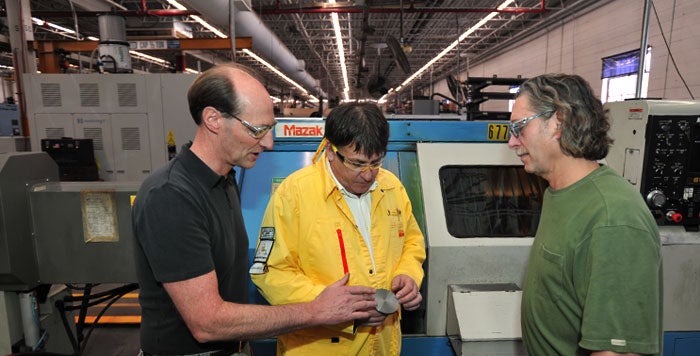
David Turk, Jim Pappas (ingeniero de ventas, Sandvik Coromant) y Tom Waite examinan el acabado de las piezas conseguido con CoroCut® QD.
A pesar de que se encontraban disponibles opciones de sistemas de herramientas ligeramente más rápidos, David Turk y BUCHER Emhart Glass se mostraban reacios a abandonar su herramienta de tronzado de eficacia probada. Pero un nuevo producto que triplicaba su productividad finalmente les convenció para dar el paso.
Puesto que los contenedores y botellas de vidrio se encuentran en todas partes, la mayoría de nosotros habremos utilizado contenedores formados e inspeccionados en una máquina de BUCHER Emhart Glass. Encargada del suministro de contenedores de vidrio de calidad durante más de un siglo, la empresa Bucher Emhart Glass ha desarrollado la máquina de Secciones Individuales (IS, por sus siglas en inglés), que se ha convertido en el estándar de la industria y en el dispositivo de formación de contenedores de vidrio de uso más extendido y preferido por los fabricantes de vidrio de todo el mundo. Esta máquina presenta un conjunto de 5 a 20 secciones idénticas, cada una de las cuales incluye un juego completo de mecanismos para realizar contenedores de vidrio de diferentes tamaños, la mayoría de ellos destinados a las industrias médica, científica y de la alimentación y las bebidas.
En la fabricación de vidrio, la inspección y el análisis de los defectos es un paso fundamental. Para garantizar que Bucher Emhart Glass pudiera continuar suministrando contenedores de vidrio de calidad superior, en el año 1982 adquirió Powers Manufacturing en Elmira (Nueva York). La empresa Powers Manufacturing se había forjado una importante fama internacional por el suministro de equipos de inspección en frío de gran calidad.
El puesto fronterizo de Elmira (Nueva York) de BUCHER Emhart Glass diseña, mecanizada, monta y envía aún en la actualidad máquinas de inspección complejas. En las instalaciones de Elmira trabajan unas 140 personas, con un taller de maquinaria y de montaje situados bajo el mismo techo. La parte de las instalaciones dedicada al taller de maquinaria ocupa unos 12.000 pies cuadrados, con 25 empleados que trabajan en dos turnos.
El taller está equipado con 7 máquinas verticales, 2 horizontales, 3 tornos de 3 ejes y 1 torno de 7 ejes. La mezcla de marcas incluye una máquina de fresado y torneado de Mazak, 3 tornos de Hardinge, 2 máquinas de Haas, 1 máquina de Komo y 1 máquina vertical de Bridgeport. Entre los principales materiales utilizados se encuentran el acero 12L14, que tiende a ser más blando y fácil de mecanizar, y el bronce de aluminio y el acero inoxidable, que tienden a ser más resistentes.
El flujo de trabajo en el taller de maquinaria de Emhart está marcado por numerosos trabajos de ejecución breve. Para limitar el tiempo de inactividad, este programa precisa flexibilidad por parte del operario, ya que los frecuentes cambios ejercen una mayor presión en las máquinas y las herramientas para que estas funcionen con la mayor rapidez posible. Estos trabajos de ejecución breve requieren velocidades de corte óptimas y una vida útil prolongada para que el taller pueda mantener su productividad.
"Hemos utilizado los sistemas de herramientas de Sandvik Coromant desde mediados de la década de los 90, principalmente para operaciones de fresado y torneado", afirma David Turk, ingeniero de MFG/CNC en Emhart Glass. "Sandvik Coromant es nuestro principal proveedor de plaquitas y portaherramientas. Contamos con algún otro, pero las de Sandvik Coromant representan probablemente el 80-85 % de nuestras plaquitas de metal duro intercambiables. Tenemos una buena relación con nuestro proveedor de herramientas local, One Time Tool, que nos recomendó que probáramos con Sandvik Coromant. Lo hicimos y hemos utilizado sus productos desde entonces".
Aunque Turk ya utilizaba sistemas de herramientas de Sandvik Coromant para otras operaciones, no estaba convencido de cambiar la operación actual de tronzado de piezas en un torno. Fiel a un proceso y a un producto que ha utilizado durante años, estaba pendiente de aquellos productos que ofrecieran una mejora significativa, pero ninguno de los que había probado resultó satisfactorio. El tronzado no es una operación poco habitual en Emhart. En realidad se necesita para varias piezas.
"Puesto que con frecuencia es la fase final del proceso de mecanizado, el tronzado es un paso crucial".
Puesto que con frecuencia es la fase final del proceso de mecanizado, el tronzado es un paso crucial. Entre los reglajes de las máquinas, la programación y el tiempo dedicado a generar viruta, los operarios y las máquinas han invertido una cantidad considerable de tiempo en el mecanizado de la pieza para cuando llega el momento del tronzado. Las piezas ya se han torneado, roscado con macho, taladrado, ranurado y acabado previamente al tronzado. Desechar una pieza después de una inversión de tiempo y capacidad de la máquina de estas características simplemente no es una opción. Por ello, lo que iban a hacer era seguir fieles al proceso que Turk y el resto de personal de Emhart consideraban que era el más seguro, a menos que algo supusiera un cambio radical en sus niveles de productividad.

Garantizar el cambio
"Probamos diferentes plaquitas, diferentes proveedores, incluso algunas plaquitas de Sandvik Coromant, pero no llegamos a ver un resultado lo suficientemente significativo como para justificar o garantizar la efectividad del cambio", afirma Turk. "Puesto que realizamos muchos trabajos de ejecución breve y ya existen numerosos reglajes y cambios de programación, queríamos ver algo con lo que pudiéramos sacar partido a nuestro dinero antes de hacer el cambio. Con el paso de los años, asistimos a un ligero aumento de la velocidad y la eficiencia con otras plaquitas y sistemas de herramientas, pero no lo suficiente como para convencernos de cambiar".
Pero incluso aunque ningún otro sistema de herramientas de tronzado del mercado había cautivado lo suficiente a Turk, el operario, Tom Waite le pidió que se mantuviera al tanto de los nuevos sistemas de herramientas para operaciones de tronzado durante el otoño de 2013. Mientras tanto, Jim Pappas, ingeniero de ventas de Sandvik Coromant, acababa de finalizar la formación sobre CoroCut QD, la nueva herramienta de tronzado y ranurado de la empresa. La llamada de Pappas a Turk no podría haber venido en mejor momento.
"Estábamos hablando sobre nuevos lanzamientos de productos y, cuando llegamos a los sistemas de herramientas para tronzado y ranurado, mencioné la solicitud de Tom de este tipo de herramientas y a ambos se nos encendió la bombilla", explica Turk. "Jim vino al taller de máquinas con CoroCut QD, nos proporcionó los parámetros, cogió una gran porción de material y empezó a llevar a cabo las pruebas. Desde el primer momento nos impresionó cómo salía la viruta de la herramienta. ¡Increíble!"
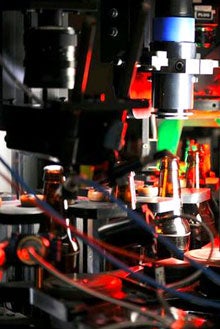
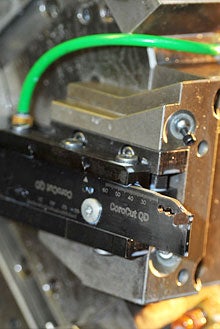
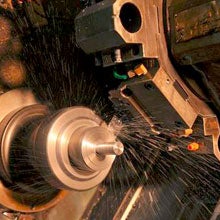
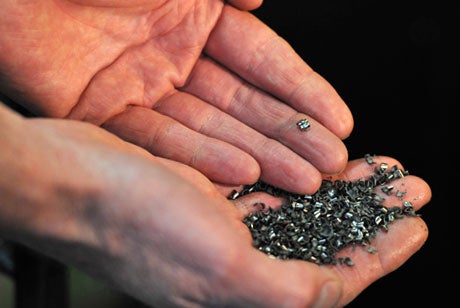
Mejoras originales
Desde el primer día, Turk obtuvo los resultados que buscaba en aplicaciones de tronzado. Gracias a CoroCut QD, ha triplicado la viruta por revolución y los pies de superficie mecanizada. El movimiento del material era tan rápido que, de hecho, tuvieron que pisar un poco el freno, ralentizando la velocidad del husillo para obtener así una optimización de la vida útil, que según Turk también ha sido notable.
"Antes utilizábamos probablemente unas 5 plaquitas a la semana; ahora hemos reducido esta cifra a 1 por semana", explica Turk. "En cuanto a la velocidad, originalmente hacíamos 220 pies de superficie por minuto, es decir, 0.002 pulgadas por revolución. Ahora, 600 pies de superficie y 0.007 pulgadas por revolución, lo que supone un aumento drástico".
El hecho de mover más material directamente significa que se realizan más piezas. La duración depende siempre del diámetro de la pieza torneada pero, en el caso de una pieza de 3 pulgadas de material, Waite y Turk han reducido el tiempo de tronzado de 20 segundos a 6-8 segundos aproximadamente. Adoptando un margen conservador de 10 segundos por pieza (debido a los cambios de diámetro), según los cálculos de Turk, gracias a CoroCut QD se obtiene un ahorro de 15 minutos por turno, lo que equivale a media hora al día. Al extrapolar esa cifra a un año se consigue un ahorro de 125 horas.
Pero toda la velocidad del mundo sería inútil sin precisión. Garantizar unos cortes rectos y repetibles es igual de importante.
"La calidad del corte está ahí y, además, el corte es excelente y recto".
"La calidad del corte está ahí y, además, el corte es excelente y recto. Al llevar a cabo operaciones de tronzado, a menudo se puede obtener un cono cóncavo o convexo; el fuelle hacia adentro o el fuelle hacia afuera", apunta Turk. "Utilizábamos un indicador, un instrumento de medición diseñado para comprobar la conicidad, para asegurarnos de que la lama se encontrara perpendicular a la superficie de la pieza. Una vez realizada la calibración, no había de qué preocuparse".
Con una mejora drástica de la productividad demostrada en las principales pruebas, manteniendo al mismo tiempo el nivel de precisión más elevado, Turk estaba impresionado. Pero, como operario de la máquina, Waite también tenía que estar convencido. La prueba de fuego tuvo lugar en una operación en la que la configuración de la torreta del torno requería que CoroCut QD funcionara del derecho en lugar de invertida.
"El protocolo habitual en las máquinas de torneado es encarar la superficie de corte invertida, de modo que la gravedad contribuye al arranque de viruta. Sin la ayuda de la gravedad, la viruta puede provocar atascos en aplicaciones de tronzado y ranurado estrechas, de unos 5 mm (3/16 pulg.) de dimensión; la ranura de que disponemos para la evacuación de la viruta es estrecha", explica Turk. "Tom no tardó en mencionar lo impresionado que estaba con cómo el refrigerante forzaba a la viruta a salir de la ranura, incluso al realizar cortes del derecho".
Según Turk, el refrigerante interior que fluye a través de la herramienta y transporta un caudal regular hasta el filo, contribuye tanto a prolongar la vida útil de la herramienta como a facilitar la evacuación de la viruta. La fresa de tronzado anterior contaba con una tubería de refrigerante exterior que no proporcionaba el mismo suministro de refrigerante de gran precisión.
El instinto de ser fiel a un sistema que funciona es, por lo general, positivo, especialmente si no hay otro proceso considerablemente mejor que el actual. Pero, a menudo, ser fiel a un proceso de eficacia probada evita que los talleres conozcan nuevas soluciones que podrían suponer para ellos un gran paso adelante desde el punto de vista técnico. Turk y Waite son excelentes ejemplos de ingenieros y operarios que tuvieron la paciencia suficiente para esperar al producto adecuado en el momento preciso y experimentaron lo suficiente para realizar el cambio tras descubrir el próximo gran avance en aplicaciones de tronzado.
"Desde el primer día, Turk obtuvo los resultados que buscaba en aplicaciones de tronzado".
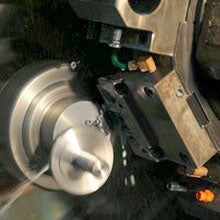
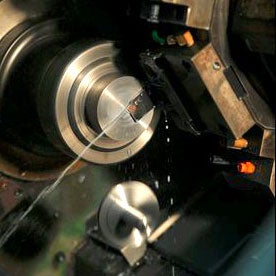
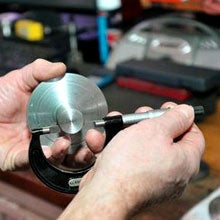