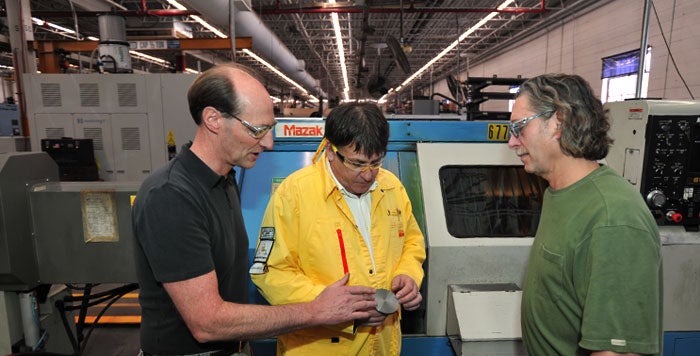
David Turk, Jim Pappas (technico-commercial Sandvik Coromant) et Tom Waite examinent l'état de surface de la pièce tronçonnée avec CoroCut® QD.
Si des options d'outillage légèrement plus rapides étaient apparues, David Turk et BUCHER Emhart Glass n'étaient guère enclins à abandonner leur solution de tronçonnage bien rodée. Mais un nouveau produit qui triplait leur productivité leur a finalement fait franchir le pas.
Les bocaux et les bouteilles en verre sont extrêmement communs, mais la plupart des gens ne savent pas qu'un grand nombre d'entre eux sont fabriqués sur des machines BUCHER Emhart Glass. Bucher Emhart Glass fabrique des contenants en verre depuis plus d'un siècle et est à l'origine de la norme industrielle des machines sectionnelles qui servent à produire la plupart des contenants en verre dans le monde. Elles possèdent des ensembles de cinq à vingt sections identiques équipées chacune de mécanismes pour former des contenants en verre creux, par exemple pour le secteur médical ou scientifique, et, bien sûr, pour l'industrie alimentaire.
Dans l'industrie verrière, l'examen et l'analyse des défauts est une étape critique. Pour assurer la pérennité de la qualité, Bucher Emhart Glass a racheté Powers Manufacturing, une entreprise située à Elmira dans l'état de New-York, en 1982. Cette société s'est taillé une réputation internationale dans le domaine des équipements d'inspection des produits finis.
La filiale de BUCHER Emhart Glass à Elmira continue à ce jour à concevoir, usiner, assembler et expédier des machines d'inspection complexes. 140 personnes environ sont employées sur le site d'Elmira. L'atelier d'usinage et l'atelier d'assemblage sont réunis sous un même toit. La partie usinage occupe un peu plus de mille mètres carrés. 25 personnes y travaillent en deux équipes.
L'atelier d'usinage comporte sept machines verticales, deux machines horizontales, trois tours trois axes et un tour sept axes. Ces machines incluent une machine de tournage-fraisage Mazak, trois tours Hardinge, deux machines Haas, une machine Komo et une machine verticale Bridgeport. Les matière usinées sont le leadloy 12L14, plus doux et facile à usiner, le bronze d'aluminium et l'acier inoxydable, plus tenace.
Le travail dans l'atelier d'usinage Emhart comporte de nombreuses productions isolées. Pour limiter les temps morts, les opérateurs doivent se montrer flexibles car les changements fréquents de montages imposent aux machines et à l'outillage de fonctionner aussi vite que possible. Ces tâches isolées nécessitent des vitesses de coupe optimales et une longue durée de vie d'outil afin de maintenir la productivité de l'atelier.
« Nous utilisons des outils Sandvik Coromant depuis le milieu des années 1990, surtout pour le tournage et le fraisage », dit David Turk, technicien chez Emhart Glass. « Sandvik Coromant est notre principal fournisseur d'outils et de plaquettes. Nous avons quelques autres fournisseurs, mais Sandvik Coromant nous fournit 80 à 85 pour cent de nos plaquettes carbure. Nous avons de bonnes relations avec notre distributeur local, One Time Tool, et c'est lui qui nous a suggéré d'essayer Sandvik Coromant ; nous l'avons fait et nous l'utilisons depuis ce temps. »
Bien qu'utilisant déjà des outils Sandvik Coromant pour d'autres opérations, David Turk n'était pas enclin à changer la configuration d'une opération de tronçonnage de pièces sur un tour. Il préférait s'en tenir au process et au produit qu'il utilisait depuis des années, mais il surveillait les nouveaux produits au cas où l'un d'eux aurait pu lui apporter des améliorations significatives. Aucun de ceux qu'il avait essayé n'apportait de réelle amélioration. Le tronçonnage est une opération assez courante chez Emhart. Elle intervient dans la fabrication de plusieurs pièces.
« Le tronçonnage intervient le plus souvent à la fin de la fabrication des pièces, alors l'erreur n'est pas permise. »
Le tronçonnage intervient le plus souvent à la fin de la fabrication des pièces, alors l'erreur n'est pas permise. Avec les différents montages, la programmation et les opérations d'usinage, les opérateurs et les machines ont déjà passé un certain temps sur la production des pièces lorsque l'opération de tronçonnage intervient. En effet, avant le tronçonnage, les pièces sont tournées, taraudées, percées, on usine des gorges et on effectue des opérations de finition. Il n'est donc pas question de risquer de devoir mettre la pièce au rebut après tout ce travail. C'est pourquoi Turk et ses collègues d'Emhart préféraient s'en tenir au process de tronçonnage qu'ils avaient éprouvé et qu'ils savaient fiable, à moins qu'il ne devienne possible d'augmenter la productivité de manière radicale.

Changer pour le mieux
« Nous avions essayé différentes plaquettes, différents fournisseurs, et même des plaquettes Sandvik Coromant, mais les résultats n'étaient pas suffisants pour justifier le changement », explique David Turk. « Nous produisons beaucoup de petites séries et il y a déjà un travail conséquent à faire pour le montage et la programmation. Pour nous décider à changer, il fallait vraiment que cela en vaille la peine. Au fil des années, nous avons observé de petites améliorations en termes de vitesses et d'efficacité avec d'autres outils et d'autres plaquettes, mais ce n'était pas assez. »
Si l'offre pour le tronçonnage et les gorges sur le marché ne convainquait pas Turk, l'opérateur Tom Waite lui a néanmoins redemandé de surveiller les nouveautés à l'automne 2013. À la même époque, le technico-commercial de Sandvik Coromant Jim Pappas venait juste de terminer sa formation sur le nouveau système de tronçonnage et gorges de sa société, CoroCut QD. Le hasard faisant bien les choses, il a appelé Turk à ce moment-là.
« Nous avons parlé des nouveaux produits qui sortaient et nous en sommes arrivés aux outils pour le tronçonnage et les gorges. J'ai mentionné la demande de Tom à propos de ces outils, et il y a eu comme un déclic », se souvient Turk. « Jim est venu à l'atelier avec le système CoroCut QD. Il nous a indiqué les paramètres, a trouvé un gros bout de barre et a commencé les essais. Dès la première tentative, nous avons été impressionnés par la manière dont les copeaux jaillissaient - c'était incroyable. »
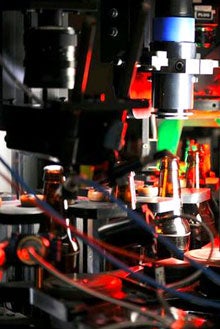
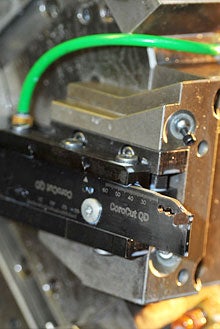
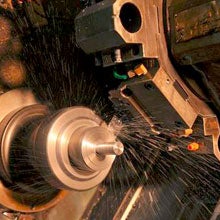
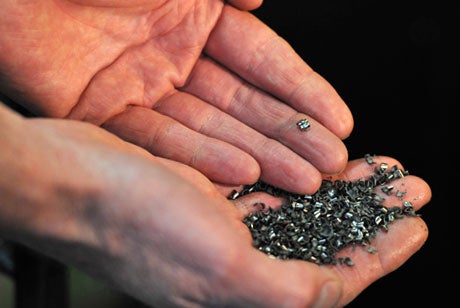
Des améliorations immédiates
Dès le premier jour, Turk a obtenu les résultats qu'il cherchait pour ses applications de tronçonnage. Avec CoroCut QD, le débit copeaux a été triplé, tout comme l'avance. La vitesse était si rapide qu'ils ont dû ralentir un peu la broche pour optimiser la durée de vie, qui, selon Turk, était remarquable.
« Auparavant, nous consommions à peu près cinq plaquettes par semaine. Maintenant, une seule plaquette tient une semaine entière », affirme Turk. “« Pour la vitesse, nous étions à 67 mètres par minute, c'est-à-dire 0,05 millimètre par tour, maintenant nous sommes presque à 183 mètres par minute, soit environ 0,18 millimètre par tour. »
L'augmentation du débit copeaux se traduit par un plus grand nombre de pièces usinées. La durée dépend du diamètre de la pièce tronçonnée, mais pour une pièce de 76,2 millimètres, Waite et Turk sont passés de 20 secondes à environ 7 secondes. En se basant sur une marge de 10 secondes par pièce, ce qui est large (mais le diamètre des pièces varie), le rapide calcul effectué par Turk indique que CoroCut QD permet de gagner 15 minutes par équipe, soit une demi-heure par jour. Ramené à l'année, cela représente 125 heures.
Mais la vitesse n'est pas tout. Sans une bonne précision, il ne sert à rien d'aller vite. Il est important de garantir la répétabilité et la rectitude des coupes.
« La qualité est là, et en plus, la coupe est propre et droite. »
« La qualité est là, et en plus, la coupe est propre et droite. La partie tronçonnée peut parfois être conique, concave, ou convexe, ou former un ventre », précise Turk. « Nous avons utilisé un instrument de mesure pour nous assurer que la lame de tronçonnage était bien perpendiculaire à l'axe de la pièce. Une fois le réglage effectué, nous étions bons. »
Turk s'est avoué convaincu après que tous les essais aient montré une très nette amélioration de la productivité en maintenant une très bonne précision. Mais Waite, en tant qu'opérateur machine, s'est montré plus circonspect. Les essais sur une opération qui nécessitait de positionner l'outil CoroCut QD vers le haut au lieu de l'orienter vers le bas, en raison de la configuration de la tourelle, étaient l'épreuve ultime.
« Sur les tours, il est toujours recommandé d'orienter l'outil vers le bas afin que la gravité favorise l'évacuation des copeaux. Sans cela, les risques de bourrages de copeaux dans la gorge étroite créée par les opérations de tronçonnage sont accrus ; la gorge ne fait guère plus de 5 millimètres, ce qui est peu pour les copeaux », explique Turk. « Tom a vite avoué qu'il était impressionné par la manière dont les copeaux étaient éjectés de la gorge par le liquide de coupe, même en travaillant avec l'outil orienté vers le haut. »
Selon Turk, l'adduction de liquide de coupe par l'intérieur de l'outil permet de produire un arrosage régulier directement au niveau de l'arête de coupe et cela favorise à la fois l'évacuation des copeaux et la durée de vie de l'outil. Avec le système utilisé auparavant, l'arrosage devait arriver par l'extérieur et la précision était moins bonne.
Il est souvent judicieux de s'en tenir à ce qui fonctionne, surtout si aucune autre solution clairement meilleure n'est disponible. Mais il arrive aussi que les solutions en place qui fonctionnent correctement nous empêchent de découvrir d'autres solutions qui pourraient peut-être apporter une amélioration intéressante. Turk et Waite ont attendu patiemment que le bon produit arrive. Lorsqu'une nouvelle solution s'est présentée, ils ont mené des expériences suffisantes pour pouvoir changer de produit, convaincus d'avoir trouvé enfin une vraie amélioration pour leurs opérations de tronçonnage.
« Dès le premier jour, Turk a obtenu les résultats qu'il cherchait depuis longtemps pour ses applications de tronçonnage. »
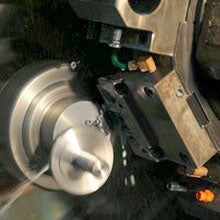
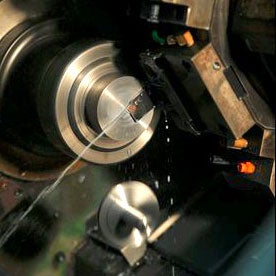
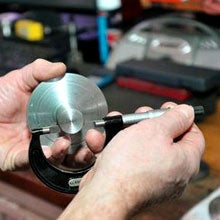