Havacılık sanayi için daha yeşil bir gelecek
OEM'lerin geleceğin uçaklarına yönelik bütüncül bir yaklaşımı benimsemesi gerekir.
Global CO2 emisyonlarına en büyük katkıda bulunanlardan biri olarak, havacılık sanayi üzerinde daha hafif ve daha uzun mesafelerde seyahat edebilen daha yeşil uçakların tedariği açısından kaçınılmaz bir baskı var. Ancak bunu başarmak için işlemesi zor alüminyum ve ısıl dirençli süper alaşımlar (HRSA'lar) ile çalışmak gerekir. Burada, Sandvik Coromant Havacılık Sanayi Çözüm Yöneticisi Sébastien Jaeger, havacılık sanayi OEM'lerinin bu tok parçaların sürdürülebilir şekilde işlenmesini sağlayan gelişmiş takımlama çözümlerini nasıl kullanabileceği hakkında bilgi veriyor.
Dünya Ekonomik Forumu (WEF)'na göre, "2050 yılına kadar net sıfır CO2 emisyon seviyesine ulaşmak, sadece çevre açısından sürdürülebilir bir geleceğin yaratılmasına yardımcı olmakla kalmayacak, aynı zamanda bir bütün olarak finansal açıdan esnek ve rekabetçi bir havacılık sanayisi de sağlayacaktır." Bununla birlikte, e-mobilite otomotiv sanayisinde giderek daha fazla yerleşik hale gelirken ve Ağustos 2021 yılında İngiltere'de elektrikli araç satışları dizel araç satışlarını geride bırakırken bu gelişmelerin havacılık sanayisinde hayata geçirilmesi daha uzun bir süre alacaktır.
Genel olarak, elektrikli uçak kullanımının 2035 yılına kadar yaygınlaşması beklenmiyor. Lonely Planet'in haberine göre easyJet'in 2030 yılına kadar 311 milin (500 km) altındaki rotalarda elektrikli uçakları kullanma beklentisine ve Norveç'in 2040 yılına kadar tüm kısa mesafeli uçuşların elektrikli uçaklarla yapılmasını hedeflemesine rağmen “şarj edilebilir jumbo jetlerle uzun mesafeli uçuşlar yakın zamanda gerçekleşmeyecek: basitçe söylemek gerekirse, aküler çok ağır.”
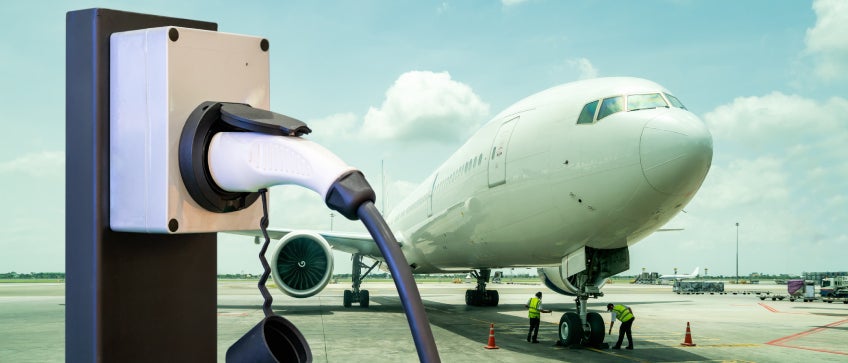
Elektrikli uçak kullanımının 2035 yılında yaygınlaşması bekleniyor.
Bu nedenle, akülerin makul olması için hafifletilmesi gerekirken, orijinal ekipman üreticilerinin (OEM'ler) omuzlarında sorunu dengelemek için daha hafif parçalar üretme konusunda giderek artan bir sorumluluk var. Bu sistemlerin daha hafif olması için alüminyumun, özellikle de yüksek mukavemete, yorulma mukavemetine ve diğer özelliklere sahip yeni alüminyum türlerinin kullanılacağından emin olabiliriz.
Yeni ısıl dirençli süper alaşımların (HRSA'lar) kullanımının da arttığını görüyoruz. Aslında, HRSA'lar yoğun ısıyla karşılaştıklarında sertliklerini korudukları için olağanüstü performans talepleriyle karşılaşılan uçak parçalarında halihazırda kullanılmaktadır. Bu malzeme özellikleri, motorların daha sert ve sıcak çalışması sürdürülebilir uçak yolculuğuna yönelik bir yaklaşım olduğundan gerekli olacaktır.
Daha dar toleranslar ile farklı tasarımlara sahip parçalar üretilmelidir. Elektrikli otomobillerde olduğu gibi, yarının elektrikli uçak tasarımları da (gövdeleri ve motorları dahil) mevcut içten yanmalı motorlu uçaklara kıyasla üreticiden üreticiye daha fazla değişiklik gösterecektir. Bazı OEM'ler, uçak gövdeleri için delta biçiminde gövde kanat ve payandalı kanat konseptlerini araştırıyor. Diğer OEM'ler ise geleneksel "büyük boru, kanatlar ve motor" tasarımlarına bağlı kalıyor.
Elektrikli, batarya ile çalışan veya elektromanyetik veya mevcut motorların elektrik gücü ile çalışan motorlar tarafından desteklendiği hibrit motorlar gibi farklı yapıda motor biçimleri de olacaktır. OEM'lerin, elektrik sistemlerin performansını etkileyen gürültü, ağırlık ve emisyonlar gibi faktörlerin azaltılması için yeni yöntemler bulmanın yanı sıra, dar toleranslar ile artan çeşitlilikte parça üretmeleri gerekecektir. Ancak alüminyum ve HRSA parçalarının işlenmesi zor olduğundan bunu sürdürülebilir bir şekilde ve uygun maliyetle başarmak zor olacaktır.
Hızlı bir şekilde ilerleme
Hafif ve yakıt açısından tasarruflu uçak üretmenin bir yolu, katkısal üretim (AM) tekniklerinin kullanılmasıdır. Katkısal üretim, çok karmaşık şekilli özel parçaların ve dar toleranslar ile fonksiyonel ürünlerin geliştirilmesine imkan tanır, böylece kafesler gibi işlenmesi zor parçalar kolayca işlenebilir. Yazılım şirketi Dassault Systemes'in tespitlerine göre, “havacılık sektöründe, katkısal üretim proseslerinin neden olduğu ağırlık azaltma maksimum yüzde 25 oranında enerji tasarrufu ile sonuçlanırken” “bir uçuşta sağlanan her kilogram (2,2 lbs) cinsinden kilo kaybı yılda 3.000 ABD doları kadar yakıt tasarrufu sağlayabilir.”
Peki katkısal üretim sürdürülebilir mi? Romanya'da bulunan Cluj-Napoca Teknik Üniversitesi İmalat Mühendisliği Bölümü tarafından yürütülen araştırmada katkısal üretim, "enjeksiyon kalıplama, kalıba döküm veya işleme gibi Geleneksel İmalat (TM) yöntemlerine harika bir alternatif" olarak tanımlanıyor. Devamında şöyle diyor: “Katkısal üretim, konvansiyonel proseslere kıyasla düşük maliyetlidir ve enerji tasarrufu sağlar.”
Katkısal üretimin ürünlerin üretim şekli ve çeşitliliği üzerinde de çok önemli etkileri olacaktır. Sağladığı avantajlar arasında karbon emisyonunun azaltılması, daha az malzeme kullanımı ve parçalar ithal edilmek yerine şirket içinde üretildiğinden daha az nakliye sayılabilir.
Ayrıca, üreticiler hızlı prototipleme yoluyla daha karmaşık, kompakt ve yenilikçi havacılık sanayi parçaları üretebilirler. Hızlı prototipleme, birkaç farklı tekniği ifade eder, ancak amaç bilgisayar destekli tasarım (CAD) dosyasından hızlı bir şekilde somut bir 3D prototip üretmektir. Bu prototiplerle, parçaların azami inovasyon ve hassasiyetle yüksek kalitede üretilmesini sağlamak için tam ölçekli üretimden önce küçük hacimli yeni malzeme denemeleri gerçekleştirilebilir.
Havacılık sanayi OEM'lerinin daha karmaşık parçaların üretiminde yeni yöntemleri nasıl kullanabileceğini inceledik. Peki özellikle tok alüminyum ve HRSA'ları işlerken, işe uygun doğru takımlara sahip olma konusunda ne düşünüyorsunuz?
Bu malzemeler, yüksek aşınma direncine ve uzun takım ömrüne sahip takımların kullanımını gerektirir. Bu nedenle Sandvik Coromant, tornalamada kullanılan çelik kesici uçlar için S205 kalitesini geliştirdi. S205 kalitesi, sıkı yapıdaki tek yönlü kristallerden oluşan Inveio® kaplama içerir. Bu, takıma mukavemet kazandırmak ve takımın mekanik özelliklerini geliştirmek için kesici ucun etrafında güçlü ve koruyucu bir engel teşkil eder. Kesici ucun motor türbin diskleri, halkalar ve şaftlar dahil olmak üzere çok sayıda uçak parçasının üretiminde faydalı olduğu zaten kanıtlanmıştır. Sandvik Coromant müşterileri, S205 kalitesi ile rakip HRSA tornalama kalitelerine kıyasla şimdiden %30 ila %50 daha yüksek kesme hızları sağladığını bildirdi.
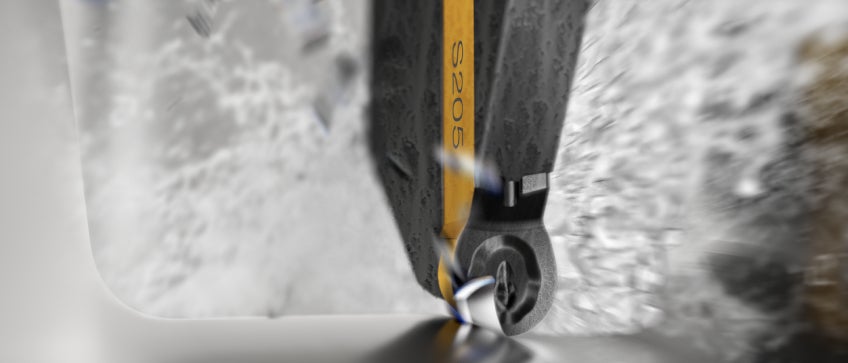
Bütüncül yaklaşım
İmalat proseslerini ve takımları ele aldık, peki bu ikisini en iyi nasıl birleştirebiliriz? Sonuç olarak, sistemler birlikte iyi çalışacak şekilde tasarlanmamışsa, tamamen entegre bir çözümü bir araya getirmek için boşa zaman harcanabilir.
Bu amaçla Sandvik Coromant, havacılık sanayisinde üretim yapan müşterilerini bir parça çözümü ile destekliyor. Çözümün, tezgah gereksinimlerine bakılması ve parça başına maliyeti incelemek üzere zaman etüdünün yapılması gibi farklı aşamaları bulunur. Aşamalardan biri de akış sırasında hem Metot-Zaman Ölçümü (MTM) hem de son kullanıcı prosesleri ile ilgili üretim yöntemlerinin analiz edilmesidir. Ayrıca, bilgisayar destekli üretim (CAM) programlama ve yerel veya yurt dışı projelerin yönetimi de parça çözümü içerisinde yer alır.
Parça çözümü, üretimde talaş kırma sorunları yaşayan bir Sandvik Coromant müşterisi için nedeni tespit ederek bir çözüm sunmamıza olanak sağladı. Sandvik Coromant'ın uzmanları, müşteri için, dinamik tahrik eğrileriyle her an talaş kırılması kontrolü sağlayan yeni bir strateji geliştirdi. Bu yeni yaklaşıma “kazançlı tornalama” adını verdik ve şimdi patentini de aldık. Müşteri, kazançlı tornalama ile üstün talaş kontrolü, iki kat daha uzun takım ömrü ve devir süresinde %80 azalma elde etti.
Dahası, müşteri güvenli işleme prosesleri ve yeşil ışıkta üretim sayesinde çok amaçlı tezgah ihtiyacını azaltarak tezgah kullanımını dörtten bire düşürdü. S205 gibi daha tok işleme kaliteleri sayesinde, düşük tezgah kullanımı ve daha az takım değişimi ile üretim çalışmalarını tamamlama özelliği, daha sürdürülebilir uçak üretiminin anahtarı olacaktır.
Sandvik Coromant'ın dijital portföyünün bir parçası olan CoroPlus® Takım Kılavuzu gibi yazılımların rolü de önemlidir. Müşteriler, üretime başlamadan önce takım seçimi ve kesme parametreleri konusunda önemli kararlar alabilir.
Döngüyü kapatma
Takım ve üretime yönelik yeni yaklaşımların dışında, havacılık sanayi OEM'leri üretime de yönelebilir. Air Transport Action Group (ATAG) tarafından hazırlanan bir rapora göre Kaiser (Boeing'e alüminyum tedarik eden şirket), şu anda sektörde türünün en büyük programlarından biri olan bir kapalı döngü geri dönüştürme sistemini kullanıyor. Kaiser'e göre, program sayesinde her yıl yaklaşık on milyon kilogram kesilmiş ve hurda metal sanayi tarafından yeniden kullanılacak.
Sandvik Coromant olarak karbür takımların geri dönüşümüne yönelik kendi döngüsel sistemimizi başlattık. Müşterilerimizin aşınmış karbür takımlarını geri alıyor ve onları yepyeni takımlara dönüştürüyoruz. Sonuç olarak, Sandvik Coromant'ın semente karbür takımlarında kullanılan ham malzemelerin çoğu hurdadan gelmektedir. Sınırlı kaynakların bulunduğu bir ortamda sürdürülebilir iş faaliyetleri gerçekleştiriyor ve aşırı israfı en aza indiriyoruz. Bunu yaparak, takımların üretiminde geri dönüştürülmüş malzemelerin kullanılması ile %70 enerji tasarrufu sağlanırken karbondioksit emisyonu salınımının %40 azaldığını tespit ettik.
Havacılık sanayi üzerinde daha hafif ve daha uzun mesafelerde seyahat eden daha yeşil uçaklar üretmesine yönelik artan bir baskı var. Ancak, yerinde kullanılan doğru prosesler ve takımlar (buna ek olarak üretime yönelik daha bütünsel bir yaklaşım) ile havacılık sanayi OEM'leri, üzerine düşeni yaparak havacılık sanayi için daha yeşil bir gelecek oluşturmaya yardımcı olabilir.