Porausvinkkejä
Ohjeita ja vinkkejä lastuamisnesteen käyttöön
Lastuamisnesteen asianmukainen käyttö on tehokkaan porauksen tärkeä edellytys. Lastuamisneste vaikuttaa:
- lastunpoistoon
- reiän laatuun
- terän kestoikään.
Lastuamisnestesäiliön tilavuuden tulisi olla 5–10 kertaa suurempi kuin pumpun tuotto minuuttia kohti. Riittävä litratuotto on olennaista.
Pumpun kapasiteetti voidaan tarkistaa ajanottokellon ja sopivan kokoisen astian avulla.
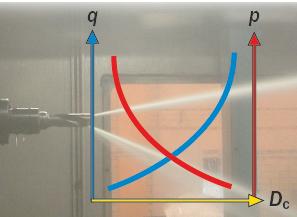
Paineen ja halkaisijan suhde lastuamisnesteen
syötössä (paine punainen, halkaisija keltainen, määrä sininen)
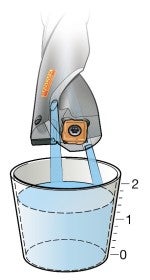
Mittaa porasta tuleva nestemäärä
- Lastuamisnesteenä tulee aina käyttää EP-lisäaineita sisältävää emulsiota. Paras terän kestoikä saadaan öljy–vesisuhteella 5–12 % (ruostumattomien terästen ja superseosten porauksessa 10–15 %). Jos öljypitoisuutta kasvatetaan, on aina varmistettava, ettei toimittajan suosittelemaa enimmäismäärää ylitetä
- Sisäinen lastuamisnestekanava on aina paras ratkaisu, jos sen käyttö on mahdollista.
- Puhdas öljy tehostaa voitelua ja on eduksi ruostumattomien terästen porauksessa. Käytä aina EP-lisäaineita. Puhdas öljy soveltuu hyvin sekä täyskovametallisille että kääntöteräisille porille.
- Edullisissa olosuhteissa ja varsinkin joidenkin valurautojen ja alumiinin porauksessa paineilma ja sumu- tai minimivoitelu voivat myös toimia hyvin. Tällöin suositellaan lastuamisnopeuden alentamista, sillä korkeammat lämpötilat voivat lyhentää terän kestoikää
Läpijäähdytys
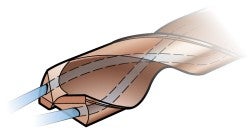
Nesteensyöttö työkalun läpi on aina suositeltavin vaihtoehto tukosten välttämiseksi, varsinkin pitkälastuisten materiaalien ja syvien reikien (>3 x DC) porauksessa.
Vaaka-asennossa olevasta porasta tulevan nestesuihkun tulisi ulottua vaakasuoraan vähintään 30 cm:n (11.81 in) mitalle.
Ulkopuolinen nesteensyöttö
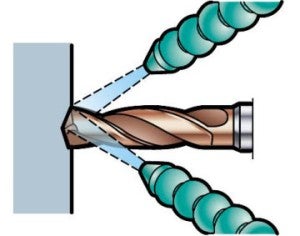
Lastuamisneste voidaan syöttää myös ulkopuolisesti, kun lastunmuodostus on tehokasta ja reikä on lyhyt. Lastunpoiston tehostamiseksi ainakin yhden nestesuuttimen (kahden, jos pora ei pyöri) tulee olla lähes poran akselin suuntainen.
Kuivaporausvinkkejä, ilman lastuamisnestettä
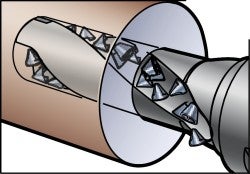
Kuivana poraamista ei yleensä suositella.
- Tulee kyseeseen lyhytlastuisten aineiden porauksessa, kun reiän syvyys on korkeintaan kolme kertaa halkaisija.
- Pora mieluiten vaakasuorassa.
- Tällöin suositellaan lastuamisnopeuden alentamista.
- Terien kestoikä lyhenee.
Kuivaporausta ei suositella lainkaan seuraaville materiaaleille ja työkaluille:
- Ruostumattomat materiaalit (ISO M ja S)
- Vaihtokärkiset porat
Nesteensyöttö korkealla paineella (HPC) (~70 bar)
Korkeapaineisen lastuamisnesteen edut:
- Tehokkaampi jäähdytys – pidempi terän kestoikä
- Tehokkaampi lastunpoisto ja mahdollisesti pidempi terän kestoikä porattaessa pitkälastuisia materiaaleja, kuten ruostumattomia teräksiä
- Tehokkaamman lastunpoiston ansiosta varmempi prosessi
- Takaa riittävän tuoton tarvittavalla painetasolla ja reikäkoolla
Vinkkejä lastunhallintaan
Lastunmuodostus ja -poisto ovat porauksessa kriittisiä tekijöitä. Niihin vaikuttavat lastuttava materiaali, pora-/terägeometria, lastuamisnesteen paine/määrä ja lastuamisarvot.
Lastutukokset voivat liikuttaa poraa radiaalisuunnassa, mikä huonontaa reiän laatua ja poran kestoikää ja luotettavuutta sekä aiheuttaa pora-/terärikkoja.
Paksummat ja jäykemmät lastut | ||
Nopeus | ![]() | Pienemmän kitkan ansiosta avoimempi |
Syöttö |
Lastut muodostuvat sopivalla tavalla, jos ne poistuvat sujuvasti reiästä. Paras tapa varmistua asiasta on kuunnella porausääntä. Kun ääni on tasainen, lastunpoisto sujuu hyvin, kun taas katkonainen ääni on merkki lastutukoksista. Tarkista syöttövoima tai tehonotto. Jos niissä on epäsäännöllisyyttä, syynä voi olla lastutukos. Tarkastele lastuja. Jos ne ovat pitkiä ja taipuneita, mutta eivät kiharaisia, reiässä on ollut lastutukos. Tarkastele reikää. Mahdollinen lastutukos näkyy pinnan epätasaisuutena.
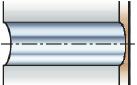
Reikä, josta lastut ovat poistuneet hyvin
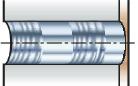
Reikä, jossa on esiintynyt lastutukoksia
Näin lastutukokset estetään:
- Varmista, että lastuamisarvot ja pora/terägeometria ovat oikeat
- Seuraa lastujen muotoa – säädä syöttöä ja nopeutta
- Tarkista lastuamisnesteen määrä ja paine
- Tarkista teräsärmät. Pitkien lastujen syynä voivat olla lastunmurtajan vajaasta käytöstä johtuvat teräsärmän vauriot/murtumat.
- Tarkista, onko lastuttavuus muuttunut uuden materiaalierän myötä, muuta tarvittaessa lastuamisarvoja
Hyvät, tyydyttävät ja huonot lastut
Kääntöteräporat
Keskiöterä ottaa helposti tunnistettavan kartiomaisen lastun. Kehäterän ottama lastu muistuttaa sorvilastua.
Keskiö | ![]() | Kehä |
Hyvä | Hyvä | |
![]() | ![]() | |
Tyydyttävä | Tyydyttävä | |
![]() | ![]() | |
Lastutukos | Lastutukos | |
![]() | ![]() |
Täyskovametalliporat
Pora ottaa yhtenäisen lastun koko särmän pituudelta.
Hyvä
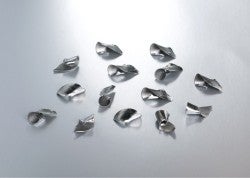
Tyydyttävä
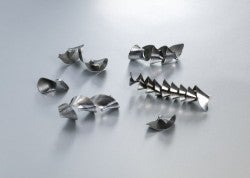
Lastutukos
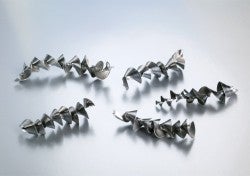
Aloituslastu
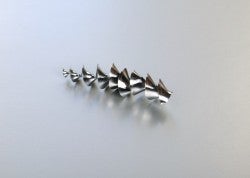
Huom: Aloituslastu, joka syntyy poran tunkeutuessa työkappaleeseen, on aina pitkä eikä aiheuta ongelmia.
Vaihtokärkiset porat
Hyvä
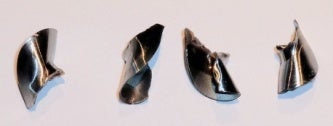
Tyydyttävä
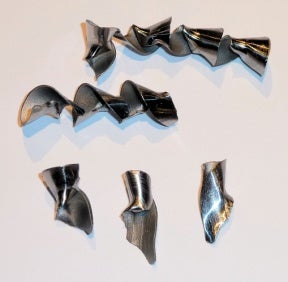
Huono, altis tukoksille
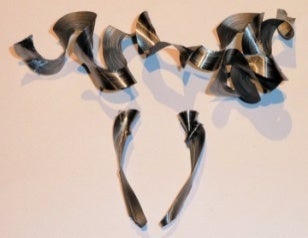
Nopeuksia ja syöttöjä koskevia ohjeita ja vinkkejä
vc (m/min)
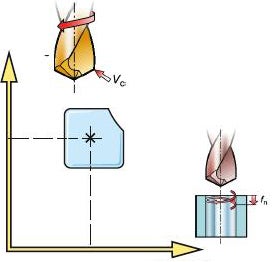
fn (mm/r)
Lastuamisnopeuden vaikutus – vc (m/min [ft/min])
Lastuamisnopeus on porattavan materiaalin kovuuden ohella tärkein terän kestoikään ja tehontarpeeseen vaikuttava tekijä.
- Tärkein kestoiän määräävä tekijä
- Vaikuttaa tehoon Pc (kW) ja vääntömomenttiin Mc (Nm)
- Mitä suurempi nopeus, sitä korkeampi lämpötila ja voimakkaampi viistekuluminen, eritoten pääsärmän nirkossa
- Nopeuden kasvattaminen tehostaa lastunmuodostusta tiettyjä pitkälastuisia, pehmeitä materiaaleja, esim. niukkahiilistä terästä porattaessa
- Liian ison lastuamisnopeuden seurauksia: Nopea viistekuluminenPlastinen muodonmuutosHuono reiän laatu, reikä ei ole toleranssissa
- Liian pienen lastuamisnopeuden seurauksia: IrtosärmäHeikko lastunpoistoPidempi koneistusaika
Syötön vaikutus – fn (mm/r [in/r])
- Vaikuttaa lastunmuodostukseen ja reiän pinnankarheuteen ja laatuun
- Vaikuttaa tehoon Pc (kW) ja vääntömomenttiin Mc (Nm)
- Iso syöttö vaikuttaa myös syöttövoimaan Ff (N), mikä tulee ottaa huomioon ei-tukevissa olosuhteissa
- Vaikuttaa poran mekaaniseen ja termiseen kuormitukseen
- Iso syöttö: Rajumpi lastunmurtoLyhyempi koneistusaikaTerä kuluu vähemmän, mutta alttius porarikkoon kasvaaHuonompi reiän laatu
- Pieni syöttö: Pidemmät ja ohuemmat lastutParempi laatuPora kuluu nopeamminPidempi koneistusaika
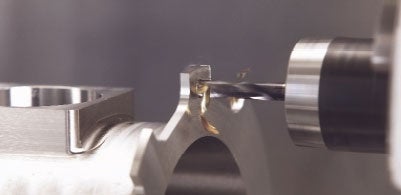
Jos pora on ohut tai työkappale heikko, syöttö tulee pitää maltillisena.
Vinkkejä hyvälaatuisten reikien koneistukseen
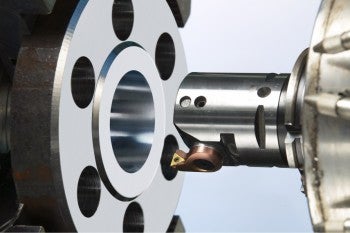
- Lastunpoisto
Varmista, että lastunpoisto on tehokasta. Lastutukokset heikentävät reiän laatua ja terän luotettavuutta/kestoikää. Pora-/terägeometria ja lastuamisarvot ovat ratkaisevan tärkeitä.
- Tukevuus, työkaluyhdistelmä
Käytä mahdollisimman lyhyttä poraa. Käytä tukevaa ja tarkkaa pidintä, jolla on mahdollisimman pieni heitto. Varmista, että koneen kara on hyvässä kunnossa ja heitoton. Varmista työkappaleen kiinnityksen tukevuus. Määrittele oikeat syöttöarvot epätasaisille, kalteville pinnoille ja risteäville rei'ille.
- Terän kestoikä
Tarkista terän kuluneisuus ja seuraa järjestelmällisesti terien kestoikää. Tehokkain tapa valvoa porausta on käyttää syöttövoimamittaria.
- Huolto
Vaihda terien kiinnitysruuvit säännöllisesti. Puhdista teräsija ennen terän vaihtoa ja käytä aina momenttiavainta. Hio täyskovametalliset porat uudelleen ennen kuin ne kuluvat liiaksi.
Vinkkejä ja menetelmiä eri materiaaleille
- Niukkahiilinen teräs
- Austeniittiset ruostumattomat teräkset ja duplexit
- Tylppägrafiittirauta (CGI)
- Alumiiniseokset
- Titaani ja kuumalujat seokset
- Kovat teräkset
Vinkkejä niukkahiilisen teräksen poraukseen

Ongelma: Lastunmuodostus voi olla hankalaa hitsattuihin kappaleisiin yleisesti käytettyjen niukkahiilisten terästen porauksessa. Muodostuvat lastut ovat sitä pitempiä, mitä alhaisempi teräksen kovuus ja hiili- ja rikkipitoisuus on.
Suositukset: Jos lastunmuodostus tuottaa ongelmia, lisää nopeutta, vc, ja pienennä syöttöä fn (huomaa, että normaalia terästä porattaessa syöttöä tulee lisätä).
Muuta: Käytä nestekanavallista poraa ja korkeaa nestepainetta.
Vinkkejä austeniittisten ja duplex-terästen poraukseen

Ongelma: Austeniittiset, duplex- ja superduplex-teräkset voivat aiheuttaa lastunmuodostus- ja lastunpoisto-ongelmia.
Suositukset: Valitse juuri oikea geometria, sillä se tehostaa lastunmuodostusta ja -poistoa. Yleensä kannattaa valita terävä särmä. Jos lastunmuodostus tuottaa ongelmia, lisää syöttöä, fn, jolloin lastunmurto tehostuu.
Muuta: Läpijäähdytys korkealla paineella.
Vinkkejä tylppägrafiittiraudan (CGI) poraukseen

Ongelma: Tylppägrafiittirauta ei yleensä vaadi erityistä huomiota. Siitä muodostuu suurempia lastuja kuin harmaasta valuraudasta, mutta ne murtuvat hyvin. Lastuamisvoimat ovat suuremmat, mikä vaikuttaa terän kestoikään. Vaatii terälaadulta erityisen hyvää kulumiskestävyyttä. Nirkon kuluminen on valuraudan porauksessa aina tyypillistä.
Suositukset: Jos lastunmuodostus tuottaa ongelmia, lisää nopeutta, vc, ja pienennä syöttöä fn.
Muuta: Läpijäähdytys.
Vinkkejä alumiiniseosten poraukseen

Ongelma: Jäysteenmuodostus ja lastunpoisto voivat aiheuttaa haasteita, ja adheesio voi huonontaa terän kestoikää.
Suositukset: Paras lastunmuodostus saadaan käyttämällä pientä syöttöä ja suurta nopeutta.
Terän kestoiän parantamiseksi voi olla tarpeen kokeilla erilaisia, adheesion minimoivia pinnoitteita. Tällaisia pinnoitteita voivat olla esimerkiksi timanttipinnoitteet. Perusaineesta riippuen myös pinnoittamaton laatu voi toimia.
Muuta: Käytä emulsiota tai sumuvoitelua suurella paineella.
Vinkkejä titaanin ja kuumalujien seosten poraukseen

Ongelma: Reiän pinta työstökarkenee ja vaikeuttaa myöhempiä työvaiheita. Lastunpoistossa voi olla vaikeuksia.
Suositukset: Titaanin poraukseen kannattaa valita teräväsärmäinen geometria. Nikkelipohjaisten seosten poraukseen vaaditaan vahvaa geometriaa. Jos työstökarkeneminen on ongelma, kokeile syötön suurentamista.
Muuta: Korkeapaineinen (jopa 70 bar) lastuamisneste parantaa suorituskykyä.
Vinkkejä kovan teräksen poraukseen

Ongelma: Terän kestoikä.
Suositukset: Pienennä lastuamisnopeutta lämpötilan alentamiseksi. Säädä syöttöä siten, että muodostuu helpommin poistuvia lastuja.
Muuta: Käytä runsaasti öljyä sisältävää emulsiota.
Reiän toleranssi
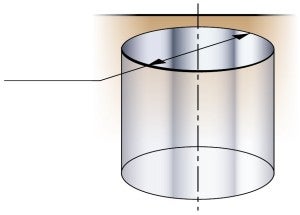
Reiän mitat voidaan jakaa kolmeen parametriin:
- Nimellismitta (teoreettinen tarkka mitta)
- Toleranssiaste (ISO-standardin merkintä: IT)
- Toleranssiasema (merkitään ISO:n mukaan isoilla kirjaimilla)
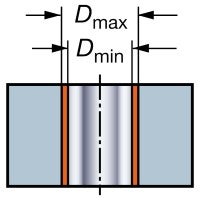
Dmax miinus Dmin = toleranssiaste (IT).
Halkaisija-alue, D (mm) | |||||||||
Työkalun leveys | D > 3–6 | D > 6–10 | D > 10–18 | D > 18–30 | D > 30–50 | D > 50–80 | D > 80–120 | D > 120–180 | D > 180–250 |
IT5 | 0.005 | 0.006 | 0.008 | 0.009 | 0.011 | 0.013 | 0.015 | 0.018 | 0.020 |
IT6 | 0.008 | 0.009 | 0.011 | 0.013 | 0.016 | 0.019 | 0.022 | 0.025 | 0.029 |
IT7 | 0.012 | 0.015 | 0.018 | 0.021 | 0.025 | 0.030 | 0.035 | 0.040 | 0.046 |
IT8 | 0.018 | 0.022 | 0.027 | 0.033 | 0.039 | 0.046 | 0.054 | 0.063 | 0.072 |
IT9 | 0.030 | 0.036 | 0.043 | 0.052 | 0.062 | 0.074 | 0.087 | 0.100 | 0.115 |
IT10 | 0.048 | 0.058 | 0.070 | 0.084 | 0.100 | 0.120 | 0.140 | 0.160 | 0.185 |
IT11 | 0.075 | 0.090 | 0.110 | 0.130 | 0.160 | 0.190 | 0.220 | 0.250 | 0.290 |
IT12 | 0.120 | 0.150 | 0.180 | 0.210 | 0.250 | 0.300 | 0.350 | 0.400 | 0.460 |
IT13 | 0.180 | 0.220 | 0.270 | 0.330 | 0.390 | 0.460 | 0.540 | 0.630 | 0.720 |
Halkaisija-alue, D (in) | |||||||||
Työkalun leveys | D > 0.118–0.236 | D > 0.236–0.394 | D > 0.394–0.709 | D > 0.709–1.181 | D > 1.181–1.969 | D > 1.969–3.150 | D > 3.150–4.724 | D > 4.724–7.087 | D > 7.087–9.843 |
IT5 | 0.0005 | 0.0002 | 0.0003 | 0.0004 | 0.0004 | 0.0005 | 0.0006 | 0.0007 | 0.0008 |
IT6 | 0.0003 | 0.0004 | 0.0004 | 0.0005 | 0.0006 | 0.0007 | 0.0009 | 0.0010 | 0.0011 |
IT7 | 0.0005 | 0.0006 | 0.0007 | 0.0008 | 0.0010 | 0.0012 | 0.0014 | 0.0016 | 0.0018 |
IT8 | 0.0007 | 0.0009 | 0.0011 | 0.0013 | 0.0015 | 0.0018 | 0.0021 | 0.0025 | 0.0028 |
IT9 | 0.0012 | 0.0014 | 0.0017 | 0.0020 | 0.0024 | 0.0029 | 0.0034 | 0.0039 | 0.0045 |
IT10 | 0.0019 | 0.0023 | 0.0028 | 0.0033 | 0.0039 | 0.0047 | 0.0055 | 0.0063 | 0.0073 |
IT11 | 0.0030 | 0.0035 | 0.0043 | 0.0051 | 0.0063 | 0.0075 | 0.0087 | 0.0098 | 0.0114 |
IT12 | 0.0047 | 0.0059 | 0.0071 | 0.0083 | 0.0098 | 0.0118 | 0.0138 | 0.0157 | 0.0181 |
IT13 | 0.0071 | 0.0087 | 0.0106 | 0.0129 | 0.0154 | 0.0181 | 0.0213 | 0.0248 | 0.0283 |
- Mitä pienempi IT-luku, sitä tarkempi toleranssi
- IT-luokan toleranssialue kasvaa isommilla halkaisijoilla
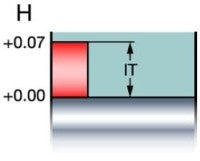
Esimerkki:
Nimellismitta: 15.00 mm
Toleranssialue: 0.07 mm (ISO: IT10)
Toleranssiasema: 0:sta ylöspäin (ISO: H)
Reikä- ja akselitoleranssit
Reiän toleranssi on usein riippuvainen reikään tulevan akselin toleranssista.
Esimerkki:
Akseli ø20 mm (0.787 in) h7
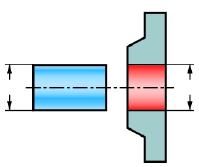
Reikä ø20 mm (0.787 in) H7
Akselin toleranssiasema merkitään reikätoleransseja vastaavilla pienillä kirjaimilla. Kuvassa kokonaisesitys reikä- ja akselitoleransseista.
Yleisin | ||
Reikä akselia isompi | ![]() | Akseli reikää isompi |
Välyssovite | | Liukusovite | Pakotussovite | | Ahdistussovite |
Välys (laakerit) | ![]() | Ahdistus = negatiivinen välys (kiinteät liitokset) |