L'usine du futur
Le Forum économique mondial a reconnu l'usine de Sandvik Coromant située à Gimo, en Suède, comme site Industrie 4.0 avancé.
Les installations de production d'outillage de Sandvik Coromant à Gimo, au nord de Stockholm, sont extrêmement automatisées et exploitent au maximum les avantages du numérique. Il n'est pas étonnant que le Forum économique mondial ait récemment désigné l'usine de Gimo comme l'un de ses « sites phares ». Ces sites ont été sélectionnés parmi plus de 1000 installations de production en fonction de leur mise en œuvre des technologies numériques et des avantages qu'ils ont su en retirer.
Selon les termes de l'annonce du Forum, l'usine de Sandvik Coromant de Gimo a créé un fil numérique reliant tous ses process de production qui a apporté un gain de productivité significatif. Le changement de production automatique en est un exemple ; grâce à lui, les modes de production peuvent être changés sans intervention humaine. Sandvik Coromant et les autres sites phares du réseau du Forum sont des vitrines qui ouvrent leurs portes et partagent leurs connaissances avec d'autres sociétés du secteur manufacturier.
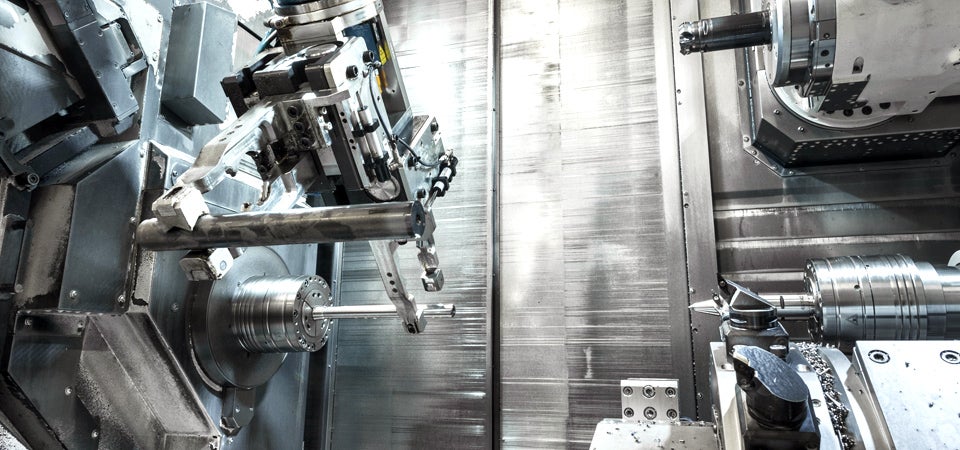
Selon Lars Matiasson, directeur technique des outils de production chez Sandvik Coromant, la nomination par le Forum a été accueillie avec fierté à Gimo car elle couronne un effort d'innovation soutenu dans le temps. « La mise en place progressive du numérique dans l'usine de Gimo a commencé il y a 30 ans avec la mise en place de la CAO/FAO paramétrique. Ensuite cette solution a été interconnectée avec des systèmes d'automatisation, et cela a été le premier fil numérique dans notre production. Ce processus a été une évolution plutôt qu'une révolution.
« L'usine est maintenant entièrement numérisée et tout est interconnecté, de la gestion des stocks à la surveillance des performances des machines en passant par la maintenance prévisionnelle. Cet esprit d'innovation a toujours été un engagement top-down. La direction et les responsables de Gimo ont toujours encouragé les techniciens à penser différemment et à innover. Le but ultime est d'utiliser la technologie pour améliorer l'efficacité et la compétitivité de l'usine. Et cette approche contribue au développement durable. »
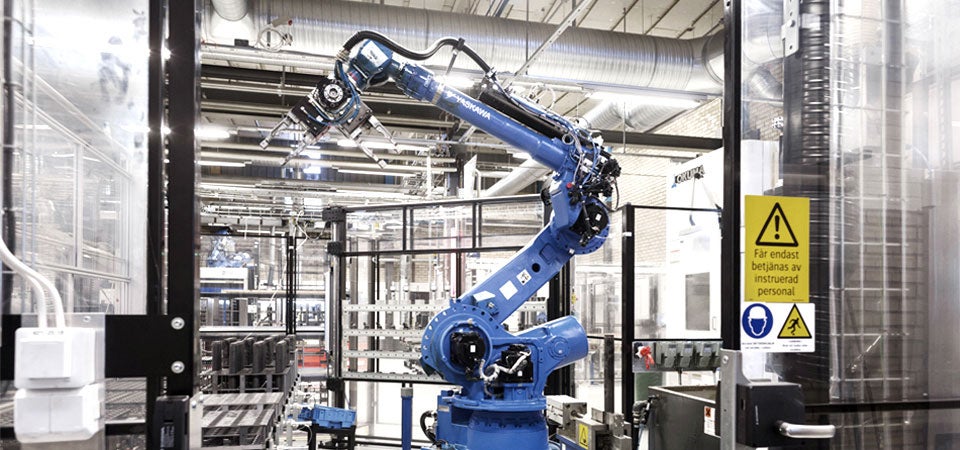
Le changement de production sans intervention humaine illustre parfaitement le niveau d'avancement. Auparavant, les schémas de production des cellules devaient être préparés manuellement par les opérateurs des équipes de jour en vue de la production nocturne. Cela prenait du temps et utilisait des ressources, et la flexibilité de la production sans surveillance était limitée. Pour pallier ce manque d'efficacité, il a fallu investir dans des robots, des machines, des outils et des systèmes de bridage ultra flexibles et dans des systèmes d'automatisation intelligents capables d'adapter la production de manière totalement automatique.
« Pour beaucoup, les techniques de production Lean se limitent à des opérations telles que des changements minute de matrices, mais nous voulions faire plus que cela. Nous voulions une mise en place de la production entièrement automatique, sans intervention humaine », dit Matiasson.
« Il y a eu une courbe d'apprentissage. La première cellule automatisée ne fonctionnait pas aussi bien que nous l'avions espéré. En fait, elle était même moins efficace qu'une machine pilotée par un opérateur. Mais dans le domaine du numérique, les essais et les erreurs sont ce qui fait progresser. Nous avons progressivement réussi apporter des améliorations importantes et les cellules robotisées ont peu à peu acquis l'efficacité dont nous avions besoin. Le travail empirique joue un rôle important dans l'amélioration. »
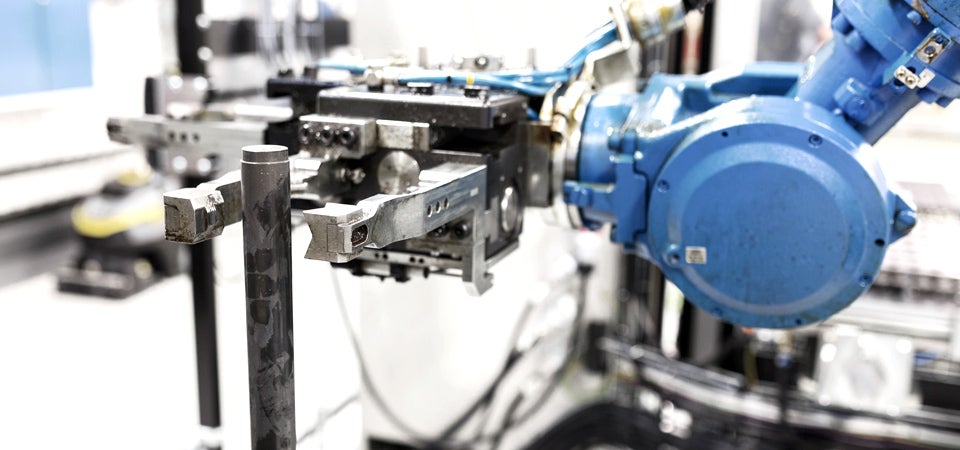
Les technologies numériques sont aussi utilisées dans d'autres domaines que la production elle-même dans l'usine de Gimo, par exemple pour la maintenance. De plus en plus d'équipements sont dotés de capteurs qui collectent des données sur un nombre toujours croissant de paramètres tels que la pression, la température, les vibrations et le bruit. Ces données sont utilisées par des systèmes d'analyse sophistiqués capables de détecter les schémas et les problèmes avant que les pannes ne surviennent.
Les données proviennent de tous les équipements, des robots, des machines CNC et même des outils de coupe eux-mêmes. Leur analyse fournit des informations précieuses sur l'état des équipements. Il est possible de prévenir les pannes, ce qui représente un gain important en termes d'efficacité.
Sandvik Coromant utilise aussi de plus en plus l'analyse en temps réel de l'environnement de production pour effectuer des ajustements précis des machines. « L'étape suivante sera d'introduire des techniques très sophistiquées comme l'intelligence artificielle et l'apprentissage grâce auxquelles les machines pourront apprendre à partir des données collectées et s'adapter d'elles-mêmes. C'est un développement extrêmement intéressant. »
Même si les avancées techniques sont considérables et même avec la reconnaissance comme site phare par le Forum économique mondial, le développement du numérique dans l'usine de Gimo ne s'arrête jamais.