Schneidstoffsorten

Einführung
Die Auswahl von Schneidstoff und Sorte ist ein entscheidender Faktor bei der Vorbereitung eines erfolgreichen Zerspanungsprozesses.
Ein Grundwissen über jeden Schneidstoff und seine Leistung ist deshalb für die richtige Wahl hinsichtlich der Anwendung ausschlaggebend. Berücksichtigt werden sollte dabei, der zu bearbeitende Werkstoff, die Form und Art des Werkstücks, die Bearbeitungsbedingungen und die für den jeweiligen Vorgang gewünschte Oberflächengüte.
Dieser Abschnitt soll Ihnen zusätzliche Informationen zu jedem Schneidstoff und seinen Vorteilen sowie die besten Einsatzempfehlungen liefern.
Schneidstoffe weisen unterschiedliche Kombinationen von Härte, Zähigkeit und Verschleißfestigkeit auf und sind in zahlreiche Sorten mit speziellen Eigenschaften unterteilt. Allgemein sollte ein Schneidstoff für eine erfolgreiche Anwendung:
- hart sein, für Widerstand gegen Freiflächenverschleiß und Deformation
- zäh sein, für hohe Gesamtbruchfestigkeit
- nicht mit dem Werkstoff reagierend
- chemisch stabil sein, für Widerstand gegen Oxidation und Diffusion
- widerstandsfähig gegen plötzliche thermische Wechselbeanspruchung sein
Schneidstoffe mit beschichtetem Hartmetall
- Beschichtung – CVD
- Beschichtung – PVD
- Hartmetall
Was sind Schneidstoffe mit beschichtetem Hartmetall?
Aus beschichtetem Hartmetall sind derzeit 80-90 % aller Schneidwerkzeugeinsätze. Es wird erfolgreich als Schneidstoff aufgrund seiner einzigartigen Kombination aus Verschleißfestigkeit und Zähigkeit sowie seiner Fähigkeit eingesetzt, zu komplexen Strukturen geformt werden zu können.
Beschichtetes Hartmetall ist eine Kombination aus Hartmetall und Beschichtung. Zusammen bilden sie eine Sorte, die speziell für deren Anwendung angepasst ist.
Beschichtete Hartmetallsorten sind erste Wahl für zahlreiche Werkzeuge und Anwendungen.
Beschichtung – CVD
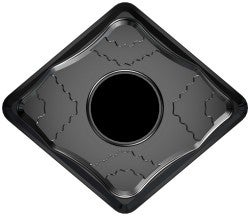
Definition und Eigenschaften
CVD steht für Chemische Gasphasenabscheidung (Chemical Vapour Deposition). Die CVD-Beschichtung erfolgt durch chemische Reaktionen bei Temperaturen von 700-1050°C.
Diese Beschichtungen verfügen über hohe Verschleißfestigkeit und ausgezeichnete Haftung auf Hartmetall.
Das erste CVD-beschichtete Hartmetall war die einschichtige Titancarbidbeschichtung (TiC). Aluminiumoxidbeschichtungen (Al2O3) sowie Titannitrid (TiN)-Beschichtungen kamen später hinzu. Vor einiger Zeit wurden moderne Titancarbonitrid-Beschichtungen (MT-Ti(C,N) oder MT-TiCN im Mittteltemperatur- CVD-Verfahren (MT-CVD) entwickelt, um die Sorteneigenschaften in Hinblick auf die Erhaltung der Hartmetallschicht zu verbessern.
Derzeitig gebräuchliche MT-CVD-Beschichtungen vereinen MT-Ti(C,N), Al2O3 und TiN. Die Eigenschaften der Beschichtungen wurden hinsichtlich Haftung, Zähigkeit und Verschleißeigenschaften ständig durch Optimierungen im Mikrostrukturbereich und den Nachbehandlungen verbessert. Siehe Inveio™-Technologie.
MT-Ti(C,N) - Seine Härte bietet Widerstand gegen Abrasionsverschleiß, was zu weniger Freiflächenverschleiß führt.
CVD-Al2O3 - Chemisch inert mit geringer Wärmeleitfähigkeit, daher widerstandsfähig gegen Kolkverschleiß. Fungiert auch als Wärmeschutz zur Erhöhung der Widerstandsfähigkeit gegen plastische Deformation.
CVD-TiN - Verbessert die Verschleißfestigkeit und wird für die Verschleißerkennung eingesetzt.
Nachbehandlungen - Verbessern Schneidkantenhärte bei unterbrochenen Schnitten und reduzieren die Adhäsionsneigung.
Anwendungen
CVD-beschichtete Sorten sind die erste Wahl bei einer breiten Anwendungspalette, bei der die Verschleißfestigkeit ausschlaggebend ist. Anzutreffen sind diese Anwendungen bei allgemeinen Drehbearbeitungen und dem Bohren in Stahl, wo die dicken CVD-Beschichtungen die Widerstandsfähigkeit gegen Kolkverschleiß ermöglichen, ebenso angewendet bei allgemeinen Drehbearbeitungen von rostfreien Stählen und Frässorten in ISO P, ISO M und ISO K. Beim Bohren werden CVD-Sorten normalerweise in der Außenschneide eingesetzt.
Beschichtung – PVD
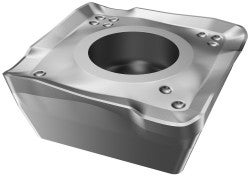
Definition und Eigenschaften
Durch physikalische Gasabscheidung (Physical Vapour Deposition = PVD) hergestellte Beschichtungen erfolgen bei relativ niedrigen Temperaturen (400-600°C). Der Prozess beinhaltet die Verdampfung eines Metalls, das z.B. mit Stickstoff reagiert, um eine harte Nitridverbindung auf der Schneidwerkzeugoberfläche auszubilden.
PVD-Beschichtungen tragen aufgrund ihrer Härte zur Verschleißfestigkeit einer Sorte bei. Ihre Druckspannungen verhelfen darüber hinaus zu Schneidkantenzähigkeit und Widerstand gegen Kammrisse. Siehe Zertivo™-Technologie.
Die Hauptbestandteile der PVD-Beschichtungen werden im Folgenden näher beschrieben. Moderne Beschichtungen sind Kombinationen aus diesen Komponenten in aufeinanderfolgenden Schichten und/oder lamellenartigen Beschichtungen. Letztere verfügen über zahlreiche dünne Schichten im Nanometerbereich, was die Beschichtung sogar noch härter macht.
PVD-TiN - Titannitrid war die erste PVD-Beschichtung. Es hat universelle Eigenschaften und eine goldene Farbe.
PVD-Ti(C,N) - Titancarbonitrid ist härter als TiN und trägt zur Festigkeit gegen Freiflächenverschleiß bei.
PVD-(Ti,Al)N - Titanaluminiumnitrid verfügt über einen hohen Härtegrad gepaart mit Widerstandsfähigkeit gegen Oxidation, was die gesamte Verschleißfestigkeit verbessert.
PVD-Oxid - Wird wegen seiner chemischen Inertanz und erweiterten Widerstandsfähigkeit gegen Kolkverschleiß eingesetzt.
Anwendungen
PVD-beschichtete Sorten werden aufgrund ihrer zähen, aber trotzdem scharfen Schneidkanten auch für adhäsive Werkstoffe empfohlen. Die Anwendungsbereiche sind breit gefächert und schließen alle Vollhartmetallfräser und -bohrer sowie die Mehrzahl der Sorten für das Einstechen, Gewindeschneiden und Fräsen ein. PVD-beschichtete Sorten werden außerdem in großem Umfang bei Schlichtvorgängen sowie als Zentrumschneidensorte beim Bohren eingesetzt.
Hartmetall
Definition und Eigenschaften
Das Hartmetall ist ein metallurgisches Pulvermaterial, bestehend aus: Wolframcarbid (WC)-Partikeln und Kobalt (Co) als Bindemittel. Hartmetalle für Zerspanungsvorgänge bestehen zu mehr als 80 % aus Hartphasen-WC. Zusätzliche kubische Carbonitride sind weitere wichtige Komponenten, insbesondere bei gradient-gesinterten Sorten. er Hartmetallkörper wird – entweder durch Verpressen von Pulver oder durch Spritzguss – zu einer Masse geformt und anschließend durch Sintern verdichtet.
Die WC-Korngröße ist einer der wichtigsten Parameter für die Einstellung des Härte/Zähigkeit-Verhältnisses einer Sorte; je feiner die Korngröße, desto größer die Härte bei einem bestimmten Bindemittelphasengehalt.
Die Menge und Zusammensetzung des Kobalt-Bindemittels beeinflusst die Zähigkeit der Sorte und die Widerstandsfähigkeit gegenüber plastischer Deformation. Bei gleicher WC-Korngröße führt eine höhere Menge an Bindemittel zu einer zäheren Sorte, die widerstandsfähiger gegen plastische Deformation ist. Ein zu geringer Bindemittelgehalt kann einen spröden Werkstoff ergeben.
Kubische Carbonitride, auch als γ-Phase bezeichnet, werden im Allgemeinen hinzugefügt, um die Warmfestigkeit zu erhöhen und Gradienten zu bilden.
Gradienten werden eingesetzt, um höhere Widerstandsfähigkeit gegen plastische Deformation mit Schneidkantenzähigkeit zu kombinieren. In der Schneidkante konzentrierte kubische Carbonitride verbessern, wo nötig, die Warmfestigkeit. Darüber hinaus verhindert ein an Wolframcarbid reiches Bindemittel Risse und Brüche durch Spanhämmern.
Anwendungen
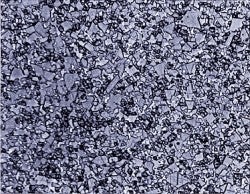
Mittlere bis grobe WC-Korngröße
Mittlere bis grobe WC-Korngrößen versorgen die Hartmetalle mit einer besseren Kombination aus Warmfestigkeit und Zähigkeit. Zusammen mit CVD- oder PVD-Beschichtungen werden sie bei Sorten für alle Bereiche eingesetzt.
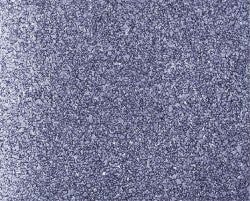
Feine oder Submikrometer-WC-Korngröße
Feine oder Submikrometer-WC-Korngrößen werden für scharfe Schneidkanten mit einer PVD-Beschichtung eingesetzt, um die Stabilität der scharfen Kante noch einmal zu verbessern. Sie profitieren auch von einer höheren Widerstandsfähigkeit gegenüber Wärme und zyklischen mechanischen Belastungen. Zu den typischen Anwendungen gehören Vollhartmetallbohrer und -fräser, Wendeschneidplatten zum Ab- und Einstechen sowie Sorten für das Schlichten.
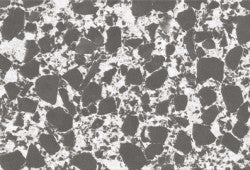
Hartmetall mit Gradient
Die vorteilhafte duale Eigenart von Gradienten wird erfolgreich zusammen mit CVD-Beschichtungen in vielen Hauptsorten für das Drehen, Ab- und Einstechen von Stahl sowie rostfreiem Stahl eingesetzt.
Schneidstoffe mit unbeschichtetem Hartmetall
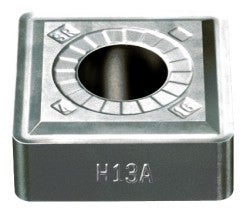
Was sind Schneidstoffe mit unbeschichtetem Hartmetall?
Unbeschichtete Hartmetallsorten machen nur einen geringen Teil des Gesamtsortiments aus. Diese sind entweder reine WC-/Co-Sorten oder sie enthalten eine hohe Menge an kubischen Carbonitriden.
Anwendungen
Typische Anwendungen sind die Bearbeitung von warmfesten Superlegierungen (HRSA) oder Titanlegierungen sowie das Drehen von gehärteten Werkstoffen bei niedriger Geschwindigkeit.
Der Verschleiß unbeschichteter Hartmetallsorten erfolgt schnell aber kontrolliert, mit einem selbstschärfenden Vorgang.
Suchen Sie Werkzeugempfehlungen?
Hier finden Sie unsere Zerspanungswerkzeuge chevron_right
Brauchen Sie Beratung?
Stellen Sie uns eine Frage chevron_right
Was es sonst noch über die Grundlagen unserer Metallzerspanung zu lernen gibt?
Registrieren Sie sich für unser kostenloses E-Learning Programm chevron_right
Cermet-Schneidstoffe
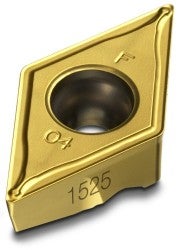
Was ist Cermet?
Cermet ist ein Hartmetall auf Basis von Titanpartikeln. Die Bezeichnung ist eine Zusammensetzung aus Keramik und Metall. Ursprünglich war es eine Verbindung aus TiC und Nickel. Moderne Cermets sind nickelfrei und verfügen über eine Struktur aus Kernpartikeln von Titancarbonitrid Ti(C,N), einer zweiten Hartphase von (Ti, Nb,W)(C,N) sowie Kobalt als Bindemittel.
Ti(C,N) verleiht der Sorte Verschleißfestigkeit, die zweite Hartphase erhöht den Widerstand gegen plastische Deformation und das Kobalt bestimmt die Zähigkeit.
Verglichen mit Hartmetall weist Cermet bessere Verschleißfestigkeit und geringere Neigung zum Kleben auf. Andererseits hat es eine geringere Druck- und Wärmewechselfestigkeit. Cermets können für eine höhere Verschleißfestigkeit auch PVD- beschichtet sein.
Anwendungen
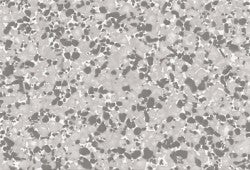
Cermet-Sorten werden bei klebenden Anwendungen, bei denen Aufbauschneidenbildung ein Problem darstellt, eingesetzt. Ihr selbstschärfendes Verschleißmuster hält die Schnittkräfte selbst nach langen Schnittzeiten niedrig. Bei Schlichtvorgängen verlängert dies die Standzeit und ermöglicht enge Toleranzen sowie glänzende Oberflächen.
Typische Anwendungen sind das Schlichten von rostfreien Stählen, Kugelgraphitguss, Stählen mit niedrigem Kohlenstoffgehalt und ferritischen Stähle. Cermets sind auch die Lösung bei allen Eisenwerkstoffen.
Tipps:
- Geringe Schnitttiefe und Vorschub verwenden
- Schneidkante wechseln, wenn der Freiflächenverschleiß 0,3 mm erreicht
- Kammrisse und Brüche aufgrund von Arbeiten ohne Kühlschmierstoff vermeiden
Keramik-Schneidstoffe
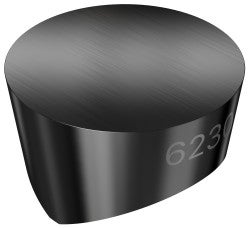
Was sind Keramik-Schneidstoffe?
Alle keramischen Schneidwerkzeuge verfügen über eine ausgezeichnete Verschleißfestigkeit bei hohen Schnittgeschwindigkeiten.
Für eine Vielzahl von Anwendungen sind deshalb zahlreiche Keramiksorten verfügbar.
Oxidkeramiken bestehen aus Aluminiumoxid (Al2O3) und Zirkondioxid (ZrO2), das zur Vermeidung von Rissen beigefügt wurde. Dadurch entsteht ein Werkstoff, der chemisch sehr stabil ist, dem es jedoch an Wärmewechselfestigkeit fehlt.
(1) Mischkeramiken sind teilchenverstärkt durch die Zugabe von kubischen Carbiden oder Carbonitriden (TiC, Ti(C,N)). Dadurch werden Zähigkeit und Wärmeleitfähigkeit verbessert.
(2) Whisker-verstärkte Keramiken verwenden Siliziumcarbid-Whisker (SiCw), um die Zähigkeit beträchtlich zu verbessern und ermöglichen auch den Einsatz von Kühlschmierstoff. Diese Keramiken sind ideal für die Bearbeitung von Ni-Legierungen.
(3) Siliziumnitridkeramik (Si3N4) stellen eine weitere Gruppe der keramischen Werkstückstoffe dar. Längliche Kristalle bilden ein selbstverstärktes Material mit hoher Zähigkeit. Siliziumnitrid-Sorten werden erfolgreich bei Grauguss eingesetzt, ihre mangelnde chemische Stabilität limitiert jedoch ihre Anwendung in anderen Werkstoffen.
Sialon (SiAlON)-Sorten vereinen die Festigkeit einer selbstverstärkten Siliziumnitridstruktur mit gesteigerter chemischer Stabilität. Sie sind ideal für die Bearbeitung von warmfesten Superlegierungen (HRSA).
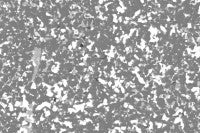
(1) Mischkeramik
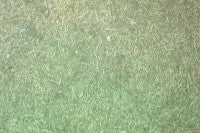
(2) Whisker-verstärkte Keramik
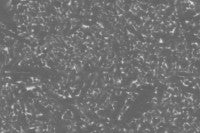
(3) Siliziumnitrid-Keramik
Anwendungen
Keramiksorten haben ein breitgefächertes Einsatzgebiet; sie sind meistens bei Hochgeschwindigkeits-Drehbearbeitungen anzutreffen, aber auch bei Einstech- und Fräsvorgängen. Die speziellen Eigenschaften jeder Keramiksorte ermöglichen bei richtigem Einsatz eine hohe Produktivität. Deshalb ist es für ein gutes Arbeitsergebnis wichtig zu wissen, wann und wie die Keramiksorten einzusetzen sind.
Allgemeine Beschränkungen der Keramiken betreffen ihre Wärmewechselfestigkeit und Bruchzähigkeit.
Schneidstoffe mit polykristallinem kubischem Bornitrid
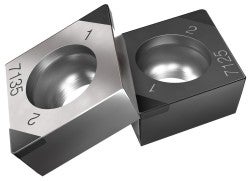
Was sind Schneidstoffe mit polykristallinem kubischem Bornitrid?
Polykristallines kubisches Bornitrid (CBN) ist ein Schneidstoff mit ausgezeichneter Warmfestigkeit, das bei sehr hohen Schnittgeschwindigkeiten eingesetzt werden kann. Es zeichnet sich außerdem durch eine gute Zähigkeit und Wärmewechselfestigkeit aus.
Moderne CBN-Sorten sind keramische Verbundwerkstoffe, die einen CBN-Anteil von 40-65 % aufweisen. Das keramische Bindemittel fügt dem CBN, das anderenfalls sehr anfällig für chemischen Verschleiß ist, Verschleißfestigkeit hinzu. Eine andere Sortengruppe ist durch einen sehr hohen Anteil (85 bis fast 100 %) CBN gekennzeichnet. Diese Sorten verfügen für eine bessere Zähigkeit über einen Metallbinder.
CBN wird auf einen Hartmetallträger aufgelötet, um eine Wendeschneidplatte zu bilden. Die Safe-Lok™-Technologie verbessert darüber hinaus die Bindung der CBN-Tips auf negativen Wendeschneidplatten.
Anwendungen
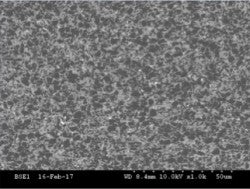
CBN-Sorten werden weitläufig für die Schlichtbearbeitung beim Drehen gehärteter Stähle mit einer Härte von mehr als 45 HRc verwendet. Über 55 HRc ist CBN das einzige Schneidwerkzeug, das die herkömmlichen Schleifmethoden ersetzen kann. Weichere Stähle unter 45 HRc enthalten einen höheren Ferritgehalt, was negative Auswirkungen auf die Verschleißfestigkeit von CBN hat.
CBN kann ebenfalls für Hochgeschwindigkeitsschruppen von Grauguss eingesetzt werden – sowohl bei Dreh- als auch Fräsbearbeitungen.
Schneidstoffe mit polykrystallinem Diamant (PKD)
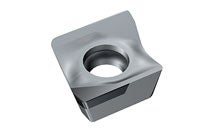
Was sind Schneidstoffe mit polykristallinem Diamant (PKD)?
PKD ist eine Verbindung aus Diamantpartikeln und metallischem Bindemittel. Diamant ist der härteste Werkstoff, und damit auch abriebfesteste aller Werkstoffe. Als Schneidwerkzeug ist es hochgradig verschleißfest, allerdings fehlt ihm bei hohen Temperaturen die chemische Stabilität, und der Kohlenstoff im Diamant diffundiert leicht ins Eisen.
Anwendungen
PKD-Werkzeuge sind begrenzt auf NE-Materialien, wie z.B. hoch siliziumhaltiges Aluminium, Metallmatrixverbundwerkstoffe (MMC) sowie mit Kohlenstofffasern verstärkte Kunststoffe (CFRP). PKD mit flüssigem Kühlschmierstoff kann außerdem bei Feinstschlichtanwendungen in Titan eingesetzt werden.
Sandvik Coromant Sorten
Informationen zu Wendeschneidplatten und Schneidstoffe von Sandvik Coromant finden Sie hier.
Anhand dieser Informationen können Sie Ihre Wendeschneidplatte oder Sorte, je nach Werkstoff oder Anwendungsbereich, auswählen.
Suchen Sie Werkzeugempfehlungen?
Hier finden Sie unsere Zerspanungswerkzeuge chevron_right
Brauchen Sie Beratung?
Stellen Sie uns eine Frage chevron_right
Was es sonst noch über die Grundlagen unserer Metallzerspanung zu lernen gibt?
Registrieren Sie sich für unser kostenloses E-Learning Programm chevron_right