeschneidplatte auf. Er ist auf eine chemische Reaktion zwischen Werkstoff und Schneidwerkzeug zurückzuführen und wird durch die Schnittgeschwindigkeit weiter verstärkt. Großflächiger Kolkverschleiß schädigt die Schneidkante und kann zu deren Bruch führen.
Aufbauschneidenbildung
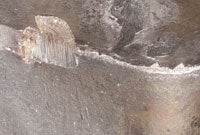
Adhäsiv
Diese Verschleißart wird durch das Festschweißen des Spans an der Wendeschneidplatte hervorgerufen. Sie tritt sehr häufig bei der Bearbeitung von adhäsiven Werkstoffen wie Stahl mit niedrigem Kohlenstoffgehalt, rostfreiem Stahl und Aluminium auf. Niedrige Schnittgeschwindigkeiten verstärken die Aufbauschneidenbildung zusätzlich.
Kerbverschleiß
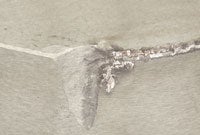
Adhäsiv
Verschleiß an der Wendeschneidplatte, der durch übermäßige Beschädigung an Span- sowie Freifläche der Platte an der Tiefenschnittlinie gekennzeichnet ist. Verursacht durch Adhäsion (Festschweißen der Späne) und eine durch Verformung gehärtete Oberfläche. Eine häufige Verschleißart bei der Bearbeitung von HRSA/SS (Rostfreier Stahl).
Plastische Deformation
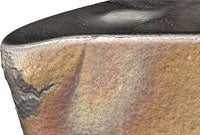
Thermisch
Plastische Deformation tritt dann auf, wenn das Werkzeugmaterial weich wird. Das passiert, wenn die Arbeitstemperatur zu hoch für eine bestimmte Sorte ist. Im Allgemeinen verbessern härtere Sorten und dickere Beschichtungen den Widerstand gegen plastische Deformation.
Kammrisse
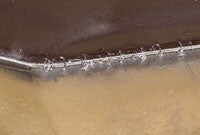
Thermisch
Ändert sich die Temperatur an der Schneidkante sehr schnell von heiß auf kalt, können senkrecht zur Schneidkante Mehrfachrisse auftreten. Kammrisse stehen in Verbindung mit Schnittunterbrechungen, üblich bei Fräsvorgängen; ihre Bildung wird durch Einsatz von Kühlschmierstoff verstärkt.
Absplittern/Bruch der Schneidkante
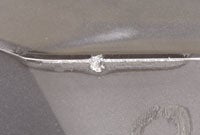
Mechanisch
Schneidkantenausbrüche oder -brüche sind das Ergebnis einer Überbelastung durch mechanische Zugspannungen an der Schneidkante. Diese Spannungen können eine Reihe von Ursachen haben, u.a. Spanhämmern, zu große Schnitttiefe oder zu hoher Vorschub, Sandeinschlüsse im Werkstoff, Aufbauschneidenbildung, Vibrationen oder übermäßiger Verschleiß an der Wendeschneidplatte.
Suchen Sie Werkzeugempfehlungen?
Hier finden Sie unsere Zerspanungswerkzeuge chevron_right
Brauchen Sie Beratung?
Stellen Sie uns eine Frage chevron_right
Was es sonst noch über die Grundlagen unserer Metallzerspanung zu lernen gibt?
Registrieren Sie sich für unser kostenloses E-Learning Programm chevron_right