La fábrica del futuro
La planta de producción de herramientas de Sandvik Coromant en Gimo (Suecia) ha sido reconocida por el Foro Económico Mundial como un centro avanzado con la etiqueta Industria 4.0.
La planta de producción de herramientas de Sandvik Coromant en Gimo, al norte de Estocolmo, es un centro altamente automatizado que ha abierto de par en par sus puertas a la fabricación digital conectada, una realidad que recientemente le ha valido el reconocimiento del Foro Económico Mundial, que ha elegido la planta de Gimo como uno de sus «faros» internacionales. Cada uno de estos faros se ha seleccionado a partir de un estudio realizado a más de 1.000 unidades de producción, valorando su nivel de adopción de tecnologías digitales y las ventajas tangibles demostradas.
Según el Foro Económico Mundial, la planta de Gimo ha introducido en sus procesos de producción un flujo digital que ha conseguido multiplicar la productividad. Un ejemplo es su sistema de cambio sin contacto, que permite cambiar patrones de diseño automáticamente, incluso en turnos sin intervención de operadores. Gracias a estos importantes avances, Gimo formará parte ahora de la red internacional de faros y podrá compartir conocimientos con otras empresas de fabricación.
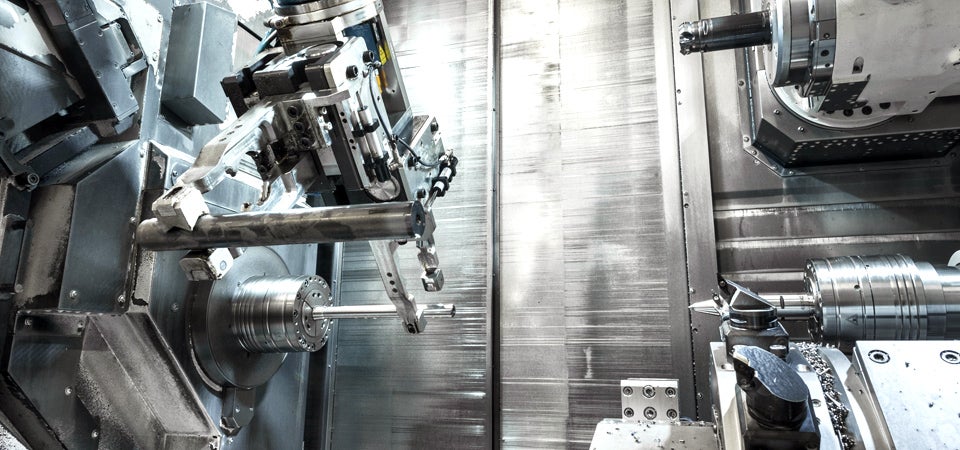
Para la planta de Gimo, el reconocimiento ha supuesto un auténtico espaldarazo, según asegura Lars Matiasson, director de herramientas para tecnologías de producción de Sandvik Coromant, ya que representa la culminación de un esfuerzo de innovación de largo recorrido. «El camino hacia la digitalización en Gimo empezó hace 30 años con la introducción de sistemas CAD/CAM paramétricos, que unos años más tarde conectamos con nuestra tecnología de automatización inteligente, con lo que conseguimos crear el primer flujo digital en nuestra producción. Ha sido más una evolución que una revolución».
«Ahora vemos que este flujo digital recorre toda la planta, desde la gestión de inventario hasta la productividad de las máquinas y el mantenimiento predictivo. Este espíritu de innovación siempre ha sido fruto de un compromiso que va de arriba abajo. Históricamente, en Gimo los directivos y los supervisores han animado a los ingenieros a pensar diferente y a apostar por el cambio. Al final, el objetivo siempre ha sido ver cómo pueden usarse las tecnologías para mejorar la eficiencia y aumentar la competitividad de la planta. Y esto, a su vez, nos asegura un futuro más sostenible».
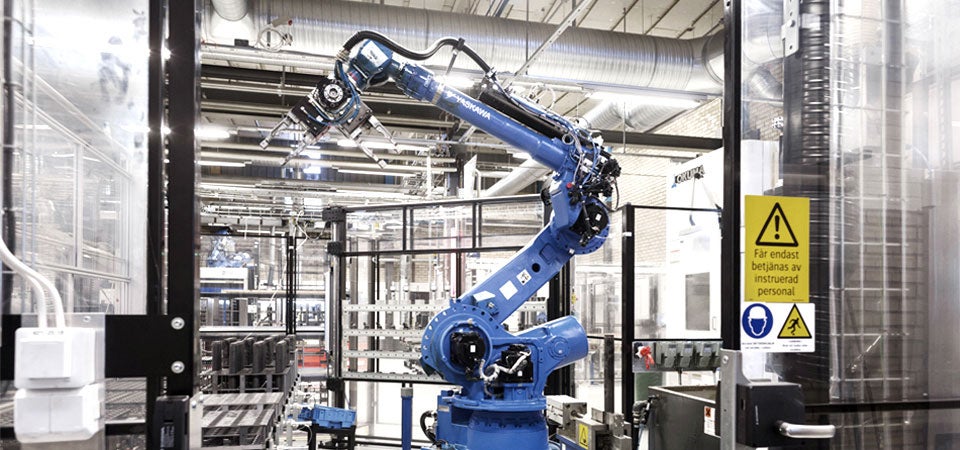
El sistema de cambio sin contacto es un ejemplo paradigmático. Históricamente, los patrones de diseño de las células de producción tenían que cambiarse manualmente y los operadores de los turnos de día preparaban las máquinas para las operaciones nocturnas. Este proceso consumía tiempo y recursos, además de restar flexibilidad durante los turnos automatizados. Una alternativa fue la inversión en sistemas de automatización inteligentes basados en robots, máquinas, herramientas y fijaciones extremadamente flexibles, que juntos consiguieron realizar complejas operaciones de cambio sin contacto y sin necesidad de supervisión humana.
«Se habla mucho de técnicas de producción ajustada, como los cambios de matriz en un minuto, pero nosotros queríamos ir más allá. Queríamos unas configuraciones con trabajo cero», explica Matiasson.
«Fue todo un proceso de aprendizaje. La primera célula automatizada no funcionó todo lo bien que esperábamos. De hecho, era menos eficiente incluso que trabajar con un operador y una máquina. Pero es lo que ocurre con la digitalización: hay que poder fracasar para aprender. Poco a poco, fuimos introduciendo mejoras importantes y las células robotizadas empezaron a llegar a los niveles de eficiencia que necesitábamos. El ensayo y error es fundamental en todo proceso de mejora».
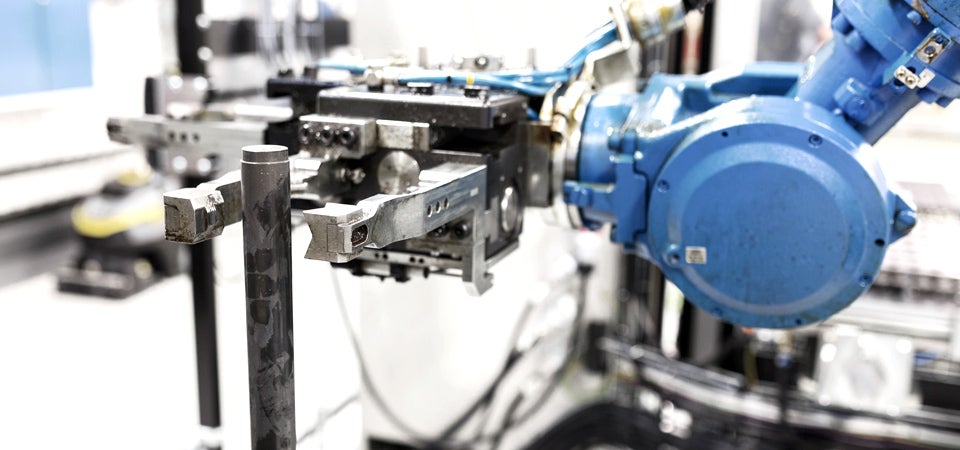
En Gimo, las tecnologías digitales también se aplican para introducir mejoras en otras áreas, como el mantenimiento. Los sensores cada vez son más habituales en un amplio abanico de equipos de la planta, para recopilar datos sobre diferentes parámetros, como la presión, la temperatura, las vibraciones y la acústica. Estos datos, combinados con sofisticados análisis, pueden destapar patrones y problemas antes de que se produzcan averías.
Los ingenieros ahora pueden recopilar datos de todas las instalaciones de producción, como máquinas CNC, robots e incluso herramientas de corte. Una vez extraídos y analizados, estos datos pueden aportar información de gran interés sobre el estado de los equipos. Esta información, a su vez, puede utilizarse para predecir y prevenir fallos y, por tanto, mejorar la eficiencia de la planta.
Sandvik Coromant apuesta cada vez más por la aplicación de análisis en tiempo real al entorno de producción, para realizar ajustes más precisos y pertinentes en las máquinas. «La siguiente fase será la introducción de técnicas mucho más sofisticadas, como la inteligencia artificial y el aprendizaje automático, para que las máquinas puedan aprender a partir de datos históricos y trabajar con un cierto nivel de autocontrol. Es un horizonte muy emocionante».
A pesar de estos importantes avances técnicos y del reconocimiento del Foro Económico Mundial, el viaje hacia la digitalización de Gimo todavía está lejos de llegar a su destino.