Hoe de bewerking van aluminium in de automotive industrie te optimaliseren
Met het toenemende gebruik in de automotive sector van motor-, aandrijflijn- waterpomp- en remsysteemonderdelen vervaardigd uit aluminium , is het voor OEM's en hun partners in de toeleveringsketen een uitdaging om productievere freesbewerkingen te leveren. Gereedschapsselectie vormt de sleutel tot werkelijke marktdifferentiatie in dit segment, waar de correcte toepassing van geoptimaliseerde frezen over het hele scala van bewerkingen van motorcomponenten significante voordelen kan opleveren.
Het aantal geproduceerde aluminium motoren blijft jaar op jaar stijgen, zowel voor conventionele als hybride personenwagens. Er worden er nu zelfs bijna 100 miljoen per jaar geproduceerd. Deze motoren bevatten onderdelen die vaak een complexe vorm hebben en die en na het gieten een opeenvolging van gevarieerde maar essentiële freesbewerkingen vereisen.
Sandvik Coromant heeft nu een compleet aanbod voor het bewerken van aluminium in de automotive industrie, van eerste fase cubing (eerste bewerking op oppervlakken na het gieten), via voorbewerken, semi-nabewerken tot nabewerken. Elk speciaal ontworpen freesgereedschap, vijf in totaal, is ontworpen voor het leveren van geoptimaliseerde kwaliteit en kosten per onderdeel. Om het laatste te realiseren, vervullen bepaalde gereedschappen in het assortiment een combinatie van taken, zoals zowel voorbewerken als nabewerken, in één enkele bewerking, teneinde de cyclustijden te verkorten.
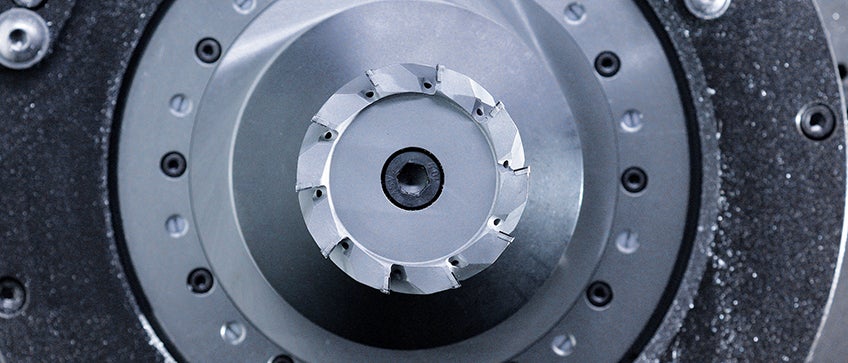
Een goed voorbeeld hiervan is de M5C90, een innovatieve frees die voorbewerken en semi-nabewerken combineert in één gereedschap. De M5C90 is een vlakfreesgereedschap voor hoge snelheid dat op maat is gemaakt om lange insteltijden op de locatie van de klant te elimineren. M5C90 werkt met een gereduceerd aantal tanden vergeleken met conventionele frezen, voornamelijk als resultaat van unieke radiale en axiale wisselplaatpositionering op haar nabewerkingsrij/binnendiameter (er is geen wisselplaatinstelling vereist). Deze positionering staat garant voor frezen zonder bramen en een optimale oppervlakte-afwerking van cilinderkoppen, cilinderblokken, remsystemen en alle aluminium componenten waar een brede freesaangrijping kan worden gerealiseerd (niet van toepassing op dunne wanddelen).
Bekijk, om een voorbeeld te geven van de potentiële winst die geboden kan worden door gebruik te maken van de M5C90, een nog lopend praktijkvoorbeeld waarbij een klep van een remsysteembehuizing gemaakt van AlSi12Cu1 is betrokken. Met een uitwendige diameterreeks van 10 hardmetalen wisselplaten en een binnendiameter van vier wisselplaten (plus één wiperwisselplaat), wordt het gereedschap ingezet met een spiltoerental van 8000 tpm, een snijsnelheid van 4021 m/min (13,192 ft/min) en een voeding van 0,25 mm/tand (0.009 in/tand). Daarnaast is de axiale snedediepte 2 mm (0.078 in) bij een radiale snedediepte van 140 mm (5.51 in), hetgeen resulteert in een verspaningsvolume van 5600 cm3/min (342 in3/min). Hoewel de totale standtijd nog bepaald moet worden, bevindt hetzelfde gereedschap zich na 18 maanden gebruik nog steeds in de machine .
Voor diegenen die een frees nodig hebben die ook dunwandige aluminium componenten kan nabewerken zoals tandwielkasten en behuizingen, heeft Sandvik Coromant een andere frees die net zo effectief is, de M5F90. De M5F90 is eveneens een "one-shot" voorbewerkings- en nabewerkingsgereedschap. Specifiel voor het bewerken van dunwandige aluminium componenten en kleine vlakfeesbewerkingen, is het freeslichaam (25-80 mm, 0.98 – 3.15 inch in diameter) voorzien van hardgesoldeerde PCD-punten. Elke punt heeft zowel een voorbewerkingssnijkant als een nabewerkingssnijkant. Het voorbewerkingsgebied werkt als een conventioneel freesgereedschap, met alle snijkanten op dezelfde diameter en hoogte, terwijl het nabewerkingsvlak bestaat uit radiale en axiale getrapte snijkanten. Dit concept maakt een dichte vertanding mogelijk, voor het leveren van een braamvrije bewerking en uitstekende oppervlaktewaarde.
Indrukwekkende tijdsbesparingen zijn mogelijk, zoals gezien in een praktijkgeval waarbij er sprake was van het vlakfrezen van een aluminium (hoog Si-gehalte) cilinderkop. Hier betekende het gebruik van de M5F90 vergeleken met een speciale PCD frees van een concurrent niet alleen een besparing van 150% op de cyclustijd, maar het elimineerde ook het genereren van bramen. Snijgegevens inbegrepen: 15.915 tpm spiltoerental; 2000 m/min (6562 ft/min) snijsnelheid; een voedingssnelheid van 0.16 mm/tand (0.006 in/tand); en 1,5 mm (0.06 inch) snedediepte.
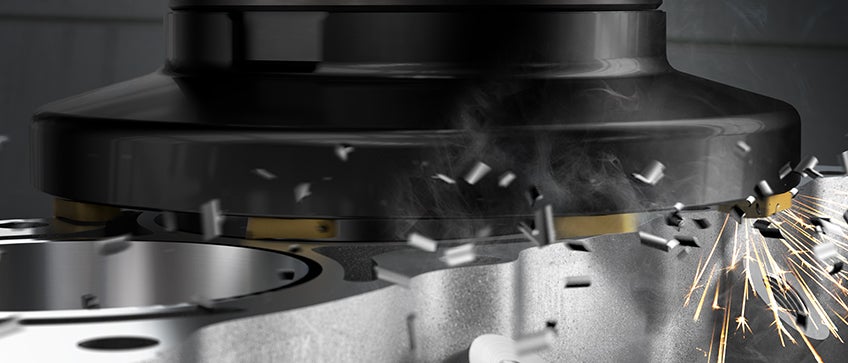
In een ander M5F90-voorbeeld werden cyclustijdreducties van 44% gerealiseerd op een aluminium kettingbehuizing in vergelijking met het gebruik van een frees van een concurrent van 63 mm (2.48 inch) diameter wisselplaatfrees met zes PCD wisselplaten. Bovendien elimineerde de oplossing een eerder nog noodzakelijke ontbramingsbewerking.
Een ander nieuw speciaal ontworpen gereedschap is ontwikkeld om het bovenvlak van motorcilinderblokken te frezen met bimetalen interfaces, typisch aluminium en grijs gietijzer (CGI).
Een scala van thermische en mechanische eigenschappen maakt het frezen van bimetaal materialen uitdagend. Bestaande frezen voor deze toepassing zijn complex en vereisen instelling, hetgeen resulteert in lagere doorvoerwaarden. Daarnaast veroorzaken dergelijke gereedschappen vaak uitbrokkeling op de GCI-gedeelten van het component.
De M610 daarentegen vereist geen configuratie en instelling, en resulteert in de mogelijkheid om hoge voedingswaarden toe te passen, zonder uitbreking, braamvorming of krassen van werkstukken. Deze functionaliteit is belangrijk omdat onvolkomenheden aan het oppervlak het potentieel hebben te leiden tot lekkage tussen het cilinderblok en de kop, hetgeen op haar beurt weer het vermogen en de prestaties aantast. Sommige wereldwijde automotive OEM’s profiteren al van de invoering van de M610.
Om er één specifieke klant uit te lichten, er werd een enorm concurrentievoordeel bereikt bij het nabewerken van het verbrandingsvlak op bi-metalen motorblokken. In vergelijking met een instelbare frees met cassettes van een concurrent, realiseerde de M610 een verbetering van de standtijd van 833%, waarbij meer dan 4000 werkstukken werden voltooid, vergeleken met de 480 welke werden vervaardigd met de frees van de concurrent. Daarnaast presteerde de M610 bij 10 maal de snelheid. Snijgegevens voor de 15-wisselplaat M610 omvatte: 3000 m/min (9843 ft/min) snijsnelheid; een voedingssnelheid van 5720 mm/min (225 in/min); een spiltoerental van 3820 tpm; een voedingssnelheid van 0,15 mm/tand (0.006 in/tand); en een snedediepte in aluminium van 0,5 mm (0.02 inch) en in gietijzer van 0,05 mm (0.002 inch).
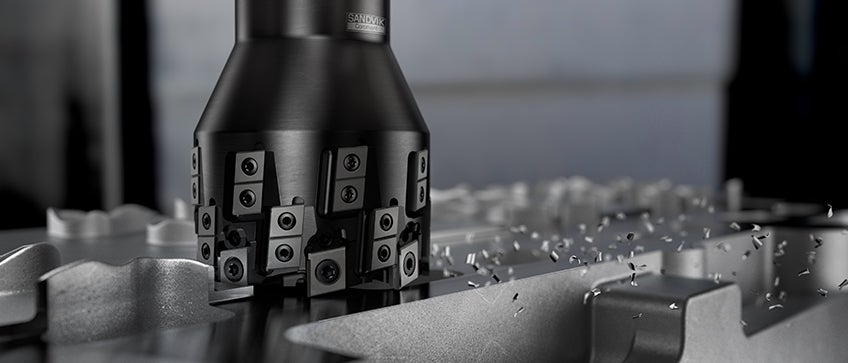
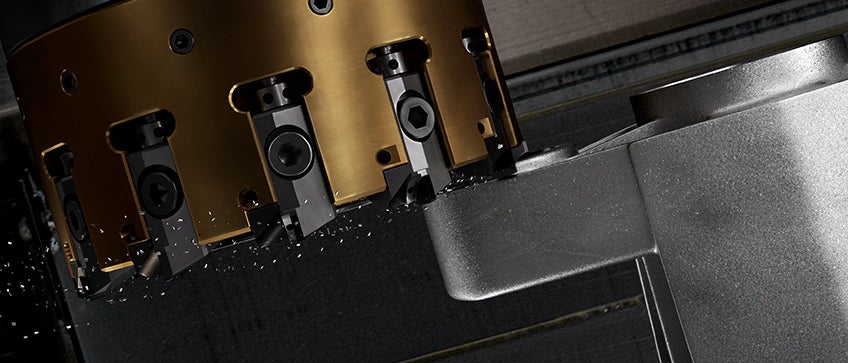
Andere gereedschappen in de familie omvatten de M5Q90 tangentiale voorbewerkingsfrees, die de eerste fase cubing uitvoert (eerste bewerking op oppervlakken na het gieten) in één enkele bewerking zonder braamvorming. Het gereedschap is uitgerust met PCD tangentiële wisselplaten die zorgen voor een soepele en stabiele snijwerking om het energieverbruik te verminderen en trillingen te elimineren.
Aluminium cilinderkoppen en blokken zijn onder andere componenten die profiteren van de M5Q90. De cubing-bewerking bijvoorbeeld op een gegoten cilinderkop zou typisch het bewerken van het nokkenasvlak, het inlaat/uitlaatvlak en het verbrandingsvlak omvatten. In een casestudy bij een klant leverde het ruw vlakfrezen van cilinderkoppen gegoten uit AS-9 aluminiumlegering op een horizontaal bewerkingscentrum zeer indrukwekkende standtijdresulaten op. Bij 3000 m/min (9843 in/min) snijsnelheid, een voeding per tand van 0,2 mm (0.008 in) en 2,0 mm (0.079 in) axiale snedediepte (volledig aangegrepen tot 40 mm (1.57 in), werden meer dan 10,000 componenten voltooid.
Een ander gereedschap is de M5R90 voor tweede fase voorbewerken / semi-nabewerken. Deze standaard frees werkt met instelbare cassettes en ondersteunt een snedediepte van maximaal 8 mm (0.315 inch) met een 0.4 of 0.8 mm (0.016 of 0.031 inch) radius afhankelijk van de gebruikte cassette. Gemakkelijk in te stellen cassettes zijn een voordeel in vele automotive toepassingen, zoals duidelijk werd in een recente test bij een klant bij het vlakfrezen van een motorafdekking. Gegoten uit een MRHB Si12 aluminiumlegering, presteerde de M5R90 bijzonder goed vergeleken met de huidige frees van een concurrent. Op basis van identieke snijgegevens, verlengde de M5R90 de standtijd van 8000 tot 10.000 werkstukken. Daarnaast moest de frees van de concurrent na elke 1000 werkstukken worden afgesteld als gevolg van cassettebeweging die nadelig was voor de oppervlakte-afwerking. De M5R90 daarentegen, produceerde 8000 werkstukken voordat enige afstelling aan de cassette nodig was.
Ook inbegrepen in de familie is de M5B90 vlakfrees voor super-nabewerken met zijn unieke axiale en radiale positionering van wisselplaten. Deze configuratie, samen met de wiperwisselplaat, zorgt voor braamvrij verspanen met een uitstekende oppervlaktekwaliteit zoals een fabrikant van cilinderkoppen voor personenauto's recent ontdekte. Het bedrijf had last van procesinstabiliteit en problemen met bramen, terwijl een ander probleem de onvoorspelbare standtijd van de wisselplaat was, afhankelijke van de cassette-instellingen die verschilden per configuratie. Het overschakelen naar de M5B90 frees bood een soepele nabewerking met een voorspelbare slijtage en geen braamvorming. Het gereedschap produceerde alleen hele dunne spanen, welke gemakkelijk worden verwijderd tijdens het verspaningsproces om eventuele beschadiging van het componentvlak te voorkomen. Daarnaast werd de standtijd door over te schakelen op de M5B90 gemiddeld verlengd van 30.000 tot 45.000 componenten.
De CoroDrill® en CoroTap® familie van boor- en tapgereedschappen kunnen aan klanten worden aangeboden als onderdeel van dezelfde familie van oplossingen voor het bewerken van aluminium automotive componenten, net als de standaard CoroMill® Century 590 vlakfrees.
In alle gevallen is het potentieel om cyclustijden en kosten per component te reduceren en tegelijkertijd de standtijd en de kwaliteit van het gereedschap te verbeteren zeer realistisch, zoals te zien is in de beschreven praktijkgevallen bij klanten. In de automotive industrie, waar grote productievolumes de overhand hebben, kan zelfs een kleine besparing in de cyclustijd significantie financiële voordelen betekenen. Met deze gedachte in het achterhoofd, is elke technologie die de mogelijkheid kan aantonen om grotere verbeteringen te leveren, moeilijk te negeren.