Five Questions with Brian Schmidinger
We catch up with Brian Schmidinger, Project and Program Leader for the Mebane Production Unit (PU) in Mebane, NC and ask him some questions about being an essential business and steps in place to keep employees safe in our facilities during COVID-19, safety and sustainability initiatives and a special customer project that Brian has been working on. Brian joined the Sandvik Coromant family in 2015 as an engineer creating manufacturing process plans for engineered tools. See what he has to say in this five-minute read.
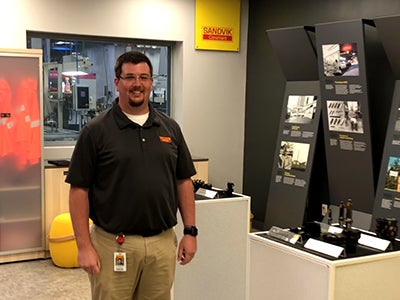
1. Sandvik Coromant: What can you tell us about theMebane Production Unit - what products are made there, how many tools areproduced per month and who uses those products?
Brian Schmidinger: The Mebane production unit islocated in Mebane, North Carolina in the United States. Our facility has beenaround since we broke ground in 1979. We are currently the onlyproduction unit manufacturing indexable tools under the Sandvik Coromant brand for the Americas region (North, Central and South America) and fully support and contribute to the overall strategy of Sandvik Coromant.
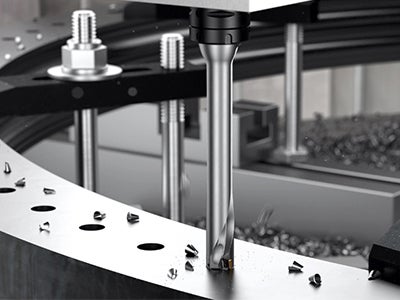
Here we manufacture indexable metal cutting toolsserving many industries such as aerospace, automotive, and generalengineering that fall into one of two product categories: standard products (froma catalog) and engineered tools (customized tools). Standard products that wemanufacture include indexable drills, including the new
CoroDrillDS20
7x deep drill, face mills, end mills, Coromant EH adaptors (or e-top holders) and boring bars. Engineered tools can varywidely in complexity and size. So the best way to describe those tools is theycan be as small as a 12mm boring bar up to a 36-inch diameter face mill, assimple as a single point turning tool or as complex as a multi-component arbormilling assembly for machining complex components such as crank or camshafts.
2. SC: What are your day-to-day responsibilities as aProject and Program Leader and can you tell us about an interesting project youare currently working on?
BS: A
s a Project and Program leader,
I am a member of our
core
management team reporting to the PU manager, Richard Boyle
, where m
y responsibilities
are to
lead
various
projects and programs for the Mebane Production Unit. My projects can vary from production improvements
and initiatives
,
utilizing and implementing
digital
tools and
analytics, lean manufacturing concepts and general project management. One of my favorite projects that began in early 2019 and is ongoing has been working with our sales and marketing colleagues to develop a customer experience program. This program enables customers to come visit the production unit, take a tour of the facility, meet our staff and operators that are responsible for manufacturing the products they use every day, and learn about our manufacturing processes. I like to point out how our attention to quality is what differentiates us from our competition.
I
am privileged for the opportunity to work with a very diverse group of people here in Mebane. Within our facility, we have colleagues that come from
many
countries
(for example
Sweden,
Brazil, China, and India
)
.
The diversity of cultures as well as
professional backgrounds such as finance, engineering, machining,
safety,
and quality
creates a great working environment where ideas are openly shared and collaboration on some of our most challenging obstacles are overcome
.
We also share diversity within our business as some
global
employees that sit here in Mebane work for different
business areas
of Sandvik or Sandvik
Coromant
from solid carbide round tools, global EHS, and R&D
.
In total, we have 130 employees that
operate
out of
Mebane. This number will only increase as we get closer to the opening of the new
Sandvik Coromant Center
that was announced late last year.
"Customer visits to our Mebane Production Unit are opportunities for Sandvik Coromant to strengthen relationships with our customers and partners to work through manufacturing challenges. As a manufacturer ourselves, we are in the unique position to understand our
customers’ challenges and our Production Units can be used a source of machining knowledge and expertise." – Brian Schmidinger
3. SC: COVID-19 has changed life as we know it. Howhas it affected the Mebane Production Unit which, as an essential business,has remained operational?
BS: Much like the rest of America, things have been constantly evolving as we navigate through this public health crisis. What has really been a great outcome has been the collaboration and forethought that everyone has contributed to changing the way we work. Our focus from day one has been minimizing risk of contracting and spreading the virus, continuing to keeping everyone safe and healthy, and to meet our customers' delivery expectations. Here in Mebane, the management team has leveraged the use of Microsoft Teams meetings to develop a robust strategy against COVID-19 without having to be in the same room, state or even country. These online meetings have occurred every day since March 9th and, as a result, we have implemented several new practices to keep everyone safe. Each day we find better ways to use digital tools like Office 365 to improve the way we work and share data while enabling employees who do not have to physically be in the building to work from home and still contribute to the success of Sandvik Coromant.
Other precautions we have enacted include providing spray bottles with diluted bleach and paper towels to wipe down frequently used items, placing hand sanitizer throughout the facility to keep hands clean when we don't have the option of soap and water, restricting access to the facility for all visitors that are not business critical requiring that body temperature be checked for all contractors and visitors that are essential to our current activities, and implementing social distancing policies. To promote and enforce social distancing, we began staggering operator breaks and lunches to reduce the number of people in our breakroom at one time, removed chairs from the break room to ensure that everyone remain six feet from each other, and moved some employees from their desks to our training center to help them spread out. The management team reviews concerns from our employees and publishes a frequently asked questions (FAQ) document to provide updates to our strategy for COVID-19. We utilize our digital information boards throughout the facility to remind everyone of best practices we should all engage in to ensure we keep everyone safe and healthy. All these activities have helped maintain a healthy work environment and take the edge off the worry surrounding COVID-19.
4. SC: What types of safety and sustainability practicesdo we have in place at the Mebane Production Unit?
BS:
We proudly stand on a very solid safety-minded culture here in Mebane. Safety is the first thing we talk about anytime we meet.
Every employee is encouraged
to bring up safety issues and
we
document them as hazards or near misses; we even look for things to make sure our offices are safe.
A
safety committee that meets monthly review
s all
hazards and near misses that have been reported and
develop
long-term solutions
to prevent these incidents from happening again.
Our safety committee is led by our EHS manager and consists of
a diverse group of employees including
operators, engineers, production leaders, managers, and even our PU manager
,
Richard Boyle.
The safety committee
also
routinely audits the entire facility to ensure
our safety
and environmental
policies
are being followed and enforced
.
Each year we host a safety week where employees
can
participate in
many activities throughout
the workday. Employees can
learn about personal safety at home and in the workplace, healthy eating and living, ergonomics, fire safety, and even participate in a live demonstration where the employee will extinguish a fire with a
real fire and
fire extinguisher.
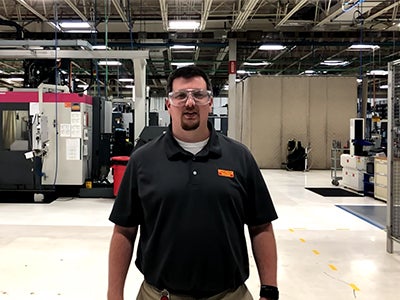
We take safety seriously because it is not just a requirement for us, it is an assurance that every employee will go home to their families the same way they came to work.
I am proud to say that we have many activities and programs here in Mebane that make our facility a sustainable business partner in our community. We proactively
review
our sustainability
approach
and work towards creating more activities each year
as new opportunities, technologies, and strategies emerge
.
We
are
consistently look
ing
for ways to minimize our impact on the environment
. Some projects we have already
impleme
nted
are
centered around reducing water, electricity, and natural gas consumption, and recycling
or
reconditioning carbide
inserts,
and solid carbide tools used in our manufacturing processes.
We partner only with suppliers and contractors that have environmental and sustainability policies that do not contradict our policies
. We also look at our most valuable
aspect of our business
,
our people
. W
e have
implemented
development programs where employees are challenged to learn new roles
and sharpen their skill sets
by giving them the tools and experiences needed to grow and develop within Sandvik
Coromant
.
One example of a cool environmental project that we have implemented is air conditioning condensate reclamation.
Since we are a machine shop, m
ost of our
equipment
use coolant diluted with water. During machining process
es,
coolant mists and evaporates into the air. Our facility is air conditioned to keep the humidity and temperature of the manufacturing environment stable (North Carolina has very unkind and humid summers)
. As the air conditioner units run, they con
densate moisture from the air.
Normally, this condensate is drained into our wastewater. However, we have implemented a simple system where the condensate water is piped into the cooling tower for the facility significantly offsetting the amount of tap water we use.
5. SC: You could say that digital machining is anotheropportunity for manufacturers to be sustainable. How does having aconnected machine shop help the Mebane PU reduce waste?
BS:
Mebane uses Sandvik
Coromant's
CoroPlus MachiningInsights
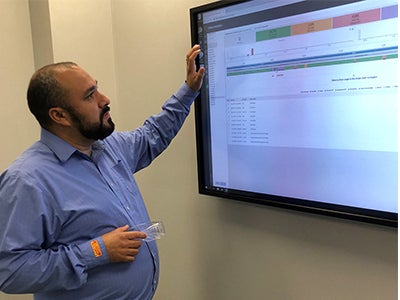
technology to monitor our 5-axis machines. We can see all
our connected
machines in one dashboard and important statistics
such as
machine uptime, utilization, current product being manufactured, current tool being used,
and
machine alarms. By connecting our machines, we have been able
see into our machining processes and identify activities of waste and underutilization. The system even has the capability to notify engineers, supervisors, or production managers when machines have sat idle for too long, when a machine has an alarm, or if there are any problems. It has also been a great tool for operators to record logs and notes for transparency for the next shift.
Bonus question: What's your favorite Sandvik Coromantcutting tool and why?
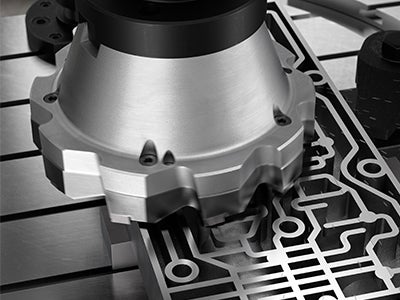
This is a hard question to answer because there are so many advanced products that Sandvik
Coromant
manufactures that are fascinating. However, m
y favorite tool that we manufacture here in Mebane
has to
be the
M5B90
. We began manufacturing
the M5B90
back in 2016. This product looks like an ordinary face
mill
;
h
owever, it functions in a totally different way.
The M5B90
acts as a “broach
ing
"
tool
for machining aluminum
components
such as automotive cylinder heads. Each carbide insert is at a different axial and radial position which enables it to machine and deburr
the workpiece
simultaneously. The manufacturing process for this product is also interesting as it is
an assembly of a
steel ring
and
an aluminum body
. This
assembly is critical in reducing the tool’s inertia allowing it to operate at
very high
rotational speeds
.