Solid carbide round tool reconditioning
How to order tool reconditioning

1. Order shipping box
Send an e-mail to Sandvik Coromant to order a tool transportation box.
Notify us what size box you require:
- Standard box (300 mm x 200 mm x 138 mm), Article number: 6949557
- Large box (400 mm x 300 mm x 138 mm), Article number: 6949558
2. Select tools
Identify the worn tools that you want to recondition. Use the tool wear guide to ensure that the tools are eligible for reconditioning.
The minimum quantity for ordering the reconditioning service is five tools. The service is only available for Sandvik Coromant tools.
3. Pack carefully
The box is delivered to you with foam inlays to secure that your tools will be protected during transportation.
Follow the packing instructions to avoid chipping and breakage.
4. Ship
Sandvik Coromant will provide shipping information based on your request.
When reconditioning has been completed, we will ship the tools back to you.
Questions and answers
Will all tools that I send be reconditioned?
A technical inspection will determine which tools are suitable for reconditioning. Tools that cannot be regenerated will be returned, marked with red tape.
How long does reconditioning take?
Expect your reconditioned tools to be delivered back within four weeks after shipping to us. A delivery confirmation with exact dispatch time will be sent to you within two weeks.
How can I track the number of times my tools have been reconditioned?
A laser mark on the tool shank indicates each reconditioning service performed.
A tool’s maximum number of regrinding (NORGMX) is available by entering the tool’s product number in the search bar on the Sandvik Coromant website.
Restoring original quality
The tool reconditioning process restores worn solid carbide drills and end mills to their original quality and prolongs their total lifecycle. Reconditioning increases manufacturing’s utilization of raw material and at the same time decreases your cutting tool costs.
Restore your tools to original quality and prolong their total lifecycle
By incorporating a process into the designing of our tools which allows exact copying in a future reconditioning we can guarantee new tool performance. The reconditioning process will reproduce geometry and coating of the original tool. The performance testing of reconditioned tools follows the same process as for new tools.
The graph below illustrates the cost of buying four new tools ( I ) compared to buying one tool and reconditioning it three times ( II ). The result is savings up to 50%.
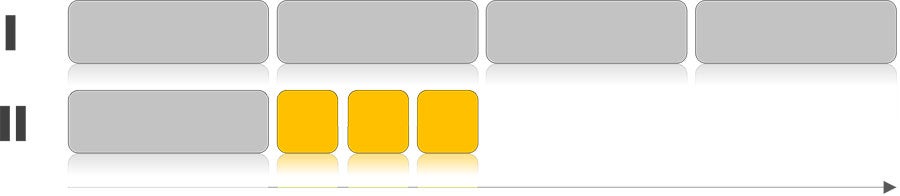
Total tool cost
Available for reconditioning
The following tools can be reconditioned:
How to pack for reconditioning
To avoid damaging your tools in transportation, follow these instructions:
- Use the tool’s original plastic packing to avoid tools hitting each other.
- If the original packaging is not available, use bubble wrap or similar that you have on hand.
- Place all tools in-between the two foam inlays that comes with the shipping box.
Click the image to enlarge
Recycling
At the end of the solid carbide tool’s lifecycle, please consider the Sandvik Coromant buy-back program. Your solid carbide will be recycled and used to create new tools. Read more about carbide recycling.
Find new Solid Round Tools
If you are looking for new tools, visit our Solid Round Tools section.
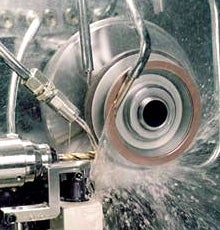
Identify tool wear
Use the guide below to identify your tools’ wear type.
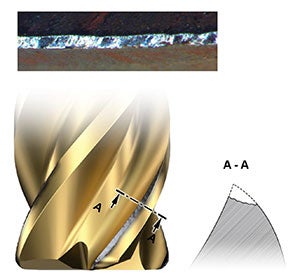
Uniform flank wear
One of the most common wear types (typical for dry ISO-P). Usually starts on the cutting edge and develops more towards the flank side of cutting edge.
Main wear mechanism - abrasive
Cause:
- High cutting speed and low feed
- Low wear resistance
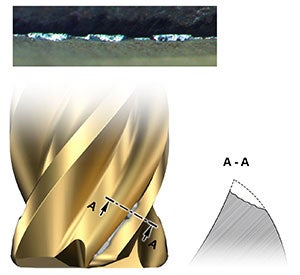
Non-uniform flank wear
Initially, some parts of the cutting edge are worn faster than others.
Main wear mechanism - partial flaking of coating and irregular micro-chipping on the cutting edge followed by abrasive wear.
Cause:
- High cutting speed and low feed
- Vibrations
- Low wear resistance
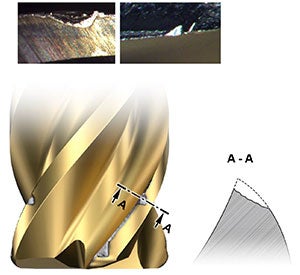
Localized flank wear
Usually on tool corners and/or at maximum depth of cut.
Main wear mechanisms - adhesive, thermomechanical or chemical.
Cause:
- High temperature
- Vibrations
- Chip re-cutting
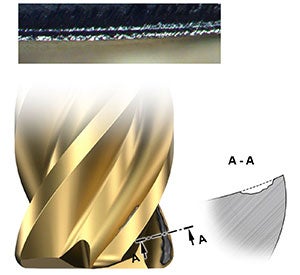
Crater wear
Rarely seen on solid end mills.
Main wear mechanisms – chemical and abrasive.
Cause:
- High temperature (high cutting speed)
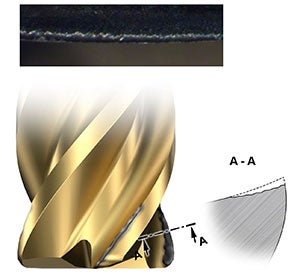
Stair-formed face wear
Usually occurs when flood (low pressure) coolant is supplied through external nozzles.
Main wear mechanism – chemical
Cause:
- High temperature
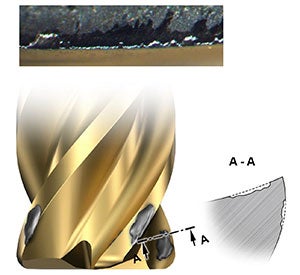
Flaking
Usually when milling materials which are easily smearing to the cutting edge.
Main wear mechanism – adhesive
Cause:
- Sticky workpiece material
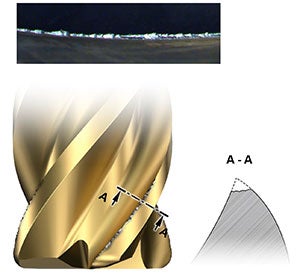
Uniform chipping (frittering)
Minor damages of the cutting edge. Other wear types can be followed by chipping.
Main wear mechanisms – thermomechanical or adhesive
Cause:
- Cutting edge is too weak and brittle
- Excessive temperature fluctuations
- Vibrations
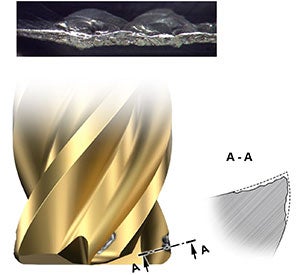
Top slicing
Usually when milling ISO-S materials. Starts on the edge line, extends to rake face and forms top slices.
Main wear mechanisms – adhesive and brittle fracturing
Cause:
- Sticky workpiece material
- High temperature
- Vibrations
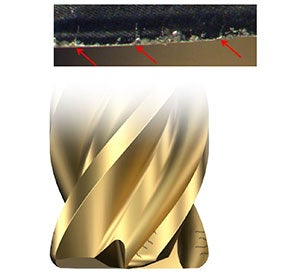
Comb cracks
Appears on cutting edge and extends on rake and flank faces. Initially oriented perpendicularly to the cutting edge, forms lateral cracks and provoke edge chipping.Main wear mechanism – thermomechanical
Cause:
- Rapid fluctuations in temperature
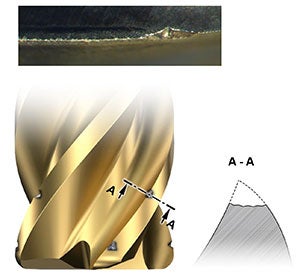
Localized chipping
Damage occurs consistently at certain position along the cutting edge line.
Main wear mechanisms – thermomechanical or adhesive
Cause:
- Cutting edge is too weak and brittle
- Excessive temperature fluctuations
- Vibrations
Chip re-cutting
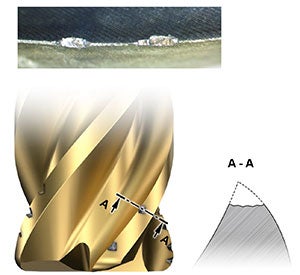
Non-uniform chipping
Damage of the cutting edge irregularly positioned along the cutting edge line.
Main wear mechanisms – thermomechanical or adhesive
Cause:
- Cutting edge is too weak and brittle
- Excessive temperature fluctuations
- Vibrations
- Chip re-cutting
- Remedy

Working together for a sustainable future
We can help you make your products and processes greener and more efficient. For several years Sandvik Coromant has been developing a code of conduct for environmental, health and safety management systems. An important part of that is a new life-cycle approach we apply when purchasing and collecting your worn tools so they can be reconditioned or recycled. This process saves both parties energy and reduces carbon dioxide emissions.