Solutions for cost effective and high-quality machining of oil and gas api seal ring grooves
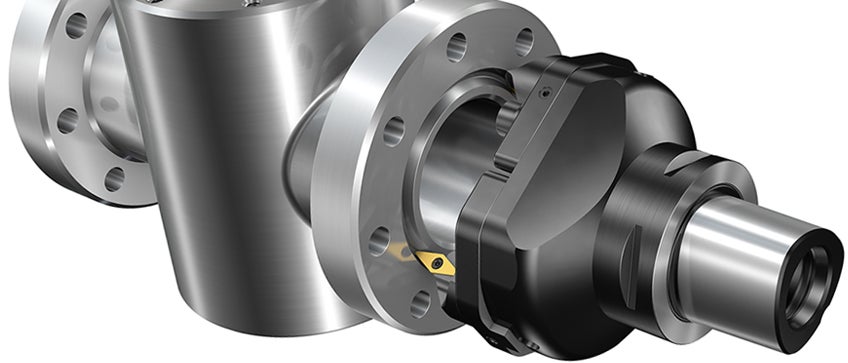
Seal ring grooves are critical features on many oil and gas components, and require close tolerances and a high-quality surface finish. The high component value and complexity make process security essential. Adding to the challenges is the common use of difficult-to-machine materials solid Inconel 718 and cladded Inconel 625.
Tooling solutions for machining of oil and gas – API seal ring grooves features
Machining challenges
Many conventional methods for machining seal ring grooves have poor process security and slow down production. Existing conventional plunging and radial turning tools need to perform roughing and finishing in multiple operations, and they involve high cutting forces with limited tool life. When secure, these processes are slow and costly with no flexibility regarding groove-diameter size.
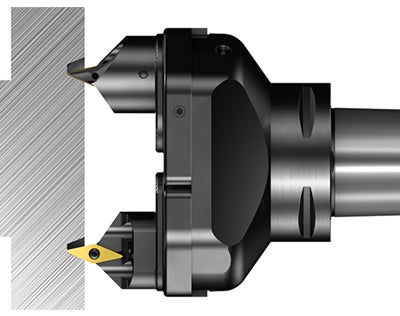
SpiroGrooving™
SpiroGrooving is a new, groundbreaking innovation – a simple yet sophisticated manufacturing process of grooves for sealing rings. The method is used with the CoroBore XL system and utilizes a spirograph tool path to create close-tolerance seal ring grooves in a very secure and productive way.
The tool path consists of tapered, circular ramping where the tool engagement is according to a set ramping-pitch for each revolution. An NC-code generator calculates the SpiroGrooving tool path based on a few input-parameters, such as groove diameter, process pitch and chosen maximum chip thickness. Tool presetting is done in a few simple steps.
This solution is ideal for making seal ring grooves in pre-clad machining of steel and stainless steel. The unique internal coolant solution of CoroBore XL facilitates machining in advanced materials. Roughing and finishing are carried out in the same operation, which significantly reduces machining time and improves productivity.
Main benefits
SpiroGrooving™ fulfils all the crucial objectives for machining seal ring grooves in the most efficient and reliable way:
- Considerably reduced cutting time through higher cutting data
- Very high process security
- Wide application flexibility with minimized tool inventory
- Quick and easy programming with the unique NC code generator tool and spindle.
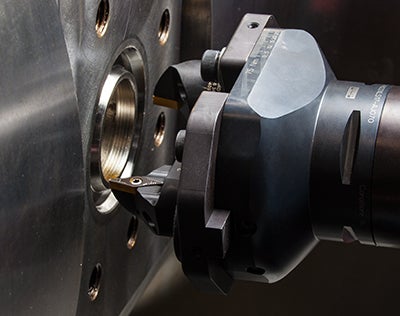
Spirograph
SpiroGrooving uses a circular spirograph tool movement in a taper. This reduces chip thickness, enabling light cutting action and increased feed. Parts of the insert cutting edge have an interrupted cutting behavior, eliminating long chips tangling with the tool and spindle.
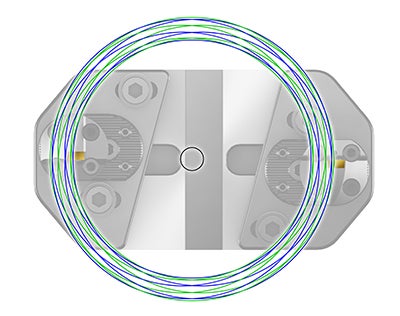
Tooling components
The tooling is based on state-of-the-art, proven standard concepts, where modularity provides broad groove-application flexibility. Where conventional methods require a new set of tools for every groove type or size, one SpiroGrooving tool covers a range of diameters, providing flexibility in production and a minimized tool inventory.
The tool for SpiroGrooving is an uncomplicated, clever twin-edge tool with two V-style inserts based on the well-established CoroBore® XL boring system. When combined with the Coromant Capto® modular tooling concept, it offers a dedicated solution for seal ring groove machining
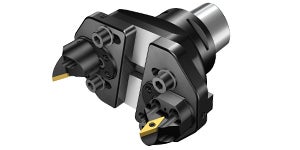
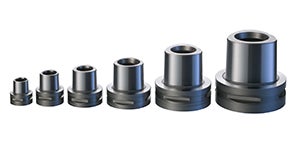
SpiroGrooving with CoroBore™ XL
Component features | BX-154 grooves in a steel valve body Diameter: 101 mm (3.99 inch) Groove width: 15.4 mm (0.606 inch) depth: 7.5 mm (0.297 inch) | |||||
vc | n | Roughing vf | Finishing vf | ap | Total time | |
Competitor seal ring groove solution | 187 m/min (614 ft/min) | 500 rpm | 100 mm/min (4 in/min) | 50 mm/min (2 in/min) | 1 mm/cycle (0.04 inch) | 2 min |
vc | n | Roughing vf | Finishing vf | Pitch | Total time | |
SpiroGrooving™ with CoroBore XL | 300 m/min (984 ft/min) | 922 rpm | 392 mm/min (15 in/min) | 50 mm/min (2 in/min) | 2 mm/rev | 50 sec |
With the conventional radial, multi-edge turning concept for roughing and finishing operations, the total machining time was two minutes. No diameter flexibility was available and setting was a relatively lengthy procedure.
After switching to SpiroGrooving™, machining time was reduced to 50 seconds. The tool can be used and easily re-set for several other groove applications. The component was finished in less than half the time with the new method.
58%
SHORTER
MACHINING
TIME