Fabrik der Zukunft
Die Produktionsstätte für Werkzeuge von Sandvik Coromant in Gimo (Schweden) wurde vom Weltwirtschaftsforum als fortschrittliche Industrie-4.0-Anlage ausgezeichnet.
Diese weltweit größte Anlage von Sandvik Coromant in Gimo, nördlich von Stockholm, ist ein hoch automatisiertes Werk, das die vielen Vorteile der digital vernetzten Fertigung voll ausnutzt. Dies wurde kürzlich vom Weltwirtschaftsforum bestätigt, das Gimo als einen seiner globalen „Leuchtturmstandorte“ bezeichnete. Jeder „Leuchtturm“ wird mit Hilfe einer Umfrage unter 1000 Fertigungsstätten ausgewählt, die alle erfolgreich digitale Technologien eingeführt haben und damit konkrete Erfolge erzielen.
Laut Weltwirtschaftsforum hat das Werk in Gimo mit seinen Produktionsprozessen einen digitalen roten Faden realisiert, der die Produktivität deutlich erhöht hat. Ein Beispiel ist die „berührungslose Umrüstung“, mit der Konstruktionsmuster auch während unbemannter Schichten automatisch geändert werden können. Mit diesen herausragenden Fortschritten gehört Gimo nun zum weltweiten Leuchtturmnetzwerk. Es verfolgt damit das Prinzip der offenen Tür und teilt sein Wissen mit anderen Fertigungsunternehmen.
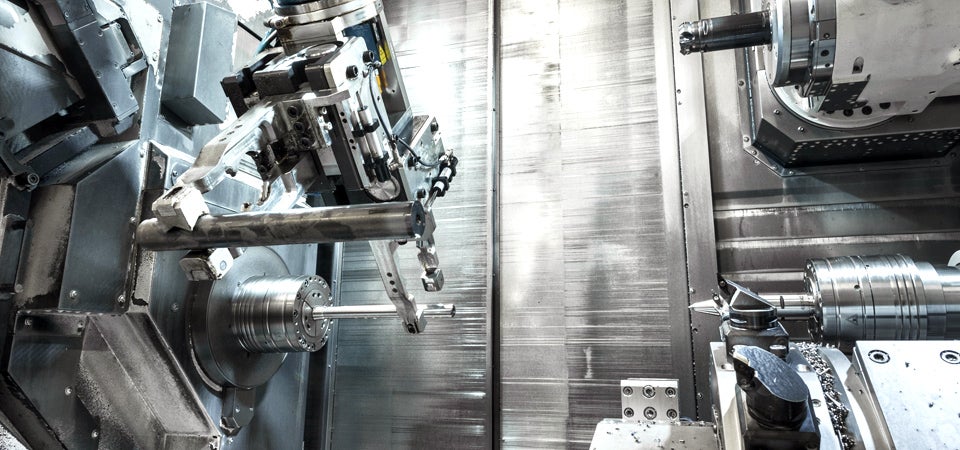
„Gimo hat diese Auszeichnung mit großem Stolz entgegengenommen“, erklärt Lars Matiasson, Director of Production Technology Tools bei Sandvik Coromant. „Mit ihr werden unsere langjährigen Bemühungen zur Förderung von Innovationen gewürdigt. Der Weg zur Digitalisierung begann hier in Gimo bereits vor 30 Jahren mit der Implementierung von parametrischem CAD/CAM. Ein paar Jahre später haben wir das mit unserer intelligenten Automatisierung verbunden und damit den ersten digitalen roten Faden in unserer Produktion geschaffen. Es war eher eine Evolution als eine Revolution.
Jetzt durchzieht ein digitaler roter Faden unser gesamtes Werk, von der Bestandsverwaltung bis hin zur Maschinenleistung und vorausschauenden Wartung. Dieser Innovationsgeist war schon immer eine Verpflichtung, die von oben nach unten ausgerichtet wurde. Die Direktoren und Führungskräfte von Gimo haben die Ingenieure immer ermutigt, neue Wege zu gehen und Veränderungen voranzutreiben. Letztendlich ging es darum zu untersuchen, wie neue Technologien zur Steigerung der Effizienz und der Wettbewerbsfähigkeit des Werks eingesetzt werden können. Das wiederum hat dazu beigetragen, eine nachhaltige Zukunft zu schaffen.“
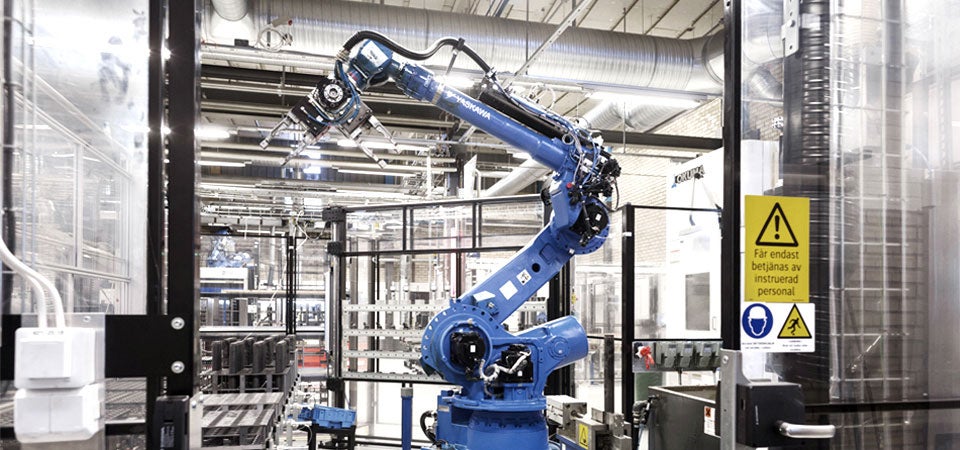
Die berührungslose Umrüstung ist ein typisches Beispiel. In der Vergangenheit mussten die Konstruktionsmuster in Produktionszellen manuell geändert werden, wobei die Bediener der Tagschichten die Maschinen für den Nachtbetrieb vorbereiteten. Dies erforderte Zeit und Ressourcen und begrenzte die Flexibilität bei unbemannten Schichten. Der alternative Ansatz bestand darin, in eine intelligente Automatisierung mit hochflexiblen Robotern, Maschinen, Werkzeugen und Vorrichtungen zu investieren, die zusammen in der Lage waren, komplexe berührungslose Umrüstungen ohne menschliche Aufsicht durchzuführen.
„Die Menschen sprechen von Lean Production, wenn sie den Werkzeugwechsel im einstelligen Minutenbereich meinen. Wir wollten jedoch noch einen Schritt weiter gehen. Wir wollten diesen Arbeitsaufwand auf null reduzieren“, berichtet Matiasson.
„Es war ein Lernprozess. Die erste automatisierte Zelle funktionierte nicht so gut, wie wir gehofft hatten. Das bisherige Konzept mit einem Bediener an der Maschine war effizienter. Aber man muss bei der Digitalisierung in der Lage sein, aus seinen Fehlern zu lernen. Nach und nach gelang es uns, signifikante Verbesserungen vorzunehmen, und die Roboterzellen begannen, die von uns geforderte Effizienz zu erreichen. Fortschritte lassen sich am besten mit dem Trial-und-Error-Prinzip erreichen."
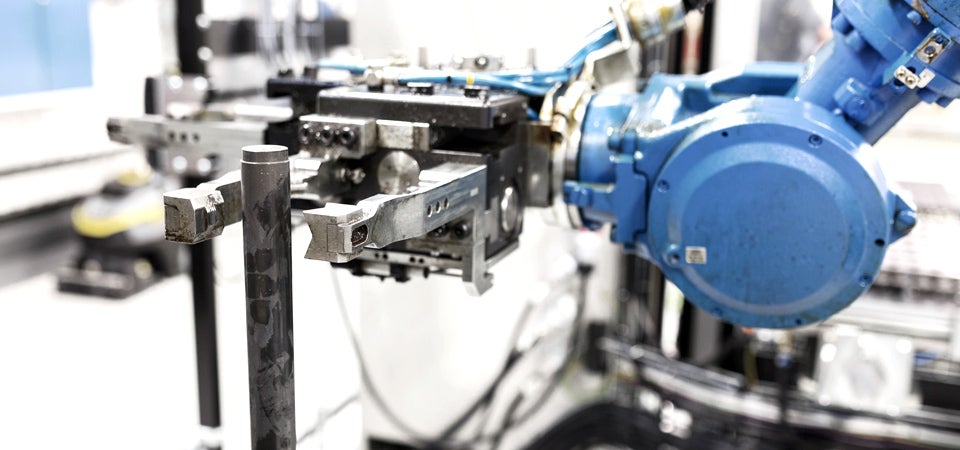
Digitale Verfahren werden in Gimo auch in anderen Bereichen eingesetzt, beispielsweise auch in der Instandhaltung. Es werden zunehmend Sensoren an einer Vielzahl von Geräten im Werk angebracht, die Daten über eine wachsende Liste von Parametern wie Druck, Temperatur, Vibrationen und Akustik sammeln. Diese Daten, kombiniert mit ausgefeilten Analysen, können Muster und Probleme aufdecken, bevor es zu Ausfallzeiten kommt.
Die Ingenieure sammeln nun Daten aus der gesamten Produktionsstätte, von den Robotern, den CNC-Maschinen bis hin zu den Zerspanungswerkzeugen selbst. Sobald diese Daten extrahiert und analysiert sind, können sie wertvolle Erkenntnisse über den Gerätezustand liefern. Diese Informationen können wiederum genutzt werden, um Ausfälle vorherzusagen und zu verhindern und so die Anlageneffizienz verbessern.
Sandvik Coromant setzt in wachsendem Maße auch Echtzeit-Analysen der Produktionsumgebung ein, um noch genauere und zeitnähere Anpassungen an den Maschinen vornehmen zu können. „Auf der nächsten Stufe werden hoch entwickelte Verfahren wie künstliche Intelligenz und maschinelles Lernen eingeführt, bei denen Maschinen aus früheren Daten lernen und über eine gewisse Selbstkontrolle verfügen. Das ist ein wirklich spannendes Gebiet.“
Auch nach diesen bemerkenswerten technischen Fortschritten und der Auszeichnung als Leuchtturm durch das Weltwirtschaftsforum wird in Gimo der Weg zur Digitalisierung konsequent fortgesetzt.