Hogyan készítettük
Így készítette el a Sandvik a világ első 3D-nyomtatott, törésbiztos gitárját
A rocksztárok – élükön a gitárvirtuóz Yngwie Malmsteennel – évtizedek óta előszeretettel törik ripityára gitárjaikat a színpadon. A Sandvik úgy döntött, hogy csúcstechnológiás megoldásainak tesztelése érdekében elkészíti a világ első, kizárólag fémet tartalmazó, törhetetlen gitárját, melyen Malmsteen igazán próbára teheti gitártörési képességét.
A Sandvik összehívta szakértőit a vállalat különböző területeiről, hogy bemutassa, hogyan alkalmaznak mérnökei fenntartható, csúcstechnológiás technikákat a rendkívül precíz és elképesztően tartós eredményért.
„Fejlett anyagok, precíziós megmunkálás, additív gyártás, adatközpontú termelés – ilyen megoldások szükségesek, ha profi zenészeknek szeretnénk bonyolult és szép gitárt készíteni” – fogalmaz Klas Forsström, a Sandvik Machining Solutions elnöke. „De azt is szerettük volna megmutatni, hogy képesek vagyunk olyan törhetetlen hangszert gyártani, amelynek tönkretételéhez még Yngwie elszántsága is kevés. Ezt a projektet pont cégünk és Yngwie szakértelméhez és képességeihez találták ki.”
Együttműködés a kezdetektől
Hónapokkal a floridai koncert előtt a Sandvik Svédországban összehívta a cég különböző területein – anyagok, megmunkálás, additív gyártás – dolgozó szakértőket, hogy együtt gondolkodjanak a lehetséges megoldásokon.
A Sandvik korábban nem foglalkozott gitárokkal, ezért segítségül hívta a jól ismert brit gitárkészítő céget, a Drewman Guitars-t. „Teljes körű innovációra volt szükség” – kezdi Andy Holt, a Drewman tervezője. „Azt akartuk, hogy a zenészek elképedve mondják, ilyen hangszert még sosem láttak.”
Holt elmondása szerint volt olyan időszak a fejlesztés során, amikor minden egyes nap új digitális tervfájlt küldött a Sandvik mérnökeinek. Végül a gitárkészítő céggel szoros együttműködésben olyat alkottak, amely mindkét fél szerint a technológiai kreativitás mesterműve.
A világ első törésbiztos gitárja
Henrik Loikkanen, a Sandvik Coromant megmunkálási folyamatfejlesztője fiatalon kezdett gitározni, és példaképe Malmsteen volt. Azonban egyetlen hangszert sem tört össze („túl drága mulatság lenne” – mondja). Ezért a YouTube-on kellett megnéznie, mi történik, amikor Malmsteen összetör egy gitárt.
„Olyan gitárt kellett terveznünk, amely törhetetlen, bárhogy is próbáljuk összetörni” – folytatja Loikkanen. „A mérnöki kihívást a hangszer nyaka és teste közötti kritikus rész jelentette, amely általában először reped el a gitáron.” Ezért a Sandvik Coromant mérnökei úgy döntöttek, hogy megszüntetik ezt a részt. A nyakat és a fogólapot is meghosszabbították egy négyszögletes agy formájában, amely mélyen benyúlik a gitártestbe.
Kagylósított fogólapon Yngwie biztosabban tudja lefogni a hangokat, ezért a mérnököknek hosszú és sima íveket kellett metszeniük a bundok közé. Annak érdekében, hogy a gitár a lehető legkönnyebb legyen, a Sandvik Coromant kivájta a nyak és a fogólap belsejét.
„A bundok magasságának tökéletesen egyformának kell lennie, hogy ne hallatszódjon, amikor a húrok a bundhoz érnek” – magyarázza Loikkanen.
Forgácsolóél-adatok
Az olyan hosszú és vékony darabok, mint a fogólap és a nyak különösen hajlamosak a deformációra a megmunkálás során. A fejlett szoftvernek köszönhetően a Sandvik Coromant digitális úton szimulálta a feladatot a tényleges forgácsolás előtt.
„A pontosság kritikus fontosságú” – magyarázza Henrik Loikkanen. „Szoftverünk mögött sok évnyi tapasztalat áll. A szerszámokra és forgácsolási adatokra vonatkozó javaslatok segítségével a fogólapot bizonyos helyeken sikerült mindössze egy milliméteres vastagságúra marni.”
Ráadásul az automatizált folyamattal a fogólap marásához egyetlen gép is elegendő volt. A folyamat 90 műveletből állt, melyek során nem kellett leállítani a gépet új szerszámok vagy vágások beállításához.
„Betesszük a nyers alapanyagot, és kijön a kész darab” – magyarázza Loikkanen. „Ez az anyagleválasztás okosabb módja. A ciklusidő csökken, a gyártás olcsóbb.”
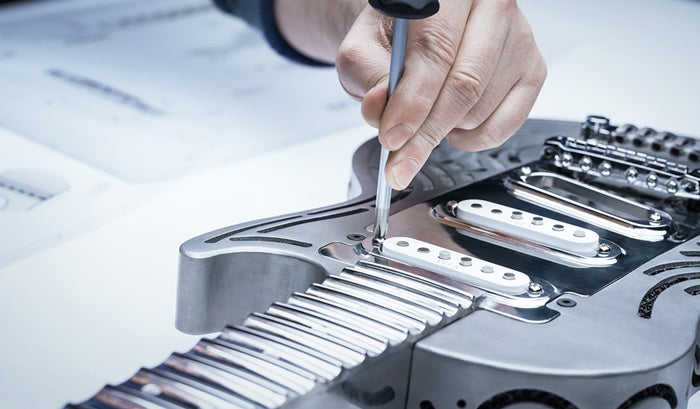
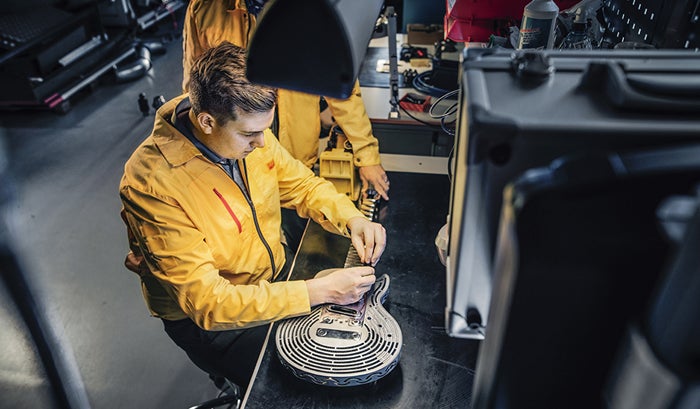
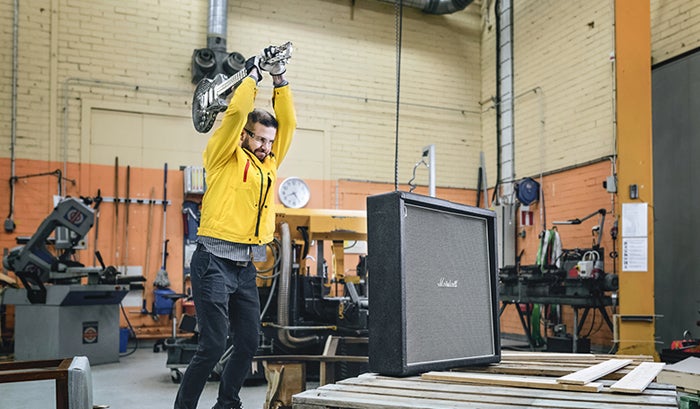
A mérnökök által előállított mindegyik prototípus könnyebb lett az előző változatnál, míg végül elkészült a gitár. A finom forgácsolást végző CoroMill® szerszámok csodálatosan sima és csillogó fémfelületet hoztak létre.
Loikkanen szerint a törésbiztos gitár létrehozásának kulcsa a Sandvik különböző részlegei közötti együttműködés volt. Támogatta a Sandvik additív megmunkálási területét a gitártest és a kisebb alkatrészek felületének marásában, amelyek mind 3D nyomtatással, titánból készültek. A Sandvik Coromant emellett együttműködött a Sandvik anyagtechnológia területével az alkatrészekhez használt acél kiválasztásában, valamint egy hiperduplex rácsszerkezet nyakba történő építésében. Elmondása szerint ez a csapatmunka volt a gitárkészítési folyamat valódi célja.
„A Sandvik Coromant híres arról, hogy összetett feladatok terén segíti ügyfeleit – nemcsak szerszámokkal, hanem olyan megoldások kidolgozásában is, amelyekkel a szerszámok ideálisan alkalmazhatók a konkrét folyamatokban” – fogalmaz Loikkanen.