Barenatura di precisione
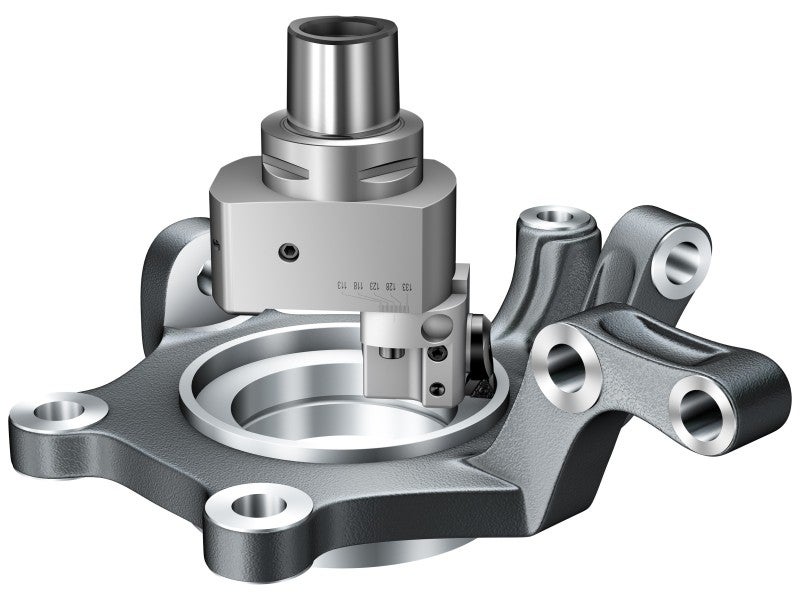
Le operazioni di barenatura di precisione servono a completare un foro preesistente per ottenere tolleranze strette, un corretto posizionamento e una finitura superficiale di elevata qualità. La lavorazione avviene a piccole profondità di taglio, generalmente inferiori a 0.5 mm (0.020 poll.).
La barenatura ad un tagliente viene utilizzata per le operazioni di finitura a piccole profondità di taglio quando è necessaria una tolleranza stretta (da IT6 a IT8) o una finitura superficiale di alta qualità. Il diametro di un bareno microregistrabile può essere regolato con una precisione micrometrica con un dispositivo ad alta precisione. La barenatura ad un tagliente può essere eseguita con un bareno di sgrossatura per la finitura di fori con tolleranze IT9 o superiori.
Barenatura in tirata
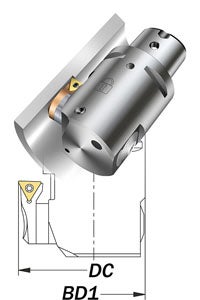
La barenatura in tirata permette la lavorazione di un foro con uno spallamento che non può essere raggiunto dalla direzione opposta. La barenatura in tirata può essere utilizzata anche per ottimizzare la concentricità di un foro con uno spallamento, dato che l'intero foro viene lavorato da una sola posizione.
Nota: Occorre verificare che il bareno passi attraverso il foro con lo spallamento e che la parte frontale del bareno non entri in collisione con il componente. Durante la barenatura in tirata, il bareno è configurato per passare attraverso un foro con diametro minimo di DC/2 + BD1/2.
Regolazione dell'utensile per la barenatura in tirata:
- Rimuovere la vite senza testa dal punto di uscita superiore del fluido da taglio e fissarla nel punto di uscita inferiore
- Regolare in modo da ottenere la corretta posizione del refrigerante (negli utensili di dimensioni più piccole, la vite senza testa non può essere fissata nel punto di uscita inferiore del fluido da taglio)
- Ruotare la cartuccia di 180°
- Se necessario, utilizzare l'estensione della slitta
- Invertire il senso di rotazione
Barenatura esterna
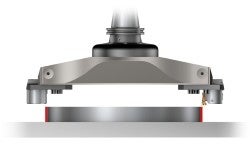
Le operazioni esterne di finitura possono essere eseguite con un bareno microregistrabile, in modo da ottenere tolleranze strette sui diametri.
Regolazione dell'utensile per la barenatura esterna:
- Invertire il senso di rotazione
- Capovolgere la testina di 180°
- Considerare la massima lunghezza possibile di lavorazione l3 e il diametro esterno dell'utensile per evitare collisioni
Nella lavorazione esterna, la massa della slitta e quella della testina microregistrabile ruotano attorno al pezzo generando forze centrifughe elevate. Quindi, la massima velocità di taglio di un'applicazione esterna deve essere calcolata rispetto alla massima velocità di taglio per il diametro lavorabile quando la testina viene ruotata di 180° ovvero quando l'utensile è configurato per la barenatura di precisione.
Esempio di calcolo:
- Diametro esterno da lavorare: 80 mm (3.15 poll.)
- Diametro interno che potrebbe essere lavorato (con slitta e testina in questa posizione): 210 mm (8.27 poll.)
Nota: per ottenere il diametro necessario a calcolare il numero massimo di giri al minuto, aggiungere sempre 130 mm (5.12 poll.) al diametro che dovrebbe essere lavorato - Massima velocità di taglio in base alla lavorazione interna (in questo esempio, per CoroBore® 825): 1200 m/min (3937 piedi/min)
- 1200 m/min (3937 piedi/min) al diametro di 210 mm (8.27 poll.) è uguale a 1820 giri/min. Ciò significa che 1820 giri/min è la massima velocità di rotazione possibile con slitta e testina in questa posizione
- Per la lavorazione esterna, 1820 giri/min corrispondono a una velocità di taglio di 460 m/min (1509 piedi/min) al diametro di 80 mm (3.15 poll.)
Scelta dell'inserto per le operazioni di finitura
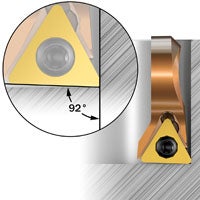
Gli inserti con posizionamento di base positivo rappresentano la scelta prioritaria per tutte le applicazioni di barenatura di precisione, in quanto garantiscono forze di taglio inferiori rispetto a quelli con posizionamento di base negativo. Inoltre, è disponibile un'ampia gamma di geometrie degli inserti.
L'angolo di registrazione per la barenatura di precisione dovrebbe essere di almeno 90° (angolo di attacco di 0°), in modo da minimizzare le forze di taglio radiali ed evitare vibrazioni.
La maggior parte dei bareni microregistrabili di Sandvik Coromant ha un angolo di registrazione di 92° (angolo di attacco di -2°), per consentire la lavorazione di spallamenti e fori ciechi senza impegnare l'intero tagliente.
Ulteriori informazioni su come scegliere il corretto inserto di tornitura.
Forze di taglio nella barenatura di precisione
Quando l'utensile è impegnato nel taglio, una componente tangenziale ed una componente radiale della forza di taglio tendono a flettere l'utensile allontanandolo dal pezzo. La componente tangenziale spinge con forza l'utensile verso il basso rispetto all'asse. Così facendo, l'angolo di spoglia inferiore dell'utensile si riduce.
La flessione radiale invece riduce la profondità di taglio e lo spessore del truciolo, generando una tendenza alle vibrazioni.
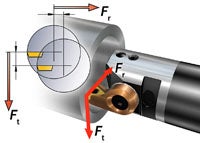
Bilanciamento nella barenatura di precisione
Lo sbilanciamento, dovuto a un utensile asimmetrico o a un grande runout, genera una forza che agisce sul bareno. Nella maggior parte delle applicazioni, la forza generata dallo sbilanciamento è trascurabile rispetto alle forze di taglio.
A velocità elevate, soprattutto con lunghe sporgenze, lo sbilanciamento può invece generare vibrazioni ed incidere sulla qualità del foro.
Flessione dell'utensile
La misura delle componenti tangenziale e radiale della forza di taglio è influenzata da profondità di taglio, raggio di punta ed angolo di registrazione.
La flessione in direzione radiale incide sul diametro del foro lavorato. La flessione tangenziale incide sul tagliente dell'inserto spingendolo verso il basso, lontano dall'asse. Per compensare le flessioni radiali, seguite le nostre raccomandazioni. I bareni microregistrabili di Sandvik Coromant sono dotati di un meccanismo di regolazione che consente di registrare il diametro con una precisione di 2 μm (0.0787 μpoll.).
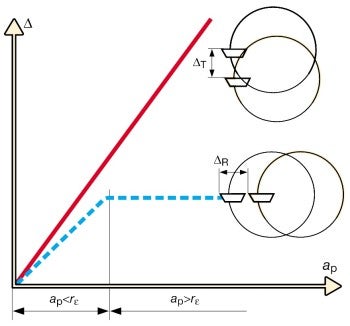
Asse X: profondità di taglio
Asse Y: flessione
Linea rossa: flessione tangenziale
Linea blu: flessione radiale
Checklist applicativa per la barenatura di precisione
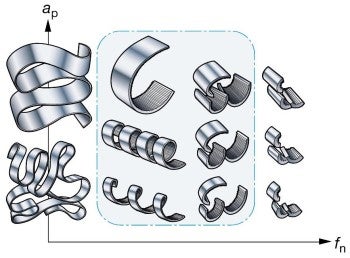
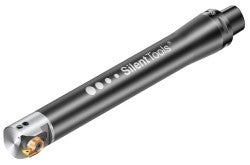
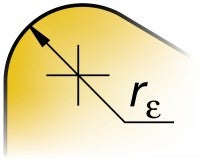
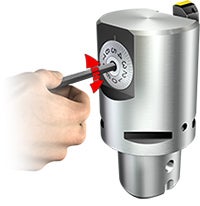
- Scegliere l'accoppiamento o il diametro barra più grande possibile
- Verificare il corretto controllo truciolo. I trucioli corti o duri possono generare vibrazioni mentre i trucioli lunghi potrebbero pregiudicare la finitura superficiale o provocare la rottura dell'inserto
- Scegliere la sporgenza più corta possibile e utilizzare barre di alesatura antivibranti per sporgenze superiori a quattro volte le dimensioni dell'accoppiamento
- Un raggio di punta (RE) dell'inserto grande aumenta l'affidabilità del processo e migliora la finitura superficiale ma potrebbe generare vibrazioni. Un raggio di punta superiore a 0.4 mm (0.016 poll.) non è consigliabile. Quando si usano barre di alesatura per piccoli diametri, è opportuno selezionare un raggio di punta di 0.2 mm (0.008 poll.)
- Generalmente, gli inserti con rivestimento sottile o quelli non rivestiti generano basse forze di taglio rispetto agli inserti con rivestimento di elevato spessore. Ciò è particolarmente importante quando la relazione tra lunghezza e diametro dell'utensile è notevole.
- Un tagliente affilato migliora, in genere, la qualità del foro grazie alla minore tendenza alle vibrazioni
- Una geometria con un rompitrucioli aperto risulta spesso vantaggiosa
- Scegliere un inserto ad azione di taglio leggera per generare una buona finitura superficiale (non consigliato per condizioni instabili o lunghe sporgenze)
- L'impegno insufficiente del tagliente può aumentare le vibrazioni dovute all'attrito durante il taglio
- Un eccessivo impegno del tagliente (grande profondità di taglio e/o avanzamento) può aumentare le vibrazioni a causa della flessione dell'utensile
- In alcune operazioni, per contrastare il rischio di intasamento da truciolo o la tendenza alle vibrazioni, potrebbe essere considerata una qualità di inserto più tenace
- Quando si lavora con tolleranze di foro strette, dopo la misurazione del diametro del foro, eseguire sempre una regolazione finale mentre l'utensile è ancora nel mandrino della macchina. Ciò compensa gli eventuali disallineamenti tra dispositivo di presettaggio e misurazione (tool presetter) e mandrino della macchina utensile, le flessioni radiali o l'usura dell'inserto
- Assicurarsi di bloccare correttamente bareno e pezzo
- Utilizzare fluido da taglio per favorire l'evacuazione truciolo, aumentare la durata utensile e migliorare la geometria del foro
- Sistema modulare per piccoli diametri Con uno stelo conico si ottiene un foro più diritto con sporgenze lunghe, indipendentemente dal mandrino utilizzato. Per sporgenze fino a 6xD, è consigliabile utilizzare uno stelo conico in metallo duro integraleCon uno stelo cilindrico, la rettilineità migliore si ottiene con sporgenze cortePer una maggiore stabilità e una minore tendenza alle vibrazioni a corte sporgenze, scegliere steli in acciaio ad alta densitàScegliere mandrini idraulici ad alta precisione per ottenere massima stabilità e sicurezza di produzione
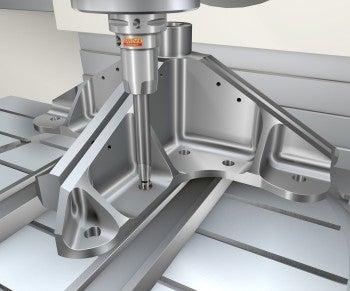
Per le raccomandazioni di ordine generale, vedere anche Come procedere alla barenatura.
Fare clic sulle istruzioni di manipolazione che seguono per individuare il momento torcente di serraggio consigliato.
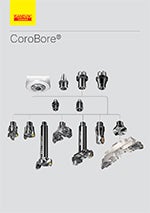