자동차 산업에서 알루미늄 가공을 최적화하는 방법
자동차 산업에서 알루미늄으로 제조한 엔진, 파워트레인, 유압 펌프 및 제동 장치 시스템 부품의 사용이 증가하면서 더욱 생산적인 가공 공정을 구현하는 것이 OEM과 공급망 파트너의 과제가 되었습니다. 엔진 부품 가공 공정 전체에 걸쳐 최적화된 밀링 커터를 올바르게 사용할 경우 상당한 이득을 얻을 수 있는 자동차 산업에서 공구 선택은 진정한 시장 차별화를 위한 열쇠입니다.
기존 자동차와 하이브리드 자동차용으로 생산되는 알루미늄 엔진의 수는 매년 계속해서 증가하고 있는데, 실제로 매년 1억 개 가까이가 생산되고 있습니다. 이러한 엔진은 모양이 복잡한 부품이 사용되는 경우가 많으며, 주조 후에는 다양한 필수 밀링을 순서대로 거쳐야 합니다.
샌드빅 코로만트는 1단계 큐빙에서 황삭, 준정삭 및 정삭에 이르기까지 자동차 산업의 알루미늄 가공에 필요한 모든 제품을 제공하고 있습니다. 총 5개인 각 엔지니어링 밀링 공구는 품질과 부품당 비용이 최적화되도록 설계되었습니다. 일부 공구는 사이클 시간 단축을 통해 부품당 비용이 최적화되도록 한 번의 작업에서 황삭과 정삭을 모두 처리하는 것과 같은 복합 작업을 수행합니다.
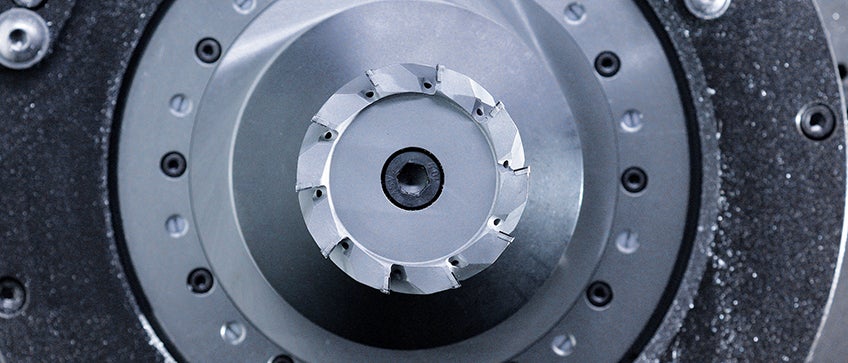
황삭과 준정삭을 하나의 공구에 구현한 혁신적인 커터인 M5C90이 좋은 예입니다. M5C90은 고객의 생산 현장에서 셋업 시간이 단축되도록 맞춤형으로 제작된 고속 단면 밀링 공구입니다. 독특한 반경 방향 및 축 방향 인서트 위치를 지정하므로 기존 커터보다 사용하는 날이 적습니다(인서트 조정이 필요하지 않음). 이러한 위치 지정을 통해 커터 맞물림이 넓은 실린더 헤드, 실린더 블록, 브레이크 시스템 부품 및 모든 알루미늄 가공물에서 버 없는 밀링과 최적의 표면 조도가 가능합니다(얇은 박판 부품에는 적용 불가).
M5C90을 사용할 때의 장점에 대한 예가 필요하면 AlSi12Cu1로 만든 브레이크 시스템 바디 밸브가 사용되는 고객 사례를 참고하시기 바랍니다. 바깥쪽에 외경 황삭용으로 초경 인서트 10개가 배치되고 안쪽에 인서트 4개(1개의 와이퍼 인서트 추가)로 구성된 내경(바닥면 가공용)이 특징인 이 공구는 스핀들 속도가 8,000 rpm, 절삭 속도가 분당 4,021 m(분당 13,192 ft)이며, 이송 속도가 날당 0.25mm(날당 0.009인치)입니다. 또한 축 방향 절입 깊이는 2 mm(0.078인치)이고, 반경 방향 절입 깊이는 140 mm(5.51인치)로 금속 제거율이 분당 5,600 cm3(분당 342 in3)입니다. 총 공구 수명은 아직 정해지지 않았지만 18개월 후에도 동일한 공구가 기계에서 계속 사용됩니다.
기어박스 하우징, 케이싱처럼 벽이 얇은 알루미늄 부품도 정삭하는 커터가 필요한 고객을 위해 샌드빅 코로만트는 마찬가지로 뛰어난 성능을 보이는 다른 커터인 M5F90을 제공하고 있습니다. M5F90도 한 번에 황삭과 정삭을 모두 처리할 수 있는 공구입니다. 얇은 박판 알루미늄 부품의 가공 및 스폿 단면 가공 전용인 커터 바디(25~80 mm, 직경 0.98~3.15 인치)에는 브레이징된 PCD 팁이 있으며, 각 팁에는 황삭 날과 정삭 날이 모두 포함되어 있습니다. 황삭 영역은 같은 직경 위치에 높이가 동일한 모든 절삭날이 있는 기존 밀링 공구로 작동하지만, 정삭 영역은 반경 방향 및 축 방향 스텝 절삭날로 구성됩니다. 이러한 공구를 이용하면 버가 없는 가공과 표면 조도를 향상시키는 것이 가능합니다.
Si 함량이 높은 알루미늄 실린더 헤드를 단면 밀링하는 고객 사례 시험에서 볼 수 있듯이 작업 시간을 많이 줄일 수 있습니다. M5F90을 이용하면 경쟁업체에서 제조한 특수 PCD 커터를 사용할 때보다 사이클 시간이 150% 줄어들며 버도 발생하지 않습니다. 절삭 조건은 스핀들 속도 15,915 rpm, 절삭 속도 2,000 m/min(6,562 ft/min), 이송률 0.16 mm/날(0.006 in/날), 절입 깊이 1.5 mm(0.06 inch)입니다.
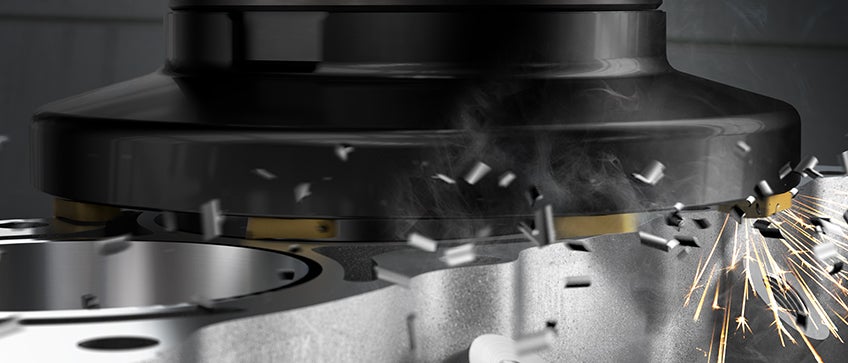
M5F90 사용에 대한 다른 예에서는 6개의 PCD 인서트가 있는 경쟁사의 직경 63 mm(2.48 inch) 인서트 교환형 커터를 사용할 때와 비교하여 알루미늄 체인 케이스에서 사이클 시간이 44% 단축되었습니다. 또한 이전에는 필수였던 버 제거 작업이 필요하지 않게 되었습니다.
또 다른 최신 엔지니어링 공구인 M610은 주로 알루미늄과 회주철(CGI)로 만들어진 바이메탈 소재를 가진 엔진 실린더 블록의 상단 표면을 밀링하기 위해 개발되었습니다.
바이메탈 소재는 열 특성과 기계적 특성 때문에 가공하기 어렵습니다. 이 작업에 사용되는 기존의 밀링 커터는 복잡하고 조정이 필요해서 처리 속도가 느리며, 가공물의 GCI 부분에서 칩핑이 발생하는 경우가 많습니다.
반면에 M610은 셋업과 조정이 필요하지 않으므로 부품의 치핑, 버 또는 스크래치가 없이 빠르게 이송이 진행됩니다. 표면 결함이 실린더 블록과 헤드 사이에 누출을 발생시켜 출력과 성능을 저하시킬 수 있으므로 이 기능은 매우 중요합니다. 일부 글로벌 자동차 OEM은 이미 M610을 도입하여 큰 효과를 보고 있습니다.
한 고객의 경우 바이메탈 엔진 블록의 연소면 정삭에서 경쟁사보다 훨씬 나은 품질을 얻고 있습니다. M610은 공구 수명이 경쟁사의 카트리지가 있는 조정식 커터의 833%이고, 가공할 수 있는 부품 수도 경쟁사 커터의 480개보다 훨씬 많은 4,000개 이상입니다. 또한 M610는 작동 속도가 경쟁사 제품의 10배입니다. 15인서트형 M610의 절삭 조건은 절삭 속도 3,000 m/min(9,843 ft/min), 이송 속도 5,720 mm/min(225 in/min), 스핀들 속도 3,820 rpm, 이송률 날당 0.15 mm(날당 0.006 in), 알루미늄 절입 깊이 0.5 mm(0.02 inch), 주철 절입 깊이 0.05 mm(0.002 inch)입니다.
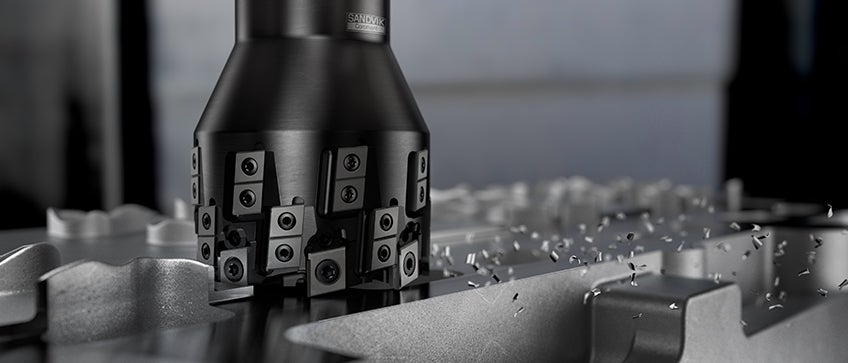
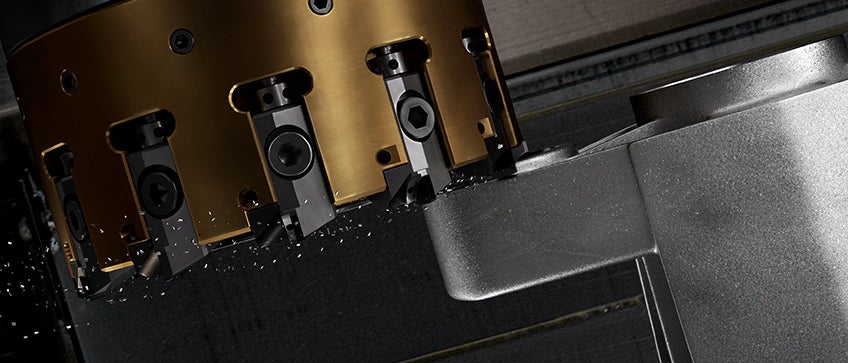
이 제품군에는 버 없는 단일 작업으로 1단계 큐빙(주조 후 면의 첫 번째 표면 가공)을 처리하는 M5Q90 탄젠셜 황삭 커터도 있습니다. 이 공구는 부드럽고 안정적인 절삭으로 전력 소비와 진동을 최소화하는 PCD 탄젠셜 인서트가 장착되어 있습니다.
알루미늄 실린더 헤드 및 블록과 같은 구성요소는 M5Q90로 가공을 하면 효과가 좋습니다. 예를 들어 주조 실린더 헤드를 큐빙 작업할 때는 캠축 표면, 흡입구/배출구 표면, 연소 표면을 가공해야 합니다. 한 고객의 사례에서는 수평 머시닝 센터에서 AS-9 알루미늄 합금으로 주조된 실린더 헤드를 황삭 단면 밀링 가공했더니 공구 수명이 크게 늘었습니다. 3,000 m/min(9,843 in/min)의 절삭 속도에서 날당 이송은 0.2 mm(0.008in), 축 방향 절입 깊이는 2.0 mm(0.079 in)이고, 반경 방향 40 mm(1.57 in)까지 100% Ae로 10,000개 이상의 부품 가공을 완료했습니다.
2단계 황삭/준정삭에 사용되는 M5R90도 있습니다. 표준 커터이며, 조정 가능한 카트리지가 사용되고, 카트리지에 따라 반경이 0.4 또는 0.8 mm(0.016 또는 0.031인치)인 최대 8 mm(0.315인치)를 절입할 수 있습니다. 조정하기 쉬운 카트리지는 엔진 커버의 단면 밀링이 사용된 최근의 고객 사례에서 볼 수 있듯이 많은 자동차 분야 가공에서 큰 도움이 됩니다. MRHB Si12 알루미늄 합금으로 주조된 M5R90은 기존의 경쟁업체 커터에 비해 매우 우수한 성능을 보였습니다. 동일한 절삭 조건에서 M5R90으로 가공할 수 있는 가공물은 8,000개에서 10,000개로 늘었습니다. 또한 경쟁사 커터는 카트리지가 움직여서 부품 1,000개를 가공할 때마다 조정해야 했습니다. 반면에 M5R90은 카트리지 조정이 필요하기까지 8,000개의 부품을 가공할 수 있었습니다.
이 제품군에는 독특한 축 방향 및 반경 방향에 인서트가 배치된 M5B90 수퍼피니싱(초정삭) 단면 밀링 커터도 있습니다. 이 구성을 와이퍼 인서트와 함께 사용하면 최근에 승용차용 실린더 헤드 제조업체에서 발견한 것처럼 표면 품질이 우수한 버 없는 절삭이 가능합니다. 이 업체는 공정 불안정성, 버 문제와 함께 셋업마다 카트리지 조정에 따라 인서트 수명이 예측할 수 없게 된다는 문제를 겪고 있었는데, M5B90 커터를 도입한 후 부드러운 정삭이 가능하고, 마모를 예상할 수 있게 되었으며, 버가 발생하지 않았습니다. 이 공구에서는 절삭 과정에서 쉽게 제거할 수 있는 매우 얇은 칩만 발생하므로 부품 표면이 손상되지 않습니다. 또한 M5B90을 도입한 후 공구 수명 내에서 가공할 수 있는 부품이 평균 30,000개에서 45,000개로 증가했습니다.
CoroDrill® 및 CoroTap® 제품군 드릴링 및 태핑 공구는 표준 CoroMill® Century 590 단면 밀링 정삭 커터와 마찬가지로 알루미늄 자동차 부품 가공을 위한 솔루션 제품군의 일부로 고객에게 제공될 수도 있습니다.
고객 사례에서 볼 수 있듯이 이 제품을 이용하면 사이클 시간과 부품당 비용을 줄이는 동시에 공구 수명과 품질을 쉽게 향상시킬 수 있습니다. 대량 생산이 주로 이루어지는 자동차 산업에서는 가공 공정 시간을 조금만 줄여도 수익성 향상에 큰 도움이 됩니다. 기업 입장에서는 더 많은 수익을 안겨주는 기술에 관심을 줄 수 밖에 없습니다.