Five Questions with Joe Hobbs
This month we catch up with Joe Hobbs, Drilling Specialist extraordinaire on the Product & Industry team in the US. In his 27 year career, Joe worked as a machinist, lead person, and shop supervisor before joining Sandvik Coromant in 2006. With a passion for both math and metal cutting, he puts his experience, expertise, and energy to work for every customer he encounters. We asked Joe about his passion for the industry, how modern technology plays a role in metal cutting, why the CoroDrill DS20, the 7 X D indexable drill is the “workhorse of production shops,” and more. Here’s what he has to say in this five-minute read.
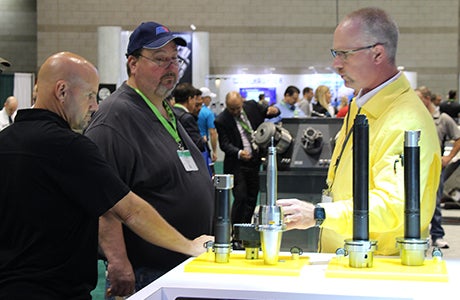
Sandvik Coromant: What is your background and why are you so passionate about metal cutting? And share with us what is so impressive about indexable drills like the CoroDrill DS20.
Joe Hobbs: I have always had a passion for math and cutting metal, and the two go hand in hand. I have a character flaw called perfectionism, which drives me to do better than I have done in the past. That drive works well in metal cutting as it is a precise science. My metal cutting experience of 27 years and my love of working with people, makes me a perfect representative for drilling. I always say that I love drilling since it, like me, is so straight forward. In my career, I have attended many different metal cutting classes and have had some great mentors and engineers who have taken me under their wing and taught me everything they know. While some of these lessons were how to approach part prints or how to set up a machine, I had to learn the molecular structure of centrifugal cast duplex stainless materials and how the center of the material cuts differently than the outer layers that lead to the free machining metals in between them. I guess you can say the I attended the school of hard knocks in metal cutting.
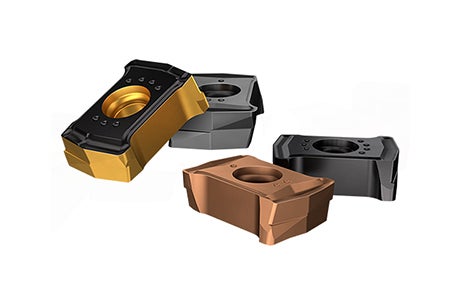
The true beauty in an insert drill comes from its inserts. While the body is important to stabilize the process of drilling and remove the chips, it is the inserts that make the drill so flexible. Whereas many general engineering shops cut a variety of metal for the constantly changing industries, the new CoroDrill DS20 is a perfect fit. Having a variety of geometries and grades that can be changed very inexpensively makes this new insert drill very productive. The variety of cutting edges and grades give the new CoroDrill DS20 the ability to be the workhorse of production shops with large volumes of work, to job shops with short runs. However, this new drill comes with the most rigid drill body in the industry. This is why we have released the CoroDrill DS20 in 4 - 7 X D lengths that range from 15mm (.590”) to 65mm (2.559”) diameters. To give a little perspective on how hard it is to drill at 7 X D, there are 43 times more deflection forces at 7 X D than there is at 1 X D. That is why Sandvik Coromant has set this new drill to focus on the largest deflective cutting forces. The CoroDrill DS20 is not just about drilling deep holes though, many applications require shops to reach over fixturing or into the bottom of deeper features to drill a hole. This new drill can not only drill a hole, it can drill and bore, counterbore, chamfer, drill off-center with a radial adjustment, and even cut the burr from the back of a through-hole in a lathe. The new CoroDrill DS20 changes the way we have to approach parts that once had to be flipped to drill from both sides, to now drilling very productively from just once side.
SC: What are the important considerations for drilling? Do those considerations change depending on the material you are drilling or the industry? And when using a 7 x D drill, what types of methods or best practices need to be followed to avoid vibration or any other negative consequences?
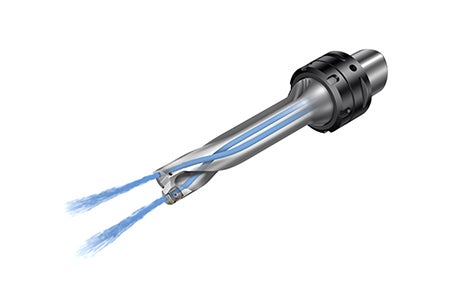
JH: There are many considerations to evaluate when we look at any drilling application. Material, machine, hole size, hole depth, hole tolerances such as diameter and finish are the obvious considerations. And then we have to select the correct drill for the hole that is being produced as well as the drill holder, work holding, and coolant flow. I often hear machinists say that they have high-pressure coolant when I ask about coolant flow for the machine they are working on. But coolant flow is not the same as pressure, and the two should not be conflated, and need to be kept separate. Coolant pressure helps to get the coolant to the cutting edges at high RPM’s and in an insert drill, it is very helpful in through holes to push the end disc away from the hole. Coolant flow, however, helps to carry the chips up the drill flutes and out of the hole that we are creating. Materials all react differently when being drilled so the insert geometry and coating grades will help optimize the operation to keep the cost per hole low. While the material dictates geometry and grade, it is the machine that is impacted by these choices, so we focus on horsepower and torque requirements, especially with larger drills or using driven tooling units in lathes with lower horsepower allotment. It is also important to remember that insert drills are roughing drills and have fast metal removal rates but that comes at a cost of hole tolerance. Depending on the diameter and length of the drill, insert drills can have tolerances as high as .015” or even higher in some applications. These tolerances can be mitigated with certain tool holders and techniques. That is why it is so important to discuss an entire process and application with the machinist and engineer to get the full benefit of the machining and meet our customer’s needs.
Drilling 7 X D means that we must have full stability. We discussed before the 43 times more deflective forces that we see at 7 X D over 1 X D. These deflective cutting forces only become greater when the drill is not in a rigid environment. This means that the drill has to be held in the best drill holders. The lowest stable drill holder that the CoroDrill DS20 should be held in is the ISO-9766 drill holder. This holder, while looking similar to the Weldon shank holder, has a tighter tolerance on the bore that holds the shank of the drill that meets the same standards that govern how the shank is given its tolerance. The new CoroDrill (Modular Drilling Interface) MDI holder is the best method for holding these drills as it has very tight ground tolerances and fully stabilizes the drill at its shortest possible length in a holder. We need to drill with the shortest possible drill to provide optimum hole quality. The same holds for the entire length of the drill and its holder. Shorter is best. When we encounter vibration we need to isolate the cause and correct that cause. The cause could be in the work holding or the drill holding. Where we have all the best practices in place we need to then look at the geometry of the inserts and ask if there are adjustments in both peripheral and central geometries that could help reduce these vibrations.
SC: You recently visited a customer who is using the CoroDrill DS20. What can you tell us about changes to their operation once they started using the drill and what happens after a customer buys a tool such as the CoroDrill DS20?
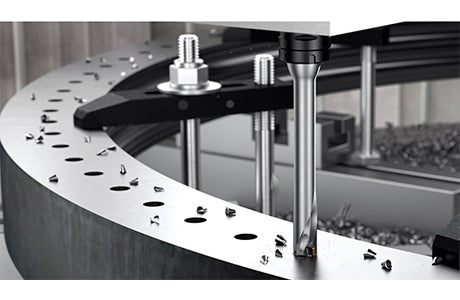
JH: A customer was drilling a component from both sides on a lathe. The hole was a through-hole that needed to be 1.250” in diameter and had to be 8 inches long or 6.4 times diameter to length. Our customer previously tried using spade style drill tips but they encountered too much drill walk by the end of the hole that they had to go to using a shorter drill and drill from both sides flipping the part mid-operation. With the CoroDrill DS20, we were able to drill to length from one side with no drill walk and gave the customer the best hole results with a single operation. Not only did the customer save on the time cost of not flipping the part but with the 4 corner solution of the CoroDrill DS20, the customer saved a large amount of tooling cost over the spade drill tip.
Depending on the application, we can have a range of support options for customers. Our local Sales Engineers can always assist, but they can also call on the support of a local Machining Specialist, conduct a Microsoft Teams meeting or an iPhone face time meeting with the Drilling Specialist for the region, or if it is needed, Drilling Specialists can fly out to the customer and help support the implementation process. The longer the drill becomes, like the 7 X D CoroDrill DS20, the more tricky the application can become. We do not need to pilot drill for the longer drills like the CoroDrill DS20 so stability is key to success.
SC: Research and development is valuable for innovative companies to continue to provide tooling like the CoroDrill DS20. What impressed you about the R&D team at Sandvik Coromant and how they were able to overcome challenges to be the first on the market to produce such a drill?
JH: The R&D team, while designing and creating this new drill, had 50 technical points to consider. Any time they changed even one of those technical points, let’s say like the insert seat angle, they had to adjust for the impact that this one change would have on the remaining 49. This drill took a long time to balance and many modifications had to be made to bring this drill to the market. Perhaps the most impressive part of the creation of the new CoroDrill DS20 is the direction that R&D took after the Product Specialists in the field-tested the drill and returned our feedback on its performance. Our feedback was key and instrumental in the creation of this drill. The feedback we provided could not have been as profound without the customers that allowed us to test this prototype drill in their shops on several occasions with the different revisions that we brought to them. We at Sandvik Coromant value greatly our customer partnerships, and without these partnerships, new tools like the CoroDrill DS20 cannot become reality.
machine monitoringSC: What types of additional improvements to an operation could a shop see if they were to monitor their drilling operation with software such as CoroPlus Machining Insights? And how can using a tool such as the CoroDrill DS20 can help shops be more sustainable?
JH: CoroPlus Machining Insights monitors a machine processes. This monitoring allows us to identify cutting data improvements and also find the spikes in machine loads that help to find the points where cutting edges are wearing down and can help prevent drill failure. When drilling at deeper lengths like 7 X D, CoroPlus Machining Insights can mean the difference between changing inserts that are worn out, or purchasing new drills if there are complications in the hole.
While it is easy to understand how insert drills help to keep lower inventories, what many folks may not know is that our carbide is produced using recycled carbide along with newly mined carbide. Sandvik Coromant is very concerned about the impact that mining has on our planet and the importance of using recycled materials to provide a safe, clean, and healthy planet for all generations to come. It is important to find out from your Sandvik Coromant sales team how you can recycle carbide with Sandvik Coromant to help save our environment.
SC: Bonus question: What does “Shaping the future together” mean to you?
JH: Christopher Columbus required about 10 weeks to travel from Spain to the Caribbean Islands of the Americas in 1492. Some 285 years later, in 1777, the British required 10 weeks to travel to the colonies in America. This happened because there was no change in technology. Wooden hull ships with canvas sails were the best technology available. Now, just over 240 years later, we can go from London, England to New York City in under three hours because of the advancements in technology, especially in the past 50 years. Technology will shape the future of the planet that we all share. The speed of which technology changes will never be as slow as it is today, again. Therefore, we need to adapt to changing technology as quickly as we can, to capture its full benefits and realize the cost savings that new technologies bring along in the world of manufacturing. It is my responsibility to assist our customers in grasping the new technologies that we introduce, as well as learning from our customers about what the market needs are today, and will be tomorrow. Sandvik Coromant, from our sales teams to our managers, and research and development teams, with our customers, work symbiotically to change technology, processes, and challenge what is normal today, shaping the future together.