Jak Internet Rzeczy (IoT) wspiera działania proekologiczne
Organizacja GSMA (Groupe Speciale Mobile Association) wzywa liderów przemysłu do zwiększenia wykorzystania inteligentnych technologii w wyścigu o osiągnięcie neutralności klimatycznej i przewiduje, że podjęcie takich działań może przyczynić się do wymaganej redukcji światowych emisji gazów cieplarnianych na poziomie do 40%. Zastosowanie inteligentnych technologii w celu zmniejszenia zużycia energii nie jest nowym rozwiązaniem w sektorze produkcji, ale wyzwania związane z wdrożeniem tych technologii w zakładach produkcyjnych od dawna są barierą dla ich upowszechnienia. W artykule Jörgen Friesendahl, Global Offer Manager ds. obróbki opartej na danych w Sandvik Coromant, udziela rad firmom z branży obróbki skrawaniem metali na temat wdrożenia rozwiązań dla inteligentnej fabryki – z myślą o redukcji emisji związków węgla, jak i zwiększeniu zysków.
W swoich badaniach dotyczących Internetu Rzeczy (IoT) i zmniejszenia emisji dwutlenku węgla organizacja GSMA oszacowała, że w sferze produkcji 16% redukcji emisji związków węgla wymaganej do osiągnięcia poziomu zerowego netto można uzyskać dzięki zastosowaniu inteligentnych procesów produkcyjnych. Wartości tej odpowiada 1,4 gigatony CO2 lub emisje ze 140 milionów samochodów.
Biorąc pod uwagę te uderzające liczby, nasuwa się pytanie, dlaczego w sektorze, który pierwszy ukuł termin Przemysł 4.0 już ponad 10 lat temu, inteligentne technologie nie zostały powszechnie wprowadzone? Co więcej, według doniesień zaledwie 1% sektora produkcji wykorzystuje obecnie technologie połączone.
Najczęściej spotykaną barierą dla upowszechnienia inteligentnych technologii w sektorze produkcji jest brak zrozumienia, jak łatwo narzędzia te mogą być wdrożone. Gdy sięgniemy myślą do początków idei Przemysłu 4.0 – kiedy nazwa ta pojawiła się pierwotnie podczas niemieckich targów Hannover Messe w 2011 r. – inteligentne fabryki uważane były za futurystyczne obiekty w niczym nie przypominające prawdziwych zakładów produkcyjnych. Dzisiaj rozumiemy, że ucyfrowienie nie wymaga całkowitej transformacji zakładu, lecz jest częściej wprowadzane stopniowo w oparciu o skalowalne technologie IoT i wielkie zbiory danych.
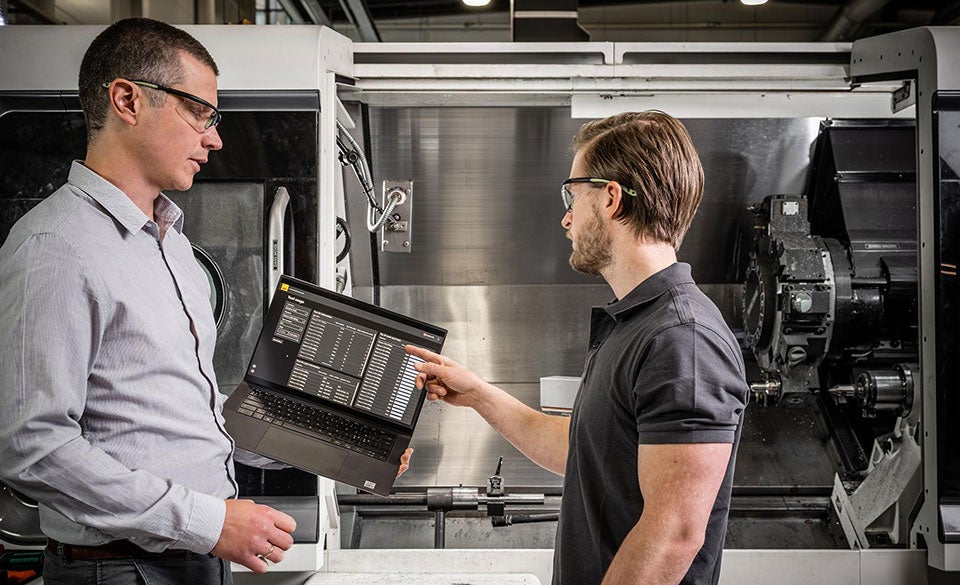
Pozyskiwanie danych z wykorzystaniem Internetu Rzeczy
Każdy obiekt produkcyjny generuje każdego dnia, świadomie lub nie, olbrzymie ilości danych. Dane są bez wątpienia najcenniejszym zasobem, po który mogą sięgnąć producenci starający się ograniczyć emisję związków węgla. Wielu producentów jednak nie wykorzystuje optymalnie tego zasobu. Jak producenci mogą rozpocząć działania zmierzające do zmniejszenia zużycia energii bez dostępu do zbieranych w całym obiekcie danych pokazujących, gdzie energia jest wykorzystywana i w jakiej ilości?
Rozpowszechnione jest błędne przekonanie, że całe wyposażenie musi być inteligentne, aby możliwe było skuteczne generowanie danych. W rzeczywistości nawet zakłady działające w oparciu o starsze, ponad dziesięcioletnie maszyny mają możliwość zbierania danych z linii produkcyjnych, a ludzie przemysłu wiedzą, że takie obiekty są dużo powszechniejsze niż futurystyczne inteligentne fabryki, których wizje zaprezentowano w Hanowerze w 2011 r. Może to wymagać połączenia czujników i inteligentnego oprogramowania – w zależności od takich czynników jak wiek urządzeń i oryginalny producent sprzętu (OEM) oraz wykorzystywane protokoły komunikacyjne – ale jest to możliwe.
Zyskanie wglądu w zużycie energii w zakładzie jest niezbędne do ustalenia punktów krytycznych. Może się okazać, że niewielkie modyfikacje w kilku obszarach produkcji mogą zaowocować znaczną redukcją emisji związków węgla. Możliwe jest jednak także, że indywidualne elementy wyposażenia będą oferować największe możliwości poprawy. Zbieranie danych z tych obszarów jest kluczowe dla obniżenia zużycia energii przez poszczególne maszyny, a producenci mogą wykorzystać do tego różne dostępne technologie.
Jednym z takim rozwiązań jest pakiet CoroPlus® z oferty produktów firmy Sandvik Coromant do obróbki opartej na danych. Produkty te mają pomóc przedsiębiorstwom produkcyjnym zwiększyć wydajność procesów obróbki skrawaniem metali.
Podstawowym celem narzędzia CoroPlus® Process Control jest zmniejszenie zużycia przez redukcję odpadów materiału. Narzędzie monitoruje maszyny w czasie rzeczywistym i może aktywować działania według zaprogramowanych protokołów. Wyobraźmy sobie, że w maszynie wystąpi określony wcześniej problem. Technologia CoroPlus® Process Control automatycznie uruchomi działanie naprawcze, np. zatrzymanie maszyny w celu zapobieżenia dalszym stratom. Oprócz tego wykazano, że przeprowadzanie konserwacji z wykorzystaniem tej technologii może podnieść efektywność operacyjną aż o 89%.
Energia i ekonomika
Biorąc pod uwagę problemy i straty, z jakimi zmagali się producenci w czasie pandemii COVID-19, czy istnieje ryzyko, że redukcja emisji związków węgla stanie się sprawą drugorzędną, gdyż pierwsze miejsce zajmie generowanie zysków potrzebnych do nadrobienia strat? 49% członków kadry kierowniczej biorących udział w ankiecie firmy Accenture na temat komercyjnego przemysłu lotniczego (Accenture Commercial Aerospace Insight Report) przewiduje, że przemysł lotniczy potrzebuje do trzech lat, aby jego kondycja wróciła do poziomu z roku 2019. Podobnie też przemysł motoryzacyjny odnotował spadek sprzedaży pojazdów w niemal każdym kraju.
To prawda, że inwestując w nowe narzędzia i procesy obróbki, należy zawsze uwzględnić ekonomikę produkcji. Jednak właściwe technologie mogą prowadzić jednocześnie do wzrostu zysków i obniżenia zużycia energii.
System CoroPlus® Machining Insights, na przykład, służy do wykorzystywania pozyskiwanych danych w czasie rzeczywistym w celu optymalizacji narzędzi. W ten sposób zwiększa zarazem wydajność i zysk. W zakładzie obróbki skrawaniem metali technologia ta może zapewnić natychmiastowy dostęp do danych o konkretnej maszynie, aby operatorzy mogli monitorować całkowitą efektywność sprzętu (ang. overall equipment effectiveness – OEE) i wyniki pracy. W rezultacie taki nadzór prowadzi do wydajniejszego działania i większej rentowności zakładu produkcyjnego.
Od pojawienia się terminu Przemysł 4.0 minęło już ponad 10 lat i wyrażenie to weszło na stałe do słownictwa produkcyjnego. Jednak badania sugerują, że pomimo imponujących możliwości oszczędzania energii związanych z tą technologią wielu producentów nie wykorzystuje tych narzędzi. Aby osiągnąć cele dotyczące zmniejszenia światowych emisji związków węgla, producenci muszą podjąć świadome działania prowadzące do redukcji zużycia energii. Zespół Sandvik Coromant stara się pomóc klientom skutecznie wdrażać takie narzędzia z korzyścią dla ludzi, zysku i planety.
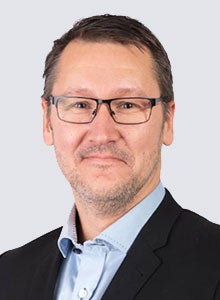
Jörgen Friesendahl
Global Offer Manager for data driven machining at Sandvik Coromant
Has over 30 years’ of experience in the world of metal cutting, mainly within product management, R&D and sales.