Turbinenschaufel
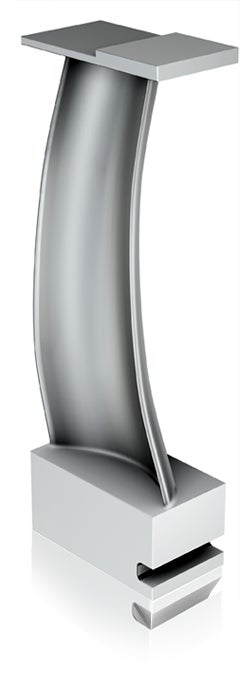
Bearbeitung von Turbinenschaufeln erreicht neues Niveau
Die konkurrenzfähige Fertigung von Turbinenschaufeln für Dampf- und Gasturbinen ist eine große Herausforderung, da hier hohe Anforderungen für die Zerspanung gelten:
- Die Werkstoffe der Bauteile weisenunterschiedliche Zerspanbarkeit auf(manche Werkstoffe erfordern daher spezielle Schneidplatten).
- Es müssen große Teile des Werkstoffs entfernt und eine hohe Oberflächengüte erzielt werden (ohne negative Beeinträchtigungen der Turbinenschaufel, zum Beispiel durch Eigenspannung).
- Die Form der Bauteile ist komplex (einige erfordern moderne CAMProgramme mit den besten Methoden).
- Turbinenschaufeln sind während der Bearbeitung vibrationsanfällig (lange, schmale, dünne Teile erfordern leichtschneidende Werkzeuge und Dämpfungsvorrichtungen).
- Eine effiziente Produktion ist wichtig (es werden große Mengen gefertigt).
- Es müssen mehrere verschiedene Werkzeuge eingesetzt und richtig angewendet werden (von unkompliziertem Planfräsen bis hin zu 4- bis 5-achsigem Profilfräsen).
Gut ausgearbeitete Bearbeitungsstrategien und kontinuierliche Verbesserungen sind ausschlaggebend für Produktivität und nachfolgende Prozesse. Nur durch innovative Werkzeuge und deren kompetente Anwendung können die Herausforderungen, insbesondere bei rotierendenTurbinenschaufeln, gemeistert werden.
Vor allem bei mittelgroßen Turbinenschaufeln steht das Schruppen von Rhombus und Schaufel, um den Rohlingen die grobe Schaufelform zu verleihen, häufigim Mittelpunkt. Dies ist der Hauptteil der Bearbeitung. Viele Schaufeln sind aus martensitischem Edelstahl, aber sie werden auch aus Duplex, HRSA und Titan gefertigt. Für diese Operation gab es im Laufe der Jahre viele verschiedene Lösungen, aber die Haupttendenz geht zu Fräsern mit runden Wendeplatten und Kugelschaftfräsern, da sie Profile mit einer sicheren und starken Schneidkante erzeugen können und eine gute Freigängigkeit vom Fräser zum Bauteil bieten.
Beim Einsatz eines Fräsers zum Schruppen des Rhombus ist ein großer
Eingriff des Fräsers in das Bauteil wichtig; 60 bis 80% sind das Ziel. Dies muss durch die Kombination des am besten geeigneten Fräserdurchmessers mit dem optimalen Werkzeugweg erreicht werden. Außerdem sollte für verbesserte Leistung, Sicherheit und Ergebnisse das optimale Gleichgewicht zwischen Vorschub, Schnitttiefe,Wendeplattengröße, -geometrie und-sorte, Anstellwinkel der Wendeplattesowie den entstehenden Schnittkräften
hergestellt werden.
Das Schruppen der Wurzeln der Turbinenschaufel, insbesondere der Übergang zwischen Kopf und Fuß (Nabe und Deckband), ist eine wichtiger Vorgang, bei dem viel Material betroffen ist. Der Rundplattenfräser des Rhombus ist aufgrund der vorhandenen Ecken hierfür jedoch nichtgeeignet. Um hohe Effizienz zu erreichen ist hier eine Speziallösung erforderlich.
Auch das Vorschlichten und Schlichten der Turbinenschaufel erfordern optimales Werkzeug und die besten Methoden,
um bei hoher Effizienz gute Qualität zu erzielen. Ein ergänzender Rundplattenfräser, Vollhartmetallfräser und ein moderner, geeigneter Planfräser sowie fortschrittliche Methoden entsprechend Schaufelgröße sowie Maschinen- und Programmmöglichkeiten vervollständigen die Maschineneinrichtung.
Rhombus-Schruppen
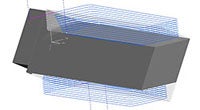
Eine häufig verwendete Methode zum Schruppen des Rhombus ist ein gerader Eintritt des Fräsers in das Werkstück. Diese Methode verbessert Standzeit und Produktivität jedoch nicht. Wir empfehlen das Einrollen bei Fräsrichtung im Gleichlauf und einen konstanten Eingriff des Fräsers. So wird die Vorschubgeschwindigkeit gesteigert und eine hohe Standzeit ermöglicht.
Der CoroMill 600 ist der ideale Fräser für Ihre Profilschrupp-und Vorschlichtbearbeitungen. Verbesserte Ausführung des Fräserkörpers, spezielle Sorten und Geometrie und das patentierte iLock™ System machen ihn optimal für die Bearbeitung von Schaufel und Rhombus.
Neues Fräskonzept für
Turbinenschaufeln
Schaufel
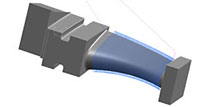
Komplizierte Oberflächengeometrien maximieren die Effizienz von modernen Turbinenschaufeln. Daher erfordert die Bearbeitung dieser Oberflächen eine
sorgfältige Bearbeitungsstrategie.
Sandvik Coromant bietet Know-how und hochwertige Fräser zum Schruppen, Vorschlichten und Schlichten der Schaufel, wie CoroMill 600, CoroMill 300,
CoroMill 316 und CoroMill Plura.
Schaufelbearbeitung
Deckband und Nabe
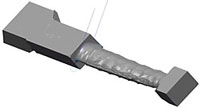
Das Schruppen der Übergangsradien zwischen Kopf/Fuß und Schaufel war immer ein anspruchsvoller und zeitaufwändiger Vorgang mit mehreren Spezialwerkzeugen.
Der konische Kugelschaftfräser mit Wendeschneidplatten (Tailor-Made-Lösung) verbindet das Beste der CoroMill Technologie mit einer speziellen Fräserlösung und sorgt so für eine fertig geformte Oberfläche für Schlichtbearbeitungen. Setzen Sie zum Schlichten CoroMill Plura Fräser ein – die Produktivitätssteigerungen sind beträchtlich.
Deckband und Nabe der Turbinenschaufel
Kopf und Fuß
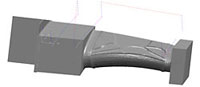
Beim Planfräsen von Kopf und Fuß sollte der Eintritt in das Werkstück durch Einrollen des Werkzeugs erfolgen. Durch eine außermittige Positionierung des Fräsers entstehen beim Austritt besonders dünne Späne. Dies führt zu geringeren Vibrationen und
ermöglicht höhere Vorschubgeschwindigkeiten.
Der CoroMill 490 ist eine neue, hochmoderne Fräslösung mit einer einmaligen Ausführung, die auf einem großen, axialen Spanwinkel zusammen mit einer positiven,
scharfen Schneidkante basiert. Dieses Fräserkonzept sorgt für erstklassige Oberflächengüte von Kopf und Fuß.
Aufnahmenut
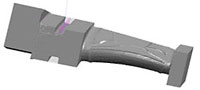
Die Bearbeitungsstrategie hängt von der Größe der Turbinenschaufel und der Position der Aufnahmenut ab. Ein Hochvorschubfräser ist zum Öffnen einer Nut oft eine gute Methode.
Die erste Wahl zum Schruppen der Nut ist der CoroMill 316 Hochvorschubfräser mit schrägem Werkzeugweg. Der CoroMill Plura bietet eine vielseitige Lösung zum Nutschlichten, wobei die Schneidkantenlänge die verschiedenen Tiefen der Nut abdeckt.
Neues Fräskonzept für
Turbinenschaufeln
Der CoroMill 600 ist ein moderner, innovativer Fräser – eine völlig neue Ausführung, die auf einer einzigartigen, hochmodernen Werkzeugplattform basiert. Dieser zum Schruppen und Vorschlichten von Turbinenschaufeln entwickelte Rundplattenfräser ermöglicht einen völlig neuen Ansatz für die anspruchsvolle Fertigung von Turbinenschaufeln.
Das neue Konzept umfasst fünf neue Elemente:
- Plattensitzschnittstelle; dieser Faktor hat in letzter Zeit an Bedeutung gewonnen, da die Schnittstelle die möglichen Optionen beeinflusst. Für Wendeschneidplatten wurde das iLock-Konzept eingeführt, um die akkurate Positionierung der Wendeplatte in Werkzeughalter/Fräserkörper zu gewährleisten. Der Bediener kann die Wendeschneidplatte beim Indexieren oder Auswechseln leichter in Position drehen. Die sorgfältig entwickelte Ausführung genau übereinstimmender Profile und Nuten mit optimalen Formen und Größen hat Stabilität, Genauigkeit und Sicherheit der Schneidkante sowie die Handhabung der Werkzeuge deutlich verbessert. Infolgedessen sind die Wendeschneidplatten des CoroMill 600 Fräsers nicht mehr auf seitliche Halterungen am Plattensitz zur Indexierung/Befestigung angewiesen. So können wir Wendeschneidplatten mit völlig neuen, verbesserten Geometrien anbieten, die zuvor nicht in Betracht kamen. In Bezug auf Schneidwirkung, Schneidengeometrien, Vorschuboptimierung usw. sind nun neue Visionen möglich.
- Der Fräserkörper des CoroMill 600 ist mit seinem gänzlich neuen Design für das Fräsen von Wölbungen, wie beim 4- und 5-achsigen Fräsen von Turbinenschaufeln, optimiert. Form und Freigängigkeit des Fräserkörpers ermöglichen optimierte Werkzeugwege, größere Bearbeitungssicherheit und verbesserte Spanabfuhr. Eine Differentialteilung minimiert Vibrationen.
- Für den CoroMill 600 werden neue Wendeplattengeometrien für leichtschneidende bis mittelschwere Bearbeitungen entwickelt. Die Wendeschneidplatten werden nach dem neuesten Herstellungsprozess gepresst. Leichtschneidende Wendeplatten weisen häufig eine bessere Leistung auf als geschliffene Wendeplatten mit ähnlicher Geometrie. Diese Wendeschneidplatten haben eine scharfe, positive, aber stabile Schneidkante mit optimierter Mikrogeometrie für zahlreiche Werkstoffe für Turbinenschaufeln.
- Für die CoroMill 600 Werkzeuge wurde eine neue Wendeplattensorte entwickelt. Diese völlig neue CVD-beschichtete Sorte, speziell entwickelt und optimiert für das Fräsen von Turbinenschaufeln, ermöglicht die Verbesserung der Leistung bei Turbinenschaufeln aus martensitischem rostfreien Stahl. Die Sorte ist eine neue Kombination aus Schneidplattensubstrat, Beschichtung und Herstellungsprozess. Außerdem haben sich für andere Turbinenschaufelwerkstoffe moderne CVD- und PVD-beschichtete Wendeplattensortenbewährt.
- Hochdruck-Kühlung, Luftzufuhr bzw. minimale Schmiervorrichtungen sind Teil des CoroMill 600 Fräsers. Jeder Plattensitz verfügt mit einer optionalen Düse für bessere Spanbildung über das Standard-HD-Konzept. So entsteht für anspruchsvollereWerkstoffe ein hydraulischer Keil aus Kühlschmierstoff oder Druckluft zur Verbesserung von Spanablauf und -abfuhr – ein Hauptfaktor beim Fräsen von Turbinenschaufeln mit relativ geringen Schnittgeschwindigkeiten.Zurück
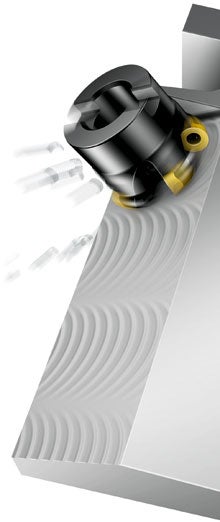
Schruppen
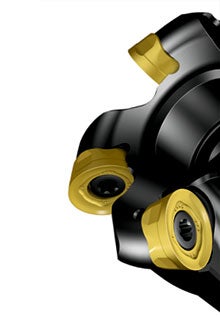
Einzigartige Plattensitz-
Technologie
Schaufelbearbeitung
Beinhaltet die Wahl der Werkzeuge zum Vorschlichten und Schlichten der Kontur der Turbinenschaufel. Diese ist abhängig von der Größe der Turbinenschaufel, der Maschine und der Methode. Für optimale Resultate muss die Werkzeugwahl auf die Materialmenge und die bearbeitete Oberfläche abgestimmt werden. Der CoroMill 300 Rundplattenfräser ist ein hervorragender Profilfräser für die fünfachsige Bearbeitung mit guter Freigängigkeit, Leichtschnitteigenschaften und einer großen Bandbreite zum Vorschlichten. Eine Version mit besonders enger Teilung ist fürs Vorschlichten mit hohem Vorschub ohne bzw. mit nur minimalen Vibrationen geeignet. Für optimale Leistung können 12 und 8 mm IC-Wendeplatten mit unterschiedlichen Geometrien, Durchmessern und Teilung gewähltwerden.
Vorschlichten und Schlichten der Schaufel erfolgen mit CoroMill Plura Vollhartmetallfräsern oder mit dem CoroMill 316 mit Wechselköpfen. Der Vorschlichtvorgang beeinflusst die beim abschließenden Schlichtvorgang erzielte Oberflächengüte. Das Ziel sollte ein äußerst gleichmäßiges Aufmaß sein. Eventuell sind dazu zwei Vorschlichtvorgänge erforderlich. Vibrationen sind ein weiterer Faktor für die Qualität des Ergebnisses und können durch Fräsereingriff, Vorschub, Ansatz und Schneidwirkung des eingesetzten Werkzeugs beeinflusst werden.
Das CoroMill Plura Programm ist eine fortschrittliche Entwicklung von Vollhartmetallfräsern mit zeitgemäßen Schneidstoffen für sämtliche Werkstoffe. Bei der Entwicklung der Geometrien wurden die Anforderungen für Fräsarbeiten in heutigen Maschinen berücksichtigt. Die Spankanaltiefe wurde modifiziert und mit maximaler Steifigkeit des Kerns und ausreichend Raum für eine effiziente Spanabfuhr für die Bearbeitung von Turbinenschaufeln optimiert. Bei Fräsarbeiten dominierten bisher vorwiegend zwei, sich in ihren Anwendungsbereichen teilweise überschneidende Werkzeugtypen: Wendeschneidplattenfräser und Vollhartmetallfräser. Die Anwendungsbereiche unterschieden sich in erster Linie durch Werkzeugdurchmesser, Art der Operation und geforderter Werkstückoberfläche. Wendeschneidplattenfräser haben keine Obergrenze für den Durchmesser, aber – praxisbedingt – eine Untergrenze von meist 12 oder 16 mm. Vollhartmetallfräser hingegen können Durchmesser von Zehntelmillimetern haben, aber haben in der Regel eine ökonomische Durchmesser-Obergrenze von ungefähr 25 mm.
Wendeschneidplattenfräser sind in Bezug auf Operation und Oberfläche flexibleWerkzeuge mit hohen Zerspanungsraten und eignen sich gut für die meisten Anwendungen, während Vollhartmetallfräser enge Werkzeugtoleranzen haben und hohe Oberflächengüte und äußerste Genauigkeit bieten, insbesondere bei großen axialen Schnitttiefen, dank langer radialer Schneidkanten.
Ein Vollhartmetallwerkzeug ist ein komplettes Präzisionswerkzeug; in einem Stück vom Schaft bis zur Schneidkante. Ein Wendeschneidplattenwerkzeug hingegen besteht aus zwei Werkzeugelementen, was mehr Variations- und Optimierungsmöglichkeiten bietet. Neben den Wendeschneidplatten- und Vollhartmetallwerkzeugen gibt es eine alternative Werkzeuglösung, die sich mit beiden überschneidet. Eine Lösung, die Indexierbarkeit der Schneidkante und die Vorteile von Vollhartmetallwerkzeugen für kleine bis mittlere Fräserdurchmesser vereint.
Das CoroMill 316 Frässystem mit auswechselbaren Schneidköpfen nutzt die hochentwickelten Plura Vollhartmetallschneidkanten zusammen mit einer fortschrittlichen Kupplungen zwischen Schneidkopf und Werkzeugschaft. Mit dem umfangreichen Programm an Vollhartmetall-Schneidköpfen kann es für viele Anwendungen eingesetzt werden. Das CoroMill 316 Frässsystem verfügt über eine ausgewogene Konstruktion und ist daher für relativ hohe Spindeldrehzahlen geeignet. Es vereint zwei Vorteile: rentable Werkzeugkosten und effiziente Werkzeugorganisation. Die Möglichkeit, zwischen Hochvorschub- und Vielzahnschneidköpfen zu wählen ermöglicht hohe Vorschubgeschwindigkeit und somit eine gesteigerte Produktivität. Das Wechselkopf-Konzept erleichtert außerdem die Anpassung der Schneidengeometrie an verschiedene Werkstoffe und Bedingungen. Die Ausführung der Schneidköpfe bietet gute Bearbeitungsstabilität und minimale Werkzeugablenkung durch Spiral- und Differentialteilung.
Zurück
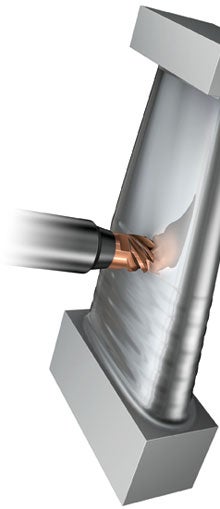
Innovative Kupplung
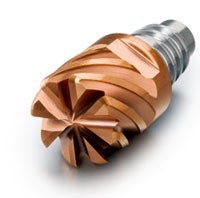
Deckband und Nabe der Turbinenschaufel
Oberflächen an den Übergangsradien zwischen Fuß und Kopf der Turbinenschaufel werden in der Regel als unabhängiger Prozess mit speziellen Werkzeugen angesehen. Die beim Schruppen notwendige Restmaterialbearbeitung ist anspruchsvoll und erfordert einen Fräser mit hoher Zerspanungsrate bei seitlichem und punktuellem Eingriff.
Ein konischer Fräser ist ideal und CoroMill – je nach Größe der Turbinenschaufel entweder in Form eines Wendeschneidplattenfräsers oder eines Vollhartmetallfräsers. Hier ist CoroMill Plura eine gute Wahl. Zur Verbesserung der Produktivität dieses Vorgangs, bei dem viel Werkstoff zerspant werden muss, ist ein geeigneter Wendeschneidplattenfräser in der Regel die beste Lösung. Ein Kugelschaftfräser und ein Walzenstirnfräser bieten sich für nachfolgende Operationen an – dabei sind CoroMill 216 und CoroMill 390 die beste Wahl.
Jedoch wartete dieser Vorgang noch auf eine spezielle Fräserlösung. Und die wurde mit einem speziellen, konischen Kugelschaftfräsers, der das Beste der CoroMill-Technologie in sich vereint, geliefert. Dieses Werkzeug ermöglicht das Schruppfräsen der Ausrundungen von Deckband und Nabe nach dem Schruppen des Rhombus und vor den Schlichtarbeiten. In einem Vorgang – oder zumindest in weniger Durchgängen als bei bisherigen Lösungen – wird der Übergangsbereich für eine Vorschlichtbearbeitung geformt. Dieser Fräser kann mit bewährten Standardwendeplatten für zahlreiche Turbinenschaufelgrößen angepasst werden. Dieses hochmoderne Spezialwerkzeug bietet eine neue Lösung für eine anspruchsvolle, oft zeitaufwändige Bearbeitung und verbessert die Produktivität erheblich.
Zurück
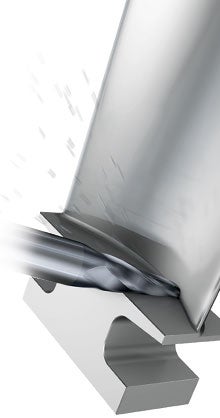
Neue Entwicklungen zum
Schruppen und Schlichten mit
konischen Kugelschaftfräsern
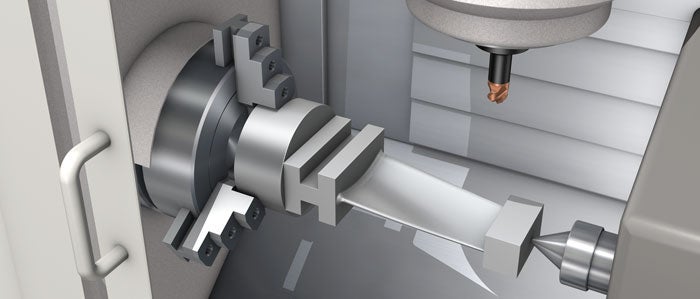