Jak při soustružení dosáhnout dobré kvality obrobených součástí
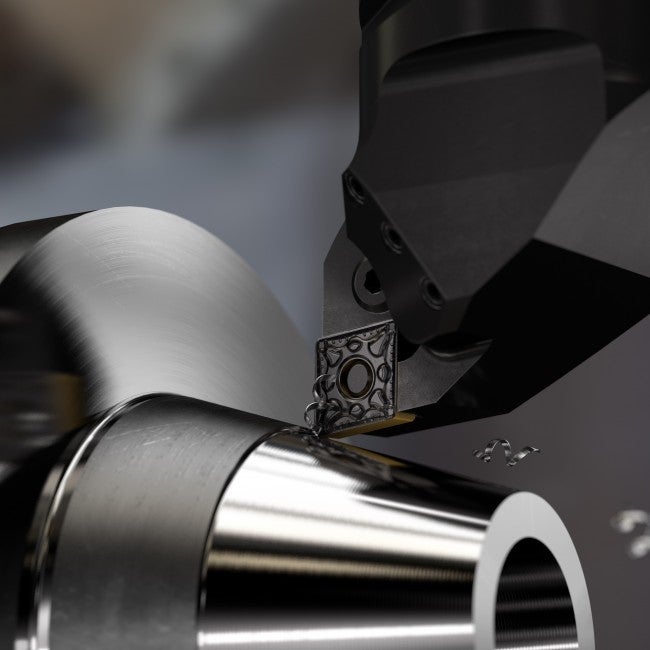
Jedním z nejdůležitějších faktorů, kterými je třeba se zabývat, jestliže chcete dosáhnout dobré kvality soustružených součástí, je kontrola utváření třísek. Chcete-li dosáhnout dobré kvality obráběné součásti, zvolte vhodné hodnoty řezných parametrů a řiďte se našimi praktickými radami.
Úspěšná kontrola utváření třísek
Kontrola utváření třísky je při soustružení jedním z nejdůležitějších faktorů, přičemž existují tři hlavní způsoby dělení třísky:
- Samovolné dělení třísky (např. u šedé litiny)
- Dělení třísky o nástroj
- Dělení třísky o obrobek
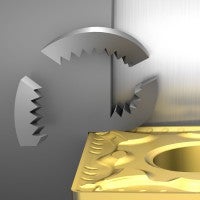
Samovolné dělení
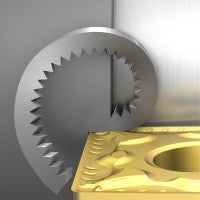
Dělení třísky o nástroj
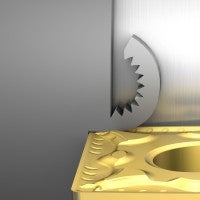
Dělení třísky o obrobek
Faktory ovlivňující dělení třísek
- Geometrie břitové destičky: V závislosti na vzdálenosti utvářeče třísek od ostří a tvaru mikro- a makrogeometrie mohou třísky volně odcházet, nebo dochází k jejich větší deformaci
- Poloměr zaoblení špičky: Menší poloměr špičky umožňuje lepší kontrolu třísky než větší poloměr špičky
- Úhel nastavení (úhel hlavního břitu): V závislosti na velikosti tohoto úhlu jsou třísky nasměrovány různým směrem - směrem do rohu nebo směrem z rohu ven
- Hloubka řezu: Protože zvětšení hloubky řezu vede ke zvýšení sil umožňujících dělení a odvádění třísek, v závislosti na obráběném materiálu ovlivňuje dělení třísky
- Posuv: Při vyšším posuvu vznikají obecně pevnější třísky. V některých případech může pomoci zlepšit kontrolu a dělení třísek
- Řezná rychlost: Změnou řezné rychlosti lze ovlivnit schopnost dělení třísky
- Materiál: Snadno obrobitelné jsou obecně materiály tvořící krátké třísky (např. šedá litina). V případě materiálů s vynikající mechanickou pevností a odolností proti creepu
(sklon pevných látek se pod mechanickým napětím pomalu deformovat a měnit tvar, např. slitiny Inconel) má dělení třísek mnohem větší význam
Řezné podmínky pro soustružení
Při volbě vhodné řezné rychlosti a rychlosti posuvu pro soustružení vždy vezměte v úvahu stroj, nástroj, břitové destičky a obráběný materiál.
- Má-li být zajištěna bezpečnost břitové destičky a drsnost obrobené plochy, začněte s nízkou rychlostí posuvu a následně ji zvyšujte, aby se zlepšilo dělení třísek
- Používejte hloubky řezu větší, než je poloměr zaoblení špičky. Minimalizuje se tak radiální vychýlení břitové destičky, což je velice důležité při obrábění vnitřních ploch
- Použití příliš nízké řezné rychlosti má za následek nedostatečnou životnost nástroje. Vždy dodržujte doporučenou řeznou rychlost, vc m/min (ft/min)
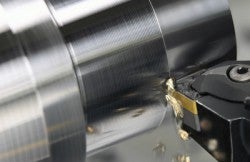
Kvalitu soustružených součástí zlepšíte použitím řezné kapaliny
Správné použití řezné kapaliny zvyšuje bezpečnost obráběcího procesu a zlepšuje funkci a výkonnost nástroje a kvalitu obráběné součásti. Při použití řezné kapaliny mějte na paměti:
- Pro dokončovací aplikace je důrazně doporučeno použití nástrojů s přesným přívodem řezné kapaliny
- Tlak řezné kapaliny potřebný pro dělení třísek závisí na průměru trysky (výstupním), obráběném materiálu, hloubce řezu a posuvu
- Požadovaný průtok řezné kapaliny závisí na tlaku a celkovém průřezu kanálků pro přívod řezné kapaliny
- Pro střední obrábění a hrubovací aplikace je doporučeno použití přívodu řezné kapaliny ze spodní strany
- Pro dokončovací operace je doporučeno použít jak přesný přívod řezné kapaliny, tak i přívod řezné kapaliny ze spodní strany
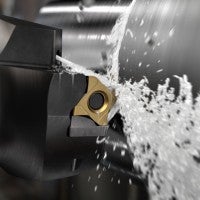
Řešení problémů s pomocí správně využívaného přívodu řezné kapaliny
- Problémy s kontrolou utváření třísek: Použijte přívod řezné kapaliny z horní strany
- Problémy s dodržením rozměrových tolerancí: Obvykle způsobované vysokými teplotami – použijte přívod z horní i ze spodní strany a současně co nejvyšší tlak řezné kapaliny
- Špatná kvalita obrobené plochy: Jsou-li zjištěny defekty způsobované třískami, použijte přívod řezné kapaliny z horní strany
- Nepředvídatelná životnost nástroje při provádění hrubovacích operací: Použijte pouze přívod řezné kapaliny ze spodní strany
- Nepředvídatelná životnost nástroje při provádění dokončovacích operací: Použijte přívod řezné kapaliny z horní i ze spodní strany
- Špatné odvádění třísek při obrábění vnitřních ploch: Použijte přívod z horní i ze spodní strany a co nejvyšší tlak řezné kapaliny
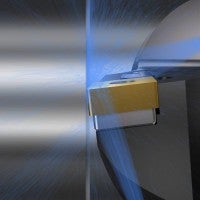
Použití řezné kapaliny a chlazení při soustružení
Dosažení dobré kvality obrobeného povrchu soustružených součástí
Všeobecná pravidla pro kvalitu obrobené plochy:
- Kvalitu obrobeného povrchu lze často zlepšit použitím vyšší řezné rychlosti
- Drsnost obrobené plochy ovlivňuje geometrie břitové destičky (neutrální, pozitivní nebo negativní úhel čela a také pozitivní úhel hřbetu)
- Volba třídy břitové destičky do jisté míry ovlivňuje drsnost obrobené plochy
- V případě, že se projevují sklony ke vzniku vibrací, zvolte menší poloměr zaoblení špičky
Hladící břitové destičky
Hladící břitové destičky (Wiper) umožňují soustružení součástí při vysokých rychlostech posuvu, aniž by docházelo ke ztrátě jejich schopnosti dosahovat dobré kvality obrobeného povrchu nebo schopnosti dělit třísky.
Všeobecným pravidlem je: Dvojnásobná rychlost posuvu – stejná kvalita obrobené plochy. Stejná rychlost posuvu – dvojnásobně lepší kvalita obrobené plochy.
Hladící břitové destičky byly navrženy tak, aby při pohybu břitové destičky podél obrobku docházelo k vyhlazení obráběného povrchu, přičemž jejich konstrukce je taková, že se hladící efekt uplatňuje hlavně při přímočarém a čelním soustružení.
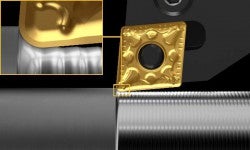
Standardní poloměr špičky
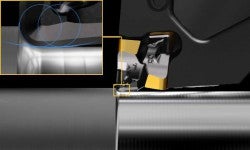
Poloměr špičky s hladící úpravou
Srovnání standardních a hladících břitových destiček v závislosti na rychlosti posuvu
Poznámka! Všechny hodnoty pro standardní poloměr zaoblení špičky jsou stanovené teoretickým výpočtem. Hodnoty pro hladící poloměr špičky vycházejí z experimentálních hodnot zjištěných pro nízkolegovanou ocel.
Posuv mm (inch) | Standardní RE 0.4 mm (0.016 inch) Ra µm (µinch) | Wiper (-WF/-WM) RE 0.4mm (0.016 inch) Ra µm (µinch) | Standardní RE 0.8 mm (0.031 inch) Ra µm (µinch) | Wiper (-WMX) RE 0.8 mm (0.031 inch) Ra µm (µinch) |
0.07 (0.003) | 0.31 (12.4) | 0.30 (12.0) | - | - |
0.10 (0.004) | 0.63 (25.2) | 0.32 (12.8) | 0.31 (12.4) | - |
0,12 (0,005) | 0.90 (36.0) | 0.45 (18.0) | 0.45 (18.0) | - |
0,15 (0,006) | 1.41 (56.4) | 0.70 (28.0) | 0.70 (28.0) | 0.25 (10.0) |
0.18 (0.007) | 2.03 (80.8) | 1.00 (40.0) | 1.00 (40.4) | 0.30 (12.0) |
0.20 (0.008) | 2.50 (100.0) | 1.25 (50.0) | 1.25 (50.0) | 0.35 (14.0) |
0.22 (0.009) | 3.48 (139.2) | 1.74 (69.6) | 1.74 (69.6) | 0.40 (16.0) |
0.25 (0.010) | - | - | 2.25 (90.0) | 0.45 (18.0) |
0.28 (0.011) | - | - | 2.82 (112.8) | 0.50 (20.0) |
0.30 (0.012) | - | - | 3.23 (129.2) | 0.55 (22.0) |
0.35 (0.014) | - | - | 4.40 (176.0) | 0.60 (24.0) |
0.40 (0.016) | - | - | 5.75 (230.0) | 0.70 (28.0) |
0.45 (0.018) | - | - | 8.54 (341.6) | 1.1 (44.0) |
0.50 (0.020) | - | - | 10.55 (422.0) | 1.3 (51.0) |
Posuv mm (inch) | Standardní RE 1.2 mm (0.047 inch) Ra µm (µinch) | Wiper (-WMX) RE 1.2mm (0.047 inch) Ra µm (µinch) | Standardní RE 1.6 mm (0.063 inch) Ra µm (µinch) | Wiper (-WMX) RE 1.6 mm 1) (0.063 inch) Ra µm (µinch) |
0.15 (0.006) | 0.47 (18.8) | - | - | - |
0.18 (0.007) | 0.68 (27.2) | - | - | - |
0.20 (0.008) | 0.83 (33.3) | 0.3 (12.0) | 0.63 (25.2) | - |
0.22 (0.009) | 1.16 (46.4) | 0.3 (12.0) | 0.87 (34.8) | - |
0.25 (0.010) | 1.50 (60.0) | 0.4 (16.0) | 1.12 (44.8) | 0.3 (12.0) |
0.28 (0.011) | 1.88 (75.2) | 0.4 (16.0) | 1.41 (56.4) | 0.35 (14.0) |
0.30 (0.012) | 2.16 (86.4) | 0.4 (16.0) | 1.62 (64.8) | 0.4 (16.0) |
0.35 (0.014) | 2.93 (117.2) | 0.5 (20.0) | 2.20 (88.0) | 0.4 (16.0) |
0.40 (0.016) | 3.83 (153.2) | 0.65 (26.0) | 2.88 (115.2) | 0.4 (16.0) |
0.45 (0.018) | 5.70 (228.0) | 0.85 (34.0) | 4.27 (170.8) | 0.5 (20.0) |
0.50 (0.020) | 7.03 (281.2) | 1.15 (46.0) | 5.27 (210.8) | 0.7 (28.0) |
0.55 (0.022) | 8.51 (340.4) | 1.2 (48.0) | 6.38 (255.2) | 0.9 (36.0) |
0.60 (0.024) | 10.13 (405.2) | 1.3 (52.0) | 7.59 (303.6) | 1.05 (42.0) |
0.65 (0.026) | - | - | 8.91 (356.4) | 1.25 (50.0) |
0.70 (0.028) | - | - | 10.31 (413.6) | 1.3 (52.0) |
0.85 (0.033) | - | - | 15.24 (609.6) | 1.9 (76.0) |
0.90 (0.035) | - | - | 17.09 (683.0) | 2.1 (84.0) |
- Hodnoty pro poloměr špičky 1,6 mm (0.06 inch) byly stanoveny pro břitové destičky DNMX
Praktické rady pro soustružení vnějších ploch
Součásti náchylné ke vzniku vibrací
Použijte obrábění na jeden průchod (např. u trubky)
Aby působící síla zůstala orientovaná v axiálním směru proti sklíčidlu/vřetenu, je při obrábění doporučeno odebrat celý přídavek na jeden průchod.
Příklad:
Vnější průměr (OD) 25 mm (0.984 inch)
Vnitřní průměr (ID) 15 mm (0.590 inch)
Hloubka řezu, ap = 4.3 mm (0.169 inch)
Výsledná tloušťka stěny = 0.7 mm (0.028 inch)
OD = 25 mm (0.984 inch) | ap 4.3 mm (0.169 inch) |
![]() | ID = 15 mm (0.590 inch) |
Pro dosažení orientace řezných sil v axiálním směru lze využít úhel nastavení blízký 90° (úhel hlavního břitu 0°). To vede ke snížení ohybových sil působících na součást na minimum.
Obrábění na dva průchody
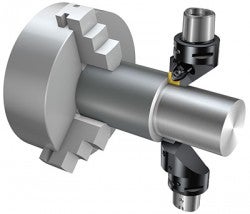
Synchronizované obrábění s využitím horní a spodní revolverové hlavy vyrovnává radiální řezné síly a brání tak vzniku vibrací a průhybu součásti.
Štíhlé/tenkostěnné součásti
Při soustružení štíhlých/tenkostěnných součástí je třeba vzít v úvahu následující skutečnosti:
- Použijte úhel nastavení blízký 90° (úhel hlavního břitu 0°). Dokonce i malá změna (z úhlu 91/-1 na 95/-5 stupňů) má vliv na orientaci řezných sil v průběhu obrábění
- Hloubka řezu,ap, by měla být větší než je poloměr špičky, RE. Při velkých hodnotách ap dochází ke zvýšení axiální řezné síly, Fz, a snížení radiální řezné síly, Fx, která způsobuje vznik vibrací
- Použijte břitové destičky s ostrou řeznou hranou a malým poloměrem zaoblení špičky RE, díky kterým se snižují vznikající řezné síly
- Zvažte použití cermetové nebo PVD nástrojové třídy, která nabízí odolnost proti otěru a ostrý břit, což je pro tento typ operací výhodnější
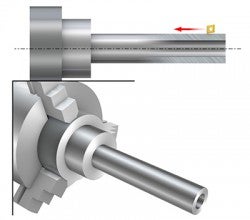
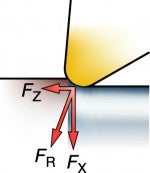
Soustružení osazených ploch/soustružení do rohu
Abyste předešli poškození ostří břitové destičky, postupujte podle kroků 1–5. Tato metoda je velice vhodná pro břitové destičky s CVD povlakem a může výrazně omezit výskyt lomů.
Krok 1–4:
Aby nedocházelo k zasekávání třísek, měla by být vzdálenost mezi jednotlivými kroky (1–4) stejná jako velikost posuvu.
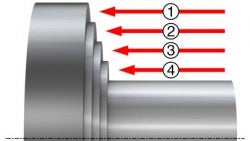
Krok 5:
Poslední řez proveďte jedním vertikálním řezem, který začíná na vnějším průměru a pokračuje směrem k nejmenšímu průměru.
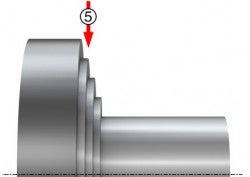
Jestliže při soustružení čelní plochy osazení probíhá obrábění směrem od vnitřního průměru k vnějšímu, může rovněž docházet k problémům s namotáváním třísek při obrábění přechodového poloměru. Otočit směr odcházení třísek a vyřešit tento problém může změna dráhy nástroje.
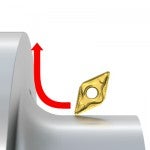
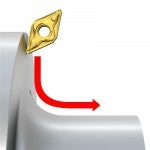
Soustružení čelních ploch
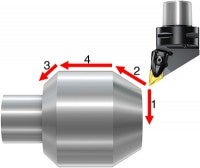
Začněte soustružením čelních ploch (1) a zkosení (2). Pokud je to možné a jestliže to geometrický tvar obrobku umožňuje, pokračujte obrobením zkosení (3). Poslední operací je podélný řez (4), přičemž vstup břitové destičky do záběru a její výstup ze záběru probíhá klidně a plynule.
První operací musí být soustružení čelních ploch, protože se tak na součásti stanoví vztažný bod pro další průchod.
Častým problémem na konci řezu (při výstupu z obrobku) je tvorba otřepů. Minimalizovat nebo zabránit vzniku otřepů lze ponecháním zkosení nebo zaoblení rohu (nájezd do rohu narolováním do řezu).
Zkosení hran na součásti umožňuje hladší a plynulejší vstup ostří břitové destičky do záběru (při soustružení čelních ploch i při podélném soustružení).
Přerušované řezy

Při obrábění s přerušovaným řezem:
- U aplikací s rychle přerušovaným řezem, např. v případě šestihranných tyčí, použijte pro zajištění houževnatosti řezné hrany PVD nástrojovou třídu
- Pro aplikace na velkých součástech a v případě těžkých přerušovaných řezů použijte pro zajištění houževnatosti v celém objemu houževnatou CVD nástrojovou třídu
- S ohledem na dostatečné zvýšení odolnosti proti vylamování ostří je vhodné zvážit použití odolnějšího lamače třísek
- Aby se předešlo vzniku tepelných trhlin, je vhodné zastavit přívod řezné kapaliny
Dokončování součásti s podsoustružením (oddělovacím zápichem)
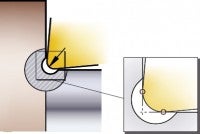
Použití největšího možného poloměru zaoblení špičky RE při podélném a čelním soustružení přináší:
- Zvýšení pevnosti břitu, bezpečnosti a spolehlivosti
- Dobrou kvalitu obrobené plochy
- Možnost použití vysokých rychlostí posuvu
Nepřekračujte šířku podsoustružení a aby došlo k odstranění otřepů, provádějte podsoustružení jako poslední operaci.
Praktické rady pro soustružení vnitřních ploch
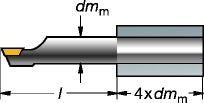
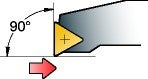
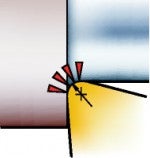
- Zvolte největší možný průměr tyče, ale zároveň se ujistěte, že mezi tyčí a stěnou díry zbývá dostatečný prostor pro odvádění třísek
- Ujistěte se, že odvádění třísek je adekvátní použitým řezným podmínkám a že vznikají třísky vhodného typu
- Zvolte nejkratší možné vyložení nástroje, ale zároveň se ujistěte, že délka vyvrtávací tyče umožňuje dodržení doporučené délky upnutí. Délka upnutí by nikdy neměla být kratší než trojnásobek průměru tyče
- Pro výrobu součástí náchylných ke vzniku vibrací použijte tlumené vyvrtávací tyče
- Aby řezné síly směřovaly podél vyvrtávací tyče, zvolte úhel nastavení tak blízký 90° (úhel hlavního břitu 0°), jak jen je to možné. Úhel nastavení by nikdy neměl být menší než 75° (úhel hlavního břitu -15°)
- Hlavní prioritou je, aby vyměnitelná břitová destička měla pozitivní základní tvar a pozitivní geometrii, aby se minimalizoval průhyb nástroje
- Zvolte poloměr špičky břitové destičky, který je menší než je hloubka řezu
- Nedostatečný záběr břitu může vést ke zvýšení sklonů ke vzniku vibrací, ke kterým dochází v důsledku tření v průběhu řezu. S ohledem na správný průběh řezu zvolte délku záběru břitu větší než je poloměr zaoblení špičky
- Příliš velký záběr břitu (velká hloubka řezu a/nebo velká rychlost posuvu) může mít za následek vibrace vznikající v důsledku průhybu nástroje
- Ve srovnání s břitovými destičkami se silnou povlakovou vrstvou obvykle vznikají při použití břitových destiček s tenkým povlakem nebo nepovlakovaných břitových destiček menší řezné síly. To je důležité zejména v případech, kdy poměr mezi délkou a průměrem je vysoký. Díky snížení sklonů ke vzniku vibrací na minimum přináší obvykle použití ostrých břitů zlepšení kvality díry
- Pro soustružení vnitřních ploch může být často vhodnější geometrie s otevřeným lamačem třísek
- U některých operací lze zvážit použití houževnatější třídy břitových destiček, protože je schopna lépe čelit riziku zasekávání třísek nebo sklonům ke vzniku vibrací
- Pokud je nutné zlepšit utváření třísek, zvažte alternativní dráhu nástroje
Praktické rady pro soustružení tvrzených součástí
Vedle obecných doporučení pro soustružení existují ještě další důležité faktory, které je při soustružení tvrzených součástí třeba uvážit (jestliže výrobní proces zahrnuje také vlastní přípravu součásti před jejím vytvrzením):
- Zamezte tvorbě otřepů
- Dodržujte úzké rozměrové tolerance
- V měkkém stavu proveďte zkosení hran a obrobte poloměry
- Nezahajujte ani neukončujte řez náhle
- Pro vstup a výstup do a ze záběru použijte techniku rolování
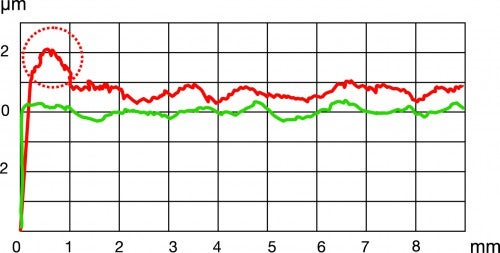
Měření drsnosti povrchu
Osa X: Měřená délka
Osa Y: Odchylka od průměru
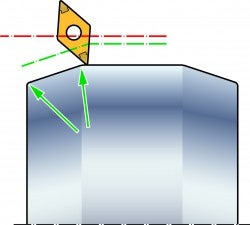
Hodnocený povrch
Seřízení
- Velice důležitá je dobrá stabilita obráběcího stroje a upnutí a vyrovnání obrobku
- Všeobecně dodržovaným pravidlem je, že v případě podepření obrobku pouze na jednom konci je doporučený poměr délky vůči průměru 2 : 1. Jestliže je obrobek podepřen také koníkem, tento poměr je možné zvýšit
- Mějte na paměti, že k dalšímu zvýšení rozměrové stability přispívá tepelně symetrická konstrukce vřeteníku a koníku
- Použijte systém Coromant Capto®
- Abyste dosáhli maximální tuhosti systému, minimalizujte všechna vyložení
- Zvažte použití vyvrtávacích tyčí s karbidovou stopkou nebo tlumených nástrojů Silent Tools pro vnitřní soustružení
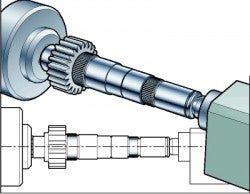
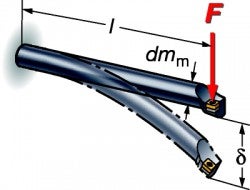
Mikrogeometrie břitové destičky
Dvě charakteristické úpravy řezné hrany, s nimiž se lze setkat u CBN břitových destiček, jsou úprava typu S a typu T.
- Typ S: Nejvyšší pevnost řezné hrany. Odolnost proti vylamování mikročástic z břitu a zaručená konzistentní kvalita obrobeného povrchu.
- Typ T: Nejvyšší kvalita povrchu při provádění spojitých řezů a minimální tvorba otřepů při provádění přerušovaných řezů. Nižší řezné síly.
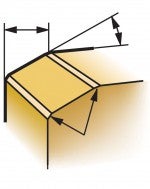
Typ S
Fazetka s lehkým honováním
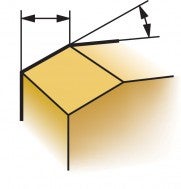
Typ T
Fazetka bez honování
Geometrie rohu břitové destičky
- Jsou-li podmínky stabilní, vždy použijte hladící geometrii, protože umožňuje dosažení nejvyšší kvality povrchu.
- V případě vysokých požadavků na produktivitu použijte koncepci břitových destiček s malým úhlem nastavení.
- Pouze je-li stabilita špatná (štíhlý obrobek atd.), měla by být použita břitová destička s normálním poloměrem zaoblení rohu.
Obrábění za sucha nebo za mokra
Soustružení tvrzených součástí bez přívodu řezné kapaliny představuje ideální situaci a je naprosto žádoucí. Jak CBN, tak i keramické břitové destičky odolávají vysokým teplotám v řezu, což umožňuje snížení nákladů a odstranění problémů souvisejících s použitím řezné kapaliny.
Některé aplikace mohou vyžadovat použití řezné kapaliny např. z důvodu kontroly tepelné stability obrobku. V takových případech je nutné zajistit nepřetržitý přívod řezné kapaliny po dobu trvání celé soustružnické operace.
Obecně platí, že teplo vznikající během obrábění se přenáší do třísky (80 %), obrobku (10 %) a břitové destičky (10 %). Z toho je patrné, jak důležité je odvádění třísek z místa řezu.
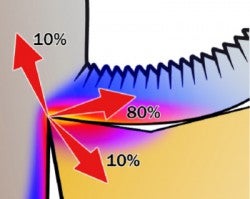
Řezné podmínky a opotřebení
Vysoké teploty v místě řezu vedou ke snížení řezných sil. Proto příliš nízké řezné rychlosti, při kterých vzniká méně tepla, mohou mít za následek lom břitové destičky.
Opotřebením ve tvaru žlábku se postupně snižuje pevnost břitové destičky, na druhou stranu příliš neklesá kvalita obrobené plochy. Naproti tomu opotřebení hřbetu postupně snižuje rozměrovou přesnost.
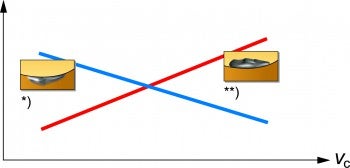
Podíl jednotlivých druhů opotřebení určujících životnost nástroje
*) Opotřebení hřbetu **) Opotřebení ve tvaru žlábku
Kritéria výměny břitové destičky
Častým a praktickým kritériem pro výměnu břitové destičky je předem stanovená hodnota drsnosti povrchu (B). Drsnost povrchu se automaticky měří na samostatném stanovišti a touto hodnotou je určena předepsaná kvalita obrobeného povrchu.
Abyste zajistili optimalizovaný a stabilnější obráběcí proces, stanovte jako kritérium výměny břitové destičky předem určený počet součástí (A). Tato hodnota by měla být o 10–20 % nižší, než odpovídá předem stanovené hodnotě drsnosti povrchu, přesné číslo je nutné stanovit podle konkrétního případu.
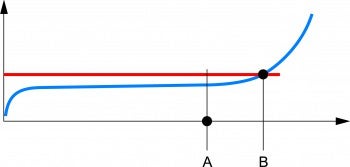
A: Předem stanovený počet součástí
B: Předem stanovená drsnost povrchu
Osa X: Počet součástí
Osa Y: Drsnost povrchu
Modrá čára: Opotřebení břitové destičky
Červená čára: Maximální hodnota Ra/Rz
Strategie jednoho řezu
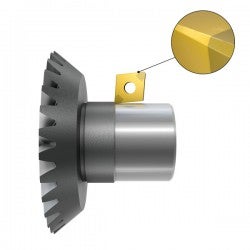
Strategie „odebrání kovu“ jedním řezem je vhodná jak pro vnější, tak i pro vnitřní obráběcí operace. Velice důležitá je stabilita nástrojové sestavy, přičemž vyložení nástroje by při soustružení vnitřních ploch nemělo přesáhnout průměr vyvrtávací tyče (1×D). S ohledem na dobré výsledky obráběcího procesu je doporučeno použití břitové destičky s fazetkou s mírným honováním a střední řezné rychlosti a rychlosti posuvu.
Výhody
- Nejkratší možná doba obrábění
- Jedna nástrojová pozice
Nevýhody
- Potíže se splněním přísných požadavků na rozměrové tolerance
- Kratší životnost nástroje (než při dvou řezech)
- Ztráta přesnosti v důsledku relativně rychlého opotřebení
Strategie dvou řezů
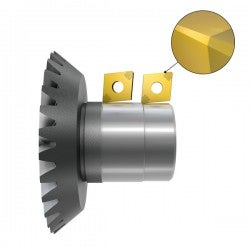
Bezobslužné obrábění s vysokou kvalitou obrobené plochy umožňuje strategie dvou řezů. Doporučeno je použití hrubovací břitové destičky s poloměrem zaoblení špičky 1,2 mm (0.047 inch) a dokončovací břitové destičky pouze se zkosenou hranou. Oba typy břitových destiček by měly mít hladící geometrii Wiper.
Výhody
- Nástrojové vybavení optimalizované pro hrubování a pro dokončování
- Vyšší bezpečnost, užší tolerance a potenciálně delší pracovní cyklus mezi dvěma výměnami nástrojů
Nevýhody
- Zapotřebí jsou dvě břitové destičky
- Využívány jsou dvě nástrojové pozice
- Jedna výměna nástroje navíc